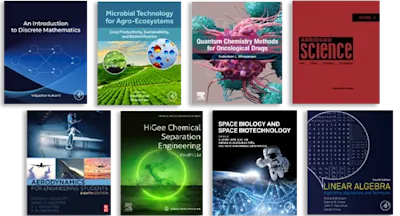
Fretting Wear and Fretting Fatigue
Fundamental Principles and Applications
- 1st Edition - December 9, 2022
- Editors: Tomasz Liskiewicz, Daniele Dini
- Language: English
- Paperback ISBN:9 7 8 - 0 - 1 2 - 8 2 4 0 9 6 - 0
- eBook ISBN:9 7 8 - 0 - 1 2 - 8 2 4 0 9 7 - 7
Fretting Wear and Fretting Fatigue: Fundamental Principles and Applications takes a combined mechanics and materials approach, providing readers with a fundamental unders… Read more
Purchase options
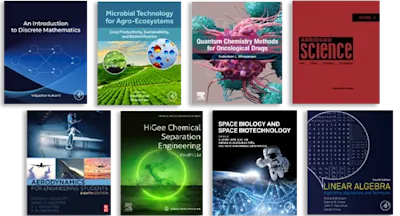
- Covers theoretical fundamentals, modeling and experimentation techniques, and applications of fretting wear and fatigue
- Takes a combined mechanics and materials approach
- Discusses the differences and similarities between fretting wear and fretting fatigue as well as combined experimental and modeling methods
- Covers applications including medical implants, heat exchangers, bearings, automotive components, gas turbines, and more
Tribology and contact/surface mechanics researchers; Researchers working on bearings, aircraft components, automotive electrical connectors, medical implants, and steel wire ropes; graduate students in these areas. Professional engineers (aerospace, automotive, mechanical, biomedical, civil)
Contributors xiii
Preface xvii
Section I History and fundamental principles
1 Brief history of the subject
Daniele Dini and Tomasz Liskiewicz
1.1 Early stages
1.2 Initial milestones in the understanding of the mechanics of fretting
1.3 Crucial steps toward a better understanding of fretting wear and fretting fatigue
1.4 State of the art at the beginning of the new millennium
Acknowledgments
References
2 Introduction to fretting fundamentals
2.1 Fretting—complexities and synergies
Tomasz Liskiewicz and Daniele Dini
2.1.1 Fretting within a wider context of tribology
2.1.2 Fretting wear
2.1.3 Fretting fatigue
2.1.4 Mitigating fretting damage
References
2.2 Contact mechanics in fretting
Daniele Dini and Tomasz Liskiewicz
2.2.1 Contact geometry
2.2.2 Friction and fretting regimes
References 36
2.3 Transition criteria and mapping approaches
Tomasz Liskiewicz, Daniele Dini, and Yanfei Liu
2.3.1 Transition criteria
2.3.2 Mapping approaches
References
2.4 Experimental methods
Tomasz Liskiewicz, Daniele Dini, and Thawhid Khan
2.4.1 Early developments
2.4.2 Basic test configurations
2.4.3 Fretting wear tests and analytical methods
2.4.4 Fretting fatigue tests and analytical methods
2.4.5 Combined fretting wear and fatigue approaches
References
2.5 Modelling approaches
Daniele Dini and Tomasz Liskiewicz
2.5.1 Theoretical models
2.5.2 Numerical models
References
Section II Fretting wear
3.1 The role of tribologically transformed structures and debris in fretting of metals
Philip Howard Shipway
3.1.1 Overview
3.1.2 Wear in both sliding and fretting—Contrasts in the transport of species into and out of the contacts
3.1.3 The nature of oxide debris formed in fretting
3.1.4 Formation of oxide debris in fretting—The role of oxygen supply and demand
3.1.5 Tribo-sintering of oxide debris and glaze formation
3.1.6 Microstructural damage—Tribologically transformed structures in fretting
3.1.7 The critical role of debris in fretting: Godet’s third body approach
3.1.8 Godet’s third body approach revisited: Rate-determining processes in fretting wear
3.1.9 Conclusion
References
3.2 Friction energy wear approach
Siegfried Fouvry
3.2.1 Friction energy wear approach
3.2.2 Basics regarding friction energy wear approach
