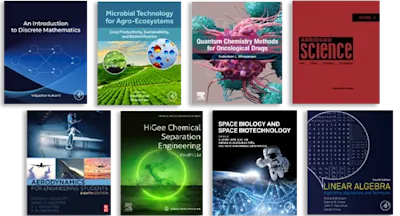
High Temperature Oxidation and Corrosion of Metals
- 1st Edition, Volume 1 - August 6, 2008
- Author: David John Young
- Language: English
- eBook ISBN:9 7 8 - 0 - 0 8 - 0 9 5 1 5 9 - 1
- eBook ISBN:9 7 8 - 0 - 0 8 - 0 5 5 9 4 1 - 4
This book is concerned with providing a fundamental basis for understanding the alloy-gas oxidation and corrosion reactions observed in practice and in the laboratory. Starting… Read more
Purchase options
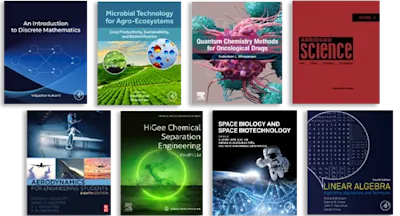
This book is concerned with providing a fundamental basis for understanding the alloy-gas oxidation and corrosion reactions observed in practice and in the laboratory. Starting with a review of the enabling thermodynamic and kinetic theory, it analyzes reacting systems of increasing complexity. It considers in turn corrosion of a pure metal by a single oxidant and by multi-oxidant gases, followed by corrosion of alloys producing a single oxide then multiple reaction products. The concept of “diffusion paths” is used in describing the distribution of products in reacting systems, and diffusion data is used to predict reaction rates whenever possible.
- Provides a logical and expert treatment of the subject for use as a guide for advanced-level academics, researchers and practitioners
- Text is well supported by numerous micrographs, phase diagrams and tabulations of relevant thermodynamic and kinetic data
- Combines physical chemistry and materials science methodologies
Upper-level undergraduate and graduate students, professionals, researchers and consultants in the field of high temperature corrosion resistance
Preface
Abbreviations and Acronyms
Glossary of Symbols
1. THE NATURE OF HIGH TEMPERATURE OXIDATION
1.1 Metal Loss due to the Scaling of Steel
1.2 Heating Elements
1.3 Protecting Turbine Engine Components
1.4 Hydrocarbon Cracking Furnaces
1.5 Prediction and Measurement
Oxidation Rates
1.6 Rate Equations
Linear Kinetics
Diffusion Controlled Processes and Parabolic Kinetics
Diffusion and Phase Boundary Processes Combined
Volatilisation
Thin Oxide Film Growth
1.7 Reaction Morphology: Specimen Examination
1.8 Summary
References
2. ENABLING THEORY
2.1 Chemical Thermodynamics
Chemical Potential and Composition
Chemical Equilibrium in Gas Mixtures
2.2 Chemical Equilibria between Solids and Gases
Chemical Equilibria Involving Multiple Solids
Gases Containing Two Reactants
2.3 Alloys and Solid Solutions
Dissolution of Gases in Metals
2.4 Chemical Equilibria Between Alloys and Gases
Equilibria between Alloys and a Single Oxide
Equilibria between Alloys and Multiple Oxides
2.5 Thermodynamics of Diffusion
Driving Forces
Point Defects
2.6 Absolute Rate Theory Applied to Lattice Particle Diffusion
2.7 Diffusion in Alloys
Origins of Cross Effects
Kirkendall Effect
Diffusion Data for Alloys
2.8 Diffusion Couples and the Measurement of Diffusion Coefficients
2.9 Interfacial Processes and Gas Phase Mass Transfer
Gas Adsorption
Gas Phase Mass Transfer at Low Pressure
Mass Transfer in Dilute Gases
2.10 Mechanical Effects: Stresses in Oxide Scales
Stresses Developed during Oxidation
Stresses Developed during Temperature Change
2.11 Further Reading
References
