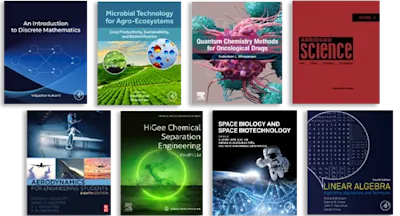
Fatigue Testing and Analysis of Results
- 1st Edition - October 22, 2013
- Author: W. Weibull
- Language: English
- eBook ISBN:9 7 8 - 1 - 4 8 3 1 - 5 4 1 6 - 9
Fatigue Testing and Analysis of Results discusses fundamental concepts of fatigue testing and results analysis. The book begins with a description of the symbols and nomenclature… Read more
Purchase options
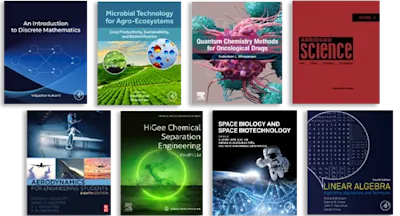
Fatigue Testing and Analysis of Results discusses fundamental concepts of fatigue testing and results analysis. The book begins with a description of the symbols and nomenclature selected for the present book, mainly those proposed by the ASTM Committee E-9 on Fatigue. Fatigue testing methods are then discussed including routine tests, short-life and long-life tests, cumulative-damage tests, and abbreviated and accelerated tests. Separate chapters cover fatigue testing machines and equipment; instruments and measuring devices; and test pieces used in fatigue testing. The factors affecting test results are considered, including material, types of stressing, test machine, environment, and testing technique. The final two chapters cover the planning of test programs and the presentation of results. Test program planning involves the statistical design of a test series; specification and sampling of test pieces; and choice of test pieces, testing machines, and test conditions. The chief purpose of most fatigue tests is the experimental determination of the relation between the endurance and the magnitude of the applied stress range for the material and the specimen under consideration, and final results can be condensed into a table, graph, or analytical expression.
Foreword
Chapter I. Symbols and Nomenclature
10. General
11. Applied Stress Cycles
12. Strengths and Fatigue Limits
13. Fatigue Life and Numbers of Cycles
14. Statistical Quantities and Mathematical Signs
15. Types of Applied Load Cycle
16. Variable-Stress Level Tests
Chapter II. Fatigue Testing Methods
20. General
21. Routine Tests
21.1. All-Failed Tests
21.2. Fraction-Failed Tests
22. Short-Life Tests
22.1. Constant-Stress Amplitude Tests
22.2. Constant-Strain Amplitude Tests
23. Long-Life Tests
23.1. Response Tests
23.2. Increasing-Amplitude Tests
24. Cumulative-Damage Tests
24.1. Preloading Tests
24.2. Prestressing Tests
25. Service-Simulating Tests
25.1. Program Tests
25.2. Spectrum Tests
26. Abbreviated and Accelerated Tests
27. Methods for Determining Crack Initiation and Crack Propagation
27.1. Non-destructive Tests
27.2. Destructive Tests
Chapter III. Fatigue Testing Machines and Equipments
30. General
31. Machines for General Purposes
31.1. Axial Loading
31.2. Repeated Bending
31.3. Rotating Bending
31.4. Torsion
31.5. Combined Bending and Torsion
31.6. Biaxial and Triaxial Loading
32. Machines for Special Purposes
32.1. High Frequencies
32.2. Elevated or Low Temperatures and Cyclic Thermal Stresses
32.3. Corroding Environments and Fretting Corrosion
32.4. Multi-Stress Level Tests
32.5. Contact Stresses
32.6. Repeated Impact
32.7. Combined Creep and Fatigue Tests
33. Equipments for Testing Parts and Assemblies
33.0. General
33.1. Wires, Tires and Ropes
33.2. Coil and Leaf Springs
33.3. Turbine and Propeller Blades
33.4. Large Specimens, Structures, Beams, Rails
33.5. Aircraft Structures
34. Components of Fatigue Testing Machines
34.0. General
34.1. Load-Producing Mechanisms
34.2. Load-Transmitting Members
34.3. Measuring Devices
34.4. Control Devices and Shut-off Apparatuses
34.5. Counters
34.6. Frameworks
35. Calibration and Checking of Testing Machines
35.0. General
35.1. Static Calibration and Checking
35.2. Dynamic Calibration and Checking
36. Accuracies of Actual Testing Machines and Equipments
Chapter IV. Instruments and Measuring Devices
40. General
41. Displacement-Measuring Instruments and Devices
41.0. General
41.1. Mechanical Instruments and Devices
41.2. Electrical Instruments and Devices Based on Measurement of Resistance, Inductance, or Capacitance
41.3. Photo-Electric Instruments and Devices
41.4. Optical Instruments and Devices
41.5. Pneumatic Instruments and Devices
42. Strain-Measuring Instruments and Devices
42.0. General
42.1. Mechanical Instruments and Devices
42.2. Electrical Instruments and Devices Based on Measurement of Resistance
42.3. Optical Instruments and Devices
43. Load-Measuring Instruments and Devices
43.0. General
43.1. Mechanical Instruments and Devices
43.2. Electrical Instruments and Devices
43.3. Piezo-Electric Instruments and Devices
43.4. Optical Instruments and Devices
44. Stress-Measuring Instruments and Devices
44.0. General
44.1. Optical Instruments and Devices
44.2. X-Ray Instruments and Devices
45. Instruments and Devices for Determining Surface Conditions
45.0. General
45.1. Stylus Methods
45.2. Taper Sectioning Methods
45.3. Optical Interference Methods
45.4. Optical Reflection Methods
45.5. Reflection Electron Microscopy
