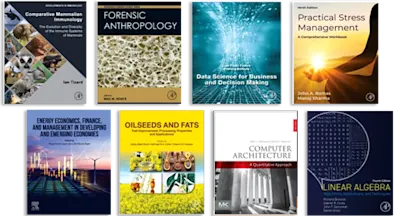
Hot Embossing
Theory and Technology of Microreplication
- 1st Edition - February 14, 2014
- Imprint: William Andrew
- Author: Matthias Worgull
- Language: English
- Paperback ISBN:9 7 8 - 0 - 3 2 3 - 1 6 5 5 4 - 9
- eBook ISBN:9 7 8 - 0 - 0 8 - 0 9 4 7 5 9 - 4
- eBook ISBN:9 7 8 - 0 - 8 1 5 5 - 1 9 7 4 - 4
This book is an overview of replication technology for micro- and nanostructures, focusing on the techniques and technology of hot embossing, a scaleable and multi-purpose… Read more
Purchase options
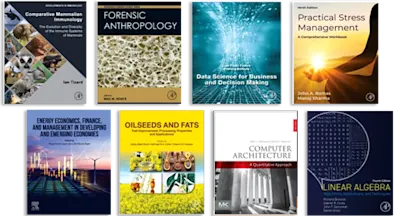
This book is an overview of replication technology for micro- and nanostructures, focusing on the techniques and technology of hot embossing, a scaleable and multi-purpose technology for the manufacture of devices such as BioMEMS and microfluidic devices which are expected to revolutionize a wide range of medical and industrial processes over the coming decade.The hot embossing process for replicating microstructures was developed by the Forschungszentrum Karlsruhe (Karlsruhe Institute of Technology) where the author is head of the Nanoreplication Group. Worgull fills a gap in existing information by fully detailing the technology and techniques of hot embossing. He also covers nanoimprinting, a process related to hot embossing, with examples of actual research topics and new applications in nanoreplication.
- A practical and theoretical guide to selecting the materials, machinery and processes involved in microreplication using hot embossing techniques
- Compares different replication processes such as: micro injection molding, micro thermoforming, micro hot embossing, and nanoimprinting
- Details commercially available hot embossing machinery and components like tools and mold inserts
Engineers and students involved in microreplication. Polymer processors and polymer developers
1 Introduction
1.1 Hot embossing as a replication technology for microstructures
1.2 History of (Micro) Hot Embossing
1.3 Development of hot embossing
1.3.1 The beginning of hot embossing
1.3.2 Micro hot embossing today - state of the art
1.4 Aim of the book
2 Replication Processes
2.1 Overview Micro Replication Processes
2.2 Micro Reaction Injection molding (RIM)
2.2.1 Process
2.2.2 Technology of micro reaction injection molding
2.2.3 Material
2.2.4 Cost effectiveness
2.2.5 Characteristics
2.3 Micro Injection Molding
2.3.1 process
2.3.2 Technology of micro injection molding
2.3.3 Materials for micro injection molding
2.3.4 Cost effectiveness
2.3.5 Characteristics
2.4 Injection compression molding
2.5 Micro Hot Embossing
2.5.1 Technology of hot embossing
2.5.2 Materials for hot embossing
2.5.3 Cost effectiveness
2.5.4 Characteristics
2.6 Micro Thermoforming
2.6.1 Process
2.6.2 Materials for thermoforming
2.6.3 Cost effectiveness
2.6.4 Characteristics
2.7 Nanoimprint
2.7.1 Micro contact printing
2.7.2 Nanoimprint of UV-curable materials
2.7.3 Nanoimprint of thermoplastic polymers
2.8 Comparison of Processes
2.8.1 Design
2.8.2 Materials
2.8.3 Technology
2.8.4 Cost effectiveness
2.9 Table of characteristic properties
3 Molding Materials for hot embossing
3.1 Classiffcation of materials
3.1.1 Non polymer materials
3.1.2 Polymer materials
3.2 Polymer melts
3.2.1 Shear rheologic behavior
3.2.2 Strain-rheologic behavior
3.2.3 Molecular orientation and relaxation
3.3 Solidiffcation
3.3.1 Amorphous and semicrystalline strcutures
3.3.2 p-v-T-diagram
3.4 Solid polymers
3.4.1 Linear viscoelasticty in the solid state
3.4.2 Mechanical characteristics
3.4.3 Friction
3.5 Thermal aggregate states of polymers
3.5.1 Amorphous polymers
3.5.2 Semicrystalline polymers
3.5.3 Molding windows
3.5.4 Commercial availible polymers
3.6 Thermal characteristics of polymers
3.6.1 Thermal material data
3.6.2 Measurement of calorimetric data
4 Hot Embossing Process
4.1 Molding Principles
4.2 Components for Hot Embossing
4.3 Process Steps
4.4 Molding Parameters
4.4.1 Process Parameters
4.4.2 Material Parameters
4.4.3 In uencing Factors
4.5 Process variations
4.5.1 Position controlled molding
4.5.2 Double sided molding
4.5.3 Molding of through holes
