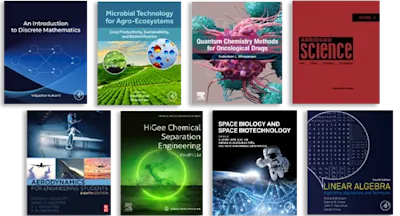
Flow Assurance in Pipelines
A Reference Guide
- 1st Edition - August 29, 2025
- Authors: Saeid Mokhatab, Juan Manzano-Ruiz, Antonin Chapoy, Jonathan J. Wylde
- Language: English
- Paperback ISBN:9 7 8 - 0 - 3 2 3 - 9 6 1 0 9 - 7
- eBook ISBN:9 7 8 - 0 - 3 2 3 - 9 9 3 8 9 - 0
Flow assurance is critical for effective design and operation of hydrocarbon production and transmission systems. The aim is to ensure safe and economical flow of hydrocarbon fl… Read more
Purchase options
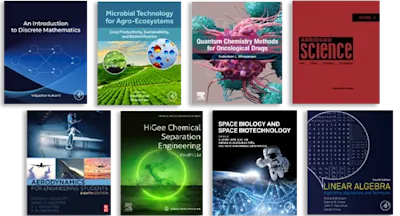
Flow assurance is critical for effective design and operation of hydrocarbon production and transmission systems. The aim is to ensure safe and economical flow of hydrocarbon fluids from the source to the markets. As future development of hydrocarbon resources moves into more challenging environments, the importance of flow assurance is becoming more asserted.
Written by an internationally recognized team of experts, Flow Assurance in Pipelines: A Reference Guide is a unique, well-researched, and comprehensive work in the flow assurance discipline that addresses the stages of a flow assurance study and identifies how they relate to the pipeline system design and operation. This book is a fundamental resource for flow assurance engineers, pipeline engineers, operators, and production chemists, providing a detailed explanation of basic flow assurance issues that can arise in the pipeline systems and discusses practical methods to solve those issues, safely and cost effectively.
- Provides a systematic understanding of the concept of flow assurance
- Discusses flow assurance challenges in pipelines and how to overcome them
- Reviews latest flow assurance technologies, engineering principles, and practices
- Describes the best operating philosophies of pipeline systems to minimize flow assurance risks
- Explores sustainable pipeline applications in the transition to a low-carbon economy
Flow assurance engineers, pipeline engineers and operators, production chemists and engineers as well as scientists, academics, and scholars working in the flow assurance discipline.
