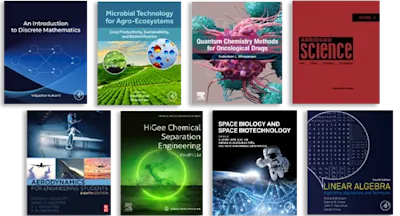
Handbook of Silicon Based MEMS Materials and Technologies
- 2nd Edition - September 22, 2015
- Editors: Markku Tilli, Mervi Paulasto-Kröckel, Teruaki Motooka, Veikko Lindroos
- Language: English
- Hardback ISBN:9 7 8 - 0 - 3 2 3 - 2 9 9 6 5 - 7
- eBook ISBN:9 7 8 - 0 - 3 2 3 - 3 1 2 2 3 - 3
The Handbook of Silicon Based MEMS Materials and Technologies, Second Edition, is a comprehensive guide to MEMS materials, technologies, and manufacturing that examines the state… Read more
Purchase options
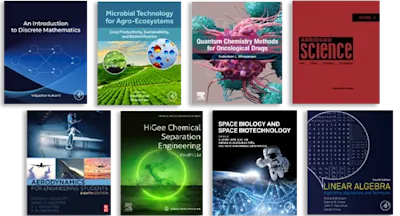
The Handbook of Silicon Based MEMS Materials and Technologies, Second Edition,
is a comprehensive guide to MEMS materials, technologies, and manufacturing that examines the state-of-the-art with a particular emphasis on silicon as the most important starting material used in MEMS.The book explains the fundamentals, properties (mechanical, electrostatic, optical, etc.), materials selection, preparation, manufacturing, processing, system integration, measurement, and materials characterization techniques, sensors, and multi-scale modeling methods of MEMS structures, silicon crystals, and wafers, also covering micromachining technologies in MEMS and encapsulation of MEMS components.
Furthermore, it provides vital packaging technologies and process knowledge for silicon direct bonding, anodic bonding, glass frit bonding, and related techniques, shows how to protect devices from the environment, and provides tactics to decrease package size for a dramatic reduction in costs.
- Provides vital packaging technologies and process knowledge for silicon direct bonding, anodic bonding, glass frit bonding, and related techniques
- Shows how to protect devices from the environment and decrease package size for a dramatic reduction in packaging costs
- Discusses properties, preparation, and growth of silicon crystals and wafers
- Explains the many properties (mechanical, electrostatic, optical, etc.), manufacturing, processing, measuring (including focused beam techniques), and multiscale modeling methods of MEMS structures
- Geared towards practical applications rather than theory
Engineers, researchers, research labs and companies working in the fields of MEMS, precision engineering and microfabrication; Research students in the area of MEMS
- List of Contributors
- Preface to the Second Edition
- Overview. Impact of Silicon MEMS—40 Years After
- 1 Introduction
- 2 Towards Mass Volumes of MEMS Devices
- 3 Towards Every Pocket
- 4 Mobile Phones, Smart Phones, and Tablets
- 5 Ubiquitous Sensing, Computing and Communication
- 6 Future of MEMS Technologies
- 7 Conclusions
- Acknowledgments
- References
- Part I: Silicon as MEMS Material
- Chapter 1. Properties of Silicon
- 1.1 Properties of Silicon
- References
- Chapter 2. Czochralski Growth of Silicon Crystals
- 2.1 The CZ Crystal-Growing Furnace
- 2.2 Stages of Growth Process
- 2.3 Selected Issues of Crystal Growth
- 2.4 Improved Thermal and Gas Flow Designs
- 2.5 Heat Transfer
- 2.6 Melt Convection
- 2.7 Magnetic Fields
- 2.8 Hot Recharging and Continuous Feed
- 2.9 Heavily n-Type Doped Silicon and Constitutional Supercooling
- 2.10 Growth of Large Diameter Crystals