3.2.3 Influence of contact loadings regarding friction energy wear rate
vi Contents
3.2.4 Influence of ambient conditions
3.2.5 Surface wear modeling using the friction energy density approach
3.2.6 Conclusions
References
3.3 Lubrication approaches
Taisuke Maruyama
3.3.1 Introduction
3.3.2 Parameter definition
3.3.3 Oil lubrication
3.3.4 Grease lubrication
3.3.5 Mechanism for fretting wear reduction in grease lubrication
3.3.6 Conclusions
Acknowledgments
References
3.4 Impact of roughness
Krzysztof J. Kubiak and Thomas G. Mathia
3.4.1 Introduction
3.4.2 Contact of rough surfaces
3.4.3 Stress distribution in rough contact
3.4.4 Effective contact area
3.4.5 Coefficient of friction
3.4.6 Bearing capacity
3.4.7 Surface anisotropy and orientation
3.4.8 Transition between partial and gross slip
3.4.9 Impact of surface roughness on fretting wear
3.4.10 Friction in lubricated contact conditions
3.4.11 Energy dissipated at the interfaces for smooth and rough surfaces
3.4.12 Impact of surface roughness on crack initiation
3.4.13 Dynamics of surface roughness evolution in fretting contact
3.4.14 Measurement of fretting wear using surface metrology
References
3.5 Materials aspects in fretting
Thawhid Khan, Andrey Voevodin, Aleksey Yerokhin, and Allan Matthews
3.5.1 Physical processes impacting materials in industrial fretting contacts
3.5.2 Factors affecting fretting behavior of different materials groups
Contents vii
3.5.3 Materials engineering approaches to the mitigation of fretting wear
3.5.4 Application of coatings to mitigate fretting wear
3.5.5 Advanced coating designs and architectures
3.5.6 Concluding remarks
References
3.6 Contact size in fretting
Ben D. Beake
3.6.1 Introduction
3.6.2 Experimental techniques for nano-/microscale fretting and reciprocating wear testing
3.6.3 Case studies
3.6.4 Conclusions
References
Section III Fretting fatigue
4.1 Partial slip problems in contact mechanics
David A. Hills and Matthew R. Moore
4.1.1 Introduction
4.1.2 Global and pointwise friction
4.1.3 Global and local elasticity solutions
4.1.4 Half-plane contacts: Fundamentals
4.1.5 Sharp-edged (complete) contact: Fundamentals
4.1.6 Partial slip of incomplete contacts
4.1.7 Dislocation-based solutions
4.1.8 Asymptotic approaches
4.1.9 Summary
Appendix 4.1.1 Eigenfunctions for the Williams’ wedge solution
Appendix 4.1.2 Size of the permanent stick zone for a Hertz geometry with large remote tensions
References
4.2 Fundamental aspects and material characterization
Antonios E. Giannakopoulos and Thanasis Zisis
4.2.1 Introduction
4.2.2 Mechanical models and metrics
4.2.3 The crack analogue approach
4.2.4 Modification of the crack analogue
4.2.5 Material testing and characterization
4.2.6 Looking ahead
References
viii Contents
4.3 Fretting fatigue design diagram
Yoshiharu Mutoh, Chaosuan Kanchanomai, and Murugesan Jayaprakash
4.3.1 Equations for estimating fretting fatigue strength based on strength of materials approach
4.3.2 Fracture mechanics approach for fretting fatigue life prediction
4.3.3 Fretting fatigue design diagram based on stresses on the contact surface
4.3.4 Summary
References
4.4 Life estimation methods
Toshio Hattori
4.4.1 Fretting fatigue features and fretting processes
4.4.2 Fretting fatigue crack initiation limit
4.4.3 High-cycle fretting fatigue life estimations considering fretting wear
4.4.4 Low-cycle fretting fatigue life estimations without considering fretting wear
4.4.5 Application of failure analysis of several accidents and design analyses
4.4.6 Conclusions
References