1. Pipeline Transportation of Hydrocarbons
1.1 Introduction
1.2 Oil and Gas Production
1.2.1 Reservoir Boundary Conditions
1.2.2 Well Nodal Analysis
1.2.3 Reservoir Decline
1.2.4 Reservoir Pressure Maintenance
1.2.5 Produced Water
1.2.6 Increment of Gas-Oil Ratio
1.2.7 Delivery Point Boundary Condition
1.2.8 Upstream Processing
1.2.9 Production Delivery to Downstream Facilities
1.2.10 Produced Water Disposal
1.2.11 Chemical Injection Umbilical
1.2.12 Midstream Products
1.3 Well’s Production String
1.3.1 Vertical and Deviated Wells
1.3.2 Horizontal Wells
1.3.3 Well Clusters and Manifolds
1.4 Flowlines and Gathering Systems
1.4.1 Flowlines
1.4.2 Gathering System
1.4.3 Risers
1.4.4 Test Line
1.5 Export Pipelines
1.5.1 Gas Pipelines
1.5.2 Crude Oil Pipelines
1.5.3 Water Injection Lines
1.6 Offshore and Onshore Pipelines
1.6.1 Environmental Conditions
1.6.2 Bathymetry and Terrain Profile
1.7 Pipeline Construction
1.8 Pipeline Maintenance
1.9 References
2. PVT and Phase Behavior of Petroleum Fluids
2.1 Introduction 2.2 Fluid Composition
2.3 Phase Behaviour
2.3.1 Pure Component
2.3.2 Binary Mixtures
2.3.3 Multicomponent Fluids
2.4 Classification of Petroleum Fluids
2.4.1 Oil Systems
2.4.2 Retrograde Condensate Gas
2.4.3 Wet and Dry Gas
2.5 Compositional Analysis, PVT Experiments and Correlations
2.5.1 Definitions
2.5.2 Compositional Analysis
2.5.3 PVT Experiments
2.5.3.1 Flash Vaporization
2.5.3.2 Differential Liberation
2.5.3.3 Separator Tests
2.5.3.4 Constant Volume Depletion
2.5.4 Black Oil Correlations
2.5.4.1 Bubble Point Pressure
2.5.4.2 Oil Formation Volume Factor
2.5.4.3 Solution Gas Oil Ratio
2.5.4.4 Oil Viscosity
2.6 Phase Equilibria and Equations of State
2.6.1 Equilibrium Calculations
2.6.2 Cubic Equations of State
2.6.3 Other Equations of State
2.6.3.1 Statistical Associating Fluids Theory
2.6.3.2 Cubic Plus-Association Approach
2.6.3.3 Multiparameters Equation of State
2.6.4 Multiphase Isothermal Flash
2.7 Fluid Characterization
2.7.1 Critical and Physical Properties Estimation
2.7.1.1 Critical Properties Estimation
2.7.1.2 Molecular Weight Estimation
2.7.1.3 Acentric Factor Estimation
2.7.1.4 Characterization Methods based on PNA Determination
2.7.1.5 Method Selection
2.7.2 Splitting and Lumping Processes
2.7.2.1 Splitting Process
2.7.2.2 Lumping Process
2.8 Physical and Transport Properties
2.8.1 Density
2.8.2 Enthalpy and Heat Capacity
2.8.3 Joule-Thomson Coefficient
2.8.4 Speed of Sound
2.8.5 Viscosity
2.8.5.1 Hydrocarbon and Gas Viscosities
2.8.5.2 Water and Produced Water Viscosities
2.8.5.3 Oil–Water Emulsion Viscosities
2.8.6 Thermal Conductivity
2.8.7 Interfacial Tension / Surface Tension
2.8.7.1 Gas–Oil Surface Tension
2.8.7.2 Oil-Water Surface Tension and Gas-Water Surface Tension
2.9 References
3. Hydrocarbon Flow
3.1 Introduction
3.2 Single-Phase One-Dimensional Flow for Uniform Diameter Pipeline
3.2.1 Continuity Equation
3.2.2 Momentum Equation
3.2.3 Friction Head Term
3.2.4 Energy Equation
3.3 Two-Phase Flow
3.3.1 Two-Phase Flow Occurrence During Hydrocarbon Transportation
3.3.2 Two-Phase Flow Terminology
3.3.3 Two-Phase Flow Conservation Equations - Integral Models
3.3.3.1 Mass Conservation
3.3.3.2 Momentum Conservation
3.3.3.3 Energy Conservation
3.3.4 Flow Patterns
3.3.4.1 Gas-Liquid Flow
3.3.5 Two-Phase Flow Conservation Equations – Differential Models
3.3.5.1 Homogeneous Equilibrium Model
3.3.5.2 Drift-Flux Model 3.3.5.3 Two-Fluid Model
3.3.5.4 Mixture Flow (Separate Flow) Model
3.3.5.5 Mechanistic Models
3.3.5.6 Beggs and Brill Model
3.3.5.7 Brill and Mukherjee Model
3.3.5.8 Hasan and Kabir Model
3.3.6 Heat Transfer in Pipe
3.3.6.1 Internal Heat Transfer Coefficient
3.3.6.2 External Heat Transfer Coefficient
3.3.6.3 Buried Pipelines
3.3.6.4 Insulation Materials and Coatings
3.3.6.5 Active Pipeline Heating
3.3.7 Thermo-Hydraulic Simulations Workflow
3.4 References
4. Flow Assurance Concept
4.1 Introduction
4.2 Importance of Flow Assurance
4.3 Flow Assurance Principal Constraints
4.4 Flow Assurance Tasks and Workflow
4.4.1 Pipeline Design
4.4.2 Operation
4.4.2.1 Normal Operation
4.4.2.2 Transient Operations