- References
- Further Reading
- Chapter 3. Properties of Silicon Crystals
- 3.1 Dopants and Impurities
- 3.2 Typical Impurity Concentrations
- 3.3 Concentration of Dopants and Impurities in Axial Direction
- 3.4 Resistivity
- 3.5 Radial Variation of Impurities and Resistivity
- 3.6 Thermal Donors
- 3.7 Defects in Silicon Crystals
- 3.8 Control of Vacancies, Interstitials, and the OISF Ring
- 3.9 Oxygen Precipitation
- 3.10 Conclusions
- Acknowledgments
- References
- Chapter 4. Silicon Wafers: Preparation and Properties
- 4.1 Silicon Wafer Manufacturing Process
- 4.2 Standard Measurements of Polished Wafers
- 4.3 Sample Specifications of MEMS Wafers
- 4.4 Standards of Silicon Wafers
- References
- Chapter 5. Epi Wafers: Preparation and Properties
- 5.1 Silicon Epitaxy for MEMS
- 5.2 Silicon Epitaxy—The Basics
- 5.3 The Epi-Poly Process
- 5.4 Etch Stop Layers
- 5.5 Epi on SOI Substrates
- 5.6 Selective Epitaxy and Epitaxial Layer Overgrowth
- 5.7 Considerations for Chemical Mechanical Polishing
- 5.8 Metrology
- 5.9 Commercially Available Epitaxy Systems
- 5.10 Summary
- References
- Chapter 6. Thin Films on Silicon
- Chapter 6.1 Thin Films on Silicon: Silicon Dioxide
- Chapter 6.2 Thin Films on Silicon: Silicon Nitride
- Chapter 6.3 Thin Films on Silicon: Poly-SiGe for MEMS-Above-CMOS Applications
- Chapter 6.4 Thin Films on Silicon: ALD
- Further Reading
- Chapter 6.5 Piezoelectric Thin Film Materials for MEMS
- Chapter 6.6 Metallic Glass Thin Films
- Chapter 7. Thick-Film SOI Wafers: Preparation and Properties
- 7.1 Introduction
- 7.2 Overview of SOI
- 7.3 Silicon Wafer Parameters for Direct Bonding
- 7.4 Fabrication of Thick-Film BSOI by Mechanical Grinding and Polishing
- 7.5 BESOI Process
- 7.6 Techniques Based on Thin-Film SOI and Silicon Epitaxy
- 7.7 SOI Wafers with Buried Cavities
- 7.8 SOI Wafers with Buried ALD Thin Film
- 7.9 Conclusions
- References
- Chapter 1. Properties of Silicon
- Part II: Modeling in MEMS
- Chapter 8. Multiscale Modeling Methods
- 8.1 Macroscopic and Microscopic Equations
- 8.2 Computational Methods
- 8.3 First Principles Calculation Method
- 8.4 Concluding Remarks
- References
- Chapter 9. Mechanical Properties of Silicon Microstructures
- 9.1 Basic Structural Properties of Crystalline Silicon
- 9.2 Dislocations in Silicon
- 9.3 Physical Mechanisms of Fracture in Silicon
- 9.4 Physical Mechanisms of Fatigue of Silicon
- References
- Chapter 10. Electrostatic and RF-Properties of MEMS Structures
- 10.1 Introduction
- 10.2 Model System for a Dynamic Micromechanical Device
- 10.3 Electrical Equivalent Circuit
- 10.4 Electrostatic Force
- 10.5 Electromechanical Coupling
- 10.6 Sensing of Motion
- 10.7 Pull-in Phenomenon
- 10.8 Parasitic Capacitance
- 10.9 Effect of Built-in Potential on Capacitively Coupled MEMS-Devices
- 10.10 Further Effects of Electrostatic Nonlinearities from Applications Point of View
- 10.11 Application Example: Capacitively Coupled Reference Oscillator
- 10.12 RF-Properties
- 10.13 Acknowledgments
- References
- Chapter 11. Optical Modeling of MEMS
- 11.1 Introduction
- 11.2 Optical Properties of Silicon and Related Materials
- 11.3 Theoretical Background
- 11.4 Numerical Modeling Methods for Optical MEMS
