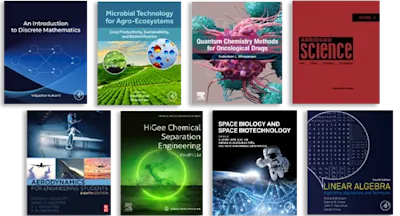
International Gear Conference 2014: 26th-28th August 2014, Lyon
- 1st Edition - September 18, 2014
- Imprint: Chandos Publishing
- Author: Philippe Velex
- Language: English
- eBook ISBN:9 7 8 - 1 - 7 8 2 4 2 - 1 9 5 - 5
This book presents papers from the International Gear Conference 2014, held in Lyon, 26th-28th August 2014. Mechanical transmission components such as gears, rolling element… Read more
Purchase options
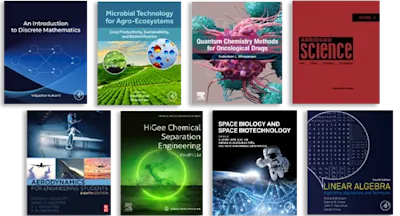
This book presents papers from the International Gear Conference 2014, held in Lyon, 26th-28th August 2014. Mechanical transmission components such as gears, rolling element bearings, CVTs, belts and chains are present in every industrial sector and over recent years, increasing competitive pressure and environmental concerns have provided an impetus for cleaner, more efficient and quieter units. Moreover, the emergence of relatively new applications such as wind turbines, hybrid transmissions and jet engines has led to even more severe constraints. The main objective of this conference is to provide a forum for the most recent advances, addressing the challenges in modern mechanical transmissions. The conference proceedings address all aspects of gear and power transmission technology and range of applications (aerospace, automotive, wind turbine, and others) including topical issues such as power losses and efficiency, gear vibrations and noise, lubrication, contact failures, tribo-dynamics and nano transmissions.
- A truly international contribution with more than 120 papers from all over the world
- A judicious balance between fundamental research and industrial concerns
- Participation of the most respected international experts in the field of gearing
- A wide range of applications in terms of size, power, speed, and industrial sector
These papers will be particularly useful for experts on mechanical transmissions both from a research and industrial perspective.
- Foreword
- Industrial Sponsors
- Plenary Papers
- High ratio transmissions – the key component for future mechatronic systems
- Tribo-dynamic behavior of gear pairs
- Influence of enveloping stressed volume and trochoidal interference on durability of gear teeth
- Gearbox power losses – Influence of lubricants, tooth and casing geometry
- Session 1: Worm Gears
- Measurement of helix deviation for planar double enveloping hourglass worms
- ABSTRACT
- 1 INTRODUCTION
- 2 WORKING PRINCIPLE AND CONSTITUTION OF THE MACHINE
- 3 MEASUREMENT PRINCIPLE
- 4 DATA PROCESSING
- 5 CONCLUSIONS
- Calculation of the efficiency of worm gear drives
- ABSTRACT
- 1 INTRODUCTION
- 2 POWER FLOW IN WORM GEAR DRIVES
- 3 CALCULATION OF THE POWER LOSSES BY WORM GEAR DRIVES
- 4 COMPARISON OF THE MEASUREMENT AND THE SIMULATION
- 5 ANALYSIS OF THE POWER LOSSES
- 6 CONCLUSION
- Strength of plastic helical wheels meshed with various types of worms
- ABSTRACT
- 1 INTRODUCTION
- 2 EXPERIMENTAL METHOD AND APPARATUS
- 3 EXPERIMENTAL RESULTS AND DISCUSSION
- 4 CONCLUSION
- Loaded behaviour of steel/bronze worm gear
- ABSTRACT
- 1 INTRODUCTION
- 2 NUMERICAL MODEL
- 3 RESULTS AND STUDIES
- 4 CONCLUSION
- Measurement of helix deviation for planar double enveloping hourglass worms
- Session 2: Tooth Modifications
- Optimal modifications on helical gears for good load distribution and minimal wear
- ABSTRACT
- 1 INTRODUCTION
- 2 MESHING SIMULATION - ACTUAL PATH OF CONTACT
- 3 LOAD DISTRIBUTION - LOCAL PRESSURE DISTRIBUTION
- 4 WEAR-SIMULATION
- 5 COMPARISON TO TEST RESULTS - DISCUSSION
- 6 CRACK CRITERION
- SUMMARY
- Profile optimization of the teeth of the double rackand-pinion gear mechanism in the MCE-5 VCRi
- ABSTRACT
- 1 INTRODUCTION
- 2 STUDY OF THE CORRECTION PARAMETERS INFLUENCE
- 3 CALCULATION OF THE OPTIMUM PROFILE ON A 3D MODEL
- 4 CONCLUSION
- A procedure to determine the optimum flank line modifications for planetary gear configurations
- 1 INTRODUCTION
- 2 ADAPTION OF THE METHOD FOR PLANETARY GEARS
- 3 APPLICATION: EVALUATION OF A ‘FLEX PIN DESIGN’
