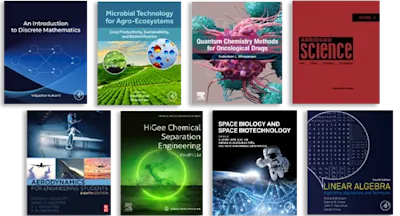
Fluid Catalytic Cracking Handbook
An Expert Guide to the Practical Operation, Design, and Optimization of FCC Units
- 4th Edition - April 16, 2020
- Author: Reza Sadeghbeigi
- Language: English
- Hardback ISBN:9 7 8 - 0 - 1 2 - 8 1 2 6 6 3 - 9
- eBook ISBN:9 7 8 - 0 - 1 2 - 8 1 2 6 6 4 - 6
Fluid Catalytic Cracking Handbook: An Expert Guide to the Practical Operation, Design, and Optimization of FCC Units, Fourth Edition, enables readers to maximize the profitabi… Read more
Purchase options
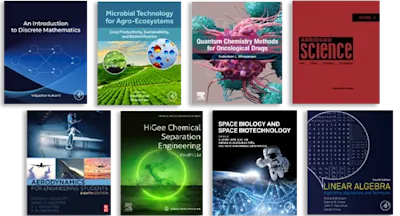
Fluid Catalytic Cracking Handbook: An Expert Guide to the Practical Operation, Design, and Optimization of FCC Units, Fourth Edition, enables readers to maximize the profitability and reliability of fluid catalytic cracking operations by covering all stages of FCC, including their design, operation, troubleshooting and optimization. It includes valuable chapters on FCC Main Fractionator and Gas Plant and Process Engineering Tools that provide engineers with the relevant tools they need to fully optimize processes and operations. This book presents technologies and processes that will improve the profitability and reliability of FCC units, along with lessons from Mr. Sadeghbeigi’s 30 years of field experience.
The book provides a valuable reference for experienced engineers, but is also an ideal reference for those who are developing their skills and knowledge base.
- Presents relevant, real world examples that enable petrochemical engineers to achieve real term savings
- Contains dedicated chapters on lessons learned from troubleshooting cases carried out by the author
- Includes sections on FCC Main Fractionator and Gas Plant
- Covers both SI and Imperial Units throughout
Petrochemical and process engineers
- Edition: 4
- Published: April 16, 2020
- Language: English
RS