3. OXIDATION OF PURE METALS
3.1 Experimental Findings
3.2 Use of Phase Diagrams
3.3 Point Defects and Nonstoichiometry in Ionic Oxides
3.4 Lattice Species and Structural Units in Ionic Oxides
3.5 Gibbs-Duhem Equation for Defective Solid Oxides
3.6 Lattice Diffusion and Oxide Scaling – Wagner’s Model
3.7 Validation of Wagner’s Model
Oxidation of Nickel
Oxidation of Cobalt
Oxidation of Iron
Sulphidation of Iron
Effects of Oxidant Partial Pressure on the Parabolic Rate Constant
Effect of Temperature on the Parabolic Rate Constant
Other Systems
Utility of Wagner’s Theory
3.8 Impurity Effects on Lattice Diffusion
3.9 Microstructural Effects
Grain Boundary Diffusion
Multi-Layer Scale Growth
Development of Macroscopic Defects and Scale Detachment
3.10 Reactions not Controlled by Solid-State Diffusion
Oxidation of Iron at low to form Wüstite Only
Oxidation of Silicon
References
4. MIXED GAS CORROSION OF PURE METALS
4.1 Selected Experimental Findings
4.2 Phase Diagrams and Diffusion Paths
Scaling of Chromium in Oxidising-Nitriding and Oxidising-Carburising Gases
Scaling of Chromium in Oxidising-Sulphidising-Carburising Gases
Scaling of Iron in Oxidising-Sulphidising Gases
Scaling of Nickel in Oxidising-Sulphidising Gases
4.3 Scale-Gas Interactions
Identity of Reactant Species
Rate Determining Processes in SO2 Reactions
Production of Metastable Sulphide
Independent Oxide and Sulphide Growth in SO2
4.4 Transport Processes in Mixed Scales
Effect of Pre-oxidation on Reaction with Sulphidising-Oxidising Gases
Solid-State Diffusion of Sulphur
Gas Diffusion Through Scales
Scale Penetration by Multiple Gas Species
Metal Transport Processes
4.5 Predicting the Outcome of Mixed Gas Reactions
References
5. ALLOY OXIDATION I: SINGLE-PHASE SCALES
5.1 Introduction
5.2 Selected Experimental Results
5.3 Phase Diagrams and Diffusion Paths
5.4 Selective Oxidation of One Alloy Component
5.5 Selective Oxidation of One Alloy Component under Non Steady-State Conditions
5.6 Solid Solution Oxide Scales
Modelling Diffusion in Solid Solution Scales
5.7 Transient Oxidation
Transient Behaviour Associated with Alumina Phase Transformations
5.8 Microstructural Changes in Subsurface Alloy Regions
Subsurface Void Formation
Scale-Alloy Interface Stability
Phase Dissolution
New Phase Formation
Other Transformations
5.9 Breakdown of Steady-State Scale
5.10 Other Factors Affecting Scale Growth
References
6. ALLOY OXIDATION II: INTERNAL OXIDATION
6.1 Introduction
6.2 Selected Experimental Results
6.3 Internal Oxidation Kinetics in the Absence of External Scaling
6.4 Experimental Verification of Diffusion Model
6.5 Surface Diffusion Effects in the Precipitation Zone
6.6 Internal Precipitates of Low Stability
6.7 Precipitate Nucleation and Growth
6.8 Cellular Precipitation Morphologies
6.9 Multiple Internal Precipitates
6.10 Solute Interactions in the Precipitation Zone
6.11 Transition from Internal to External Oxidation
6.12 Internal Oxidation Beneath a Corroding Alloy Surface
6.13 Volume Expansion in the Internal Precipitation Zone
References
7. ALLOY OXIDATION III: MULTI-PHASE SCALES
7.1 Introduction
7.2 Binary Alumina Formers
The Ni-Al System
The Fe-Al System
7.3 Binary Chromia Formers
The Ni-Cr and Fe-Cr Systems