4.4.2.3 Safe Operation
4.4.2.4 Environmental Concerns
4.5 Flow Assurance Work Process
4.5.1 Pre-Work
4.5.1.1 Fluid Sampling
4.5.1.2 Laboratory Analyses
4.5.1.3 Concept Definition
4.5.2 Scenarios Definition
4.6 Flow Assurance Strategies
4.6.1 Scenario Modelling
4.6.2 Operability Assurance
4.6.2.1 Prediction
4.6.2.2 Prevention and Mitigation
4.6.2.3 Remediation
4.6.2.4 Optimization
4.7 Flow Assurance Outlook
4.8 References
Part II - Fluid Related Risks
5. Hydrates
5.1 Introduction
5.2 Hydrate Thermodynamics and Structures
5.2.1 Gas Hydrate Formation and Stability Zone
5.2.2 Where Can Gas Hydrates Form?
5.2.3 Common Structures of Gas Hydrates
5.2.4 Hydrate Formers
5.2.5 Other Hydrate Structures and Structure Transition
5.2.6 Hydration Number
5.3 Water Content Determination of Natural Gas System
5.4 Predicting the Hydrate Stability Zone and Phase Equilibria
5.4.1 Hand Calculation Methods
5.4.2 Computer Aided – Thermodynamic Modelling
5.5 Hydrate Prevention Techniques
5.5.1 Water Removal
5.5.2 Pipeline System Depressurization
5.5.3 Thermal Methods
5.5.4 Chemical Methods
5.5.4.1 Thermodynamic Inhibitors
5.5.4.2 Low Dosage Hydrate Inhibitors
5.6 References
6. Petroleum Waxes
6.1 Introduction
6.2 What is Petroleum Wax?
6.2.1 Wax Appearance Temperature vs. Wax Disappearance Temperature
6.2.2 Pour Point
6.2.3 Wax Precipitation and Deposition
6.3 Wax Phase Behaviour of Petroleum Fluids
6.4 WAT / WDT Measurement
6.5 Thermodynamic of Wax Precipitation
6.5.1 Thermodynamic Modelling
6.5.2 High-Pressure Correction
6.5.3 Fluid Characterization
6.6 Viscosity of Oil and Wax Suspension
6.7 Wax Management and Remediation
6.7.1 Heating
6.7.2 Insulation
6.7.3 Solvents
6.7.4 Wax crystal modifier
6.7.5 Mechanical
6.8 References
7. Asphaltene
7.1 Introduction
7.2 What Are Asphaltenes?
7.2.1 Asphaltene Definition
7.2.2 Asphaltene Composition, Structure and Properties
7.2.3 Manifestations of Asphaltenes in Crude Oil
7.3 Formation and Impact of Asphaltene Deposits
7.3.1 Flocculation and Deposition of Asphaltenes
7.3.2 Asphaltene Destabilising Factors
7.3.3 Problematic Asphaltenic Crudes
7.3.4 Deposition Downhole and in the Reservoir
7.3.5 Deposition in Subsea and Topsides Production Systems
7.3.6 Asphaltene Impacts on Processing Systems
7.4 Asphaltene Stability Prediction
7.4.1 Influences on Asphaltene Prediction
7.4.2 Prediction Workflow
7.4.3 Reservoir Fluid Sampling
7.4.4 Experimental Testing for Asphaltene Stability
7.4.4.1 Simple Screening Techniques
7.4.4.2 Live Oil Asphaltene Onset Pressure Testing
7.4.4.3 Live Oil Asphaltene Deposition Tests
7.4.5 Asphaltene Precipitation Modelling
7.4.6 Asphaltene Deposition Modelling
7.5 Asphaltene Prevention and Remediation
7.5.1 Asphaltene Prevention
7.5.1.1 Non-Chemical Prevention
7.5.1.2 Chemical Prevention
7.5.1.3 Chemical Prevention Application Methods
7.5.1.4 Chemical Screening and Selection
7.5.2 Asphaltene Remediation
7.5.2.1 Non-Chemical Remediation
7.5.2.2 Chemical Remediation
7.5.2.3 Field Case Study
7.6 References
8. Scale
8.1 Introduction
8.2 Produced Water
8.2.1 Definitions and Significance
8.2.2 Characterization, Composition, and Sources of Water
8.2.2.1 The Chemistry of Formation Water
8.2.2.2 The Chemistry of Seawater
8.3 Scale Formation
8.3.1 Types of Mineral Scale and Basic Formation Mechanisms
8.3.1.1 Sulfates
8.3.1.2 Carbonates
8.3.1.3 Sulfides
8.3.1.4 Black Powder
8.3.1.5 Other Scale Types (Halite and Silica)
8.3.2 Crystal Nucleation and Growth Mechanisms
8.3.2.1 Homogeneous vs. Heterogeneous Nucleation
8.3.2.2 Crystal Growth
8.3.2.3 Adsorption
8.3.2.4 Deposition
8.4 Scale Precipitation Prediction
8.4.1 Why Use Scale Prediction?
8.4.2 Input and Output Information Data
8.4.3 Mineral Solubility Data
8.4.4 Shortcomings and Limitations
8.5 Operational Problems Due to Scales
8.5.1 Magnitude of the Problem
8.5.2 Scale Formation in a Multiphase Environment
8.5.3 Types of Issue 8.6 Scale Prevention and Remediation
8.6.1 Overview and Dealing with Scale – Strategies
8.6.2 Prevention
8.6.2.1 Mechanical and Unconventional Scale Prevention
8.6.2.2 Chemical Scale Inhibition
8.6.2.3 Chelation Chemistry
