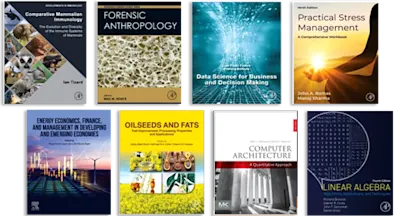
Hot Embossing
Theory of Microreplication
- 2nd Edition - June 13, 2024
- Imprint: Elsevier
- Author: Matthias Worgull
- Language: English
- Paperback ISBN:9 7 8 - 0 - 1 2 - 8 2 1 1 9 3 - 9
- eBook ISBN:9 7 8 - 0 - 3 2 3 - 9 8 4 2 1 - 8
Hot Embossing: Theory of Microreplication, Second Edition presents the current state-of-the-art in microreplication, with a focus on hot embossing, nanoimprint, thermo… Read more
Purchase options
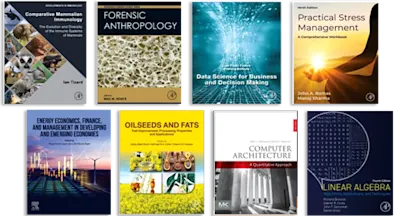
Hot Embossing: Theory of Microreplication, Second Edition presents the current state-of-the-art in microreplication, with a focus on hot embossing, nanoimprint, thermoforming, and roll-to-roll replication. Polymer processing, the theory of polymers and the processing of polymers are discussed in detail. The book contains in-depth analysis of processing processes and replication techniques, including mold fabrication. Monitoring, data analysis and reliability of molded parts is also discussed. In this updated edition, new processes are included, such as the process of micro- and nanothermoforming to generate 3D structures and the hot pulling processes to generate hierarchical structures with high aspect ratios.
Based on hot pulling, “Nanofur” for Oil-water-separation is a large-scale biomimetic application. Upscaling, especially the seamless roll-to-roll replication, is also explored. The book is designed to cover the entire workflow for a seamless lithographic sleeve. This new edition marks a substantial update of the previous edition, incorporating several new chapters. It is an important resource for materials scientists and engineers working in the areas of micro- and nanofabrication.
Based on hot pulling, “Nanofur” for Oil-water-separation is a large-scale biomimetic application. Upscaling, especially the seamless roll-to-roll replication, is also explored. The book is designed to cover the entire workflow for a seamless lithographic sleeve. This new edition marks a substantial update of the previous edition, incorporating several new chapters. It is an important resource for materials scientists and engineers working in the areas of micro- and nanofabrication.
- Comprehensively updated to include new techniques, processes, and variables that have come to prominence in recent years
- Includes new chapters that address monitoring, properties of molded parts, 3D thermoforming, hot pulling, functional materials, smart surfaces, and upscaling by roll-2-roll
- Discusses the entire microreplication process, from theory and processes to technology and mold to surface-oriented applications
Materials Scientists and Engineers
1. Introduction
2. Replication Processes
3. Hot Embossing Process
4. Enhanced Hot Embossing Processes
5. Hot Pulling
6. Thermoforming
7. Modeling and Process Simulation
8. Fundamentals of Polymers
9. Polymer Materials for Hot Embossing
10. Enhanced Embossing Materials
11. Process Monitoring
12. Quality control
13. Hot Embossing Technology
14. Hot Embossing Tools
15. Mold Inserts
16. Functional Biomimetic Surfaces
17. SMART surfaces
18. Roll-to-Roll Embossing
19. Roll-to-Roll Tooling
20. Hot Embossing Applications.
21. Outlook
2. Replication Processes
3. Hot Embossing Process
4. Enhanced Hot Embossing Processes
5. Hot Pulling
6. Thermoforming
7. Modeling and Process Simulation
8. Fundamentals of Polymers
9. Polymer Materials for Hot Embossing
10. Enhanced Embossing Materials
11. Process Monitoring
12. Quality control
13. Hot Embossing Technology
14. Hot Embossing Tools
15. Mold Inserts
16. Functional Biomimetic Surfaces
17. SMART surfaces
18. Roll-to-Roll Embossing
19. Roll-to-Roll Tooling
20. Hot Embossing Applications.
21. Outlook
- Edition: 2
- Published: June 13, 2024
- Imprint: Elsevier
- Language: English
MW
Matthias Worgull
Matthias Worgull is an associated professor and lecturer at the Institute of Microstructure Technology, Karlsruhe Institute of Technology, Germany and has more than 20 years of experience in polymer micro structuring by replication processes. He is currently head of the group "Large Scale Structuring" with focus on the upscaling of hot embossing, nanoimprint, and roll-to-roll replication and the implementation of functional bionic surfaces with enhanced materials.
Affiliations and expertise
Lecturer, Institute of Microstructure Technology, Karlsruhe Institute of Technology, Karlsruhe Institute of Technology, GermanyRead Hot Embossing on ScienceDirect