- References
- Chapter 12. Modeling of Silicon Etching
- 12.1 Introduction
- 12.2 Requirements for Modeling Micromachining
- 12.3 Micromachining as a Front Propagation Problem
- 12.4 Anisotropic Etching: Geometrical Simulators
- 12.5 Anisotropic Etching: Atomistic Simulators
- 12.6 A Survey of Etching Simulators
- References
- Chapter 13. Gas Damping in Vibrating MEMS Structures
- 13.1 Introduction
- 13.2 Damping Dominated by Gas Viscosity
- 13.3 First-Order Frequency Dependencies
- 13.4 Viscoacoustic Models
- 13.5 Simulation Tools
- References
- Chapter 8. Multiscale Modeling Methods
- Part III: Measuring MEMS
- Chapter 14. Introduction to Measuring MEMS
- 14.1 On MEMS Measurements
- 14.2 Variation and Mapping
- 14.3 MEMS Measurement Challenges
- References
- Chapter 15. Silicon Wafer and Thin Film Measurements
- 15.1 Important Measurements
- 15.2 Wafer Shape
- 15.3 Resistivity
- 15.4 Thickness of Thin Films
- References
- Chapter 16. Optical Measurement of Static and Dynamic Displacement in MEMS
- 16.1 Camera-Based Measurements
- References
- Chapter 17. MEMS Residual Stress Characterization: Methodology and Perspective
- 17.1 Introduction
- 17.2 MEMS Residual Stress Characterization Techniques
- 17.3 Perspective and Conclusion
- References
- Chapter 18. Strength of Bonded Interfaces
- 18.1 Introduction
- 18.2 Solid Mechanics
- 18.3 Double Cantilever Beam Test Method
- 18.4 Tensile Test Method
- 18.5 Blister Test Method
- 18.6 Chevron Test Structures
- 18.7 Non-Destructive Bond Strength Testing of Anodic Bonded Wafers
- 18.8 Summary and Outlook
- References
- Chapter 19. Oxygen and Bulk Microdefects in Silicon
- 19.1 Measuring Oxygen in Silicon
- 19.2 Measuring Bulk Microdefects
- References
- Chapter 14. Introduction to Measuring MEMS
- Part IV: Micromachining Technologies in MEMS
- Chapter 20. MEMS Lithography
- 20.1 Lithography Considerations Before Wafer Processing
- 20.2 Wafers in Lithography Process
- 20.3 Processing After Lithography
- 20.4 Thick Photoresist Lithography
- 20.5 Special Lithography Approaches
- References
- Chapter 21. Deep Reactive Ion Etching
- 21.1 Etch Chemistries
- 21.2 Equipment
- 21.3 DRIE Processes
- 21.4 DRIE Advanced Issues and Challenges
- 21.5 DRIE Applications
- 21.6 Post-DRIE Etch Treatments
- 21.7 Choosing Between Wet and Dry Etching
- References
- Chapter 22. Wet Etching of Silicon
- 22.1 Basic Description of Anisotropic Etching: Faceting
- 22.2 Beyond Faceting: Atomistic Phenomena
- 22.3 Beyond Atomistics: Electrochemistry
- 22.4 Typical Surface Morphologies (I. Zubel and Miguel A. Gosálvez)
- 22.5 Effects from Silicon Wafer Features (Eeva Viinikka)
- 22.6 Convex Corner Undercutting
- 22.7 Examples of Wet Etching
- 22.8 Popular Wet Etchants
- 22.9 Temperature Dependence of the Etch Rate
- 22.10 Concentration Dependence of the Etch Rate
- 22.11 Other Variables Affecting the Etch-Rate Values
- 22.12 Experimental Determination of Etch Rates
- 22.13 Converting Between Different Measures of Concentration
- References
- Chapter 23. Porous Silicon Based MEMS
- 23.1 Porous Silicon Background
- 23.2 PS Sacrificial Layer Technologies
- 23.3 PS Fabrication Technology
- 23.4 Microscopic Processes Underlying PS Formation
