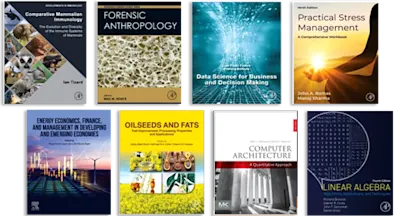
Electric Motors and Drives
Fundamentals, types and applications
- 1st Edition - January 1, 1990
- Imprint: Newnes
- Author: Austin Hughes
- Language: English
- Paperback ISBN:9 7 8 - 0 - 4 3 4 - 9 0 7 9 5 - 3
- eBook ISBN:9 7 8 - 1 - 4 8 3 1 - 0 5 2 7 - 7
Electric Motors and Drives: Fundamentals, Types and Applications provides information regarding the inner workings of motor and drive system. The book is comprised of nine chapters… Read more
Purchase options
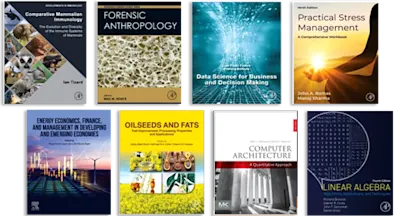
Electric Motors and Drives: Fundamentals, Types and Applications provides information regarding the inner workings of motor and drive system. The book is comprised of nine chapters that cover several aspects and types of motor and drive systems. Chapter 1 discusses electric motors, and Chapter 2 deals with power electronic converters for motor drives. Chapter 3 covers the conventional d.c. motors, while Chapter 4 tackles inductions motors – rotating field, slip, and torque. The book also talks about the operating characteristics of induction motors, and then deals with the inverter-fed induction motor drives. The stepping motor systems; the synchronous, switched reluctance, and brushless d.c. drives; and the motor/drive selection are also covered. The text will be of great use to individuals who wish to familiarize themselves with motor and drive systems.
Preface1 Electric Motors Introduction Producing Rotation Electromagnetic Force Magnetic Flux and Flux Density Force on a Conductor Magnetic Circuits Magnetomotive Force (MMF) Electric Circuit Analogy and Reluctance The Air-Gap Air-Gap Flux Densities Saturation Magnetic Circuits in Motors Torque Production Magnitude of Torque Slotting Specific Loadings and Specific Output Specific Loadings Torque and Motor Volume Specific Output Power - Importance of Speed Motional EMF Power Relationships - Stationary Conditions Power Relationships - Conductor Moving at Velocity V Equivalent Circuit Motoring Condition Behavior without Load Behavior when Loaded Relative Magnitudes of V, E and Efficiency General Properties of Electric Motors Operating Temperature and Cooling Torque per Unit Volume Power per Unit Volume - Importance of Speed Size Effects - Specific Torque and Efficiency Efficiency and Speed Rated Voltage Short-Term Overload2 Power Electronic Converters for Motor Drives Introduction General Arrangement of Drive Voltage Control - D.C. Output from D. C Supply Switching Control Transistor Chopper Chopper with Inductive Load - Over-Voltage Protection Features of Power Electronic Converters D.C. from A.C. - Controlled Rectification The Thyristor and Controlled Rectification Single Pulse Rectifier Single-Phase Fully Controlled Converter - Output Voltage and Control 3-Phase Fully Controlled Converter Firing Circuits A.C. from D.C. - Inversion Single-Phase Inverter Output Voltage Control Sinusoidal PWM 3-phase Inverter Forced and Natural Commutation Converter Waveforms and Acoustic Noise Cooling of Power Switching Devices Thermal Resistance Arrangement of Heat-Sinks and Forced-Air Cooling Cooling Fans3 Conventional D.C. Motors Introduction Torque Production Function of the Commutator Operation of the Commutator - Interpoles Motional E.M.F. Equivalent Circuit D.C. Motor - Steady-State Characteristics No-Load Speed Performance Calculation - Example Behavior when Loaded Base Speed and Field Weakening Transient Behavior - Current Surges Shunt, Series and Compound Motors Shunt Motor - Steady-State Operating Characteristics Series Motor - Steady-State Operating Characteristics Universal Motors Compound Motors Four Quadrant Operation and Regenerative Braking Full Speed Regenerative Reversal Dynamic Braking4 D.C. Motor Drives Introduction Thyristor D.C. Drives Motor Operation with Converter Supply Motor Current Waveforms Converter Output Impedance: Overlap Four-Quadrant Operation and Inversion Single-Converter Reversing Drives Double Converter Reversing Drives Power Factor and Supply Effects Control Arrangements for D.C Drives Current Control Torque Control Speed Control Overall Operating Region Armature Voltage Feedback and IR Compensation Drives without Current Control Chopper-Fed D.C. Motor Drives Performance