- 4 INFLUENCE OF PLANET CARRIER TORSION WHEN USING ISO6336-1, ANNEX E, METHOD
- 5 SOME REMAINING QUESTIONS
- 6 CONCLUSION
- Multi-objective optimisation of profile modifications in spur and helical gears – an analytical approach
- ABSTRACT
- 1 INTRODUCTION
- 2 THEORY
- 3 ELEMENTS OF VALIDATION
- 4 PERFORMANCE DIAGRAMS ON THE MASTER CURVE
- 5 CONCLUSION
- Optimal modifications on helical gears for good load distribution and minimal wear
- Session 3: Manufacturing (I)
- Manufacturing method of double helical gears using multi-axis control and multi-tasking machine tool
- ABSTRACT
- 1 INTRODUCTION
- 2 TOOTH SURFACES OF DOUBLE HELICAL GEARS
- 3 CAD/CAM SYSTEM
- 4 MANUFACTURING OF DOUBLE HELICAL GEARS
- 5 MEASUREMENT OF DOUBLE HELICAL GEARS
- 6 TOOL WEAR AND LIFE TIME
- 7 APPLICATION TO PUMP GEARS
- 8 CONCLUSIONS
- Gear tooth surface roughness of helical gears manufactured by a form milling cutter
- ABSTRACT
- 1 INTRODUCTION
- 2 GEOMETRY OF TOOL
- 3 MILLING PROCESS
- 4 THE MACHINED SURFACE
- 5 NUMERICAL EXAMPLE AND VALIDATION
- 6 CONCLUSION
- ACKNOWLEDGEMENT
- Grinding face-hobbed hypoid gears through full exploitation of 6-axis hypoid generators
- ABSTRACT
- 1 INTRODUCTION
- 2 THE FACE-HOBBING METHOD
- 3 PROPOSED METHOD TO GRIND FACE-HOBBED BEVEL GEARS
- 4 A NUMERICAL EXAMPLE
- 5 CONCLUSIONS
- Process model for honing larger gears
- ABSTRACT
- 1 INTRODUCTION
- 2 CHALLENGE
- 3 RESEARCH OBJECTIVE AND APPROACH
- 4 WORKPIECE AND HONING TOOL DESIGNS
- 5 ANALYTICAL MODELLING OF THE GEAR HONING PROCESS
- 6 EXPERIMENTAL SETUP
- 7 EMPIRICAL PROCESS ANALYSIS
- 8 SUMMARY AND OUTLOOK
- Manufacturing method of double helical gears using multi-axis control and multi-tasking machine tool
- Session 4: Plastic Gears
- Gear tooth deflection of spur polymer gears
- ABSTRACT
- 1 INTRODUCTION
- 2 THEORETICAL BACKGROUND
- 3 PRACTICAL EXAMPLE
- 4 RESULTS
- 5 CONCLUSION
- 6 ACKNOWLEDGEMENTS
- Experimental and numerical study of a loaded cylindrical glass fibre reinforced PA6 gear
- ABSTRACT
- 1 INTRODUCTION
- 2 GENERALITY ON PA6 + 30%GF GEARS
- 3 NUMERICAL MODEL
- 4 EXPERIMENTAL MEASUREMENTS
- 5 CONCLUSION
- Lifetime and meshing teeth temperature of plastic crossed helical gear: case of grease lubrication
- ABSTRACT
- 1 INTRODUCTION
- 2 EXPERIMENTAL PROCEDURE
- 3 RESULTS AND DISCUSSION
- 4 CONCLUSION
- Gear tooth deflection of spur polymer gears
- Session 5: Hypoid/Bevel Gears
- Improvement of the excitation behavior of bevel gears considering tolerance fields caused by manufacturing and assembly processes
- ABSTRACT
- 1 INTRODUCTION AND MOTIVATION
- 2 APPROACH OF ROBUST GEAR DESIGN VIA VARIATIONAL CALCULUS
- 3 EVALUATION OF THE LOAD-FREE EXCITATION BEHAVIOR
- 4 ANALYSIS OF THE LOADED EXCITATION BEHAVIOR
- 5 SUMMARY AND OUTLOOK
- Hypoid gears with involute teeth
- ABSTRACT
- 1 BACKGROUND
- 2 RACK COORDINATES
- 3 CYLINDORIDAL COORDINATES
- 4 HYPERBOLOIDAL CUTTER COORDINATES
- 5 ILLUSTRATIVE EXAMPLE I
- 6 SUMMARY
- Increasing the load-capacity of bevel gears by the use of modern optimization methods
- ABSTRACT
- 1 INTRODUCTION
- 2 ASYMMETRIC TOOTH PROFILE
- 3 COMPARABILITY OF DIFFERENT BEVEL GEARS
- 4 OPTIMIZATION OF THE CONTACT PATTERN
- 5 OPTIMIZATION OF THE TOOTH ROOT
- 6 CONCLUSION
- Note
- Improvement of the excitation behavior of bevel gears considering tolerance fields caused by manufacturing and assembly processes
- Session 6: Gear Noise (I)
- Effects of rib arrangements on radiated noise of gearbox
- ABSTRACT
- 1 INTRODUCTION
- 2 THEORETICAL CONSIDERATIONS
- 3 RADIATED NOISE ANALYSIS
- 4 ACOUSTIC CONTRIBUTION ANALYSIS
- 5 GEARBOX IMPROVEMENT
- 6 CONCLUSIONS
- ACKNOWLEDGEMENT
- Low noise design of a truck timing multi-stage gear: robust optimization of tooth surface modifications
- ABSTRACT
- 1 INTRODUCTION
- 2 THE OPTIMIZATION PROBLEM
- 3 THE METAHEURISTIC ALGORITHM
- 4 THE ROBUSTNESS STUDY
- 5 RESULTS
- 6 EXPERIMENTAL TESTS
- 7 CONCLUSIONS
- ACKNOWLEDGEMENTS
- Low power transmission plastic gear trains: which parameters affect the subjective acoustic quality?