Transport Processes in Chromia Scales
7.4 Ternary Alloy Oxidation
Fe-Ni-Cr Alloys
Ni-Pt-Al Alloys
Ni-Cr-Al Alloys
Fe-Cr-Al Alloys
Third Element Effect
7.5 Scale Spallation
The Sulphur Effect
Interfacial Voids and Scale Detachment
Reactive Element Effects
7.6 Effects of Minor Alloying Additions
Silicon Effects
Manganese Effects
Titanium Effects
Other Effects
7.7 Effects of Secondary Oxidants
References
8. CORROSION BY SULPHUR
8.1 Introduction
8.2 Sulphidation of Pure Metals
Sulphidation Kinetics and Rates
Growth of NiAs-type Sulphide Scales
Sulphidation of Manganese
Sulphidation of Refractory Metals Sulphides
8.3 Alloying for Sulphidation Protection
Alloying with Chromium
Alloying with Aluminium
M-Cr-Al Alloys
Alloying with Manganese
Alloying with Molybdenum
Refractory Metal Alloys
8.4 Sulphidation in H2/H2S
8.5 Effects of Temperature and Sulphur Partial Pressure
8.6 The Role of Oxygen
8.7 Internal Sulphidation
8.8 Hot Corrosion
Phenomenology of Sulphate Induced Hot Corrosion
Molten Salt Chemistry
Fluxing Mechanisms
Type I and Type II Hot Corrosion
References
9. CORROSION BY CARBON
9.1 Introduction
9.2 Gaseous carbon activities
9.3 Carburisation
9.4 Internal Carburisation of Model Alloys
Reaction Morphologies and Thermodynamics
Carburisation Kinetics
Carbide Microstructures and Distributions
9.5 Internal Carburisation of Heat Resisting Alloys
Effect of Carbon
Effect of Molybdenum
Effect of Silicon
Effect of Niobium and Reactive Elements
Effect of Aluminium
Alloying for Carburisation Protection
9.6 Metal Dusting of Iron and Ferritic Alloys
Metal Dusting of Iron
Iron Dusting in the Absence of Cementite
Effects of Temperature and gas Composition on Iron Dusting
Dusting of Low Alloy Steels
Dusting of fFerritic Chromium Ssteels
Dusting of FeAl and FeCrAl Alloys
9.7 Dusting of Nickel and Austenitic Alloys
Metal Dusting of Nickel
Dusting of Nickel Alloys in the Absence of Oxide Scales
Effects of Temperature and Gas Composition on Nickel Dusting
Dusting of Aaustenitic Alloys
9.8 Protection by Oxide Scaling
Protection by Coatings
Protection by Adsorbed Sulphur
References
10. EFFECTS OF WATER VAPOUR ON OXIDATION
10.1 Introduction
10.2 Volatile Metal Hydroxide Formation
Chromia Volatilisation
Chromia Volatilisation in Steam
Effects of Chromia Volatilisation
Silica Volatilisation
Other Oxides
10.3 Scale-Gas Interfacial Processes
10.4 Scale Transport Properties
Gas Transport
Molecular Transport
Molecular Transport in Chromia Scales
Ionic Transport
10.5 Water Vapour Effects on Alumina Formation
10.6 Void Development in Growing Scales
References
11. CYCLIC OXIDATION
11.1 Introduction
11.2 Alloy Depletion and Scale Rehealing
11.3 Spallation Models
11.4 Combination of Spalling and Depletion Models
11.5 Effects of Experimental Variables
Temperature Cycle Parameters
Continuous Thermogravimetric Analysis
Compositions of Alloys and Environments
References
12. ALLOY DESIGN
12.1 Introduction
12.2 Alloy Design for Resistance to Oxygen
12.3 Design Against Oxide Scale Spallation
12.4 Design for Resistance to Other Corrodents and Mixed Gases
12.5 Future Research
Electric Power Generation
Petrochemical and Chemical Process Industries
Greenhouse Gas Emission Control
12.6 Fundamental Research
