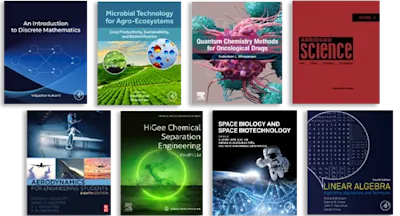
Industrial Cutting of Textile Materials
- 1st Edition - April 19, 2012
- Imprint: Woodhead Publishing
- Author: Ineta Vilumsone-Nemes
- Language: English
- Hardback ISBN:9 7 8 - 0 - 8 5 7 0 9 - 1 3 4 - 5
- eBook ISBN:9 7 8 - 0 - 8 5 7 0 9 - 5 5 6 - 5
A cutting room is a separate area in a clothing manufacturer where garment components are cut out. The accuracy and efficiency of cutting room operations is critical to all… Read more
Purchase options
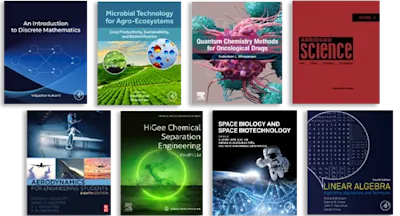
- Summarises good practice in cutting room operations
- Reviews initial steps such as unloading, sorting and quality control of materials and discusses subsequent operations from lay planning and marker making to fusing of cut components and final work operations
- Includes coverage of more intricate fabrics such as striped fabrics and fabrics with check, motif and border patterns, narrow lace and pile fabrics
About the author
Woodhead Publishing Series in Textiles
Preface
Chapter 1: Introduction to cutting room operations in garment manufacture
Abstract:
1.1 Introduction
1.2 Storage, registration and inspection of materials
1.3 Lay planning and marker making processes
1.4 The fabric spreading process
1.5 The fabric cutting process
1.6 Fusing cut components
1.7 Final stages of cutting operations
Chapter 2: Initial preparation and quality control of textile materials in textile cutting operations
Abstract:
2.1 Introduction
2.2 Unloading delivered textile materials
2.3 Sorting and counting the delivered textile materials
2.4 Storage of textile materials in a warehouse
2.5 Quality control of stored textile materials
2.6 Influence of textile faults on the industrial manufacture of garments
Chapter 3: Lay planning and marker making in textile cutting operations
Abstract:
3.1 Introduction
3.2 Basic principles of the lay planning process
3.3 Automation of the lay planning process and cutting room operations
3.4 General characteristics of the marker making process
3.5 Influence of textile material properties on the marker making process
3.6 Placing pattern pieces of fusible components in a marker
3.7 Creation of interlining markers
3.8 Automated marker making process
Chapter 4: Principles and methods of textile spreading
Abstract:
4.1 Introduction
4.2 General characteristics of the spreading process
4.3 Fabric spreading modes and their application
4.4 Dealing with different kinds of spread
4.5 Fabric quality issues
Chapter 5: Manual spreading of textile materials
Abstract:
5.1 Introduction
5.2 Characteristics of the manual spreading process
5.3 Manual spreading process modes
5.4 Disadvantages of the manual spreading process
5.5 Equipment for manual spreading
Chapter 6: Automated spreading of textile materials
Abstract:
6.1 Introduction
6.2 The spreading table
6.3 The spreading machine and its main parts
6.4 Control features in the spreading process
6.5 Semi-automated and fully automated spreading processes
6.6 Spreading machine for tubular materials
6.7 Spreading modes in the automated spreading process
6.8 Automated fabric fault registration and management systems
6.9 Comparing manual and automated spreading processes
Chapter 7: The manual textile cutting process
Abstract:
7.1 Introduction
7.2 Characteristics of the manual cutting process
7.3 Notches and cloth marking drills
7.4 Accuracy problems in the manual cutting process
Chapter 8: Manual cutting equipment in textile cutting operations
Abstract:
8.1 Introduction
8.2 The straight knife cutting machine
8.3 The round (rotary) knife cutting machine
8.4 The small round knife cutting machine
8.5 The band knife cutting machine
8.6 The fabric drilling machine
8.7 The hot notching machine
Chapter 9: Automated cutting of textile materials
Abstract:
9.1 Introduction
9.2 Automated cutting systems and their main parts
9.3 Automated knife cutting systems
9.4 Knife cutting systems for textiles
9.5 Automated laser cutting systems
9.6 Automated water-jet cutting systems
9.7 Automated plasma cutting systems
9.8 Automated ultrasonic cutting systems
9.9 Multi-purpose cutters
Chapter 10: Placement of equipment in the textile cutting room
Abstract:
10.1 Introduction
10.2 Placement of manual spreading and cutting equipment/workstations in the cutting room
10.3 Placement of automated spreading and cutting equipment/workstations in the cutting room
10.4 Lay storage systems for automated cutting processes
Chapter 11: Fusing cut textile components
Abstract:
11.1 Introduction
11.2 General characteristics of interlinings
11.3 Fusing presses and their main parts
11.4 Fusing quality problems and their prevention
Chapter 12: Final work operations in the cutting process for textiles
Abstract:
12.1 Introduction
12.2 Causes of quality problems in cut components
12.3 Quality control of cut components
12.4 Re-cutting faulty components
12.5 Numbering cut components
12.6 Sorting and bundling cut components
Chapter 13: Manual marker making, spreading and cutting of striped fabrics
Abstract:
13.1 Introduction
13.2 Marker making for styles made from materials with stripes
13.3 Spreading and cutting process
Chapter 14: Manual marker making, spreading and cutting materials with check patterns
Abstract:
14.1 Introduction
14.2 Marker making for styles from materials with check patterns
14.3 The spreading and cutting processes
Chapter 15: Manual marker making, spreading and cutting fabrics with motif patterns
Abstract:
15.1 Introduction
15.2 Marker making for styles made from materials with motif pattern
15.3 The spreading and cutting processes
Chapter 16: Manual marker making, spreading and cutting fabrics with border patterns
Abstract:
16.1 Introduction
16.2 Marker making for styles made from materials with a border pattern
16.3 The spreading and cutting processes
Chapter 17: Manual marker making, spreading and cutting narrow lace
Abstract:
17.1 Introduction
17.2 General characteristics of narrow lace
17.3 Characteristics of lingerie components cut from lace
17.4 Placement of the pattern on the components
17.5 Marker making styles directly on fabric
17.6 The spreading process
17.7 The cutting process
Chapter 18: Spreading and cutting fabrics with pile
Abstract:
18.1 Introduction
18.2 Marker making for styles made from materials with pile
18.3 Spreading and cutting fabrics with low-cut pile
18.4 Spreading and cutting fabrics with high-cut pile
Chapter 19: Problems in spreading and cutting intricate fabrics and methods to prevent them
Abstract:
19.1 Introduction
19.2 Marker making directly on a particular pattern
19.3 Precise coordination of patterns in all plies of a spread
19.4 Pin tables to prevent displacement of multi-ply spreads
19.5 Automated systems to match patterns of intricate fabrics
Glossary
Index
- Edition: 1
- Published: April 19, 2012
- Imprint: Woodhead Publishing
- Language: English
IV