- ABSTRACT
- 1 INTRODUCTION
- 2 PYSCHOACOUSTIC METRICS
- 3 METHODOLOGY
- 4 RESULTS AND DISCUSSION
- 5 CONCLUSION
- Effects of rib arrangements on radiated noise of gearbox
- Session 7: Manufacturing and Design (I)
- Improvement of the design method for helical gears by considering manufacturing related bias errors
- ABSTRACT
- 1 INTRODUCTION
- 2 OBJECTIVE AND APPROACH
- 3 INFLUENCES OF BIAS ERRORS ON OPERATIONAL BEHAVIOR
- 4 CHARACTERIZATION AND DETERMINATION OF SYSTEMATIC TOOTH FLANK DEVIATIONS
- 5 CONSIDERATION OF BIAS ERRORS IN TCA SOFTWARE
- 6 DEFINITION OF THE DESIGN METHOD
- 7 SUMMARY AND OUTLOOK
- Investigation of the effect of manufacturing errors on dynamic characteristics of herringbone planetary gear trains
- ABSTRACT
- 1 INTRODUCTION
- 2 MODELING METHODOLOGY
- 3 INTERNAL EXCITATIONS OF THE SYSTEM
- 4 AN EXAMPLE SIMULATION
- 5 CONCLUSIONS
- ACKNOWLEDGMENTS
- An approach of pairing bevel gears from conventional cutting machine with gears produced on 5-axis milling machine
- ABSTRACT
- 1 INTRODUCTION
- 2 TOPOLOGICAL MODICATION OF THE 3D MODEL
- 3 APPLICATION AND RESULT
- 4 CONCLUSIONS
- Improvement of the design method for helical gears by considering manufacturing related bias errors
- Session 8: Rollers – Roller Bearings
- Mechanical power losses of full-complement needle bearings of planetary gear sets
- ABSTRACT
- 1 INTRODUCTION
- 2 POWER LOSS MEASUREMENT METHODOLOGY
- 3 EXPERIMENTAL RESULTS
- 4 MECHANICAL POWER LOSS MODEL OF A FULL-COMPLEMENT NEEDLE BEARING
- 5 CONCLUSION
- A finite element evaluation of a bearing instrumentation method for evaluating bearing load distributions and roller stresses of the final drive of a wind turbine gearbox
- ABSTRACT
- 1 INTRODUCTION
- 2 HIGH SPEED SHAFT ANALYSIS
- 3 IMPLEMENTATION OF BEARING RACE GROOVE
- 4 CONCLUSION
- ACKNOWLEDGMENTS
- Modeling and analysis of a planetary roller screw
- ABSTRACT
- 1 INTRODUCTION
- 2 THEORY
- 3 RESULTS
- 4 CONCLUSION
- Mechanical power losses of full-complement needle bearings of planetary gear sets
- Session 9: Gear Design (I)
- Pitch factor analysis for symmetric and asymmetric tooth gears
- 1 INTRODUCTION
- 2 DEFINITION OF GEAR TOOTH PROFILES
- 3 DEFINITION OF PITCH FACTORS
- 4 AREA OF EXISTENCE AND PITCH FACTORS
- 5 EXAMPLE OF APPLICATION
- 6 SUMMARY
- Effects of the design parameters of involute gears generated by rack-cutters
- ABSTRACT
- 1 INTRODUCTION
- 2 MATHEMATICAL MODEL OF THE RACK CUTTER
- 3 SYNTHESIS OF SPUR AND HELICAL GEARS
- 4 CONTINUITY OF MOTION
- 5 UNDERCUTTING AND OVERCUTTING
- CONCLUSIONS
- Graph theory based gear transmission chain configuration modelling
- ABSTRACT
- 1 INTRODUCTION
- 2 TRANSMISSION CHAIN MODELING
- 3 GRAPH MODEL OF GEAR TRANSMISSION CHAIN
- 4 ANALYSIS BASED ON GRAPH MODEL
- 5 CONCLUSIONS
- Pitch factor analysis for symmetric and asymmetric tooth gears
- Session 10: Gear Noise and Vibration (I)
- Noise characteristics of the simplified gear box by wind turbine load
- ABSTRACT
- 1 INTRODUCTION
- 2 MATHEMATICAL MODEL
- 3 RESULTS AND DISCUSSION
- 4 CONCLUSION
- Effects of contact ratios on mesh stiffness of helical gears for lower noise design
- ABSTRACT
- 1 INTRODUCTION
- 2 THE METHOD FOR CALCULATING MESH STIFFNESS
- 3 THE FLUCTUATION OF CONTACT-LINE LENGTH
- 4 THE INFLUENTIAL FACTORS OF MESH STIFFNESS
- 5 CONCLUSIONS
- ACKNOWLEDGMENT
- Dynamic modeling of planetary gear transmission coupled with gearbox vibrations
- ABSTRACT
- 1 INTRODUCTION
- 2 DYNAMIC MODELING
- 3 DYNAMICS ANALYSIS
- 4 CONCLUSIONS
- ACKNOWLEDGEMENT
- Noise characteristics of the simplified gear box by wind turbine load
- Session 11: Contact Analysis
- Tribodynamics of differential hypoid gears
- ABSTRACT
- 2 INTRODUCTION
- 3 DYNAMIC MODEL
- 4 FULL TRIBOLOGICAL MODEL
- 5 RESULTS AND DISCUSSION
- 6 CONCLUDING REMARKS