Grain Boundaries in Oxide Scales
Water Vapour Effects
Nucleation and Growth Phenomena
12.7 Conclusion
References
Appendix A
Appendix B
Appendix C
Appendix D
Index
Abbreviations and Acronyms
Glossary of Symbols
1. THE NATURE OF HIGH TEMPERATURE OXIDATION
1.1 Metal Loss due to the Scaling of Steel
1.2 Heating Elements
1.3 Protecting Turbine Engine Components
1.4 Hydrocarbon Cracking Furnaces
1.5 Prediction and Measurement
Oxidation Rates
1.6 Rate Equations
Linear Kinetics
Diffusion Controlled Processes and Parabolic Kinetics
Diffusion and Phase Boundary Processes Combined
Volatilisation
Thin Oxide Film Growth
1.7 Reaction Morphology: Specimen Examination
1.8 Summary
References
2. ENABLING THEORY
2.1 Chemical Thermodynamics
Chemical Potential and Composition
Chemical Equilibrium in Gas Mixtures
2.2 Chemical Equilibria between Solids and Gases
Chemical Equilibria Involving Multiple Solids
Gases Containing Two Reactants
2.3 Alloys and Solid Solutions
Dissolution of Gases in Metals
2.4 Chemical Equilibria Between Alloys and Gases
Equilibria between Alloys and a Single Oxide
Equilibria between Alloys and Multiple Oxides
2.5 Thermodynamics of Diffusion
Driving Forces
Point Defects
2.6 Absolute Rate Theory Applied to Lattice Particle Diffusion
2.7 Diffusion in Alloys
Origins of Cross Effects
Kirkendall Effect
Diffusion Data for Alloys
2.8 Diffusion Couples and the Measurement of Diffusion Coefficients
2.9 Interfacial Processes and Gas Phase Mass Transfer
Gas Adsorption
Gas Phase Mass Transfer at Low Pressure
Mass Transfer in Dilute Gases
2.10 Mechanical Effects: Stresses in Oxide Scales
Stresses Developed during Oxidation
Stresses Developed during Temperature Change
2.11 Further Reading
References
3. OXIDATION OF PURE METALS
3.1 Experimental Findings
3.2 Use of Phase Diagrams
3.3 Point Defects and Nonstoichiometry in Ionic Oxides
3.4 Lattice Species and Structural Units in Ionic Oxides
3.5 Gibbs-Duhem Equation for Defective Solid Oxides
3.6 Lattice Diffusion and Oxide Scaling – Wagner’s Model
3.7 Validation of Wagner’s Model
Oxidation of Nickel
Oxidation of Cobalt
Oxidation of Iron
Sulphidation of Iron
Effects of Oxidant Partial Pressure on the Parabolic Rate Constant
Effect of Temperature on the Parabolic Rate Constant
Other Systems
Utility of Wagner’s Theory
3.8 Impurity Effects on Lattice Diffusion
3.9 Microstructural Effects
Grain Boundary Diffusion
Multi-Layer Scale Growth
Development of Macroscopic Defects and Scale Detachment
3.10 Reactions not Controlled by Solid-State Diffusion
Oxidation of Iron at low to form Wüstite Only
Oxidation of Silicon
References
4. MIXED GAS CORROSION OF PURE METALS
4.1 Selected Experimental Findings
4.2 Phase Diagrams and Diffusion Paths
Scaling of Chromium in Oxidising-Nitriding and Oxidising-Carburising Gases
Scaling of Chromium in Oxidising-Sulphidising-Carburising Gases
Scaling of Iron in Oxidising-Sulphidising Gases
Scaling of Nickel in Oxidising-Sulphidising Gases
4.3 Scale-Gas Interactions
Identity of Reactant Species
Rate Determining Processes in SO2 Reactions
Production of Metastable Sulphide
Independent Oxide and Sulphide Growth in SO2
4.4 Transport Processes in Mixed Scales
Effect of Pre-oxidation on Reaction with Sulphidising-Oxidising Gases
