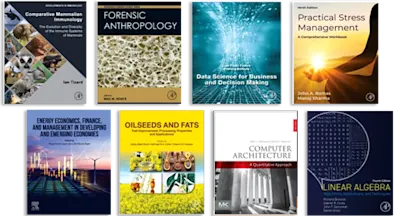
Improve
The Next Generation of Continuous Improvement for Knowledge Work
- 1st Edition - June 13, 2020
- Imprint: Butterworth-Heinemann
- Author: George Ellis
- Language: English
- Paperback ISBN:9 7 8 - 0 - 1 2 - 8 0 9 5 1 9 - 5
- eBook ISBN:9 7 8 - 0 - 1 2 - 8 0 9 7 2 0 - 5
Improve: The Next Generation of Continuous Improvement for Knowledge Work presents lean thinking for professionals, those who Peter Drucker called knowledge workers. It translate… Read more
Purchase options
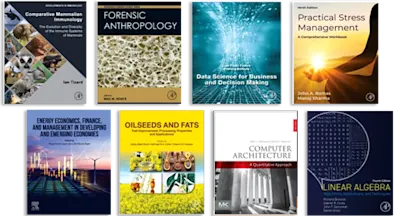
Improve: The Next Generation of Continuous Improvement for Knowledge Work presents lean thinking for professionals, those who Peter Drucker called knowledge workers. It translates the brilliant insights from Toyota’s factory floor to the desktops of engineers, marketers, attorneys, accountants, doctors, managers, and all those who "think for a living." The Toyota Production System (TPS) was born a century ago to an almost unknown car maker who today is credited with starting the third wave of the Industrial Revolution. TPS principles, better known as lean thinking or continuous improvement, are simple: increase customer value, cut hidden waste, experiment to learn, and respect others. As simple as they are, they are difficult to apply to the professions, probably because of the misconception that knowledge work is wholly non-repetitive. But much of our everyday work does repeat, and in great volume: approvals, problem-solving, project management, hiring, and prioritization are places where huge waste hides. Eliminate waste and you delight customers and clients, increase financial performance, and grow professional job satisfaction, because less waste means more success and more time for expertise and creativity.
This book is a valuable resource for leaders of professional teams who want to improve productivity, quality, and engagement in their organizations.
- Experience the proven benefits of continuous improvement
- 40%–70% increase in productivity from professionals and experts
- >85% projects on-time
- Reduce lead time by 50%–90%
- Engagement up and voluntary severance cut >50%
- Dozens of simple visual tools that anyone can implement immediately in their existing framework
- All tools and techniques applicable to both face-to-face and virtual meetings
- Easy-to-understand approach: “simplify, engage, experiment”
- Presented with deep respect for the experts; no “check the box” thinking or overused analogies to the factory floor
Foreword xiii
Endorsements xv
Preface xvii
Acknowledgments xxi
1. 30% of what you think is wrong 1
1.1 A good story 1
1.2 What problem are we trying to solve? 4
1.3 Why is it so hard to get anything done around here? 8
1.4 Six ways this book is unique 11
1.5 Who is this book for? 12
1.6 Structure of the book 12
References 16
2. A brilliant insight 17
2.1 Introduction 17
2.2 The birth of lean thinking 18
2.3 What is knowledge work? 23
2.4 Lean knowledge vs. lean manufacturing 26
2.5 Lean health care 27
2.6 Lean product development 29
2.7 The lean startup 31
2.8 Critical Chain Project Management 33
2.9 Agile software development 34
2.10 Personal experience 36
2.11 Conclusion 37
References 37
3. Creating value from knowledge work 41
3.1 Introduction 41
3.2 A definition of value 41
3.3 Who is the customer to knowledge work? 41
3.4 What is a knowledge organization? 42
3.5 Value 6¼effort 43
3.6 Five facets of value 44
3.7 Conclusion 49
References 49
4. The lean equation 51
4.1 Introduction 51
4.2 Waste is a villain 51
4.3 Effort vs value 54
4.4 Opaque workflows: A place for waste to hide 55
4.5 Cut waste by trying harder? 57
4.6 Three ways to expend effort in knowledge work 58
4.7 Conclusion 63
References 63
5. DIMINISH: Recognizing the 8 Wastes of Knowledge Work 65
5.1 Introduction 65
5.2 The 8 Wastes of lean manufacturing 65
5.3 Waste diminishes value 66
5.4 The 8 Wastes 67
5.5 Discord 68
5.6 Information Friction 69
5.7 More-is-Better Thinking 70
5.8 Inertia to Change 71
5.9 No-Win Contests 72
5.10 Inferior Problem Solving 73
5.11 Solution Blindness 74
5.12 Hidden Errors 75
5.13 Conclusion 76
References 76
6. Simplify, engage, and experiment 77
6.1 Introduction 77
6.2 Simplify workflows 77
6.3 Engage the team 83
6.4 Experiment to learn 90
6.5 Conclusion: Simplify, engage, and experiment. Repeat 105
References 106
7. Reduce Waste #1: Discord 109
7.1 Introduction 109
7.2 The engaging power of diverse thought 110
7.3 Creating highly functional teams 117
7.4 Ego vs confidence 135
7.5 Conclusion 137
References 139
8. Reduce Waste #2: Information Friction 141
8.1 Introduction 141
8.2 Single Point of Truth (SPoT) 142
8.3 Visualization vs narration 146
8.4 Visualization tools 150
8.5 The Canvas View 154
8.6 Hierarchical visualization 161
8.7 Conclusion 162
References 164
9. Reduce Waste #3: More-is-Better Thinking 165
9.1 Introduction 165
9.2 Artifacts vs work 166
