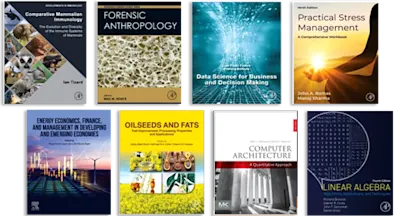
Ergonomic Solutions for the Process Industries
- 1st Edition - May 26, 2011
- Imprint: Gulf Professional Publishing
- Authors: Dennis A. Attwood, Joseph M. Deeb Ph.D. CPE M.Erg.S., Mary E. Danz-Reece
- Language: English
- Hardback ISBN:9 7 8 - 0 - 7 5 0 6 - 7 7 0 4 - 2
- Paperback ISBN:9 7 8 - 0 - 1 2 - 3 9 0 8 3 0 - 8
- eBook ISBN:9 7 8 - 0 - 0 8 - 0 4 7 0 0 7 - 8
Work-related injuries, such as back injuries and carpal tunnel syndrome, are the most prevalent, most EXPENSIVE, and most preventable workplace injuries, accounting for more than… Read more
Purchase options
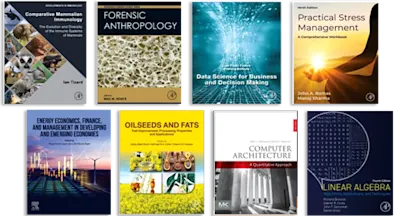
Work-related injuries, such as back injuries and carpal tunnel syndrome, are the most prevalent, most EXPENSIVE, and most preventable workplace injuries, accounting for more than 647,000 lost days of work annually (according to OSHA estimates). Such injuries, and many others, can be prevented in your facility by establishing an ergonomic design. This book shows you how to apply simple Ergonomic tools and procedures in your plant.Challenging worldwide regulations are forcing some companies to spend thousands of dollars per affected employee in order to comply. This book shows you how to comply with these regulations at a fraction of the cost, in the most timely, efficient method possible.
*Learn how to use the Human Factors/Ergonomics tools in process industries*Identify and prioritize Ergonomic issues, develop interventions, and measure their effects*Apply Ergonomics to the design of new facilities
The Process Industries, such as petrochemical, paper, and pharmaceutical: Safety engineers and project personnel within the process organization (usually at larger companies), safety consultants (smaller companies), and students in engineering courses.
PrefaceAcknowledgementsAuthor Disclaimer1. INTRODUCTION1.1 Introduction1.2 Chapter review1.2.1 Chapter 2: Personal Factors1.2.2 Chapter 3: Physical Factors1.2.3 Chapter 4: Environmental Factors1.2.4 Chapter 5: Equipment Design1.2.5 Chapter 6: Workplace Design1.2.6 Chapter 7: Job Factors1.2.7 Chapter 8: Information Processing1.2.8 Chapter 9: Human Factors in the Planning, Design and Execution of Projects1.3 Model for the Systematic Implementation of Ergonomics/ Human Factors1.4 Review Questions: Test your understanding of the Material in this Chapter1.5 References2. PERSONAL FACTORS2.1 Introduction2.2 Sensory and Cognitive Capabilities 2.2.1 Visual Sense 2.2.1.1 Accommodation of the Eye 2.2.1.2 Visual Field 2.2.1.3 Process of Adaptation 2.2.1.4 Color Vision 2.2.1.5 Visual Acuity 2.2.1.6 Age 2.2.2 Auditory Sense 2.2.3 Cognitive Capabilities 2.2.3.1 Attention 2.2.3.2 Perception 2.2.3.3 Memory 2.2.3.4 Decision Making 2.2.4 Summary of Information Processing2.3 Physical Capabilities 2.3.1 Muscular Strength and Endurance 2.3.1.1 Factors Affecting Strength 2.3.1.2 Endurance and Fatigue 2.3.2 Anthropometry: Body Size 2.3.2.1 Sources of Body Size Variability 2.3.2.2 Principles of Body Size Application2.4 Case Study 2.4.1 Method 2.4.1.1 Participants 2.4.1.2 Equipment 2.4.1.3 Procedure 2.4.2 Data Collected 2.4.2.1 Data Analyses 2.4.3 Conclusion 2.4.3.1 Recommendations for Existing Operations2.5 Review Questions: Test your understanding of the Material in this Chapter2.6 References3. PHYSICAL FACTORS3.1 Musculoskeletal Disorders3.2 Manual Handling Tasks3.2.1 Manual Handling Risk Factors3.2.2 Methods for Evaluation Manual Handling Tasks3.2.2.1 Postural Observation Checklists for Manual Handling Tasks3.2.2.2 Calculation of Weight Limit for Two-handed Lifting Tasks3.2.2.3 Biomechanical Models3.3 Hand-intensive Repetitive Tasks3.3.1 Risk Factors3.3.2 Survey/Observation Tools3.3.3 Hand Tools3.4 Behavior3.5 Ergonomics Program3.5.1 Risk Assessment Process3.5.2 