- 23.5 Formation of Silicon Microstructures
- 23.6 Application Examples
- 23.7 Summary and Conclusions
- References
- Chapter 24. Surface Micromachining
- 24.1 Polycrystalline Silicon-Based Micromachining
- 24.2 Integration Concepts
- 24.3 Metallic MEMS
- 24.4 SOI-Wafer-Based Surface Micromachining
- References
- Chapter 25. Vapor Phase Etch Processes for Silicon MEMS
- 25.1 Vapor Phase Etch Technologies
- 25.2 Vapor HF Technology for MEMS Release
- 25.3 XeF2 Technology for MEMS Release
- 25.4 Applications
- References
- Chapter 26. Inkjet Printing, Laser-Based Micromachining and Micro 3D Printing Technologies for MEMS
- 26.1 Inkjet Printing for MEMS Fabrication
- 26.2 3D Micromachining Using Laser Ablation
- 26.3 3D Micromachining of Glass Using Laser-Writing and Etching
- 26.4 3D Printing Using Micro-Laser Sintering
- 26.5 3D Printing Based on Single-Photon Polymerization—Microstereolithography
- 26.6 3D Printing Based on Two-Photon Polymerization—3D Direct Laser Writing
- 26.7 3D Micromachining by Focused Ion Beam Milling
- 26.8 3D Micromachining by Focused Ion Beam and E-Beam Assisted Deposition
- 26.9 3D Micromachining Using Scanning Probe Lithography
- 26.10 Emerging 3D Printing Technologies for Micro and Nanostructures
- References
- Chapter 27. Microfluidics and BioMEMS in Silicon
- 27.1 Silicon Properties and Machining
- 27.2 Silicon as a Molding Master
- 27.3 Needles and Nozzles
- 27.4 Microreactors
- 27.5 Silicon-Based Gas Chromatography
- 27.6 Electrophoresis of Biomolecules in Silicon-Based Sieves
- 27.7 Microfluidics Integration with CMOS
- Acknowledgments
- References
- Chapter 20. MEMS Lithography
- Part V: Encapsulation and Integration of MEMS
- Chapter 28. Introduction to Encapsulation and Integration of MEMS
- 28.1 Challenges of MEMS Packaging
- 28.2 Early Work on Bulk-MEMS Devices
- 28.3 Hermetic Encapsulation in Surface Micromachining
- 28.4 Purposes of Hermetic Encapsulation
- 28.5 Wafer Bonding Methods
- 28.6 Sealing by Film Deposition
- 28.7 Heterogeneous Integration
- 28.8 Via Technologies
- 28.9 MEMS Reliability
- References
- Chapter 29. Silicon Direct Bonding
- 29.1 Hydrophilic High-Temperature Wafer Bonding
- 29.2 Hydrophobic High-Temperature Bonding of Silicon
- 29.3 Low-Temperature Direct Bonding of Silicon
- 29.4 Direct Bonding of CVD Oxides
- 29.5 Direct Bonding of CVD Silicon
- References
- Chapter 30. Anodic Bonding
- 30.1 Introduction
- 30.2 The Mechanism of the Anodic Bonding
- 30.3 Other Material Combinations
- 30.4 Glasses for Anodic Bonding
- 30.5 Bonding Parameters
- 30.6 Bond Quality, Failure Modes, and Characterization
- 30.7 The Thermal Residual Stress
- 30.8 The Pressure Inside Vacuum Sealed Cavities
- 30.9 The Effect of the Anodic Bonding on the Flexible Micromachined Structures
- 30.10 Electrical Effects
- 30.11 Bonding with Thin Films
- 30.12 Conclusions
- References
- Chapter 31. Glass Frit Bonding
- 31.1 Bonding Principle
- 31.2 Glass Frit Materials
- 31.3 Screen Printing
- 31.4 Thermal Conditioning
- 31.5 Bonding Process
- 31.6 Physics of Bonding
- 31.7 Characteristics
- 31.8 Conductive Glass Frit Bonding
- 31.9 Cost of Glass Frit Bonding
- References
- Further Reading
- Chapter 32. Metallic Alloy Seal Bonding