- A comparison and experimental validation of gear contact models for spur and helical gears
- 1 INTRODUCTION
- 2 DECOMPOSING GEAR STIFFNESS
- 3 COMPARISON OF GEAR CONTACT MODELS
- 4 CONCLUSIONS AND FUTURE WORK
- 5 ACKNOWLEDGEMENTS
- Smooth and non-smooth contact analysis of micro-surfaces of gear teeth
- ABSTRACT
- 1. INTRODUCTION
- 2 SMOOTH-CONTACT ANALYSIS OF MICRO-TOOTH SURFACES
- 3 NON-SMOOTH CONTACT ANALYSIS OF MICRO-SURFACES OF GEAR TEETH
- 4 CONCLUSION
- ACKNOWLEDGMENTS
- Tribodynamics of differential hypoid gears
- Session 12: Gear Materials
- Alternative to Ni-bearing carburizing steels
- ABSTRACT
- INTRODUCTION
- 1 GEAR MANUFACTURING
- 2 TEST METHOD
- 3 TEST RESULTS AND DISCUSSION
- 4 ONCLUSION
- A new approach to evaluate materials for open gear
- ABSTRACT
- 1 INTRODUCTION
- 2 SPECIFICATIONS OF THE TEST BENCH
- 3 TEST BENCH CONCEPTS
- 4 CALIBRATION
- 5 FIRST RESULTS
- Load bearing capacity of sintered steel gears made of completely prealloy powder for automotive power transmission
- ABSTRACT
- 1 INTRODUCTION
- 2 EXPERIMENTAL METHOD
- 3 RESULTS AND DISCUSSION
- 4 CONCLUSIONS
- Alternative to Ni-bearing carburizing steels
- Session 13: Gear Design (II)
- Development of a user friendly interface for design and analysis of parallel axes gears based on international standards including quasi static transmission error curves
- ABSTRACT
- 1 INTRODUCTION
- 2 SPUR GEAR STRENGTH ANALYSIS
- 3 INTERNATIONAL PARALLEL AXES GEAR STANDARDS
- 4 FLOW CHART OF THE SOFTWARE
- 5 CASE STUDY
- 6 QUASI STATIC TRANSMISSION ERROR CURVE
- 7 DISCUSSIONS AND CONCLUSION
- A study on the design of asymmetric spur gears in gear pump applications
- ABSTRACT
- 1 INTRODUCTION
- 2 ASYMMETRIC GEAR MODEL
- 3 STRESS ANALYSIS USING FINITE ELEMENT METHOD
- 4 FLOWRATE ANALYSIS
- 5 RESULTS AND DISCUSSION
- 6 CONCLUSION
- Research on gear integrated error curves
- ABSTRACT
- 1 INTRODUCTION
- 2 THE GEAR INTEGRATED ERROR CURVE (GIEC)
- 3 THE GEAR PAIR INTEGRATION ERROR CURVE (GPIEC)
- 4 EXPERIMENTAL RESULTS
- 5 CONCLUSION
- ACKNOWLEDGEMENT
- The latest design technologies for gear devices with great transmission ratios
- ABSTRACT
- 1 INTRODUCTION
- 2 STRUCTURES, ADVANTAGES AND BASIC PERFORMANCES OF THE GRG
- 3 THE LATEST DESIGN AND STRENGTH ANALYSIS TECHNOLOGIES FOR GRG
- 4 FUTURE TENDENCIES
- 5 CONCLUSIONS
- Development of a user friendly interface for design and analysis of parallel axes gears based on international standards including quasi static transmission error curves
- Session 14: Gear Noise (II)
- Dynamic and acoustic simulation of helicopters drive trains
- ABSTRACT
- 1 INTRODUCTION
- 2 MAIN GEARBOXES NOISE ANALYSIS
- 3 MAIN GEARBOXES DYNAMIC AND NOISE SIMULATION
- 4 CONCLUSION
- Hammering noise modelling – Nonlinear dynamics of a multi-stage gear train
- ABSTRACT
- 1 INTRODUCTION
- 2 THE DYNAMIC MODEL OF THE GEAR SYSTEM
- 3 THE NUMERICAL METHOD
- 4 NUMERICAL EXAMPLE
- 5 CONCLUSIONS
- ACKNOWLEDGEMENTS
- Gear noise prediction in automotive transmissions
- ABSTRACT
- 1 INTRODUCTION
- 2 METHOD FOR GEAR NOISE EVALUATION
- 3 USE OF THE PRESENTED METHOD TO PREDICT GEAR NOISE FOR AUTOMOTIVE TRANSMISSIONS
- 4 CONCLUSION
- Dynamic and acoustic simulation of helicopters drive trains
- Session 15: Manufacturing and Design (II)
- Local simulation of the specific material removal rate for generating gear grinding
- ABSTRACT
- 1 INTRODUCTION
- 2 STATE OF THE ART
- 3 OBJECTIVE AND APPROACH
- 4 LOCAL APPROACH FOR CALCULATING THE SPECIFIC MATERIAL REMOVAL RATE FOR GENERATING GEAR GRINDING
- 5 GLOBAL APPROACH FOR CALCULATING THE SPECIFIC MATERIAL REMOVAL RATE FOR GENERATING GEAR GRINDING
- 6 SUMMARY AND OUTLOOK
- Semi-analytical modelling of load distribution of side-fit involute splines
- ABSTRACT
- 1 INTRODUCTION
