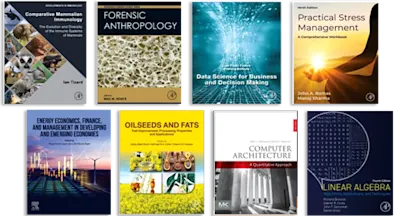
Joining Textiles
Principles and Applications
- 1st Edition - January 24, 2013
- Imprint: Woodhead Publishing
- Editors: I Jones, G K Stylios
- Language: English
- Hardback ISBN:9 7 8 - 1 - 8 4 5 6 9 - 6 2 7 - 6
- eBook ISBN:9 7 8 - 0 - 8 5 7 0 9 - 3 9 6 - 7
Understanding the techniques for joining fabrics together in a way that considers durability, strength, leak-tightness, comfort in wear and the aesthetics of the joints is critical… Read more
Purchase options
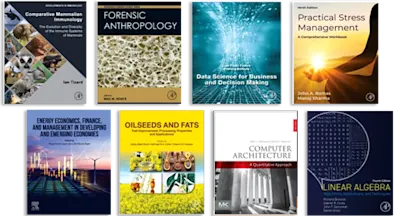
- Provides an authoritative guide to the key theories and methods used to efficiently join fabrics
- Discusses the mechanics of stitching and sewing and problems related to sewn textiles, alongside mechanisms of sewing machines, and intelligent sewing systems
- Explores adhesive bonding of textiles, including principles, methods and applications, along with a review of bonding requirements in coating and laminating of textiles
Contributor contact details
Woodhead Publishing Series in Textiles
Introduction
Chapter 1: Types of fabric and their joining requirements
Abstract:
1.1 Introduction
1.2 The main types of natural fibre
1.3 Synthetic fibres
1.4 High performance fibres
1.5 The process of creating fabrics from fibres
1.6 Woven fabric structures
1.7 Knitted fabric structures
1.8 Non-woven fabrics
1.9 Joining fabrics: seams and stitches
1.10 Stitching in practice: the case of high performance fabrics
1.11 Alternative methods of joining fabrics: welded seams
1.12 Ultrasonic welding
1.13 Conclusions
1.14 Acknowledgements
Part 1: Sewing technology
Chapter 2: The mechanics of stitching
Abstract:
2.1 Introduction
2.2 The principles of stitching
2.3 Conclusion
2.5 Appendix: nomenclature and notation
Chapter 3: The sewing of textiles
Abstract:
3.1 Introduction
3.2 Types of sewing machine
3.3 Machine feeding systems
3.4 Machine settings and sewing quality
3.5 Needle size and point type
3.6 Stitch classification and applications
3.7 Seam classification and applications
3.8 Sewing threads
3.9 Seaming quality problems
3.10 Seam pucker: causes and prevention
3.11 Thread breakage: causes and prevention
3.12 Needle breakage
3.13 Slipped/missed stitching: causes and prevention
3.14 Uneven seams: causes and prevention
3.15 Comparing welded and sewn seams
3.16 Future trends
Chapter 4: Mechanisms of sewing machines
Abstract:
4.1 Introduction
4.2 The evolution of the sewing machine
4.3 Machine categorisation
4.4 Integrated stitching unit (ISU)
4.5 Types of motors used in sewing machines
4.6 Three-thread overlock with a microprocessor
4.7 Mechanised sewing machines
4.8 Semi-automatic machines, automated workstations and transfer lines
4.9 Advantages and limitations of machine automation
4.10 Computer numerical control (CNC)
4.11 Achieving fully automated apparel manufacture through the application of robotics
4.12 Conclusion
4.13 Sources of further information and advice
Chapter 5: Problems relating to sewing
Abstract:
5.1 Introduction
5.2 Seam elasticity
5.3 Seam failure
5.4 Seam problems related to material feeding
5.5 Problems in stitch formation
5.6 Seam pucker and other surface distortions
5.7 Future trends
5.8 Sources of further information and advice
Chapter 6: The quality and performance of sewn seams
Abstract:
6.1 Introduction
6.2 Seam strength
6.3 Seam extensibility and recovery
6.4 Seam puckering
6.5 Seam slippage
6.6 Drape and bending
6.7 Seam grinning/gaping
6.8 Barrier properties of seams
6.9 Flame retardancy of seams
6.10 Degradation/damage of seams
6.11 Sources of further information and advice
Chapter 7: Intelligent sewing systems for garment automation and robotics
Abstract:
7.1 Introduction
7.2 Developments in the automation of sewing
7.3 Operational principles of the intelligent sewability environment (ISE)
7.4 Conclusions
Part II: Adhesive bonding of textiles
Chapter 8: Adhesive bonding of textiles: principles, types of adhesive and methods of use
Abstract:
8.1 Introduction to adhesives in the textile industry
8.2 Reasons for the success and failure of adhesives
