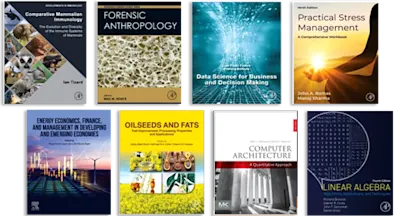
Introduction to the Physical Metallurgy of Welding
- 2nd Edition - September 17, 2013
- Imprint: Butterworth-Heinemann
- Author: Kenneth Easterling
- Language: English
- Paperback ISBN:9 7 8 - 0 - 7 5 0 6 - 0 3 9 4 - 2
- eBook ISBN:9 7 8 - 1 - 4 8 3 1 - 4 1 6 6 - 4
Introduction to the Physical Metallurgy of Welding deals primarily with the welding of steels, which reflects the larger volume of literature on this material; however, many of the… Read more
Purchase options
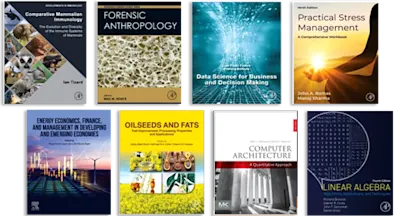
Introduction to the Physical Metallurgy of Welding deals primarily with the welding of steels, which reflects the larger volume of literature on this material; however, many of the principles discussed can also be applied to other alloys. The book is divided into four chapters, in which the middle two deal with the microstructure and properties of the welded joint, such as the weld metal and the heat-affected zone. The first chapter is designed to provide a wider introduction to the many process variables of fusion welding, particularly those that may influence microstructure and properties, while the final chapter is concerned with cracking and fracture in welds. A comprehensive case study of the Alexander Kielland North Sea accommodation platform disaster is also discussed at the end. The text is written for undergraduate or postgraduate courses in departments of metallurgy, materials science, or engineering materials. The book will also serve as a useful revision text for engineers concerned with welding problems in industry.
Preface to the 1st EditionPreface to the 2nd EditionPrologue1. Fusion Welding - Process Variables Fusion Welding Principles of Consumable Development Absorption of Gases in the Weld Metal Nitrogen Absorption Hydrogen Absorption Composition of Welds Summary of Process Variables The Weld Thermal Cycle Heat-Flow Equations The Thermal Cycle of the Base Metal Refinements to Rosenthal's Heat Flow Equation Further Refinements to the Heat-Flow Equations Heat Flow in Electroslag Welding Weld Simulation Summary of Weld Thermal Cycle Results Residual Stresses in Welds Stresses and Strains Generated by Changes in Temperature Stresses Generated by the γ→α Phase Transformation Measurement of Residual Stresses in Welds Numerical Methods of Estimating Residual Stresses in Welds Summary of Residual Stress Work References Further Reading2. The Weld Metal Characteristics of Weld Solidification Thermal Gradients and Turbulence in the Melt Geometry of the Weld Melt Epitaxial Solidification Crystal Growth and Segregation No Diffusion in Solid; Perfect Mixing in Liquid No Diffusion in Solid; Diffusional Mixing in Liquid Cellular and Dendritic Solidification in Welds Dendritic Growth in Single Crystal Welds of Stainless Steel Refining Weld Structures Phase Transformations during Cooling of the Weld Metal Kinetics of Phase Transformations Transformations in Duplex Stainless Steel Welds Transformations in Carbon and Low Alloy Steel Welds Role of Slag Inclusions in Transformation Kinetics Modeling the Microstructure and Properties of Weld Metals Weld Metal Toughness References Further Reading3. The Heat-Affected Zone The Base Material The Base Metal's Carbon Equivalent The Heating Cycle Recrystallization The α→γ Phase Transformation Precipitate Stability Precipitate Coarsening during a Weld Thermal Cycle Precipitate Dissolution during a Weld Thermal Cycle Grain Growth Kinetics of Grain Growth Grain Growth during Welding, Assuming Particle Dissolution Grain Growth during Welding, Assuming Particle Coarsening Practical Considerations of Grain Growth and Grain Growth Control in the HAZ Reactions at the Fusion Line Transformations during Cooling Grain Growth Zone Grain Refined Zone Partially Transformed Zone Zone of Spheroidized Carbides Zone of 'Unchanged' Base Material The Heat-Affected Zone Microstructure of Oxide-Dispersed Steels Predicting the Microstructure and Properties of the HAZ Weld Simulation Hardness Measurements Weld CCT Diagrams Hardness Changes in Aluminum Alloy Welds Weld Microstructure Diagrams Grain Growth Diagrams Multi-Run Welds The Weld Metal The HAZ PC Software for Weldability Prediction References Further Reading4. Cracking and Fracture in Welds Fracture Toughness Fracture Toughness Testing Solidification Cracking Solidification Structure Segregation Residual Stresses and Joint Geometry Mechanism of Solidification Cracking Liquation Cracking Lamellar Tearing Mechanism of Lamellar Tearing Cold Cracking Role of Hydrogen Role of Stress Role of Microstructure Mechanism of Cold Cracking Reheat Cracking Effect of Reheating on the Microstructure of a 0.5 Cr-Mo-V Alloy Mechanism of Reheat Cracking Case Study: The Alexander Kielland Disaster Construction of the Alexander Kielland The Construction and Fitting of the Sonar Flange Plate Capsize of the Alexander Kielland Metallographic Examination of the Sonar Flange Plate Welds Possible Effects of the Weld Thermal Cycle on the Bracing and Flange Plate Materials Mechanism of Failure: Main Conclusions References Further ReadingAppendix: Weld Cracking Tests and Weldability FormulaIndex
- Edition: 2
- Published: September 17, 2013
- Imprint: Butterworth-Heinemann
- Language: English
Read Introduction to the Physical Metallurgy of Welding on ScienceDirect