4.5 Effect of surface roughness and residual stresses
Jaime Domı´nguez, Jes
4.5.1 Introduction
4.5.2 Effect of surface roughness on fretting fatigue
4.5.3 Residual stresses in fretting
4.5.4 Modeling the effect of surface roughness on fretting
fatigue
4.5.5 Residual stress modeling in fretting fatigue
References
4.6 Advanced numerical modeling techniques for crack nucleation and propagation
Nadeem Ali Bhatti, Kyvia Pereira, and Magd Abdel Wahab
4.6.1 Introduction
4.6.2 Theoretical background
4.6.3 Numerical modeling
4.6.4 Crack nucleation prediction
4.6.5 Crack propagation lives estimation
4.6.6 Summary and conclusions
4.6.7 Way forward
References
Contents ix
4.7 A thermodynamic framework for treatment of fretting fatigue
Ali Beheshti and Michael M. Khonsari
4.7.1 Introduction
4.7.2 Thermodynamically based CDM
4.7.3 CDM analysis of fretting fatigue crack nucleation with provision for size effect
4.7.4 Fretting subsurface stresses with provision for surface roughness
4.7.5 CDM-based prediction of fretting fatigue crack nucleation life considering surface roughness
4.7.6 Conclusion and remarks
References
Section IV Engineering applications affected by fretting
5.1 Aero engines
John Schofield and David Nowell
5.1.1 Introduction
5.1.2 Examples of engine events
5.1.3 Areas subject to fretting
5.1.4 Mitigation measures
5.1.5 Design criteria—Academic perspective
5.1.6 Industrial applications perspective
5.1.7 Conclusions
References
5.2 Electrical connectors
Yong Hoon Jang, Ilkwang Jang, Youngwoo Park, and Hyeonggeun Jo
5.2.1 Introduction
5.2.2 Effects of fretting on electrical contact resistance
5.2.3 Fretting in industrial applications
5.2.4 Alternative solutions for fretting in electrical contacts
5.2.5 Summary
Acknowledgments
References
5.3 Biomedical devices
Michael G. Bryant, Andrew R. Beadling, Abimbola Oladukon, Jean Geringer, and Pascale Corne
5.3.1 Introduction
5.3.2 Common biomaterials
5.3.3 The biological environment
5.3.4 Compound tribocorrosion degradation mechanisms of materials in the biological environment
x Contents
5.3.5 In vivo fretting corrosion within the biological environment
5.3.6 Conclusions
References
5.4 Nuclear power systems
M. Helmi Attia
5.4.1 Introduction
5.4.2 Critical safety components of the nuclear reactor that are susceptible to fretting wear damage
5.4.3 Methodology for predicting fretting damage of nuclear structural components
5.4.4 Fretting wear of nuclear steam generator tubes—Effects of process parameters
5.4.5 Fretting Wear of nuclear fuel assembly—Effect of process parameters
5.4.6 Concluding remarks and future outlook
Acknowledgments
References
5.5 Rolling bearings
Amir Kadiric and Rachel Januszewski
5.5.1 Introduction
5.5.2 Mechanisms of false brinelling in rolling bearings
5.5.3 Test methods for assessing lubricant protection against fretting wear in bearings
5.5.4 Progression of false brinelling damage
5.5.5 Influence of lubricant properties and contact conditions on false brinelling
5.5.6 Possible measures to mitigate false brinelling risk in rolling bearings
5.5.7 Fretting in nonworking surfaces of bearings
References
5.6 Overhead conductors
Jos
5.7.1 Introduction
5.7.2 Design methodology for fretting in flexible marine riser
5.7.3 Experimental characterization of pressure armor material
5.7.4 Global riser loading conditions and analysis
5.7.5 Local nub-groove fretting analysis
5.7.6 Fretting wear-fatigue predictions
5.7.7 Concluding remarks
Acknowledgments
References
Index
- Edition: 1
- Published: December 9, 2022
- Language: English
TL
Tomasz Liskiewicz
DD