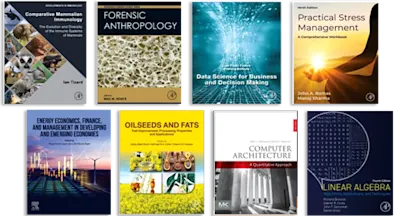
Extractive Metallurgy of Copper
- 6th Edition - December 3, 2021
- Imprint: Elsevier
- Authors: Mark E. Schlesinger, Kathryn C. Sole, William G. Davenport, Gerardo R.F. Alvear Flores
- Language: English
- Hardback ISBN:9 7 8 - 0 - 1 2 - 8 2 1 8 7 5 - 4
- eBook ISBN:9 7 8 - 0 - 1 2 - 8 2 1 9 0 3 - 4
Extractive Metallurgy of Copper, Sixth Edition, expands on previous editions, including sections on orogenesis and copper mineralogy and new processes for efficiently recoverin… Read more
Purchase options
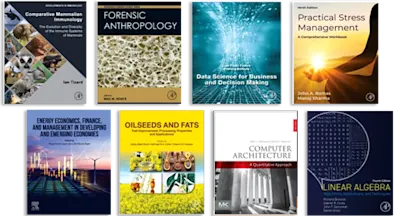
Extractive Metallurgy of Copper, Sixth Edition, expands on previous editions, including sections on orogenesis and copper mineralogy and new processes for efficiently recovering copper from ever-declining Cu-grade mineral deposits. The book evaluates processes for maintaining concentrate Cu grades from lower grade ores. Sections cover the recovery of critical byproducts (e.g., cesium), worker health and safety, automation as a safety tool, and the geopolitical forces that have moved copper metal production to Asia (especially China) and new smelting and refining processes. Indigenous Asian smelting processes are evaluated, along with energy and water requirements, environmental performance, copper electrorefining processes, and sulfur dioxide capture processes (e.g., WSA).
The book puts special emphasis on the benefits of recycling copper scrap in terms of energy and water requirements. Comparisons of ore-to-product and scrap-to-product carbon emissions are also made to illustrate the concepts included.
- Describes copper mineralogy, mining and beneficiation techniques
- Compares a variety of mining, smelting and converting technologies
- Provides a complete description of hydrometallurgical and electrometallurgical processes, including process options and recent improvements
- Includes comprehensive descriptions of secondary copper processing, including scrap collection and upgrading, melting and refining technologies
1. Overview
2. Production and use
3. Production of high copper concentratesdcomminution and flotation
4. Pyrometallurgical processing of copper concentrates
5. Theory to practice: pyrometallurgical industrial processes
6. Flash smelting
7. Bath matte smelting processes
8. Converting of copper matte
9. Continuous copper making processes
10. Copper loss in slag
11. Capture and fixation of sulfur
12. Fire refining (S and O removal) and anode casting
13. Electrolytic refining
14. Hydrometallurgical copper extraction: introduction and leaching
15. Solvent extraction
16 Electrowinning
17. Collection and processing of recycled copper
18. Chemical metallurgy of copper recycling
19. Melting and casting
20. Byproduct and waste streams
21. Costs of copper production
22. Toward a sustainable copper processing
- Edition: 6
- Published: December 3, 2021
- Imprint: Elsevier
- Language: English
MS
Mark E. Schlesinger
KS
Kathryn C. Sole
WD
William G. Davenport
Professor William George Davenport is a graduate of the University of British Columbia and the Royal School of Mines, London. Prior to his academic career he worked with the Linde Division of Union Carbide in Tonawanda, New York. He spent a combined 43 years of teaching at McGill University and the University of Arizona.
His Union Carbide days are recounted in the book Iron Blast Furnace, Analysis, Control and Optimization (English, Chinese, Japanese, Russian and Spanish editions).
During the early years of his academic career he spent his summers working in many of Noranda Mines Company’s metallurgical plants, which led quickly to the book Extractive Metallurgy of Copper. This book has gone into five English language editions (with several printings) and Chinese, Farsi and Spanish language editions.
He also had the good fortune to work in Phelps Dodge’s Playas flash smelter soon after coming to the University of Arizona. This experience contributed to the book Flash Smelting, with two English language editions and a Russian language edition and eventually to the book Sulfuric Acid Manufacture (2006), 2nd edition 2013.
In 2013 co-authored Extractive Metallurgy of Nickel, Cobalt and Platinum Group Metals, which took him to all the continents except Antarctica.
He and four co-authors are just finishing up the book Rare Earths: Science, Technology, Production and Use, which has taken him around the United States, Canada and France, visiting rare earth mines, smelters, manufacturing plants, laboratories and recycling facilities.
Professor Davenport’s teaching has centered on ferrous and non-ferrous extractive metallurgy. He has visited (and continues to visit) about 10 metallurgical plants per year around the world to determine the relationships between theory and industrial practice. He has also taught plant design and economics throughout his career and has found this aspect of his work particularly rewarding. The delight of his life at the university has, however, always been academic advising of students on a one-on-one basis.
Professor Davenport is a Fellow (and life member) of the Canadian Institute of Mining, Metallurgy and Petroleum and a twenty-five year member of the (U.S.) Society of Mining, Metallurgy and Exploration. He is recipient of the CIM Alcan Award, the TMS Extractive Metallurgy Lecture Award, the AusIMM Sir George Fisher Award, the AIME Mineral Industry Education Award, the American Mining Hall of Fame Medal of Merit and the SME Milton E. Wadsworth award. In September 2014 he will be honored by the Conference of Metallurgists’ Bill Davenport Honorary Symposium in Vancouver, British Columbia (his home town).
GA