4.5.4 Multi layer molding
4.5.5 Thermoforming of high temperature polymers by hot embossing
5 Molded parts
5.1 Component of hot embossed parts
5.2 Characterization of Molded Parts
5.2.1 Measurement Systems for characterization
5.3 Quality of Molded Parts
5.3.1 Classiffcation of failures
5.3.2 Surface quality of molded parts
5.3.3 Shrinkage and Warpage
5.3.4 Stress inside molded parts
5.3.5 Controlling quality of molded parts
6 Modeling and Process Simulation 5
6.1 Analytical Model
6.1.1 Squeezing Flow of a Newtonian Fluid
6.2 Process Simulation in Polymer Processing
6.2.1 Simulation of Macroscopic Processes
6.2.2 Simulation of Microscopic Polymer Processes
6.2.3 Commercial Simulation Programs
6.3 Process Simulation of Micro Hot Embossing
6.3.1 Modeling of Typical Microstructured Parts
6.3.2 Modeling of Material Behavior
6.3.3 The Process Step of Heating
6.3.4 The Process Step of Molding
6.3.5 The Process Step of Cooling
6.3.6 The Process Step of Demolding
6.3.7 Stress Distribution during Demolding of Structures
7 Hot Embossing Technique
7.1 Technical Requirements
7.2 Technical implementation
7.2.1 Mechanical stiffness
7.2.2 Drive unit
7.2.3 Measurement of process parameters
7.2.4 Control system
7.3 Commercial available machines
7.3.1 Jenoptik Mikrotechnik
7.3.2 Wickert Press
7.3.3 EVG
7.3.4 Suess
8 Hot embossing Tools
8.1 Requirements of hot embossing tools
8.2 Constructive elements of hot embossing tools
8.2.1 Heating concepts
8.2.2 Cooling concept
8.2.3 Alignment Systems
8.2.4 Integration of mold inserts
8.2.5 Demolding Systems
8.3 Basic tool for Hot embossing
8.4 High precision tool for double sided molding
8.4.1 Operation principle
9 Microstructured mold inserts for hot embossing
9.1 Direct structuring methods
9.1.1 Mechanical Micro Machining
9.1.2 Laser structuring
9.1.3 Electric Discharge Machining (EDM)
9.1.4 Nonconventional molds - Alternative methods
9.2 Lithographic structuring methods
9.2.1 Electroforming of mold inserts
9.2.2 Mold inserts fabricated by UV-Lithography
9.2.3 Mold inserts fabricated by X-ray Lithography
9.2.4 E-Beam-Lithography Molds
9.3 Mold coatings
9.4 Design of microstructured molds
9.4.1 Mold fflling
9.4.2 Compensation of shrinkage
9.4.3 Reduction of demolding forces
10 Hot Embossing in Science and Industry
10.1 Scientiffc applications, small series and prototypes
10.1.1 Requirements for hot embossing in scientific environment
10.1.2 Microoptical Devices
10.1.3 Micro uidic Devices
10.1.4 Structures in the Sub-mircon range
10.2 Industrial Applications
10.2.1 Requirements for the Use in Industry
10.2.2 CD-production
10.2.3 Film fabrication
10.2.4 Fresnel Lenses
10.2.5 Spectrometer
1.1 Hot embossing as a replication technology for microstructures
1.2 History of (Micro) Hot Embossing
1.3 Development of hot embossing
1.3.1 The beginning of hot embossing
1.3.2 Micro hot embossing today - state of the art
1.4 Aim of the book
2 Replication Processes
2.1 Overview Micro Replication Processes
2.2 Micro Reaction Injection molding (RIM)
2.2.1 Process
2.2.2 Technology of micro reaction injection molding
2.2.3 Material
2.2.4 Cost effectiveness
2.2.5 Characteristics
2.3 Micro Injection Molding
2.3.1 process
2.3.2 Technology of micro injection molding
2.3.3 Materials for micro injection molding
2.3.4 Cost effectiveness
2.3.5 Characteristics
2.4 Injection compression molding
2.5 Micro Hot Embossing
2.5.1 Technology of hot embossing
2.5.2 Materials for hot embossing
2.5.3 Cost effectiveness
2.5.4 Characteristics
2.6 Micro Thermoforming
2.6.1 Process
2.6.2 Materials for thermoforming
2.6.3 Cost effectiveness
2.6.4 Characteristics
2.7 Nanoimprint
2.7.1 Micro contact printing
2.7.2 Nanoimprint of UV-curable materials
2.7.3 Nanoimprint of thermoplastic polymers
2.8 Comparison of Processes
2.8.1 Design
2.8.2 Materials
2.8.3 Technology
2.8.4 Cost effectiveness
2.9 Table of characteristic properties
3 Molding Materials for hot embossing
3.1 Classiffcation of materials
3.1.1 Non polymer materials
3.1.2 Polymer materials
3.2 Polymer melts
3.2.1 Shear rheologic behavior
3.2.2 Strain-rheologic behavior
3.2.3 Molecular orientation and relaxation
3.3 Solidiffcation
3.3.1 Amorphous and semicrystalline strcutures
