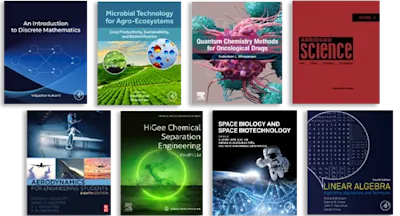
Heat Exchanger Design Guide
A Practical Guide for Planning, Selecting and Designing of Shell and Tube Exchangers
- 1st Edition - September 29, 2015
- Authors: Manfred Nitsche, Raji Olayiwola Gbadamosi
- Language: English
- Paperback ISBN:9 7 8 - 0 - 1 2 - 8 0 3 7 6 4 - 5
- eBook ISBN:9 7 8 - 0 - 1 2 - 8 0 3 8 2 2 - 2
Heat Exchanger Design Guide: A Practical Guide for Planning, Selecting and Designing of Shell and Tube Exchangers takes users on a step-by-step guide to the design of heat ex… Read more
Purchase options
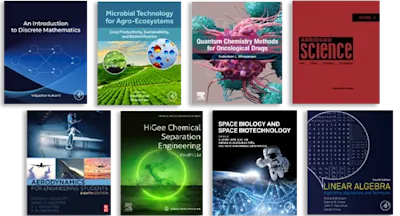
Heat Exchanger Design Guide: A Practical Guide for Planning, Selecting and Designing of Shell and Tube Exchangers takes users on a step-by-step guide to the design of heat exchangers in daily practice, showing how to determine the effective driving temperature difference for heat transfer.
Users will learn how to calculate heat transfer coefficients for convective heat transfer, condensing, and evaporating using simple equations. Dew and bubble points and lines are covered, with all calculations supported with examples.
This practical guide is designed to help engineers solve typical problems they might encounter in their day-to-day work, and will also serve as a useful reference for students learning about the field. The book is extensively illustrated with figures in support of the text and includes calculation examples to ensure users are fully equipped to select, design, and operate heat exchangers.
- Covers design method and practical correlations needed to design practical heat exchangers for process application
- Includes geometrical calculations for the tube and shell side, also covering boiling and condensation heat transfer
- Explores heat transfer coefficients and temperature differences
- Designed to help engineers solve typical problems they might encounter in their day-to-day work, but also ideal as a useful reference for students learning about the field
Chemical engineers, mechanical engineers, process engineers, chemical and mechanical engineering students.
- Foreword
- Chapter 1. Heat Exchanger Design
- 1.1. Procedure in Heat Exchanger Design
- 1.2. Information about Heat Exchangers
- Nomenclature
- Chapter 2. Calculations of the Temperature Differences LMTD and CMTD
- 2.1. Logarithmic Mean Temperature Difference for Ideal Countercurrent Flow
- 2.2. Corrected Temperature Difference for Multipass Heat Exchanger
- 2.3. Influence of Bypass Streams on LMTD
- 2.4. Mean Weighted Temperature Difference
- 2.5. Determination of the Heat Exchanger Outlet Temperatures
- Chapter 3. Calculations of the Heat Transfer Coefficients and Pressure Losses in Convective Heat Transfer
- 3.1. Tube-Side Heat Transfer Coefficient
- 3.2. Shell-Side Heat Transfer Coefficient
- 3.3. Comparison of Different Calculation Models
- 3.4. Pressure Loss in Convective Heat Exchangers
- 3.5. Heat Exchanger Design with Heat Exchanger Tables
- Nomenclature
- Chapter 4. Geometrical Heat Exchanger Calculations
- 4.1. Calculation Formula
- 4.2. Tube-Side Calculations
- 4.3. Shell-Side Calculations
- Chapter 5. Dimensionless Characterization Number for the Heat Transfer
- 5.1. Reynolds Number Re for the Characterization of the Flow Condition
- 5.2. Prandtl Number Pr, Peclet Number Pe, and Temperature Conductivity a
- 5.3. Nusselt Number Nu for the Calculation of the Heat Transfer Coefficient
- 5.4. Stanton Number St for the Calculation of the Heat Transfer Coefficient
- 5.5. Colburn Factor JC for the Calculation of the Heat Transfer Coefficient
- 5.6. Kern Factor JK for the Calculation of the Heat Transfer Coefficient
- 5.7. Graßhof Number Gr for the Calculation of the Heat Transfer Coefficient in Natural Convection
- Chapter 6. Overall Heat Transfer Coefficient and Temperature Profile
- 6.1. Calculation of the Overall Heat Transfer Coefficient