8.6.2.4 Scale Inhibitor Application Methods
8.6.2.5 Product Selection and Evaluation
8.6.2.6 Field Performance Monitoring
8.6.3 Remediation
8.6.3.1 Mechanical vs. Chemical
8.6.3.2 Scale Dissolvers
8.7 References
9. Naphthenates and Carboxylates
9.1 Introduction
9.1.1 Definition of Naphthenates and Carboxylates
9.1.2 Origin of Acidic Species
9.1.3 Structural Determination
9.2 Operational Challenges
9.2.1 Carboxylate Emulsions
9.2.2 Naphthenate Scales
9.2.3 Calcium in Crude
9.3 Mitigation Methods
9.3.1 Non-Chemical Methods
9.3.2 Chemical Methods
9.3.2.1 Removal
9.3.2.2 Prevention
9.4 Case Histories
9.5 References
Part III - Flow Related Risks
10. Flow Stability
10.1 Introduction
10.2 Principles of Flow Instability
10.3 Flow Pattern Instabilities
10.3.1 Stratified to Non-Stratified Flow Pattern Transition in Horizontal Flowlines
10.3.2 Transitions from Annular Flow in Horizontal Flowlines
10.3.3 Instability of Stratified-Smooth to Stratified-Wavy Pattern
10.3.4 Transition Between Dispersed Bubble and Intermittent Horizontal Flow
10.4 Slugging 10.4.1 Hydrodynamic Slugging
10.4.2 Terrain-Induced and Severe Slugging
10.4.3 Operationally Induced Slugging and Surging
10.5 Prediction of Slug Characteristics
10.6 Prevention and Control of Slugging
10.7 Examples of Slugging Simulation
10.7.1 Hydrodynamic Slugging of Live Oil Flow Through Horizontal Flowline
10.7.2 Severe Slugging in a Pipeline/Riser System
10.7.3 Transient Study of Severe Slugging at Riser
10.7.4 Surging Due to Pigging at Onshore Facilities
10.7.5 Choke Valve Control to Mitigate Slugging
10.8 References
11. Flow Integrity
11.1 Introduction
11.2 Pipeline Corrosion
11.3 Modes of Corrosion
11.3.1 Galvanic Corrosion
11.3.2 Stress-Corrosion Cracking
11.3.3 Pitting Corrosion
11.3.4 Hydrogen Embrittlement
11.3.5 Sulfide Stress Cracking
11.3.6 Cavitation Corrosion
11.3.7 Fatigue Corrosion
11.3.8 Microbial Induced Corrosion
11.4 Sweet Corrosion
11.4.1 Sweet Corrosion Models
11.5 Sour Corrosion
11.6 Corrosion in Flowlines
11.7 Corrosion in Pipelines
11.7.1 Corrosion in Oil Pipelines
11.7.2 Corrosion in Gas Pipelines
11.8 Erosion
11.9 Erosional Velocity
11.10 Corrosion Inhibitors
11.11 System Inspection
11.12 Corrosion and Erosion Prevention and Mitigation
11.13 References
12. Flow Deliverability
12.1 Introduction
12.2 Upstream Production Considerations
12.3 Flowline Sizing
12.3.1 Life of Field/Asset Design
12.3.2 Design and Operational Constraints
12.3.3 Risk of Erosion and Velocity Limits
12.3.4 Liquid Hold-up Management and Slugging
12.3.5 Optimum Size and Operating Envelope
12.3.6 Artificial Lift
12.4 Downstream Production Considerations
12.4.1 Host Facility Requirements
12.4.2 Emulsions Treatment
12.4.3 Foaming Control
12.5 References
13. Pipeline Operations Guidelines
13.1 Introduction 1
13.2 Normal or Steady-State Operation
13.2.1 Impacts of Production Profile on Normal Operation
13.2.2 Chemical Injection Philosophy
13.2.3 Production Support (Artificial Lift)
13.2.3.1 Gas Lift
13.2.3.2 Hydraulic and Electric Submersible Pumps
13.2.3.3 Multiphase Pumps
13.2.3.4 Subsea Compression
13.3 Transient Operations
13.3.1 Pre-Commissioning, Commissioning and First Start-up
13.3.2 Production Shutdown and Restart
13.3.3 Turn-down and Ramp-up
13.3.4 Pigging
13.3.5 Flushing and Hot Oiling
13.3.6 Depressurisation and Blowdown
13.4 Pipeline Online Operating Tools
13.5 References
14. The Role of Pipelines in Decarbonization
Appendices
Appendix A. Critical Properties Estimation Methods
Appendix B. Goossens Correlation for Molecular Weight Measurement
Appendix C. Acentric Factor Estimation Methods
Appendix D. PNA Based Estimation Methods
Appendix E. Splitting Schemes
Appendix F. Whitson Lumping Scheme
Appendix G. Flow Assurance Software Tools
- Edition: 1
- Published: August 29, 2025
- Language: English
SM
Saeid Mokhatab
JM
Juan Manzano-Ruiz