9.3 Measure change with the Action Plan 170
9.4 Measure traction with the Test Track 185
9.5 Measure value with the Bowler 189
9.6 The Success Map 195
9.7 The helicopter view 199
9.8 Conclusion 203
References 205
10. Reduce Waste #4: Inertia to Change 207
10.1 Introduction 207
10.2 Change model 207
10.3 Growth through challenge 211
10.4 Change agents, wait-and-see people, and unwilling partners 214
10.5 Conclusion 216
References 218
11. Reduce Waste #5: No-Win Contests 219
11.1 Introduction 219
11.2 Excessive multitasking 220
11.3 Oversubscription: The No-Win Contest collides with More-is-Better
Thinking 221
11.4 Escalation: Guarantor of a winnable contest 224
11.5 Conclusion 226
References 228
12. Reduce Waste #6: Inferior Problem Solving 229
12.1 Introduction 229
12.2 Formal problem solving 230
12.3 Step 1: The organizational need 231
12.4 Step 2: The problem statement 232
12.5 Step 3: Observation and analysis 234
12.6 Step 4: Root cause 245
12.7 Step 5: Countermeasures 245
12.8 Step 6: Success Map 246
12.9 Canvas View 246
12.10 Closing remarks on problem solving 246
12.11 Conclusion 249
References 251
13. Reduce Waste #7: Solution Blindness 253
13.1 Introduction 253
13.2 The falsifiable hypothesis and Solution Blindness 255
13.3 A simple example of Solution Blindness 255
13.4 Value proposition 257
13.5 The Lean Startup and the Minimal Viable Product (MVP) 260
13.6 Conclusion 264
References 266
14. Reduce Waste #8: Hidden Errors 269
14.1 Introduction 269
14.2 Two mindsets 270
14.3 Stop-Fix alarms 271
14.4 Mistake-proofing complements Stop-Fix alarms 282
14.5 Conclusion 286
References 286
15. Standardize workflow 287
15.1 Introduction 287
15.2 Building a foundation 287
15.3 The ground view 292
15.4 The helicopter view 301
15.5 Process robustness 306
15.6 Conclusion 307
References 309
16. Workflow improvement cycle 311
16.1 Introduction 311
16.2 The 8 Wastes 311
16.3 A poorly managed cycle of improvement 311
16.4 Leading improvement cycles 315
16.5 Conclusion 317
References 320
17. Workflow—Checklists and expert rule sets 321
17.1 Introduction 321
17.2 The 8 Wastes 323
17.3 The checklist 324
17.4 The expert rule set 325
17.5 A KWIC for implementing a checklist or expert rule set 328
17.6 Conclusion 328
References 331
18. Workflow—Problem Solve-Select 333
18.1 Introduction 333
18.2 The 8 Wastes 334
18.3 The Solve-Select workflow 335
18.4 The Solve-Select canvas 338
18.5 Knowledge Work Improvement Canvas (KWIC) to adopt
Solve-Select workflow 338
18.6 Conclusion 338
Reference 343
19. Workflow—Visual management for initiatives and projects 345
19.1 Why avoid the Gantt chart? 349
19.2 The Visual Action Plan 351
19.3 The regular team stand-up 354
19.4 A legend for planning and regular execution 355
19.5 Visual Action Plan execution 356
19.6 Running plays in Visual Action Plans 359
19.7 Buffer: Smoothing daily management 363
19.8 Knowledge Work Improvement Canvas (KWIC) for visual
management 363
References 366
20. Workflow—Visual management with buffer 367
20.1 Introduction 367
20.2 The 8 Wastes in unbuffered project schedules 368
20.3 The fever chart 374
20.4 The Project Schedule Canvas 376
20.5 Following a project with the Project Schedule Canvas 383
20.6 Common patterns in the fever chart 392
20.7 The portfolio snapshot fever chart 394
20.8 Creating project management standard work 396
20.9 Knowledge Work Improvement Canvas (KWIC) for visual
management with buffer 398
20.10 Conclusion 398
References 400
21. Workflow—Kanban and Kamishibai: Just-In-Time
Rationalization 401
21.1 Introduction 401
21.2 The 8 Wastes 403
21.3 Ruthless Rationalization 406
21.4 Just-In-Time Rationalization 406
21.5 Kanban Task Management 409
21.6 The Kamishibai board: Smooth flow for regular work 418
21.7 Knowledge Work Improvement Canvas (KWIC) to adopt
Just-In-Time Rationalization 421
21.8 Conclusion 421
References 425
22. Workflow—Putting out “fires” 427
22.1 Introduction 427
22.2 The 8 Wastes 428
22.3 A wasteful workflow 429
22.4 The Ford Eight Disciplines (8D) process 429
22.5 The 8D Canvas: A modified KWIC 432
22.6 The histogram: Systematically tracking recurrencewith cause codes 432
22.7 Conclusion 438
References 438
23. Workflow—Visualizing revenue gaps 439
23.1 Introduction 439
23.2 Problem solving for revenue gaps 440
23.3 The 8 Wastes 441
23.4 The waterfall chart 442
23.5 Revenue gap Knowledge Work Improvement Canvas 447
23.6 Conclusion 447
References 450
24. Workflow—Leadership review of knowledge work 451
24.1 Introduction 451
24.2 The 8 Wastes 452
24.3 A system of barriers to defects 453
24.4 Critical thinking 456
24.5 Critical thinking: Finding the pillars that support value 458
24.6 Bias and critical thinking 459
24.7 Unambiguous requirements 461
24.8 Project review Knowledge Work Improvement Canvas 462
24.9 Conclusion 465
References 465
Index 467
- Edition: 1
- Published: June 13, 2020
- Imprint: Butterworth-Heinemann
- Language: English
GE