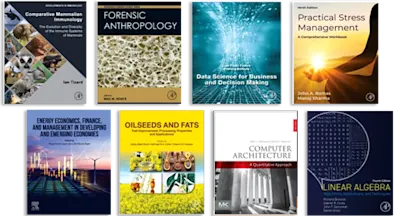
Handbook of Nonwovens
- 2nd Edition - June 1, 2022
- Imprint: Woodhead Publishing
- Author: S. J. Russell
- Language: English
- Paperback ISBN:9 7 8 - 0 - 1 2 - 8 1 8 9 1 2 - 2
- eBook ISBN:9 7 8 - 0 - 1 2 - 8 1 8 9 1 3 - 9
Handbook of Nonwovens, Second Edition updates and expands its popular interdisciplinary treatment of the properties, processing, and applications of nonwovens. Initial chapte… Read more
Purchase options
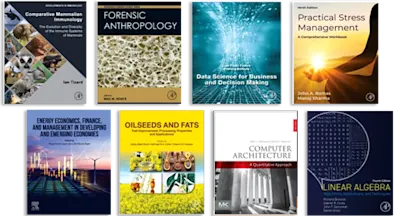
Handbook of Nonwovens, Second Edition updates and expands its popular interdisciplinary treatment of the properties, processing, and applications of nonwovens. Initial chapters review the development of the industry and the different classes of nonwoven material. The book then discusses methods of manufacture such as dry-laid, wet-laid, and polymer-laid web formation. Other techniques analyzed include mechanical, thermal, and chemical bonding, as well as chemical and mechanical finishing systems. The book concludes by assessing the characterization, testing, and modeling of nonwoven materials.
Covering an unmatched range of materials with a variety of compositions and manufacturing routes, this remains the indispensable reference to nonwovens for designers, engineers, materials scientists, and researchers, particularly those interested in the manufacturing of automotive, aerospace, and medical products. Nonwovens are a unique class of textile material formed from fibers that are bonded together through various means to form a coherent structure. The range of properties they can embody make them an important part of a range of innovative products and solutions, which continues to attract interest from industry as well as academia.
Covering an unmatched range of materials with a variety of compositions and manufacturing routes, this remains the indispensable reference to nonwovens for designers, engineers, materials scientists, and researchers, particularly those interested in the manufacturing of automotive, aerospace, and medical products. Nonwovens are a unique class of textile material formed from fibers that are bonded together through various means to form a coherent structure. The range of properties they can embody make them an important part of a range of innovative products and solutions, which continues to attract interest from industry as well as academia.
- Describes in detail the manufacturing processes of a range of nonwoven materials
- Provides detailed coverage of the mechanical and thermal properties of non-woven fabrics
- Includes extensive updates throughout on the characterization and testing of nonwovens
- Explains how to model nonwoven structures
MSc students and researchers with an interest in the properties of nonwoven materials. Product designers, technical managers, testing and characterisation staff, manufacturing engineers, and materials engineers working with nonwoven materials
1. Introduction
2. Status of the International Nonwovens Industry, Challenges, Opportunities and Future Directions
3. Overview of Nonwoven Product Applications (markets, product design, performance in use, design for end-of-life industry trends)
4. Raw Materials and Polymer Science for Nonwovens
5. Drylaid Web Formation (processes, structure and properties)
6. Wetlaid Web Formation (processes, structure and properties)
7. Spunmelt Nonwovens (processes, structure and properties)
8. Nanofibre Nonwovens (processes, structure and properties)
9. Composite Nonwovens (processes, structure and properties)
10. Mechanical Bonding (processes, structure and properties)
11. Chemical Bonding (processes, structure and properties)
12. Thermal Bonding (processes, structure and properties)
13. Nonwoven Finishes and Late-stage Functionalisation
14. Physical Testing and Characterisation of Nonwovens
15. Characterisation, 3D Imaging and Microscopic Features of Nonwoven Fabric Structure
16. Modelling of Fabric Properties
2. Status of the International Nonwovens Industry, Challenges, Opportunities and Future Directions
3. Overview of Nonwoven Product Applications (markets, product design, performance in use, design for end-of-life industry trends)
4. Raw Materials and Polymer Science for Nonwovens
5. Drylaid Web Formation (processes, structure and properties)
6. Wetlaid Web Formation (processes, structure and properties)
7. Spunmelt Nonwovens (processes, structure and properties)
8. Nanofibre Nonwovens (processes, structure and properties)
9. Composite Nonwovens (processes, structure and properties)
10. Mechanical Bonding (processes, structure and properties)
11. Chemical Bonding (processes, structure and properties)
12. Thermal Bonding (processes, structure and properties)
13. Nonwoven Finishes and Late-stage Functionalisation
14. Physical Testing and Characterisation of Nonwovens
15. Characterisation, 3D Imaging and Microscopic Features of Nonwoven Fabric Structure
16. Modelling of Fabric Properties
- Edition: 2
- Published: June 1, 2022
- Imprint: Woodhead Publishing
- Language: English
SR
S. J. Russell
Dr Stephen Russell is a Senior Lecturer in the Centre for Technical Textiles, University of Leeds and the Director of the Nonwovens Research Group (NRG), UK.
Affiliations and expertise
Senior Lecturer in the Centre for Technical Textiles, University of Leeds and the Director of the Nonwovens Research Group (NRG), UKRead Handbook of Nonwovens on ScienceDirect