46. Instruments and Devices for Detecting Cracks, Flaws and Inhomogeneities
46.0. General
46.1. Microscopic Methods
46.2. Electrical-Resistance Methods
46.3. Eddy-Current Methods
46.4. Magnaflux Methods
46.5. Ultrasonic Methods
47. Instruments and Devices for Counting Numbers of Stress Cycles
47.0. General
47.1. Counters
47.2. Frequency-Measuring Instruments and Devices
Chapter V. Test Pieces: Design, Preparation, Measurement and Protection
50. General
51. Unnotched Specimens
51.0. General
51.1. Tension-Compression Specimens
51.2. Repeated-Bending Specimens
51.3. Rotating-Bending Specimens
51.4. Torsion Specimens
52. Notched Specimens
52.0. General
52.1. Circular Specimens
52.2. Flat Specimens
53. Simulated Components and Scaled Models
54. Actual Components
54.0. General
54.1. Bolted and Riveted Joints
54.2. Welded and Bonded Joints
54.3. Screw Connexions, Aircraft Joints, Attach Angles
54.4. Loaded Holes, Lugs
54.5. Structural Components, Beams, Sandwich Constructions
54.6. Aircraft Wings, Tail Planes
54.7. Fuselages
55. Preparation of Test Pieces
55.0. General
55.1. Mechanical Treatment
55.2. Heat Treatment
56. Measurements of Test Pieces
56.0. General
56.1. Measurement of Dimensions
56.2. Measurement of Surface Geometry
56.3. Measurement of Stress Distributions
57. Protection of Test Pieces
57.0. General
57.1. Protection against Mechanical Damage
57.2. Protection against Chemical Aggression
Chapter VI. Factors Affecting Test Results
60. General
61. Material
61.1. Composition and Heat Treatment
61.2. Structure in General—Grain Size
61.3. Inclusions and Inhomogeneities
61.4. Structural Surface Conditions Produced by Heat Treatment
61.5. Structural Surface Conditions Produced by Mechanical Treatment
61.6. Structural Changes Relating to Size of Test Piece
61.7. Structural Changes Caused by Preloading and Prestressing
61.8. Anisotropy
61.9. Origin
62. Type of Stressing
62.0. General
62.1. Tension-Compression
62.2. Repeated Bending
62.3. Rotating Bending
62.4. Torsion
62.5. Combined Bending and Torsion
62.6. Biaxial and Triaxial Stresses
62.7. Surface-Contact Stresses
62.8. Failure Criteria for Multi-Axial Stresses
63. Test Piece
63.0. General
63.1. Size
63.2. Shape
63.3. Stress Concentrations
63.4. Surface Condition
63.5. Residual Stresses
64. Testing Machine
64.0. General
64.1. Type of Loading
64.2. Design of Testing Machine
64.3. Speed
64.4. Accuracy of Individual Machines
64.5. Variations of Similar Machines
65. Environment
65.0. General
65.1. Temperature
65.2. Vacuum and Air
65 3. Non-corroding Environment
65.4. Corroding Environment
65.5. Fretting Corrosion
65.6. Sunlight and Heat Radiation
65.7. Nuclear Radiation
66. Testing Technique
66.1. Definition of Fatigue Life
66.2. Runout Number of Cycles
66.3. Rest Interval
Chapter VII. Planning of Test Programs
70. General
71. Design of Test Series
72. Specification and Sampling of Test Pieces
73. Choice of Test Piece
74. Choice of Testing Machine
Chapter VIII. Presentation of Results
80. General
81. Specification of Test Conditions
81.1. Material
81.2. Type of Applied Load
81.3. Test Piece
81.4. Testing Machine
81.5. Environment
81.6. Testing Technique
82. S-N and S-S Diagrams
82.1. The S-N Diagrams
82.2. The S-S Diagrams
83. Graphical and Analytical Representation of Strength and Life Distributions
84. P-S-N Diagrams
85. Analytical Representation of Load and Life Relations
85.1. Relations between Load and Life (S-N Equations)
85.2. Relations between Two Load Components (S1-S2 Equations)
86. Analytical Representation of Probability, Load and Life Relations
Chapter IX. Analysis of Results
90. General Statistical Concepts and Methods
90.0. General
90.1. Random Variables, Probability, Distribution and Frequency Functions Transformation of Random Variables
90.2. General Properties of Means, Variances and Covariances
90.3. Order Statistics. Principle of Probability Papers. Plotting Positions Random Sampling Numbers
90.4. Fitting of Curves to Observations
90.5. Estimates of Various Statistics
90.6. Significance Tests
90.7. Confidence and Tolerance Intervals
91. Determination of Average Load-Life Relations
91.1. Graphical Methods
91.2. Analytical Methods
92. Determination of Fatigue-Life Distributions
92.0. General
92.1. Graphical Methods
92.2. Analytical Methods
93. Determination of Fatigue-Strength Distributions
93.0. General
93.1. Graphical Methods
93.2. Analytical Methods
94. Determination of Probability-Load-Life Relations
94.0. General
94.1. Combination of Average S-N Curve and Deviations from It
94.2. Fitting P-S-N Diagrams to Observations, Shape of Distribution Unknown
94.3. Fitting P-S-N Diagrams to Observations, Shape of Distribution Assumed
95. Evaluation of Data from Response Tests
95.0. General
95.1. Probit Methods
95.2. Staircase Methods
96. Evaluation of Data from Increasing-Amplitude Tests
96.0. General
96.1. Step Tests
96.2. Prot Tests
Bibliography
- Edition: 1
- Published: October 22, 2013
- Language: English
Read Fatigue Testing and Analysis of Results on ScienceDirect