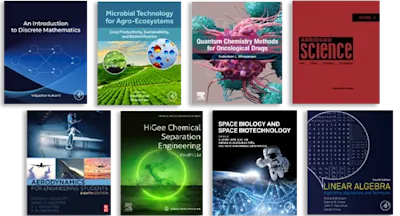
Hydrostatic, Aerostatic and Hybrid Bearing Design
- 1st Edition - October 30, 2018
- Author: W. Brian Rowe
- Language: English
- Hardback ISBN:9 7 8 - 0 - 1 2 - 3 9 6 9 9 4 - 1
- Paperback ISBN:9 7 8 - 0 - 1 2 - 8 1 0 3 3 5 - 7
- eBook ISBN:9 7 8 - 0 - 1 2 - 3 9 7 2 3 9 - 2
Solve your bearing design problems with step-by-step procedures and hard-won performance data from a leading expert and consultant Compiled for ease of use in practical design… Read more
Purchase options
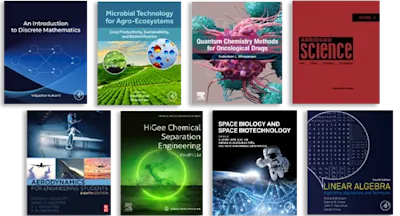
Solve your bearing design problems with step-by-step procedures and hard-won performance data from a leading expert and consultant
Compiled for ease of use in practical design scenarios, Hydrostatic, Aerostatic and Hybrid Bearing Design provides the basic principles, design procedures and data you need to create the right bearing solution for your requirements.
In this valuable reference and design companion, author and expert W. Brian Rowe shares the hard-won lessons and figures from a lifetime’s research and consultancy experience. Coverage includes:
- Clear explanation of background theory such as factors governing pressure, flow and forces, followed by worked examples that allow you to check your knowledge and understanding
- Easy-to-follow design procedures that provide step-by-step blueprints for solving your own design problems
- Information on a wide selection of bearing shapes, offering a range and depth of bearing coverage not found elsewhere
- Critical data on optimum performance from load and film stiffness data to pressure ratio considerations
- Operating safeguards you need to keep in mind to prevent hot-spots and cavitation effects, helping your bearing design to withstand the demands of its intended application
Aimed at both experienced designers and those new to bearing design, Hydrostatic, Aerostatic and Hybrid Bearing Design provides engineers, tribologists and students with a one-stop source of inspiration, information and critical considerations for bearing design success.
- Structured, easy to follow design procedures put theory into practice and provide step-by-step blueprints for solving your own design problems.
- Covers a wide selection of bearing shapes, offering a range and depth of information on hydrostatic, hybrid and aerostatic bearings not found elsewhere.
- Includes critical data on optimum performance, with design specifics from load and film stiffness data to pressure ratio considerations that are essential to make your design a success.
Designers and engineers involved in mechanical and machinery design; Tribologists and lubrication engineers; Engineering undergraduates studying tribology and bearing design
Preface
Usual Meaning of Symbols
Chapter 1. Application
1.1 Introduction
1.2 What are Hydrostatic, Hybrid, and Aerostatic Bearings?
1.3 When are Hydrostatic, Hybrid, and Aerostatic Bearings Employed?
1.4 Bearing Selection
1.5 Bearing Categories
1.6 Commercial Applications
1.7 Materials and Manufacture
1.8 Aerostatic Bearings
1.9 How to Read and Use the Book
References
Chapter 2. Basic Flow Theory
2.1 Introduction
2.2 Viscosity
2.3 Density and Consistent Units
2.4 Compressibility
2.5 Viscous Flow Between Parallel Plates
2.6 Combined Pressure- and Velocity-Induced Viscous Flow in a Two-Dimensional Nonparallel Film
2.7 Flow Through Restrictors
2.8 Recess Pressure and Pressure Ratio
2.9 Bearing Load
2.10 Use of Normalized Data
2.11 Aerostatic Bearings—Summary of Relationships
References
Further Reading
Chapter 3. Power, Temperature Rise, and Shape Optimization
Summary of Key Design Formulae
3.1 Introduction
3.2 Pumping Power Hp
3.3 Friction Power Hf
3.4 Power Ratio K
3.5 Temperature Rise ΔT
3.6 Minimum Power as an Optimization Criterion
3.7 Minimum Power for Low-Speed Bearings (K = 0)
3.8 Minimum Power for High-Speed Recessed Bearings
3.9 Speed Parameter Sh and Optimum Value Sho
3.10 Optimization of Plain Nonrecessed Hybrid Bearings
References
Chapter 4. Pads
Summary of Key Design Formulae
4.1 Pad Shapes and Shape Factors
4.2 Virtual Recesses and Dispersion Losses
4.3 Circular Pads
4.4 Square Pad Data
4.5 Rectangular Pad Data
4.6 Annular Recess Circular Pad Data
4.7 Conical Pad Data
4.8 Spherical Pad Data
4.9 Multi-Recess Circular Pad Data
4.10 Multi-Recess Rectangular Pad Data
4.11 Data for Rectangular Pad with Radiussed Recess Corners