Solid-State Diffusion of Sulphur
Gas Diffusion Through Scales
Scale Penetration by Multiple Gas Species
Metal Transport Processes
4.5 Predicting the Outcome of Mixed Gas Reactions
References
5. ALLOY OXIDATION I: SINGLE-PHASE SCALES
5.1 Introduction
5.2 Selected Experimental Results
5.3 Phase Diagrams and Diffusion Paths
5.4 Selective Oxidation of One Alloy Component
5.5 Selective Oxidation of One Alloy Component under Non Steady-State Conditions
5.6 Solid Solution Oxide Scales
Modelling Diffusion in Solid Solution Scales
5.7 Transient Oxidation
Transient Behaviour Associated with Alumina Phase Transformations
5.8 Microstructural Changes in Subsurface Alloy Regions
Subsurface Void Formation
Scale-Alloy Interface Stability
Phase Dissolution
New Phase Formation
Other Transformations
5.9 Breakdown of Steady-State Scale
5.10 Other Factors Affecting Scale Growth
References
6. ALLOY OXIDATION II: INTERNAL OXIDATION
6.1 Introduction
6.2 Selected Experimental Results
6.3 Internal Oxidation Kinetics in the Absence of External Scaling
6.4 Experimental Verification of Diffusion Model
6.5 Surface Diffusion Effects in the Precipitation Zone
6.6 Internal Precipitates of Low Stability
6.7 Precipitate Nucleation and Growth
6.8 Cellular Precipitation Morphologies
6.9 Multiple Internal Precipitates
6.10 Solute Interactions in the Precipitation Zone
6.11 Transition from Internal to External Oxidation
6.12 Internal Oxidation Beneath a Corroding Alloy Surface
6.13 Volume Expansion in the Internal Precipitation Zone
References
7. ALLOY OXIDATION III: MULTI-PHASE SCALES
7.1 Introduction
7.2 Binary Alumina Formers
The Ni-Al System
The Fe-Al System
7.3 Binary Chromia Formers
The Ni-Cr and Fe-Cr Systems
Transport Processes in Chromia Scales
7.4 Ternary Alloy Oxidation
Fe-Ni-Cr Alloys
Ni-Pt-Al Alloys
Ni-Cr-Al Alloys
Fe-Cr-Al Alloys
Third Element Effect
7.5 Scale Spallation
The Sulphur Effect
Interfacial Voids and Scale Detachment
Reactive Element Effects
7.6 Effects of Minor Alloying Additions
Silicon Effects
Manganese Effects
Titanium Effects
Other Effects
7.7 Effects of Secondary Oxidants
References
8. CORROSION BY SULPHUR
8.1 Introduction
8.2 Sulphidation of Pure Metals
Sulphidation Kinetics and Rates
Growth of NiAs-type Sulphide Scales
Sulphidation of Manganese
Sulphidation of Refractory Metals Sulphides
8.3 Alloying for Sulphidation Protection
Alloying with Chromium
Alloying with Aluminium
M-Cr-Al Alloys
Alloying with Manganese
Alloying with Molybdenum
Refractory Metal Alloys
8.4 Sulphidation in H2/H2S
8.5 Effects of Temperature and Sulphur Partial Pressure
8.6 The Role of Oxygen
8.7 Internal Sulphidation
8.8 Hot Corrosion
Phenomenology of Sulphate Induced Hot Corrosion
Molten Salt Chemistry
Fluxing Mechanisms
Type I and Type II Hot Corrosion
References
9. CORROSION BY CARBON
9.1 Introduction
9.2 Gaseous carbon activities
9.3 Carburisation
9.4 Internal Carburisation of Model Alloys
Reaction Morphologies and Thermodynamics
Carburisation Kinetics
Carbide Microstructures and Distributions
9.5 Internal Carburisation of Heat Resisting Alloys
Effect of Carbon
Effect of Molybdenum
Effect of Silicon
Effect of Niobium and Reactive Elements
Effect of Aluminium
Alloying for Carburisation Protection