- 6.2. Calculation of the Temperature Gradient in a Heat Exchanger
- 6.3. Viscosity Correction
- 6.4. Calculation of the Heat Transfer Coefficient from the Overall Heat Transfer Coefficient
- Nomenclature
- Chapter 7. Chemical Engineering Calculations
- 7.1. Vapor Pressure Calculations
- 7.2. Equilibrium between the Liquid and the Vapor Phase
- 7.3. Bubble Point Calculation
- 7.4. Dew Point Calculation
- 7.5. Calculation of Dew and Bubble Lines of Ideal Binary Mixtures
- 7.6. Flash Calculations
- 7.7. Condensation or Flash Curve of Binary Mixtures
- 7.8. Calculation of Nonideal Binary Mixtures
- 7.9. Flash Calculations for Multicomponent Mixtures
- Chapter 8. Design of Condensers
- Construction Types of Condensers
- 8.1. Condenser Construction Types
- 8.2. Heat Transfer Coefficients in Isothermal Condensation
- 8.3. Comparison of Different Calculation Models
- 8.4. Condensation of Vapors with Inert Gas
- 8.5. Condensation of Multicomponent Mixtures
- 8.6. Miscellaneous
- Nomenclature
- Chapter 9. Design of Evaporators
- 9.1. Evaporation Process
- 9.2. Evaporator Construction Types
- 9.3. Design of Evaporators for Nucleate Boiling
- 9.4. Design of Falling Film Evaporators
- Chapter 10. Design of Thermosiphon Reboilers
- 10.1. Thermal Calculations
- 10.2. Calculation of the Heat Transfer Coefficient
- 10.3. Calculation of the Two-Phase Density and the Average Density in the Reboiler
- 10.4. Flow Velocity wReb in the Reboiler
- 10.5. Determination of the Required Height H1 for the Thermosiphon Circulation or the Maximum Allowable Pressure Loss ΔPmax in Thermosiphon Circulation
- 10.6. Design of Riser and Downcomer Diameter
- 10.7. Calculation of the Pressure Losses in the Thermosiphon Circulation
- 10.8. Calculation of the Required Reboiler Length or Area for the Heating up to the Boiling Temperature and for the Evaporation in Vertical Thermosiphon Evaporators
- 10.9. Required Heating Length for Vertical Thermosiphon Reboilers According to Fair
- 10.10. Calculation of the Pressure and Boiling Point Increase by Means of the Liquid Height H1
- 10.11. Average Overall Heat Transfer Coefficient for Heating + Vaporizing
- 10.12. Calculation of the Vapor Fraction x of the Two-Phase Mixture in a Vertical Reboiler
- 10.13. Thermosiphon Reboiler Design Example
- Chapter 11. Double Pipe, Helical Coil, and Cross Flow Heat Exchanger
- 11.1. Double Pipe and Multipipe Heat Exchangers
- 11.2. Helical Coil Heat Exchanger
- 11.3. Cross Flow Bundle
- Nomenclature
- Chapter 12. Finned Tube Heat Exchangers
- 12.1. Why Finned Tube Heat Exchangers?
- 12.2. What Parameters Influence the Effectiveness of Finned Tubes?
- 12.3. Finned Tube Calculations
- 12.4. Application Examples
- Index
- Edition: 1
- Published: September 29, 2015
- Language: English
MN
Manfred Nitsche
Dr. Nitsche's extensive experience includes designing and building distillation units, tank farms, stirred tank reactor facilities, air purification units and absorption and stripping units for various applications.
RG
Raji Olayiwola Gbadamosi
Following this he worked at Claudius Peters AG - a subsidiary of Babcock in the 1970s - designing process systems for the cement industry. Mr. Gbadamosi joined BP Germany in 1975 as a senior process engineer where he was responsible for
designing heat exchangers.
In 1988 he set up the consulting company RAM Systeme PRO SIM Ingenieurbüro GmbH in Hamburg, Germany with a dynamic team of chemical, mechanical engineers and chemists. Since then, he has served the process industries and academic
institutions of Germany and Europe. Some clients include: BASF, BP, Beiersdorf, DEA, DVFG, Infineon (formally Hoechst), Sasol, Shell,TEXACO, Sulzer Chemtech, Technical University of Hamburg-Harburg, Helmut Schmidt (German Armed Forces) University, University of Clausthal-Zellerfeld, Fachhochschule Bingen, Fachhochschule Düsseldorf and many others.