4.12 Data for Any Shape with Thin Constant Land Width
4.13 Annular Multi-Recess Pad Data
Chapter 5. Flow Control and Restrictors
Summary of Key Design Formulae
5.1 Introduction
5.2 Bearing Film Stiffness
5.3 Hydrostatic Circuit Design and Sealing
5.4 Load and Stiffness of Capillary-Controlled Pads
5.5 Flow Control Mechanisms
5.6 General Stiffness Laws for Hydrostatic and Aerostatic Bearing Pads
5.7 Aerostatic Bearings and Flow Control
References
Appendix Tabular Design Procedures for Restrictors and Worked Examples
Chapter 6. Basis of Design Procedures
6.1 Introduction
6.2 An Acceptable Range for Design Pressure Ratio
6.3 Zero- and Low-Speed Hydrostatic Bearings
6.4 Zero- and Low-Speed Aerostatic Bearings
6.5 Optional Size Limits and Tolerances for Film Thickness
6.6 High-Speed Bearings
6.7 Specification for ISO Limits and Fits
6.8 Tolerance Grades for Hydrostatic and Aerostatic Bearings
References
Chapter 7. Plane Hydrostatic and Aerostatic Bearings
Summary of Key Design Formulae
7.1 Use of the Design Charts
7.2 Choice of Land Width
7.3 Flow Variation with Film Thickness
7.4 Load Variation with Film Thickness
7.5 Stiffness Variation with Film Thickness
7.6 Single-Pad Bearings
7.7 Equal Opposed-Pad Bearings
7.8 Unequal Opposed-Pad Bearings
7.9 Complex Arrangements of Pads (Capillary Controlled)
Appendix Tabular Design Procedures
Chapter 8. Partial Journal Bearings
Summary of Key Design Formulae
8.1 Recessed Partial Journal Bearings
8.2 Partial Journal Bearings with a High-Pressure Supply Groove
Reference
Chapter 9. Recessed Hydrostatic Journal Bearings
Summary of Key Design Formulae
9.1 Introduction
9.2 Flow
9.3 Load
9.4 Power, Power Ratio, and Temperature Rise
9.5 Land-Width Ratios and Concentric Pressure Ratio
9.6 Selection of Tolerances for Bearing Film Clearance
9.7 Selection of Supply Pressure, Viscosity, and Clearance
9.8 Bearing Film Stiffness
References
Appendix 1 Derivation of Journal Bearing Stiffness by an Approximate Analytical Method
Appendix 2 Tabular Design Procedure
Chapter 10. Plain Journal Bearings
Summary of Key Design Formulae
Part A Hydrostatic/Hybrid Plain Journal Bearings
10.2 Selection of Bearing Configuration
10.3 Power Ratio, K
10.4 Concentric Hydrostatic Pressure Ratio, β
10.5 Bearing Clearance and Clearance Limits
10.6 Hydrostatic Load Support
10.7 Hybrid Slot-Entry Bearings
10.8 Hybrid Hole-Entry Bearings
10.9 Size of Slot and Hole-Entry Ports
10.10 Summary of Hydrostatic and Hybrid Load Support
10.11 Concentric Hydrostatic/Hybrid Flow
10.12 Power and Temperature Rise
Part B Aerostatic Plain Journal Bearings
10.14 Concentric Aerostatic Pressure Ratio, Kgo
10.15 Aerostatic Clearance and Clearance Limits
10.16 Aerostatic Load Support
10.17 Concentric Aerostatic Flow
10.18 Hybrid Aerostatic Journal Bearings
10.19 Materials and Surface Texture for Journal Bearings
References
Appendix Tabular Design Procedures
Chapter 11. The Yates Bearing
Summary of Key Design Formulae
11.1 Introduction
11.2 Principle of Operation
11.3 Basic Parameters for the Yates Bearing
11.4 Hydrostatic Design Procedure
11.5 Aerostatic Yates Bearings
11.6 Aerostatic Design Procedure
References
Chapter 12. Conical Journal Bearings
Summary of Key Design Formulae
12.1 Application
12.2 Basic Parameters
12.3 Single-Cone Bearings
12.4 Complementary-Cone Spindle Bearings
12.5 High-Speed Design
12.6 Design Procedure for a Complementary-Cone Hydrostatic Bearing
12.7 Design Procedure for a Complementary-Cone Aerostatic Bearing
References
Chapter 13. Spherical Bearings
Summary of Key Design Formulae
13.1 Application
13.2 Basic Parameters
13.3 Central-Recess Spherical Bearing
13.4 Annular-Recess Spherical Bearing
13.5 Single Multi-Recess Spherical Bearings
13.6 Opposed Multi-Recess Spherical Bearings
Reference
Chapter 14. Dynamics
Summary of Key Design Formulae
14.1 Introduction
14.2 Static Loading
14.3 Dynamic Loading
14.4 Squeeze Film Damping
14.5 Compressibility in Hydrostatic and Aerostatic Bearings
14.6 Dynamic Model of a Thrust Pad
14.7 Hydrostatic Thrust Pad with Thin Lands
14.8 Journal Bearings: Equations of Motion
14.9 Journal Bearings in the Concentric Condition
14.10 Eccentric Journal Bearings
References
Chapter 15. Experimental Methods and Testing
15.1 Introduction
15.2 Flat-Pad Rig
15.3 Cylindrical Journal Bearing Rig
15.4 Publications on Experimental Behavior
References
- Edition: 1
- Published: October 30, 2018
- Language: English
WR