8.3 Classification of adhesives used in textile applications
8.4 Bonding processes
8.5 Trends in adhesive types
Chapter 9: Adhesive bonding of textiles: applications
Abstract:
9.1 Introduction: textiles and adhesive joining
9.2 Adhesives and adhesive applications
9.3 Properties achieved by adhesive joining
9.4 Examples of adhesive use
9.5 Future trends
9.6 Acknowledgements
Chapter 10: Bonding requirements in coating and laminating of textiles
Abstract:
10.1 Introduction
10.2 Materials and adhesives in coating and laminating
10.3 Coating process
10.4 Laminating process
10.5 Properties and applications of coated and laminated fabrics
10.6 Conclusion
Part III: Welding technologies
Chapter 11: The use of heat sealing, hot air and hot wedge to join textile materials
Abstract:
11.1 Heat sealing of textiles: introduction
11.2 Equipment for heat sealing
11.3 Factors affecting the quality of heat sealing
11.4 Applications of heat sealing in textiles
11.5 Hot air wedge and hot wedge welding of textiles: introduction
11.6 Equipment for hot air/wedge welding
11.7 Factors affecting the quality of hot air/wedge welding
11.8 Applications of hot air/wedge welding in textiles
Chapter 12: Ultrasonic and dielectric welding of textiles
Abstract:
12.1 Ultrasonic welding: an introduction
12.2 Equipment for ultrasonic welding
12.3 Factors affecting the quality of ultrasonic welding
12.4 Applications of ultrasonic welding in textiles
12.5 Dielectric welding: an introduction
12.6 Equipment for dielectric welding
12.7 Factors affecting the quality of dielectric welding
12.8 Applications of dielectric welding
Chapter 13: Laser seaming of fabrics
Abstract:
13.1 Introduction
13.2 The laser welding process
13.3 The main processing parameters in laser welding and their effects
13.4 Equipment in laser welding
13.5 Textile materials that can be laser welded
13.6 Joint designs in laser welding
13.7 Monitoring and quality control in laser welding
13.8 Comparison between stitched and laser welded seams
13.9 Applications of laser welding
13.10 Future trends
Chapter 14: Properties and performance of welded or bonded seams
Abstract:
14.1 Introduction
14.2 Performance properties of seams
14.3 Quality evaluation of welded or bonded seams
14.4 Conclusion
Part IV: Applications of joining textiles
Chapter 15: The appearance of seams in non-iron shirts
Abstract:
15.1 Introduction
15.2 Wrinkle-free fabrics
15.3 Non-iron shirts and seam pucker
15.4 Interlinings as sewing aids
15.5 The stitching of non-iron shirts
15.6 Discussion and conclusion
15.7 Acknowledgements
15.8 Appendix: key terms and definitions
Chapter 16: Seams in car seat coverings: properties and performance
Abstract:
16.1 Introduction
16.2 Materials and machines for sewing car seat covers
16.3 Influence of the seam on materials for making car seat covers
16.4 Seaming problems in car seat covers and their solution
16.5 Future trends
16.6 Conclusions
16.7 Acknowledgement
Chapter 17: Joining of wearable electronic components
Abstract:
17.1 Introduction
17.2 Conducting fibres
17.3 Conducting yarns
17.4 Fabrics and composites
17.5 Connecting technologies
17.6 Requirements of electronic interconnects
17.7 Applications
17.8 Future trends
17.9 Sources of further information and advice
17.10 Acknowledgements
Chapter 18: Joining of technical textiles with stringent seam demands
Abstract:
18.1 Introduction
18.2 Joining techniques for textiles with stringent seam demands
18.3 Applications of stringent seams in technical textiles
18.4 Future trends
18.5 Sources of further information and advice
18.6 Acknowledgement
Chapter 19: Nonwoven materials and joining techniques
Abstract:
19.1 Introduction
19.2 Principles of nonwovens
19.3 Raw materials
19.4 Web formation technology
19.5 Web bonding technology
19.6 Nonwoven fabric finishing
19.7 Techniques for joining nonwoven materials
19.8 Future trends in the nonwoven market
19.9 Acknowledgements
Chapter 20: Epilogue: joining textiles
Index
- Edition: 1
- Published: January 24, 2013
- Imprint: Woodhead Publishing
- Language: English
IJ
I Jones
GS