- 32.1 Properties of Metallic Seal Bonds
- 32.2 Metal Systems and Joint Design
- 32.3 Soft Soldering
- 32.4 Eutectic Bonding
- 32.5 TLP Bonding
- 32.6 Thermocompression Bonding
- 32.7 Ultra-Thin Metal Film Bonding
- 32.8 Reaction Bonding
- 32.9 Metallic Seal Ring Design and Process Technology
- References
- Chapter 33. Bonding of CMOS Processed Wafers
- 33.1 General Aspects, Requirements, and Limitations of CMOS-Compatible Wafer Bonding
- 33.2 CMOS-Compatible Low-Temperature Wafer Bonding
- 33.3 Anodic Bonding of CMOS-Processed Wafers
- 33.4 CMOS Wafer Glass Frit Bonding
- 33.5 Adhesive Bonding of CMOS Wafers
- 33.6 Conclusions
- References
- Chapter 34. Wafer-Bonding Equipment
- 34.1 Aligned Wafer-Bonding Requirements for MEMS Applications
- 34.2 Wafer-to-Wafer Aligners
- 34.3 Wafer Bonders
- 34.4 Aligned Wafer Bonding: Equipment Solutions for MEMS Manufacturing
- 34.5 The Future of Wafer Bonding Equipment Solutions for MEMS Manufacturing
- References
- Chapter 35. Encapsulation by Film Deposition
- 35.1 Introduction
- 35.2 Packaging Needs
- 35.3 Technologies and Methods
- 35.4 Application: Encapsulated Resonators for Frequency References
- 35.5 Summary
- References
- Chapter 36. Dicing of MEMS Devices
- 36.1 Introduction
- 36.2 History of Dicing
- 36.3 Process Flow and Methods of Dicing
- 36.4 Stealth Dicing
- 36.5 Full-Cut Dicing
- 36.6 Effects of Dicing
- 36.7 Conclusions
- References
- Chapter 37. 3D Integration of MEMS
- 37.1 Introduction
- 37.2 The Three Levels of MEMS Packaging
- 37.3 Cavity Formation
- 37.4 From Cavities to Surface Mountable Devices
- 37.5 From Device Packaging to SiP and 3D
- 37.6 Low Stress Packaging
- 37.7 Conclusions
- References
- Chapter 38. Via Technologies for MEMS
- 38.1 Through-Silicon Vias (TSV)
- 38.2 Classification of Through-Silicon Vias (TSV)
- 38.3 Various Processing Steps in TSV Fabrication
- 38.4 Overview of Various TSV Technologies
- 38.5 Reliability of TSVs
- 38.6 Future Outlook of TSVs for MEMS
- References
- Chapter 39. Outgassing and Gettering
- 39.1 Introduction
- 39.2 Gas Sources into MEMS Devices
- 39.3 Residual Gas Analysis (RGA) for MEMS
- 39.4 Outgassing Analysis
- 39.5 Getter Films for MEMS Devices
- 39.6 Lifetime
- 39.7 Conclusions
- References
- Chapter 40. Hermeticity Tests
- 40.1 Introduction
- 40.2 Basics of Leakage Measurement
- 40.3 Leakage Test Methods
- 40.4 Getter Pumps in MEMS Packages
- References
- Chapter 41. MEMS Reliability
- 41.1 Classification of MEMS Devices
- 41.2 Failure Mechanisms and Acceleration Factors
- 41.3 Reliability of Hermetic Encapsulation
- 41.4 Reliability Testing of MEMS Devices
- 41.5 Methods of Failure Analysis
- 41.6 Design for Reliability
- 41.7 Further Reading
- References
- Chapter 28. Introduction to Encapsulation and Integration of MEMS
- Appendix 1. Common Abbreviations and Acronyms
- A1.1 Definitions
- A1.2 List of Some Commonly Used MEMS Related Computational Programs
- Appendix 2. Nanoindentation Characterization of Silicon and Other MEMS Materials
- A2.1 Introduction
- A2.2 Nanoindentation Method
- A2.3 Indentation in Silicon
- References
- Index
- Edition: 2
- Published: September 22, 2015
- Language: English
MT
Markku Tilli
MP
Mervi Paulasto-Kröckel
TM
Teruaki Motooka
VL