- 2 SEMI-ANALYTICAL SPLINE CONTACT MODEL
- 3 MULTI-STEP DISCRETIZATION SOLUTION SCHEME
- 4 COMPARISON BETWEEN THE SEMI-ANALYTICAL AND DEFORMABLE-BODY MODELS
- 5 CONCLUSIONS
- ACKNOWLEDGEMENTS
- A new geometrically adaptive approach for tooth contact analysis of gear drives
- ABSTRACT
- 1 INTRODUCTION
- 2 ALGORITHM TO COMPUTE THE TCA
- 3 ALGORITHM TO SOLVE THE POSITIONAL CONTACT PROBLEM
- 4 ALGORITHM TO COMPUTE THE BEARING CONTACT
- 5 TEST CASES AND DISCUSSION
- 6 CONCLUSIONS
- A gear element in a wind-turbine gearbox
- ABSTRACT
- 1 INTRODUCTION
- 2 DEFINITIONS
- 3 CHECKING THE DATA
- 4 ADDENDUM CORRECTIONS
- 5 THEORETICAL GEAR LOAD CALCULATION
- 6 GEAR MESH CONSTRUCTION
- 7 PLANETARY STAGE MESH CONSTRUCTION
- 8 VALIDATIONS
- 9 EXAMPLES
- 10 CONCLUSIONS
- Local simulation of the specific material removal rate for generating gear grinding
- Session 16: Tooth Surfaces
- Quality and surface of gears manufactured by free form milling with standard tools
- ABSTRACT
- 1 INTRODUCTION
- 2 AIM OF STUDY AND APPROACH
- 3 TERMINOLOGY OF FREE FORM MILLING
- 4 ANALYISIS OF PROCESS CAPABILITY IN MILLING TRIALS
- 5 SUMMARY AND OUTLOOK
- Fatigue performance of cylindrical gearing with DLC coatings
- ABSTRACT
- 1 INTRODUCTION
- 2 DLC COATING
- 3 FATIGUE PERFORMANCE
- 4 CONCLUSIONS
- On the simulation of simultaneous fatigue and mild wear during a micropitting gear test
- ABSTRACT
- 1 INTRODUCTION
- 2 WEAR MODEL
- 3 FATIGUE MODEL
- 4 COMBINED WEAR AND FATIGUE DAMAGE MODEL
- 5 SIMULATION OF SURFACE DAMAGE DURING A GEAR TEST LOAD STAGE
- 6 CONCLUSION
- ACKNOWLEDGMENTS
- Restructuration of micro-topography of 2-D tooth surface including static transmission errors
- ABSTRACT
- 1 INTRODUCTION
- 2 MICRO-TOPOGRAPHY OF 2-D TOOTH SURFACE
- 3 METHOD OF CALCULATING STATIC TRANSMISSION ERRORS (STE)
- 4 COUPLING OF MICRO-TOPOGRAPHY OF 2-D TOOTH SURFACE AND STE
- 5 CONCLUSIONS
- ACKNOWLEDGMENTS
- Quality and surface of gears manufactured by free form milling with standard tools
- Session 17: Gear Design (III)
- Synthesis of the base curves of non-circular gears via the return circle
- ABSTRACT
- 1 INTRODUCTION
- 2 CONJUGATE PROFILES GENERATION AND RETURN CIRCLE
- 3 THE WORK OF ALLIEVI ON THE RETURN CIRCLE
- 4 BASE CIRCLE OF INVOLUTE CIRCULAR GEARS
- 5 BASE CURVES OF INVOLUTE NON-CIRCULAR GEARS
- CONCLUSIONS
- Integrated design of spiral bevel gear with low sensitivity and high contact ratio
- ABSTRACT
- 1 INTRODUCTION
- 2 TOOTH CONTACT ANASYSIS ALGORITHM WITH CONSIDERATION OF DISLOCATIONS (ETCA)
- 2.2 Tooth contact analysis considered dislocations (ETCA) [ 8 ]
- 3. SYNTHESIS OPTIMIZATION CONSIDERED DISLOCATIONS
- 4 RESULTS AND ANALYSIS
- 5 CONCLUSIONS
- An approach to transmission configuration in helicopter preliminary design
- ABSTRACT
- 1 INTRODUCTION
- 2 CONFIGURATION DESIGN
- 3 SPATIAL SKELETON DESIGN AND STRUCTURE DESIGN
- 4 DESIGN EXAMPLE
- 5 CONCLUSIONS
- Study on orthogonal variable transmission ratio face gear drive
- ABSTRACT
- 1 INTRODUCTION
- 2 DESIGN OF THE FACE GEAR
- 3 THE SIMULATING DESIGN AND MANUFACTURING
- 4 MANUFACTURING AND EXPERIMENTAL
- 5 CONCLUSION
- 6 ACKNOWLEDGEMENTS
- Synthesis of the base curves of non-circular gears via the return circle
- Session 18: Gear Dynamics (I)
- A torsional dynamic model of multi-stage geared systems submitted to internal and external excitations
- ABSTRACT
- 1 INTRODUCTION
- 2 STATE OF REFERENCE - RIGID-BODY MOTIONS
- 3 CHARACTERISTIC PERIODS AND MESH PHASINGS
- 4 TORSIONAL DYNAMIC MODEL OF MULTI-STAGE IDLER GEARS
- 5 APPLICATIONS
- 6 CONCLUSION
- Study on load-related dynamic behavior of helical gears
- ABSTRACT
- 1 INTRODUCTION
- 2 MODELING
- 3 RESULTS AND DISCUSSION
- 4 CONCLUSIONS
- ACKNOWLEDGEMENT
- Optimum profile modifications for the minimization of dynamic transmission error