Solutions3.5.3 Evaluating the Ergonomics Program3.6 Case Study3.7 Review Questions: Test Your Understanding of the Material in this Chapter3.8 References4. ENVIRONMENTAL FACTORS4.1 Introduction4.2 Illumination 4.2.1 Lighting and Performance 4.2.1.1 Lighting Quantity 4.2.1.2 Task Factors 4.2.1.3 Age Factor 4.2.1.4 Lighting Quality 4.2.1.4.1 Lighting Color 4.2.1.4.2 Glare 4.2.1.4.3 Luminance Ratio4.3 Temperature 4.3.1 Effects of Heat on Performance 4.3.1.1 Cognitive Tasks 4.3.1.2 Physical Activities 4.3.2 Effects of Cold on Performance 4.3.2.1 Cognitive Tasks 4.3.2.2 Physical Activities 4.3.3 Effects of Heat on Health 4.3.3.1 Hot Environment 4.3.3.2 Cold Environment 4.3.4 Comfort/Discomfort Zone 4.3.5 Work Tolerance in Hot Environment 4.3.6 Recommendations to Improve Working Conditions 4.3.6.1 Guidelines for Heat Conditions 4.3.6.2 Guidelines for Cold Conditions4.4 Noise 4.4.1 Effects of Noise on Performance 4.4.1.1 Speech and Communication 4.4.1.2 Cognitive Performance 4.4.1.3 Nuisance and Distraction 4.4.2 Effects of Noise on Health 4.4.2.1 Aging Hearing Loss 4.4.2.2 Noise-Induced Hearing Loss 4.4.3 Guidelines to Control Noise 4.4.3.1 Noise Control at Source 4.4.3.2 Noise Control in Path of Noise Transmission 4.4.3.3 Noise Control at The receiver4.5 Vibration 4.5.1 Effects of Vibration on Performance 4.5.1.1 Motor Control 4.5.1.2 Visual Performance 4.5.2 Effects of Vibration on Health 4.5.3 Guidelines to Reduce/Control Vibration4.6 Case Study 4.6.1 Method 4.6.2 Results 4.6.3 Recommendations 4.6.4 Installation of a Pilot Lighting System 4.6.5 Final Results4.7 Review Questions: Test Your Understanding of the Material in This Chapter4.8 References 5: EQUIPMENT DESIGN5.1 Human System Interface5.2 Controls5.2.1 Physical Requirements of Operating Controls5.2.2 Types of Controls5.2.3 Controls Labels and Identification5.2.4 Stereotypes5.2.5 Access to Operate5.2.6 Preventing Accidental Operation5.2.7 Valves5.3 Visual Displays5.3.1 Types of Visual Displays5.3.2 Mounting Displays5.4 Relationship between Controls and Visual Displays5.5 Auditory Displays5.6 Field Control Panels5.6.1 Field Panel Layout5.6.2 Field Panel Labeling5.6.3 Improving Field Control Panels5.7 Process Control Displays5.7.1 Process Control Display Interface5.7.1.1 Display Hierarchy5.7.1.2 Contents of Displays5.7.1.3 Display Layout5.7.1.4 Abbreviations and Labels5.7.1.5 Alarms5.7.1.6 Text Messages5.7.1.7 Lines and Arrows5.7.1.8 Numeric Values5.7.1.9 Use of Color5.7.1.10 Display Access5.7.1.11 Symbols5.7.2 Approach for developing Process Control Displays5.7.2.1 Initial Survey5.7.2.2 Scope the Improvements5.7.2.3 Prepare the Interface Design Team5.7.2.4 Brief the Board Operators5.7.2.5 Execute the Interface Design Effort5.7.2.6 Obtain Operator Feedback5.7.2.7 Transfer to the New System5.7.2.8 Summary5.8 Case Study5.9 Review Questions: Test Your Understanding of the Material in this Chapter5.10 ReferencesAPPENDIX 1: Checklist for Equipment Design6. WORKPLACE DESIGN6.1 Introduction6.2 Workplace Design Principles6.2.1 Introduction6.2.2 Controls and displays are optimally located6.2.3 Equipment is visually accessible6.2.4 The workplace is designed for the user population6.2.4.1: People differ in the characteristics necessary to perform within the workplace6.2.4.2: Workplaces are designed to accommodate the extremes of the user population6.2.4.3: Workplaces adjust to the characteristics of the user population6.2.5 Equipment is physically accessible6.2.5.1: Aisleways and corridors6.2.5.2: Distances are optimal between adjacent pieces of equipment6.2.5.3: Ladders, stairs, walkways and platforms6.2.5.3.1 Stairs, ladders and ramps6.2.5.3.2 Walkways and platforms6.2.5.4 Pathway obstructions: Eliminate or mark to increase recognition6.2.6 Positioning work6.2.6.1: Position work within