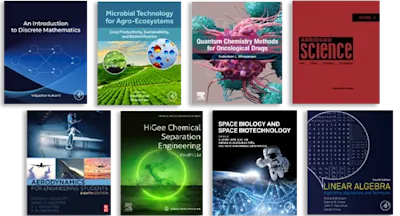
Industrial Catalytic Processes for Fine and Specialty Chemicals
- 1st Edition - April 27, 2016
- Editors: Sunil S Joshi, Vivek V. Ranade
- Language: English
- Hardback ISBN:9 7 8 - 0 - 1 2 - 8 0 1 4 5 7 - 8
- eBook ISBN:9 7 8 - 0 - 1 2 - 8 0 1 6 7 0 - 1
Industrial Catalytic Processes for Fine and Specialty Chemicals provides a comprehensive methodology and state-of-the art toolbox for industrial catalysis. The book begins by… Read more
Purchase options
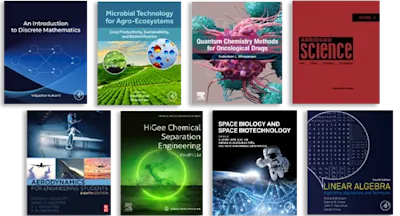
Industrial Catalytic Processes for Fine and Specialty Chemicals
provides a comprehensive methodology and state-of-the art toolbox for industrial catalysis. The book begins by introducing the reader to the interesting, challenging, and important field of catalysis and catalytic processes.The fundamentals of catalysis and catalytic processes are fully covered before delving into the important industrial applications of catalysis and catalytic processes, with an emphasis on green and sustainable technologies. Several case studies illustrate new and sustainable ways of designing catalysts and catalytic processes.
The intended audience of the book includes researchers in academia and industry, as well as chemical engineers, process development chemists, and technologists working in chemical industries and industrial research laboratories.
- Discusses the fundamentals of catalytic processes, catalyst preparation and characterization, and reaction engineering
- Outlines the homogeneous catalytic processes as they apply to specialty chemicals
- Introduces industrial catalysis and catalytic processes for fine chemicals
- Includes a number of case studies to demonstrate the various processes and methods for designing green catalysts
Industrial and academic chemists, and chemical engineers and technologists working in the area of process development using catalysis
Proposed Contents
Preface
Chapter 1: Catalysis & Catalytic Processes
Part 1: Fundamentals
Chapter 2:
Homogenous catalysis2.1 Introduction
2.2 Bonding to transition metal surfaces
2.3 Chemical bonding in organometallic complexes
2. 4 Steps in organometallic complex formation
2.5 Catalytic steps in homogeneous catalysis
2.6 Stability of homogeneous catalyst complexes
Chapter 3: Heterogeneous catalysis
3.1 Introduction
3.2 Catalytic steps in heterogeneous catalysis
3.3 Synthesis & activation of catalysts
3.4 Characterization of catalysts
3.5 Catalyst deactivation and regeneration/ disposal
Chapter 4: Catalyst synthesis and characterization
4.1 Bulk catalysts
4.2 Catalyst supports
4.3 Characterization
4.3.1 Physical properties
4.3.2 Chemical properties
Chapter 5: Catalytic Reaction Engineering
5.1 Selection of reaction media
5.2 Reaction kinetics
5.3 Reaction engineering
5.4 Reactor engineering
Part 2: Applications
Chapter 6: Catalysis for fine and Specialty Chemicals
6.1 Introduction
6.2 Solid acid catalysis
6.3 Solid base catalysis
6.4 Asymmetric hydrogenations
6.5 Catalytic oxidations
6.6 Catalytic hydroxylation
Chapter 7: Fine chemical synthesis and future perspectives
7.1 Hydrogenation ex-situ methods
7.2 Asymmetric synthesis
7.3 Selective hydrogenation
7.4 In-situ hydrogenation
7.5 Simple hydrogenation in the area of energy sector
Chapter 8: Use of Catalysis for API manufacturing
8.1 API regulatory requirement
8.2 Significance of heterogeneous catalysis in API
8.3 Scale-up and process optimization in API manufacturing
8.4 Most frequently employed catalysts
8.5 Case studies
Chapter 9: Catalysis for perfumery chemicals
9.1 Application of Heterogeneous catalysts
9.2 Isomerization reaction in perfumery chemicals
9.3 Hydrogenation reactions in perfumery chemicals
9.4 Hydroformylation reactions in perfumery chemicals
Chapter 10: Use of ion exchange resins in fine and specialty chemicals
10.1 Classification on ion exchange resins
10.2 Characteristics of ion exchange catalysts
10.3 Matrix Diffusion
10.4 Effect of Matrix Enhancement
10.5 Effect of Distribution Constant
10.6 Applications of ion exchange resins in fine and specialty chemicals
Chapter 11: Catalysis for Renewable chemicals manufacture
11.1 Renewable Chemicals: Definition and introduction
11.2 Feedstock
11.3 Selection of biochemicals
11.4 Bio-catalysis
11.5 Chemo catalysis
11.6 Conclusion and future prospects
Chapter 12: Carbonylations & Hydroformylations
12.1 Homogeneous catalysis
12.2 Biphasic catalysis
12.3 Heterogenization of homogeneous catalysts
12.4 Use of ionic liquids in hydroformylation reactions
Chapter 13: Carbamates
13.1 Conventional routes for industrially important carbamates
13.2 Greener routes for carbamates
13.3 case studies
Chapter 14: Challenges of Scale-up in Specialty Chemicals
14.1 Applications of butylaterd chemicals
14.2 Catalysis in butylated chemicals
14.3 Application of Organo tin compounds
14.4 Catalysis in organo tin chemicals
Chapter 15: Epilogue
Notations and abbreviations
References & suggested literature
Index
- Edition: 1
- Published: April 27, 2016
- Language: English
SJ
Sunil S Joshi
VR
Vivek V. Ranade
Dr Vivek Ranade is a Bernal Chair Professor of Process Engineering at Bernal Institute, University of Limerick, Ireland. He leads ‘Multiphase Reactors and Process Intensification’ group. Vivek and his group use experiments, computational flow modelling, population balance models and machine learning to generate new insights in multiphase flows, multiphase reactors, and process intensification. The group is developing novel fluidic devices, intensified processes and ‘factory in a box’ platforms for decentralised manufacturing, personalised products, responsible resource usage, decarbonisation as well as mitigation and valorisation of waste.