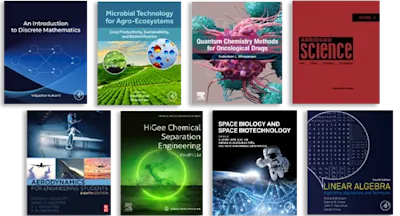
Essentials of Lean Six Sigma
- 1st Edition - June 15, 2006
- Imprint: Butterworth-Heinemann
- Author: Salman Taghizadegan
- Language: English
- Paperback ISBN:9 7 8 - 1 - 4 9 3 3 - 0 0 8 0 - 8
- Hardback ISBN:9 7 8 - 0 - 1 2 - 3 7 0 5 0 2 - 0
- eBook ISBN:9 7 8 - 0 - 0 8 - 0 4 6 2 3 2 - 5
Six Sigma is a management program that provides tools that help manufacturers obtain efficient, stream-lined production to coincide with ultimate high quality products. Es… Read more
Purchase options
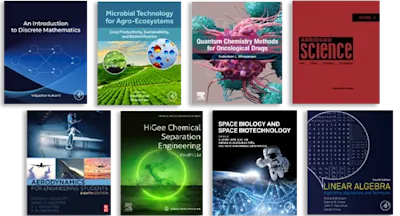
Six Sigma is a management program that provides tools that help manufacturers obtain efficient, stream-lined production to coincide with ultimate high quality products. Essentials of Lean Six Sigma will show how the well-regarded analytical tools of Six Sigma quality control can be successfully brought into the well-established models of “lean manufacturing,” bringing efficient, stream-lined production and high quality product readily together. This book offers a thorough, yet concise introduction to the essential mathematics of Six Sigma, with solid case examples from a variety of industrial settings, culminating in an extended case study.
Various professionals will find this book immensely useful, whether it be the industrial engineer, the industrial manager, or anyone associated with engineering in a technical or managing role. It will bring about a clear understanding of not only how to implement Six Sigma statistical tools, but also how to do so within the bounds of Lean manufacturing scheme. It will show how Lean Six Sigma can help reinforce the notion of “less is more,” while at the same time preserving minimal error rates in final manufactured products.
- Reviews the essential statistical tools upon which Six Sigma rests, including normal distribution and mean deviation and the derivation of 1 sigma through six sigma
- Explains essential lean tools like Value-Stream Mapping and quality improvement tools like Kaizen techniques within the context of Lean Six Sigma practice
- Extended case study to clearly demonstrate how Six Sigma and Lean principles have been actually implemented, reducing production times and costs and creating improved product quality
Graduate Students; Graduate Students in Industrial Engineering in courses on Quality Control, Reliability, Advances Production Control, Statistical Quality Control and Advanced Manufacturing
Graduate Business Students concentrating in Manufacturing and Industrial Management
Chapter 1. Introduction to Essentials of Lean Six Sigma (6)Strategies
1.1 Lean Six Sigma (6 ) Concepts Review
1.1.1 The Philosophy
1.1.2 Lean/Kaizen Six Sigma Engineering
1.2 Six Sigma Background
1.3 Some Six Sigma Successes
Chapter 2. Statistical Theory of Lean Six Sigma (6 ) Strategies
2.1 Normal Distribution Curve
2.2 Six Sigma Process Capability Concepts
2.2.1 Six Sigma Short Term Capability
2.2.2 Estimation of Six Sigma Long Term Capability
Chapter 3. Mathematical Concepts of Lean Six Sigma Engineering Strategies
3.1 Process Modeling (The heart of Lean Six Sigma)
3.2 The Normal Distribution
3.3 The Standard Normal Distribution
3.4 t-Distribution
3.4.1 Confidence interval for difference of two mean
3.5 Binomial Distribution
3.6 Poisson Distribution
3.7 Exponential Distribution
3.8 Hypegeometric Distribution
3.9 Normality Test
3.9.1 Kurtosis
3.9.2 Anderson Darling
3.10 Reliability Engineering and Estimation
3.11 Quality Cost
PART II Six Sigma Engineering and Implementation
Chapter 4. Six Sigma Continuous Improvement