the range of motion of the body6.2.6.2: Place frequently used materials and tools within easy reach6.2.6.3: Avoid static loads and fixed work postures6.2.6.4: Design to encourage frequent changes in body posture6.2.6.5: Avoid causing the upper limbs to work above the shoulder6.2.6.6: Avoid work that causes the spine to be twisted6.2.6.7: Ensure that the forces on the limbs and joints are within their capabilities6.2.6.8: Minimize manual handling6.2.6.9: Provide specialized tools to reduce body stress6.2.7 Design Standards: Workstations and seating are designed according to accepted Ergonomic Standards6.2.7.1: Major categories of workstations in the process workplace6.2.7.1.1 Seated workstations6.2.7.1.2 Standing workstations6.2.7.1.3 Sit/Stand workstations6.2.7.2 Selecting the optimal workstation design6.2.7.3: Workstation design standards6.2.7.3.1 Seated Workstations6.2.7.3.2 Standing Workstations6.2.7.3.3 Sit/Stand Workstations6.2.7.4 Seating6.2.8 Maintenance and maintainability6.2.8.1 Design considerations6.2.8.2 Maintenance considerations6.2.9 Summary of Design Principles6.3 Analytical techniques in workplace design: 6.3.1 Activity Analysis6.3.2 Task Analysis6.3.3 LINK Analysis6.4 Human Factors Design processes for existing and new workstations6.5 Case Study: Redesign of a control room in an existing plant6.6 Review Questions: Test Your Understanding of the material in this Chapter6.7 References7. JOB FACTORS7.1 Introduction7.2 Shiftwork and Work Schedule 7.2.1 Sleep and Sleep Disorders 7.2.1.1 Normal Sleep 7.2.1.2 Sleep Behavior and Disorders 7.2.1.3 Fatigue 7.2.2 Effects of Shiftwork on Performance 7.2.3 Effects of Shiftwork on Health 7.2.4 Effects of Shiftwork on Psychosocial Life 7.2.4.1 Shift Schedule Worked 7.2.4.2 Individual Differences 7.2.4.3 Personal and Social Life 7.2.5 Shiftwork Schedule Design 7.2.5.1 Length of Shift 7.2.5.2 Rotation of Shift 7.2.5.2.1 Direction of Rotation 7.2.5.2.2 Speed of Rotation 7.2.5.2.3 Number of Consecutive Days off 7.2.6 Coping Strategies with Shiftwork 7.2.6.1 Sleep 7.2.6.2 Diet 7.2.6.3 Keeping Body Clock in Synch 7.2.6.4 Personal and Mental Hygiene 7.2.6.5 Strategies for Night Work 7.2.6.6 Organizational Strategies 7.2.6.6.1 Education 7.2.6.6.2 Facilities Design 7.2.6.6.3 Career Opportunities 7.2.6.6.4 Planned Maintenance Napping 7.2.7 Process For Creating or Changing Shift Schedules7.3 Stress 7.3.1 Sources and Causes of Stress 7.3.2 Coping Strategies7.4 Job Analysis 7.4.1 Task Analysis 7.4.1.1 Purpose of Task Analysis 7.4.1.2 When to Use Task Analysis 7.4.1.3 Who can perform a Task Analysis? 7.4.1.4 Process of the Task Analysis 7.4.2 Critical Task Identification and Analysis Methodology 7.4.2.1 Critical Task Identification Process 7.4.2.2 Critical Task Analysis 7.4.2.3 Follow-up Documentation7.5 Team-Based Approach 7.5.1 Cognitive Problem Solving Style (KAI) 7.5.2 Drexler-Sibbett High Performance Team Model 7.5.3 ACUMEN 7.5.4 SYMLOG - Systematic Multilevel Observation of Groups7.6 Behavior-Based Safety 7.6.1 Lessons Learned 7.6.1.1 Implementation 7.6.1.2 During Training 7.6.1.3 Observations 7.6.1.4 Measure 7.6.1.5 Positive Outcomes 7.6.2 Recommended Core and Ancillary Elements of BBS Program 7.6.2.1 Recommended Program Elements 7.6.2.1 Practical Considerations for Implementation7.7 Case Study 7.7.1 Introduction 7.7.2 Task Analysis 7.7.3 Biomechanical Analysis7.8 Review Questions: Test your Understanding of the Material in this Chapter7.9 References8 INFORMATION PROCESSING8.1 Human Error 8.1.1 Introduction 8.1.2 Why humans make errors 8.1.3 Mental errors 8.1.4 Display errors 8.1.5 Environmental causes 8.1.6 System factors that lead to error8.2 Plant signs and labels 8.2.1 Equipment labeling program 8.2.2 Designing signs and labels 8.2.2.1 Content of the message 8.2.2.2 8.2.2.3 