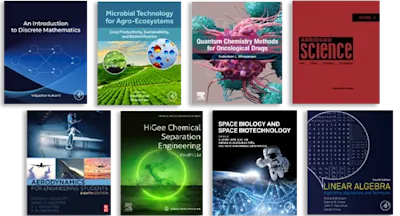
Handbook of Thin Film Deposition
Theory, Technology and Semiconductor Applications
- 5th Edition - October 24, 2024
- Imprint: Elsevier
- Editors: Dominic Schepis, Krishna Seshan
- Language: English
- Paperback ISBN:9 7 8 - 0 - 4 4 3 - 1 3 5 2 3 - 1
- eBook ISBN:9 7 8 - 0 - 4 4 3 - 1 3 5 2 4 - 8
Handbook of Thin Film Deposition: Theory, Technology and Semiconductor Applications, Fifth Edition, is a comprehensive reference focusing on thin film technologies and applicati… Read more
Purchase options
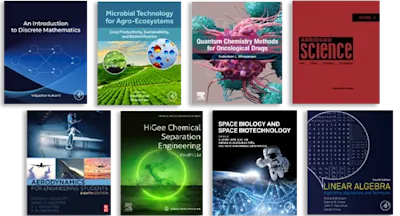
Handbook of Thin Film Deposition: Theory, Technology and Semiconductor Applications, Fifth Edition, is a comprehensive reference focusing on thin film technologies and applications used in the semiconductor industry and the closely related areas of thin film deposition, thin film microproperties, ferroelectric films, LED research, and materials for memory applications, and other thin film applications.
Of particular note in this new edition is the coverage of “reduction to practice,” a phase where the idea for a technology transitions from a concept to actual implementation. This section includes chapters that review the most relevant methods to fabricate thin films toward practical applications. This book also discusses the latest applications of various thin film deposition technologies.
Handbook of Thin Film Deposition: Theory, Technology and Semiconductor Applications, Fifth Edition, is suitable for students, materials scientists, engineers, and managers working in academia or semiconductor-related R&D.
- Offers a practical survey of thin film technologies including design, fabrication, and reliability
- Covers core processes and applications in the semiconductor industry and discusses latest advances in new thin film development
- Features new chapters that review methods on front-end and back-end thin films
Part I Reduction to Practice
2. Process Integration for On-Chip Interconnects
3. Sputter Processing
4. Epitaxial Thin Film Growth
5. CVD Processing and Processes
6. CMP: Scaling Down and Stacking Up: How the Trends in Semiconductors are Affecting Chemical-Mechanical Planarization
7. Limits of Gate Dielectric Scaling
Part II Applications and Limitations
8. Reliability Considerations for Thin Film Devices
9. Thin Film Development for LED Technologies
10. Emerging Ferroelectric Thin Films: Applications and Processing
11. Applications of Thin Film in Semiconductor Memories
12. Yield Issues and Defect Density in Thin Films
- Edition: 5
- Published: October 24, 2024
- Imprint: Elsevier
- Language: English
DS
Dominic Schepis
Dominic Schepis has over 35 years of experience in the semiconductor industry supporting logic and memory technologies. As a Principal Member of the Technical Staff at GlobalFoundries, Dominic worked on process development and integration for various advanced node CMOS technologies. His early work on SOI CMOS integration was instrumental to bringing this technology for use in IBM servers. He also was appointed Master Inventor at both IBM and GlobalFoundries and served on their patent evaluation boards. A graduate from Rensselaer Polytechnic Institute, he joined IBM’s Semiconductor Research and Development Center (SRDC) and has worked on a variety of advanced research and development projects and supported process sectors including reactive ion etching, epitaxial film growth, process integration, and other unit processes. During his tenure there, he coauthored over 29 technical journal papers and has over 100 issued US patents.
KS
Krishna Seshan
Krishna Seshan was an Assistant Professor in Materials Science at the University of Arizona with extensive professional experience as a technologist at both IBM and Intel Corporations. Dr. Seshan passed away in 2017.