9.6 Metal Dusting of Iron and Ferritic Alloys
Metal Dusting of Iron
Iron Dusting in the Absence of Cementite
Effects of Temperature and gas Composition on Iron Dusting
Dusting of Low Alloy Steels
Dusting of fFerritic Chromium Ssteels
Dusting of FeAl and FeCrAl Alloys
9.7 Dusting of Nickel and Austenitic Alloys
Metal Dusting of Nickel
Dusting of Nickel Alloys in the Absence of Oxide Scales
Effects of Temperature and Gas Composition on Nickel Dusting
Dusting of Aaustenitic Alloys
9.8 Protection by Oxide Scaling
Protection by Coatings
Protection by Adsorbed Sulphur
References
10. EFFECTS OF WATER VAPOUR ON OXIDATION
10.1 Introduction
10.2 Volatile Metal Hydroxide Formation
Chromia Volatilisation
Chromia Volatilisation in Steam
Effects of Chromia Volatilisation
Silica Volatilisation
Other Oxides
10.3 Scale-Gas Interfacial Processes
10.4 Scale Transport Properties
Gas Transport
Molecular Transport
Molecular Transport in Chromia Scales
Ionic Transport
10.5 Water Vapour Effects on Alumina Formation
10.6 Void Development in Growing Scales
References
11. CYCLIC OXIDATION
11.1 Introduction
11.2 Alloy Depletion and Scale Rehealing
11.3 Spallation Models
11.4 Combination of Spalling and Depletion Models
11.5 Effects of Experimental Variables
Temperature Cycle Parameters
Continuous Thermogravimetric Analysis
Compositions of Alloys and Environments
References
12. ALLOY DESIGN
12.1 Introduction
12.2 Alloy Design for Resistance to Oxygen
12.3 Design Against Oxide Scale Spallation
12.4 Design for Resistance to Other Corrodents and Mixed Gases
12.5 Future Research
Electric Power Generation
Petrochemical and Chemical Process Industries
Greenhouse Gas Emission Control
12.6 Fundamental Research
Grain Boundaries in Oxide Scales
Water Vapour Effects
Nucleation and Growth Phenomena
12.7 Conclusion
References
Appendix A
Appendix B
Appendix C
Appendix D
Index
- Edition: 1
- Volume: 1
- Published: August 6, 2008
- Language: English
DY
David John Young
David Young was educated at the University of Melbourne then worked in Canada for 9 years (University of Toronto, McMaster University, National Research Council of Canada) on high temperature metal-gas reactions. Returning to Australia, he worked for BHP Steel Research then joined the University of New South Wales. There he led the School of Materials Science & Engineering for 15 years, and has carried out extensive work on high temperature corrosion in mixed gas atmospheres.
His work has led to over 350 publications, including the books Diffusion in the Condensed State (with J.S. Kirkaldy), Institute of Metals (1988) and High Temperature Oxidation and Corrosion of Metals, 1st ed., Elsevier (2008). It has been recognized by his election to the Australian Academy of Technological Sciences and Engineering, the U. R. Evans Award, Institute of Corrosion Science & Technology, UK, the High Temperature Materials Outstanding Achievement Award, Electrochemical Society, USA and election as Fellow, Electrochemical Society.
Affiliations and expertise
David John Young
School of Materials Science and Engineering
University of New South Wales
New South Wales, AustraliaRead High Temperature Oxidation and Corrosion of Metals on ScienceDirect