- 1 INTRODUCTION
- 2 VALIDATION OF THE GEAR DYNAMICS MODEL USED FOR DTE OPTIMIZATION
- 3 DESCRIPTION OF MDOF MODEL USED IN OPTIMIZATION STUDIES
- 4 OPTIMIZATION
- 5 CONCLUSIONS
- Dynamic analysis of high power gear transmission system in bucket wheel excavator
- ABSTRACT
- 1 INTRODUCTION
- 2 MODEL AND EQUATION OF MOTION
- 3 NUMERICAL SIMULATION
- 4 CONCLUSION
- A torsional dynamic model of multi-stage geared systems submitted to internal and external excitations
- Session 19: Power Losses – Efficiency (I)
- Analysis of no-load dependent power losses in a planetary gear train by using thermal network method
- ABSTRACT
- 1 INTRODUCTION
- 2 EXPERIMENTAL DEVICE
- 3 THERMAL NETWORK
- 4 MODEL VALIDATION
- 5 NO-LOAD DEPENDENT POWER LOSSES DISTRIBUTION
- 6 CONCLUSION
- A methodology to predict power losses of planetary gear sets
- ABSTRACT
- 1 INTRODUCTION
- 2 POWER LOSS PREDICTION METHODOLOGY
- 3 COMPARISON TO EXPERIMENTS
- 4 PLANETARY GEAR SET POWER LOSS COMPONENTS
- 5 CONCLUSIONS
- Power loss in a planetary gearbox
- ABSTRACT
- 1 INTRODUCTION
- 2 WIND TURBINE GEAR OILS
- 3 GEARBOX TEST RIG
- 4 PLANETARY GEARBOX
- 5 EXPERIMENTAL TESTS
- 6 POWER LOSS MODEL
- 7 NUMERICAL RESULTS
- 8 CONCLUSIONS
- ACKNOWLEDGEMENTS
- Power analysis of two-dof epicyclic gear transmission and experimental validation
- ABSTRACT
- 1 INTRODUCTION
- 2 BACKGROUND THEORIES
- 3 ANALYSIS OF PROTOTYPE
- 4 EXPERIMENTAL RESULTS AND COMPARISON
- 5 CONCLUSIONS
- APPENDICES
- Analysis of no-load dependent power losses in a planetary gear train by using thermal network method
- Session 20: Durability – Fatigue (I)
- Some theoretical and simulation results on the study of the tooth flank breakage in cylindrical gears
- ABSTRACT
- 1 INTRODUCTION
- 2 DESCRIPTION OF THE CALCULATION METHOD
- 3 APPLICATION
- 4 CONCLUSION
- Tooth flank fracture – basic principles and calculation model for a sub surface initiated fatigue failure mode of case hardened gears
- ABSTRACT
- 1 INTRODUCTION
- 2 FAILURE MECHANISM OF TOOTH FLANK FRACTURE
- 3 INFLUENCE FACTORS ON THE FAILURE TYPE TOOTH FLANK FRACTURE
- 4 CALCULATION MODEL
- 5 CONCLUSIONS
- Determination of bending strength of sintered spur gear made of SINT D30 powder metal
- ABSTRACT
- 1 INTRODUCTION
- 2 FEM MODEL
- 3 EXPERIMENTAL TESTING
- 4 RESULTS
- 5 PRELIMINARY TESTING
- 6 DISCUSSION AND CONCLUSIONS
- From failure analysis to power transmission design
- ABSTRACT
- 1 INTRODUCTION
- 2 FIRST PART OF EXPERTISE
- 3 SECOND PART OF EXPERTISE
- 4 DECISIONS
- 5 TOOTH FLANK MODIFICATIONS OF PTI GEARBOX
- 6 CONTROLS AFTER MODIFICATIONS
- 7 SYNTHESIS
- Some theoretical and simulation results on the study of the tooth flank breakage in cylindrical gears
- Session 21: Gear Lubrication (I)
- FZG gearboxes lubricated with different formulations of polyalphaolefin wind turbine gear oils
- ABSTRACT
- 1 INTRODUCTION
- 2 WIND TURBINE GEAR OILS
- 3 TEST RIG
- 4 DRIVE AND TEST GEARBOXES
- 5 TEST PROCEDURE
- 6 EXPERIMENTAL RESULTS
- 7 GEARBOXES EFFICIENCY
- 8 TORQUE LOSS MODEL
- 9 COEFFICIENT OF FRICTION IN MESHING GEARS
- CONCLUSIONS
- ACKNOWLEDGEMENTS
- Aspects of lubrication at the wave generator - flexspline interface in strain wave gearing units
- ABSTRACT
- NOTATION
- 1 INTRODUCTION
- 2 CONING - ITS FORMATION AND VARIATIONS AT WG-FS INTERFACE OF HD
- 3 HYDRODYNAMIC LUBRICATION EQUATION SUITABLE FOR WG-FS INTERFACE
- 4 DERIVATION OF LUBRICATION CHARACTERISTICS PARAMETERS
- 5 CONCLUDING REMARKS
- ACKNOWLEDGEMENT
- Transient EHL analysis of helical gears
- 1 ABSTRACT
- 2 INTRODUCTION
- 3 EHL MODELLING OF HELICAL GEAR CONTACT
- 4 RESULTS
- 5 CONCLUSIONS
- 6 ACKNOWLEDGEMENTS
- A discussion on feeding cooler lubricant to the mesh exit region of a helical gear pair based on flow visualization experiments
- ABSTRACT
- 1 INTRODUCTION