Juan J. Manzano-Ruiz has extensive international oil & gas field development experience over the past 40+ years in shallow, deepwater, and onshore Flow Assurance (FA), as a technical team lead, project manager, asset manager, and R&D technical contributor. He is currently President of PetroConsulting and Associates LLC in Katy, TX, United States. Prior to this, he worked for over 23 years at two major integrated companies, PDVSA and BP, in a variety of roles as Team Lead of R&D, Manager of Commercialization, Team Lead of Process Engineering, Facilities Manager, Sr. Production Engineer, and Asset Manager of an oil field in western Venezuela. He also served as Manager of Process Engineering for Jacobs Engineering, Manager of Flow Assurance for Technip-Genesis, and Flow Assurance Manager for Bechtel Oil & Gas, supporting numerous offshore/onshore oil & gas field development projects, on behalf of Clients such as BP, Exxon-Mobil, Shell, Chevron, Pemex, CNOOC, ADNOC, Petrobras, Enterprise, Enbridge, Burlington Resources, Lukoil, Newfield Exploration, Oiltanking, PTTEP, Schlumberger, and West Engineering. While working at PDVSA, he taught for 16 years several graduate and undergraduate mechanical and chemical engineering courses in Thermodynamics, Fluid Mechanics, Turbulent Fluid Flow, Compressible Fluid Flow, Multiphase Fluid Flow, Advanced Heat Transfer, Numerical Methods, and Optimization of Thermal Systems, at Universidad Simon Bolivar and Universidad Metropolitana in Caracas, Venezuela. After some time as an Adjunct Professor, he was granted Tenure as Full Professor of Engineering at Universidad Simon Bolivar. In the period 1991-1994, he was admitted into the Faculty of Engineering of the University of Bristol, United Kingdom, as a Visiting Professor and Researcher in drag-reduction of turbulent fluid flow. He has received the SME recognition from Technip’s College of Experts (Paris, France) and the Bechtel’s Distinguished Engineer acknowledgment. He has been engaged in several professional organizations throughout his career, including the GPA Midstream, ASME Multiphase Flow Committee, SPE Flow Assurance Technical Group, and AIChE Flow Assurance Forum; and has taught a number of training courses to oil & gas industry personnel with the Fleming organization. He received his PhD, Mech. E. and MSc degrees in Mechanical Engineering from the Massachusetts Institute of Technology (MIT) and his BSc degree in Industrial Engineering from the Universidad Catolica Andres Bello, Caracas, Venezuela. He also completed his MBA Minor Program from MIT Sloan Business School and holds a Professional Engineering license in the State of Texas.
AC
Antonin Chapoy
Antonin Chapoy is a Professorial Fellow of the Institute of GeoEnergy Engineering at Heriot-Watt University, Edinburgh, United Kingdom. He started his career at Heriot-Watt University in 2004, joining the Centre for Gas Hydrate Research (now the Hydrates, Flow Assurance & Phase Equilibria Research Group-HFAPE). His research interests include experimental measurement and thermodynamic modelling of fluid phase equilibria, thermophysical properties, gas hydrates, wax, and flow assurance. With over 24 years of research experience, he has managed a wide range of projects, predominately sponsored by industry. He teaches courses at postgraduate level, as well as offering several short courses to the industry. He is the author or coauthor of over 150 papers in peer-reviewed journals, 2 book chapters, 3 patents and more than 200 technical reports and conference papers, primarily concerning gas hydrates, flow assurance, transport properties, thermophysical properties of fluids and water-hydrocarbon phase behaviour. As of September 15, 2024, he has more than 7,228 citations with an h-index of 49. He sits or has been involved in the editorial boards of many peer-reviewed scientific journals, including the Journal of Natural Gas Science & Engineering, and Molecules. Since 2014, he is also an Associate Fellow with the Centre of Thermodynamics of Processes of Mines ParisTech, France. He holds a DEA (MSc) in Chemical Engineering from Université d'Aix-Marseille (2001), an MSc in Energy Engineering from Institut Universitaire des Systémes Thermiques et Industriels (2001), and a PhD in Chemical Engineering from Paris School of Mines (2004).
JW