Message layout 8.2.2.4 Appearance of Characters 8.2.2.5 Placement of sign or label 8.2.3 Guidelines for specific types of signs and labels 8.2.3.1 Pipe labeling 8.2.3.2 Electrical wire and cables labeling 8.2.3.3 Equipment labels 8.2.3.4 Equipment signs 8.2.3.5 Sampling points 8.2.3.6 Information signs8.3 Procedures 8.3.1 Guidelines for when a procedure is needed 8.3.2 Developing procedures 8.3.3. Format of written procedures 8.3.4 How to determine why a procedure was not used 8.3.5 How to evaluate written procedures8.4 Training 8.4.1 Developing training 8.4.2 Task analysis for training development 8.4.3 Contents of a training package 8.4.4 Training for trainers 8.4.5 When to provide training 8.4.6 Evaluating training8.5 Vigilance 8.5.1 Transportation systems 8.5.2 Control room operations 8.5.3 Mining operations 8.5.4 Driving performance 8.5.6 Factors contributing to vigilance decrement 8.5.7 Operator workload analysis8.6 Case study: Procedure for how to change a tire8.7 Review questions: Test your understanding of the Material in this Chapter8.8 ReferencesATTACHMENT 1: Procedures evaluation checklist9. THE USE OF HUMAN FACTORS IN PROJECT PLANNING, DESIGN AND EXECUTION9.1 Introduction9.2 Project management9.2.1 Management of major projects9.2.2 Management of Base Projects9.3 Human Factors Tools for Project Management9.3.1 Human Factors Tracking DataBase9.3.2 HF Review -- Planning Phase9.3.3. Safety, Health and Environmental Review9.3.4. Human Factors Training for the Project Team9.3.5. Human Factors in the Hazard and Operability Reviews (HAZOP)9.3.6 Procedures9.3.7 Analysis Techniques9.3.8 QA/QC Review Process 9.3.9 Pre- Start-up Human Factors Review9.3.10 HF awareness for Construction Contractors and Company Personnel9.3.11 Post Project Review9.4 Review questions: Test your understanding of the Material in this Chapter9.5 References
- Edition: 1
- Published: May 26, 2011
- Imprint: Gulf Professional Publishing
- Language: English
DA
Dennis A. Attwood
Dennis Attwood has over 34 years of experience as a specialist in Human Factors Engineering and Ergonomics. He joined Risk, Reliability, Safety (RRS) Engineering USA in 2003 after 21 years with ExxonMobil Corporation as a Human Factors Specialist. Dennis has authored over 100 publications in the field, and holds a Bachelor's of Applied Science in Electrical Engineering and a Masters and Ph.D. in Industrial Engineering.
Affiliations and expertise
Risk Reliability and Safety Engineering LLC, Texas, USAJD
Joseph M. Deeb Ph.D. CPE M.Erg.S.
Joseph M. Deeb has over twenty years of experience in both University teaching and research and in applying Human Factors and Ergonomics to a wide range of industry businesses. Since joining ExxonMobil company,over 11years ago, Joe has provided Human Factors and Ergonomics global support for its operations. Joe has authored a number of external publications, both in refereed journals and conference proceedings, and internal reports.
Affiliations and expertise
ExxonMobil Biomedical Sciences Inc. , New Jersey, USAMD
Mary E. Danz-Reece
Mary Danz-Reece, a certified professional ergonomist, currently heads the
business planning section at ExxonMobil Biomedical Sciences, Inc. and has
previously headed the Human Factors and Chemicals Toxicology Sections.
Since joining ExxonMobil in 1991, Mary has provided human factors expertise
to ExxonMobil operations including on-and offshore production, refining,
chemical manufacturing, fuels marketing and mining operations. Mary has
been recognized for outstanding contributions to the field of ergonomics by
the Ergonomics division of the Institute of Industrial Engineers.
Affiliations and expertise
ExxonMobil Biomedical Sciences Inc. , New Jersey, USARead Ergonomic Solutions for the Process Industries on ScienceDirect