- 2 EXPERIMENTAL CONDITIONS AND METHODS
- 3 SUMMARY OF FLUID MOVEMENT OBSERVATION
- 4 DISCUSSIONS
- 5 SUMMARY
- ACKNOWLEDGEMENTS
- FZG gearboxes lubricated with different formulations of polyalphaolefin wind turbine gear oils
- Session 22: Gear Dynamics (II)
- Dynamic stress recovery in gear train simulations using elastic multibody systems
- ABSTRACT
- 1 STRESS CALCULATIONS IN GEARS
- 2 MODELLING APPROACH
- 3 EMBS SIMULATIONS AND STRESS CALCULATIONS
- 4 SUMMARY
- Impact of indexing errors on spur gear dynamics
- ABSTRACT
- 1 INTRODUCTION
- 2 DYNAMIC MODEL FORMULATION
- 3 EXPERIMENTAL TRANSMISSION ERROR MEASUREMENTS
- 4 RESULTS AND DISCUSSION
- 5 CONCLUSIONS
- Comparative analysis of the hypoid geared rotor system dynamics applying dissimilar tooth meshing formulations
- ABSTRACT
- 1 INTRODUCTION
- 2 MESH MODELS
- 3 HYPOID GEARED ROTOR SYSTEM DYNAMICS
- 4 CONCLUSION
- Dynamic stress recovery in gear train simulations using elastic multibody systems
- Session 23: Power Losses – Efficiency (II)
- Study of the influence of the design parameters on the efficiency of spur gears
- ABSTRACT
- 1 INTRODUCTION
- 2 DESCRIPTION OF THE MODEL OF EFFICIENCY
- 3 INFLUENCE OF THE DESIGN PARAMETERS
- 4 CONCLUSIONS
- ACKNOWLEDGMENT
- Effect of assembly errors in back-to-back gear efficiency testing
- ABSTRACT
- 1 INTRODUCTION
- 2 METHOD AND MATERIALS
- 3 RESULTS
- 4 DISCUSSION
- 5 CONCLUSIONS
- Efficiency of a cycloid reducer
- ABSTRACT
- 1 INTRODUCTION
- 2 CYCLOID REDUCER
- 3 RESULTS
- 4 CONCLUSIONS
- Study of the influence of the design parameters on the efficiency of spur gears
- Session 24: Durability – Fatigue (II)
- Load stresses and residual stresses in the tooth interior
- ABSTRACT
- 1 INTRODUCTION
- 2 SIMULATION OF LOAD STRESSES
- 3 RESIDUAL STRESSES
- 4 CONCLUSIONS
- Development of a granular cohesive model for Rolling Contact Fatigue analysis: influence of numerical parameters
- ABSTRACT
- 1 INTRODUCTION
- 2 GRANULAR COHESIVE FINITE ELEMENT MODEL
- 3 COHESIVE ELEMENT NUMERICAL BEHAVIOR ANALYSIS
- 4 PRELIMINARY RESULTS AND INFLUENCE OF DAMAGE MODELING
- CONCLUSION
- Crush of wear debris by tooth engagement and tooth flank damage
- 1 INTRODUCTION
- 2 OBVIOUS TRACE OF CRUSH OF FOREIGN OBJECTS
- 3 PECULIAR TOOTH FLANK FAILURE
- 4 CRUSH OF WEAR DEBRIS
- 5 OUTLOOK OF TOOTH FLANK AFTER CRUSHING WEAR DEBRIS
- 6 INFLUENCE OF SIZE AND HARDNESS OF WEAR DEBRIS
- 7 PROCESS OF DAMAGE CONCERNING CRUSH OF WEAR DEBRIS
- 8 CONCLUSIONS
- ACKNOWLEDGEMENT
- Root stresses and bending fatigue strength of thin-rimmed helical gears (helix angle β 0 = 10, 20 and 30º)
- 1 INTRODUCTION
- 2 EXPERIMENTAL PROCEDURE AND APPARATUS
- 3 EXPERIMENTAL RESULTS AND DISCUSSIONS
- 4 CONCLUSIONS
- ACKNOWLEDGEMENT
- Load stresses and residual stresses in the tooth interior
- Session 25: Gear Design (IV)
- High-conforming gearing: Kinematics and geometry
- ABSTRACT
- 1 INTRODUCTION
- 2 KINEMATICS AND GEOMETRY OF HIGH-CONFORMING GEARING: - I
- 3 NOVIKOV BOUNDARY CIRCLE
- 4 KINEMATICS AND GEOMETRY OF HIGH-CONFORMING GEARING: - II
- 5 FUNDAMENTAL DESIGN PARAMETERS OF HIGH-CONFORMING GEARING
- 6 POSSIBLE TOOTH GEOMETRIES IN HIGH-CONFORMING GEARING
- 7 CRITICAL DEGREE OF CONFORMITY AT A POINT OF CONTACT OF THE TOOTH FLANKS IN HIGH-CONFORMING GEARING
- 8 ON MACHINING GEARS FOR HIGH-CONFORMING GEARING
- CONCLUSION
- A design guide for very small power transmission gears considering tooth surface strength and manufacturing cost
- ABSTRACT
- 1 INTRODUCTION
- 2 NONLINEAR SIMULATION MODEL
- 3 SPECIFICATIONS OF ANALYSED OBJECTS
- 4 CALCULATED RESULTS AND CONSIDERATIONS
- 5 EQUATION FOR COST ESTIMATION
- 6 GESIGN GUIDE CONSIDERING TOOTH STRENGTH AND MANUFACTURING COST
- 7 CONCLUSION
- ACKNOWLEDGMENTS
- How to get most realistic efficiency calculation for gearboxes?