of Chopper-fed D.C. Motor Drives Torque-Speed and Control Arrangements Developments in Industrial D. C Drives D.C Servo Drives Servomotors Position Control5 Induction Motors-Rotating Field, Slip and Torque Introduction Outline of Approach The Rotating Magnetic Field Production of Rotating Magnetic Field Field Produced by Each Phase-Winding Resultant Field Direction of Rotation Main (Air-Gap) Flux and Leakage Flux Magnitude of Rotating Flux Wave Excitation Power and VA Summary Torque Production Rotor Construction Slip Rotor Induced E.M.F., Current and Torque Influence of Rotor Current on Flux Reduction of Flux by Rotor Current Stator Current-speed Characteristics6 Operating Characteristics of Induction Motors Methods of Starting Cage Motors Star/Delta (Wye/Mesh) Starter Autotransformer Starter Resistance or Reactance Starter Solid-State Soft Starting Run-up and Stable Operating Regions High Inertia Loads - Overheating Steady-State Rotor Losses and Efficiency Steady-State Stability - Pull-out Torque and Stalling Torque-Speed Curves - Influence of Rotor Parameters Cage Rotor Double Cage Rotors Deep Bar Rotors Starting and Run-up of Slip-ring Motors Influence of Supply Voltage on Torque-Speed Curve Generating and Braking Generating Region - Overhauling Loads Plug Reversal and Plug Braking Injection Braking Speed Control Pole-Changing Motors Voltage Control of High-Resistance Cage Motors Speed Control of Wound-Rotor Motors Power-Factor Control and Energy Optimization Slip Energy Recovery (Wound-Rotor Motors) Single-Phase Induction Motors Principle of Operation Capacitor-Run Motors Split-Phase Motors Shaded-Pole Motors7 Inverter-Fed Induction Motor Drives Introduction Comparison with D.C. Drive Inverter-Fed Induction Motors Steady-State Operation - Importance of Achieving Full Flux Torque-Speed Characteristics - Constant V/f Operation Permissible Range of Continuous Operation Limitations Imposed by the Inverter - Constant Power and Constant Torque Regions Limitations Imposed by Motor Control Arrangements for Inverter-Fed Drives Open-Loop Speed Control Closed-Loop Speed Control Vector Control8 Stepping Motor Systems Introduction Open-Loop Position Control Generation of Step Pulses and Motor Response High Speed Running and Ramping Principle of Motor Operation Variable Reluctance Motor Hybrid Motor Summary Motor Characteristics Static Torque-Displacement Curves Single-Stepping Step Position Error and Holding Torque Half Stepping Step Division - Mini-Stepping Drive Circuits and Steady-State Characteristics Requirements of Drive Pull-Out Torque under Constant-Current Conditions Drive Circuits and Pull-Out Torque-Speed Curves Resonances and Instability Transient Performance Step Response Starting from Rest Optimum Acceleration and Closed-Loop Control9 Synchronous, Switched Reluctance and Brushless D.D. Drives Introduction Synchronous Motors Excited Rotor Motors Starting Power Factor Control Permanent-Magnet Synchronous Motors Hysteresis Motors Reluctance Motors Controlled-Speed Synchronous Motor Drives Open-Loop Inverter-Fed Synchronous Motor Drives Self-Synchronous (Closed-Loop) Operation Operating Characteristics and Control Switched Reluctance Motor Drives Principle of Operation Power Converter Characteristics and Control Brushless D.C. Motors Characteristics and Control10 Motor/Drive Selection Introduction Power Range for Motors and Drives Maximum Speed and Speed Range Load Requirements - Torque-Speed Characteristics Constant-Torque Load Fan and Pump Loads General Application Considerations Regenerative Operation and Braking Duty Cycle and Rating Enclosures and Cooling Dimensional Standards Supply Interaction and Harmonics Further ReadingIndex
- Edition: 1
- Published: January 1, 1990
- Imprint: Newnes
- Language: English
AH
Austin Hughes
Austin Hughes was a long-time member of the innovative motors and drives research team at the University of Leeds, UK, and has established a reputation for an informal style that opens up complex subjects to a wide readership, including students and managers as well as technicians and engineers.
Affiliations and expertise
Department of Electrical and Electronic Engineering, University of Leeds, UKRead Electric Motors and Drives on ScienceDirect