4.1 Six Sigma Continuous Improvement Principles
4.2 Six Sigma Systems
4.2 Six Sigma Improvement and Training Model
Chapter 5. Design for Six Sigma
5.1 Design for Six Sigma (DFSS) Principles
5.2 Design for Six Sigma Steps
5.3 Tools and Techniques
5.4 Process Management
Chapter 6. Design for Lean/Kaizen Six Sigma
6.1 Lean Six Sigma and Principles
6.1.1 Elements of Lean Manufacturing/Production
6.1.2 Waste Types in the Lean Manufacturing
6.1.3 The Five Lean Themes and Steps
6.2 The Elements of Measurements
6.2.1 Strategic Measurement Model
6.2.2 Key Elements that Make a Product Successful in the Market Place
6.3 Competitive Product Benchmarking Concepts
6.4 Integration of Six Sigma, Lean and Kaizen
6.4.1 Six Sigma, Lean and Kaizen Principles
6.4.2 Prolong Production Performance (PPP)
6.4.3 A Lean Concept in Reduction of Lead-Time
6.5 Lean/Kaizen Six Sigma Infrastructure Evolution Tools and highlights in Summary
6.5.1 Corporate Commitment
6.5.2 Steps to Achieve the Six Sigma Goals
6.6 Mathematical Modeling of Lean Six Sigma Relations
6.6.1 Lean Six Sigma Experimental Design
Chapter 7. The Roles and Responsibilities to Six Sigma Philosophy and Strategy
7.1 The Roadmap to Six Sigma Philosophy and Strategy
7.2 Creation of Six Sigma Infrastructure
7.2.1 Executive Sponsor
7.2.2 Champion
7.2.3 Master Black Belt
7.2.4 Black Belt (Team Leader)
7.2.5 Green Belt (Team Participant)
7.2.6 Team Recognition/ Compensation
Chapter 8. The Road Map to Lean Six Sigma Continuous Improvement Engineering Strategies
8.1 Six-Sigma Continuous Improvement Engineering
8.2 Definition and Measurement
8.2.1 Phase 0: Process Definition/ Project Selection
8.2.1.1 Project Objectives and strategies
8.2.1.2 Process Definition Tools and Techniques
8.2.2 Phase I: Process Measurement
8.2.2.1 Process Measurement Objectives
8.2.2.2 Measurement Tools and Techniques
8.2.2.3 Key Basic Statistical Backgrounds
8.3 Evaluation of Existing Process Sigma/Base Line Sigma
8.4 Data Analysis
8.4.1 Phase II: Process Analysis
8.4.1.1 Process Analysis Objectives
8.4.1.2 Analysis Tools and Techniques
8.5 Optimization and Improvement
8.5.1 Phase III: Process Improvement
8.5.1.1 Process Improvement Objectives
8.5.1.2 Improvement Tools and Techniques
8.6 Evaluation of New Sigma
8.7 Process Control
8.7.1 Phase IV: Process Control and Maintain 8.7.1.1 Process Control Objectives
8.7.1.2 Control Tools and Techniques
PART III: Case Studies
Chapter 9
Case Study 9.1: Methodology for Machine Downtime
Reduction. A Green Belt methodology
9.1.1 Phase 0: Problem Statement
9.1.2 Phase 1: Data collection and measurement
9.1.3 Phase 2: Analysis of measurement
9.1.4 Phase 3: Improvement and verify the analyzed data
9.1.5 Phase 4: Control and maintain
Case Study 9.2: Methodology for Defect Reduction in Injection Molding Tools Life time. A Black Belt methodology.
9.2.1 Phase 0: Statement of Issues
9.2.2 Phase 1: Data collection and measurement
9.2.3 Phase 2: Analysis of collected data
9.2.4 Phase 3: The process of improvement
9.2.5 Phase 4: The process of control and maintain
Chapter 10. Case Study: Methodology for Defect Reduction in Injection Molding a Multi-Factor Central Composite Design Approach. A Master Black Belt methodology
10.1 Scope of Injection Molded Parts
10.2 Composite Design Methodology (Design Of Experiment)
10.3 Modeling (Prediction Equations)
10.4 Simulation
10.5 Conclusion
- Edition: 1
- Published: June 15, 2006
- Imprint: Butterworth-Heinemann
- Language: English
ST
Salman Taghizadegan
Hunter Industries, Inc.
San Marcos, CA