- 1 INTRODUCTION
- 2 APPLICATION OF THERMAL RATING FOR INDUSTRIAL GEARBOXES
- 3 EFFICIENCY CALCULATION OF AUTOMOTIVE TRANSMISSIONS
- 4 SUMMARY
- High-conforming gearing: Kinematics and geometry
- Session 26: Gear Dynamics (III)
- A simplified 3D dynamic model of helical and double-helical planetary gears to study the influence of some usual position and geometrical errors
- ABSTRACT
- 1 INTRODUCTION
- 2PLANETARY GEAR MODEL
- 3 DYNAMIC RESULTS
- 4 CONCLUSION
- 5 ACKNOWLEDGEMENT
- The analysis of dynamic load coefficients of double-helical planetary gear sets
- ABSTRACT
- 1 INTRODUCTION
- 2 DYNAMIC MODEL AND EQUATIONS
- 3 RESULTS AND ANALYSIS
- 4 CONCLUSION
- Back to back planetary gearbox: Influence of non-stationary operating conditions
- ABSTRACT
- 1 INTRODUCTION
- 2 DESCRIPTION OF THE TEST BENCH
- 3 NUMERICAL MODEL
- 4 NUMERICAL SIMULATIONS
- CONCLUSION
- ACKNOWLEDGEMENTS
- A simplified 3D dynamic model of helical and double-helical planetary gears to study the influence of some usual position and geometrical errors
- Session 27: Precision
- Study on evaluation system of gear accuracy based on statistical analysis
- ABSTRACT
- 1 INTRODUCTION
- 2 THE PRINCIPLE OF GEAR ACCURACY EVALUATION BASED ON STATISTICAL ANALYSIS
- 3 DESIGN OF THE DIGITAL SIMULATION EXPERIMENTS
- 4 EXPERIMENT DATA AND ANALYSIS
- 5 CONCLUSION
- ACKNOWLEDGEMENT
- Robust pre-synchronization in heavy truck transmissions
- ABSTRACT
- 1 INTRODUCTION
- 2 THE SYNCHRONISATION PROCESS
- 3 SIMULATION MODEL
- 4 RESULTS
- 5 DISCUSSION
- 6 CONCLUSION AND FUTURE WORK
- 7 ACKNOWLEDGMENTS
- Identification of radii of tooth root and pitch deviations from whole circumference scanning measurement of cylindrical gears
- ABSTRACT
- 1 INTRODUCTION
- 2 CONSTRUCTION OF DEVELOPED GMM
- 3 MEASUREMENT STRATEGY AND PROCEDURE
- 4 RESULTS AND DISCUSSIONS
- 5 CONCLUSIONS
- Study on evaluation system of gear accuracy based on statistical analysis
- Session 28: Durability – Fatigue (III)
- Online and real-time damage calculation in automotive transmissions Application to remaining service life estimation
- 1 INTRODUCTION
- 2 MODEL
- 3 SIMULATIONS AND RESULTS
- 4 PERSPECTIVES
- 5 CONCLUSION
- Effects of case depth, face width and intergranular oxidation on bending fatigue strength of case-carburized SNC815 and SCM415 steel spur gears
- 1 INTRODUCTION
- 2 EXPERIMENTAL PROCEDURE AND APPARATUS
- 3 EXPERIMENTAL RESULTS AND DISCUSSIONS
- 4 CONCLUSIONS
- Determination of maximum loads for drivetrain components in thrusters using flexible multibodysystem models
- ABSTRACT
- 1 INTRODUCTION
- 2 BASICS OF DRIVETRAIN SIMULATION
- 3 ASSEMBLY OF THE SIMULATION MODEL OF THE THRUSTER
- 4 ANALYSIS OF THE THRUSTER DRIVETRAIN IN THE FREQUENCY DOMAIN
- 5 ANALYSIS OF THE THRUSTER DRIVETRAIN IN THE TIME DOMAIN
- 6 CONCLUSIO
- Online and real-time damage calculation in automotive transmissions Application to remaining service life estimation
- Edition: 1
- Published: September 18, 2014
- Imprint: Chandos Publishing
- Language: English
PV
Philippe Velex
INSA Lyon, France
Affiliations and expertise
INSA Lyon is a top Engineering University in Europe. LaMCoS is associated with the French National Centre for Research (UMR CNRS 5259) and one of the leading research laboratories in Mechanical Engineering. In cooperation with ECAM Lyon, INSA Lyon is the most important French research centre on Mechanical Transmissions.Read International Gear Conference 2014: 26th-28th August 2014, Lyon on ScienceDirect