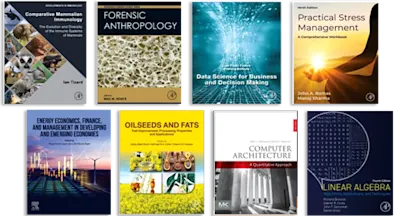
Hydrostatic and Hybrid Bearing Design
- 1st Edition - December 17, 2013
- Imprint: Butterworth-Heinemann
- Author: W B Rowe
- Language: English
- Paperback ISBN:9 7 8 - 1 - 4 8 3 1 - 1 2 1 2 - 1
- eBook ISBN:9 7 8 - 1 - 4 8 3 1 - 4 4 5 4 - 2
Hydrostatic and Hybrid Bearing Design is a 15-chapter book that focuses on the bearing design and testing. This book first describes the application of hydrostatic bearings, as… Read more
Purchase options
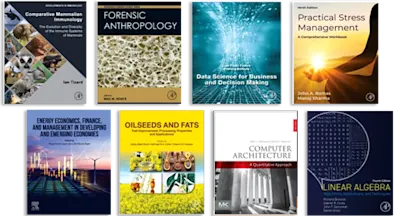
Hydrostatic and Hybrid Bearing Design is a 15-chapter book that focuses on the bearing design and testing. This book first describes the application of hydrostatic bearings, as well as the device pressure, flow, force, power, and temperature. Subsequent chapters discuss the load and flow rate of thrust pads; circuit design, flow control, load, and stiffness; and the basis of the design procedures and selection of tolerances. The specific types of bearings, their design, dynamics, and experimental methods and testing are also shown. This book will be very valuable to students of engineering design and lubrication.
PrefaceUsual Meaning of Symbols1 Application of Hydrostatic Bearings 1.1 Introduction 1.2 What is a Hydrostatic Bearing? 1.3 When Should a Hydrostatic Bearing Be Employed? 1.4 Bearing Selection 1.5 Materials Selection2 Basic Theory Governing Pressure, Flow and Bearing Forces 2.1 Viscosity 2.2 Density: Consistent Units 2.3 Compressibility 2.4 Viscous Flow between Parallel Plates 2.5 Combined Pressure and Velocity-Induced Viscous Flow in a Two-Dimensional Non-Parallel Film 2.6 Flow through Restrictors 2.7 Recess Pressure and Pressure Ratio 2.8 Bearing Load 2.9 Use of Dimensionless Data3 Power, Temperature Rise and Minimum Power 3.1 Pumping Power 3.2 Friction Power 3.3 Total Power and Power Ratio 3.4 Temperature Rise 3.5 Optimization 3.6 Minimum Power for Low-Speed Bearings (K = 0) 3.7 Minimum Power for High-Speed Recessed Bearings 3.8 Optimization of Plain Hybrid Bearings4 Thrust Pads: Load and Flow Rate 4.1 Derivation of Load and Flow Data for Plane Thrust Pads 4.2 Circular Pad Data 4.3 Square Pad Data 4.4 Rectangular Pad Data 4.5 Annular Recess Circular Pad Data 4.6 Conical Pad Data 4.7 Spherical Pad Data 4.8 Multi-Recess Circular Pad Data 4.9 Multi-Recess Rectangular Pad Data 4.10 Data for Rectangular Pad with Radiussed Recess Corners 4.11 Data for Any Shape with Thin Constant Land Width 4.12 Annular Multi-Recess Pad Data5 Circuit Design, Flow Control, Load and Stiffness 5.1 Definition of Bearing Film Stiffness 5.2 Circuit Design and Sealing 5.3 Load and Stiffness of a Capillary-Controlled Pad 5.4 Flow Control Devices 5.5 General Stiffness Law for a Bearing Pad6 The Basis of the Design Procedures and Selection of Tolerances 6.1 Zero or Low-Speed Bearings 6.2 Relationships Affecting Tolerances 6.3 High-Speed Bearings 6.4 BS 4500: Specification for ISO Limits and Fits 6.5 Tolerance Grades for Hydrostatic Bearings7 Plane Hydrostatic Bearings 7.1 Use of the Design Charts 7.2 Choice of Land Width 7.3 Flow Rate 7.4 Load 7.5 Stiffness 7.6 Single Plane Bearings 7.7 Double Plane Bearings Having Equal Opposed Pads 7.8 Double Plane Bearings Having Unequal Opposed Pads 7.9 Complex Arrangements of Plane Pads (Capillary Compensation)8 Partial Hydrostatic Journal Bearings 8.1 Recessed Partial Journal Bearings 8.2 Grooved Partial Journal Bearings9 Recessed Cylindrical Hydrostatic Journal Bearings 9.1 Introduction 9.2 Flow in Hydrostatic Journal Bearings 9.3 Load 9.4 Power and Temperature Rise 9.5 Land Width Ratios and Design Pressure Ratio 9.6 Selection of Tolerances 9.7 Selection of Supply Pressure, Viscosity and Clearance 9.8 Bearing Film Stiffness10 Hydrostatic and Hybrid Plain Journal Bearings 10.1 Introduction 10.2 Selection of Bearing Configuration 10.3 Power Ratio 10.4 Design Pressure Ratio 10.5 Clearance and Clearance Limits 10.6 Load 10.7 Flow Rate 10.8 Power and Temperature Rise11 Combined Journal and Thrust Bearings (The Yates Bearing) 11.1 Introduction 11.2 Principle of Operation 11.3 Basic Parameters 11.4 Design Procedure12 Conical Journal Bearings 12.1 Introduction 12.2 Basic Parameters 12.3 Design Procedure13 Spherical Bearings 13.1 Introduction 13.2 Basic Parameters 13.3 Central Recess Bearing 13.4 Annular Recess Bearing 13.5 Multi-Recess Bearings14 Dynamics 14.1 Introduction 14.2 Static Loading 14.3 Dynamic Loading 14.4 Squeeze Damping 14.5 Compressibility 14.6 Dynamic Model of a Thrust Pad 14.7 Thrust Pad with Thin Lands 14.8 Journal Bearings15 Experimental Methods and Testing 15.1 Introduction 15.2 Flat Pad Rig 15.3 Cylindrical Journal Bearing RigAppendix A Design Procedures and Examples A1 Single Plane Pads A2 Equal Opposed Pads A3 Unequal Opposed Pads A4 Journal Bearings (General Procedure) A5 Complex Arrangements of Plane Pads A6 Capillary Restrictor A7 Orifice Restrictor A8 Slot Restrictor (Single and Double Entry)Appendix B References and Design Bibliography B1 References B2 Design BibliographyIndex
- Edition: 1
- Published: December 17, 2013
- Imprint: Butterworth-Heinemann
- Language: English
Read Hydrostatic and Hybrid Bearing Design on ScienceDirect