3.3.2 p-v-T-diagram
3.4 Solid polymers
3.4.1 Linear viscoelasticty in the solid state
3.4.2 Mechanical characteristics
3.4.3 Friction
3.5 Thermal aggregate states of polymers
3.5.1 Amorphous polymers
3.5.2 Semicrystalline polymers
3.5.3 Molding windows
3.5.4 Commercial availible polymers
3.6 Thermal characteristics of polymers
3.6.1 Thermal material data
3.6.2 Measurement of calorimetric data
4 Hot Embossing Process
4.1 Molding Principles
4.2 Components for Hot Embossing
4.3 Process Steps
4.4 Molding Parameters
4.4.1 Process Parameters
4.4.2 Material Parameters
4.4.3 In uencing Factors
4.5 Process variations
4.5.1 Position controlled molding
4.5.2 Double sided molding
4.5.3 Molding of through holes
4.5.4 Multi layer molding
4.5.5 Thermoforming of high temperature polymers by hot embossing
5 Molded parts
5.1 Component of hot embossed parts
5.2 Characterization of Molded Parts
5.2.1 Measurement Systems for characterization
5.3 Quality of Molded Parts
5.3.1 Classiffcation of failures
5.3.2 Surface quality of molded parts
5.3.3 Shrinkage and Warpage
5.3.4 Stress inside molded parts
5.3.5 Controlling quality of molded parts
6 Modeling and Process Simulation 5
6.1 Analytical Model
6.1.1 Squeezing Flow of a Newtonian Fluid
6.2 Process Simulation in Polymer Processing
6.2.1 Simulation of Macroscopic Processes
6.2.2 Simulation of Microscopic Polymer Processes
6.2.3 Commercial Simulation Programs
6.3 Process Simulation of Micro Hot Embossing
6.3.1 Modeling of Typical Microstructured Parts
6.3.2 Modeling of Material Behavior
6.3.3 The Process Step of Heating
6.3.4 The Process Step of Molding
6.3.5 The Process Step of Cooling
6.3.6 The Process Step of Demolding
6.3.7 Stress Distribution during Demolding of Structures
7 Hot Embossing Technique
7.1 Technical Requirements
7.2 Technical implementation
7.2.1 Mechanical stiffness
7.2.2 Drive unit
7.2.3 Measurement of process parameters
7.2.4 Control system
7.3 Commercial available machines
7.3.1 Jenoptik Mikrotechnik
7.3.2 Wickert Press
7.3.3 EVG
7.3.4 Suess
8 Hot embossing Tools
8.1 Requirements of hot embossing tools
8.2 Constructive elements of hot embossing tools
8.2.1 Heating concepts
8.2.2 Cooling concept
8.2.3 Alignment Systems
8.2.4 Integration of mold inserts
8.2.5 Demolding Systems
8.3 Basic tool for Hot embossing
8.4 High precision tool for double sided molding
8.4.1 Operation principle
9 Microstructured mold inserts for hot embossing
9.1 Direct structuring methods
9.1.1 Mechanical Micro Machining
9.1.2 Laser structuring
9.1.3 Electric Discharge Machining (EDM)
9.1.4 Nonconventional molds - Alternative methods
9.2 Lithographic structuring methods
9.2.1 Electroforming of mold inserts
9.2.2 Mold inserts fabricated by UV-Lithography
9.2.3 Mold inserts fabricated by X-ray Lithography
9.2.4 E-Beam-Lithography Molds
9.3 Mold coatings
9.4 Design of microstructured molds
9.4.1 Mold fflling
9.4.2 Compensation of shrinkage
9.4.3 Reduction of demolding forces
10 Hot Embossing in Science and Industry
10.1 Scientiffc applications, small series and prototypes
10.1.1 Requirements for hot embossing in scientific environment
10.1.2 Microoptical Devices
10.1.3 Micro uidic Devices
10.1.4 Structures in the Sub-mircon range
10.2 Industrial Applications
10.2.1 Requirements for the Use in Industry
10.2.2 CD-production
10.2.3 Film fabrication
10.2.4 Fresnel Lenses
10.2.5 Spectrometer
- Edition: 1
- Published: February 14, 2014
- Imprint: William Andrew
- Language: English
MW
Matthias Worgull
Matthias Worgull is an associated professor and lecturer at the Institute of Microstructure Technology, Karlsruhe Institute of Technology, Germany and has more than 20 years of experience in polymer micro structuring by replication processes. He is currently head of the group "Large Scale Structuring" with focus on the upscaling of hot embossing, nanoimprint, and roll-to-roll replication and the implementation of functional bionic surfaces with enhanced materials.
Affiliations and expertise
Lecturer, Institute of Microstructure Technology, Karlsruhe Institute of Technology, Karlsruhe Institute of Technology, GermanyRead Hot Embossing on ScienceDirect