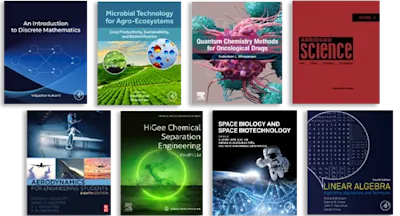
Directional Solidification of Steel Castings
- 1st Edition - December 28, 2013
- Imprint: Pergamon
- Author: R. Wlodawer
- Language: English
- Paperback ISBN:9 7 8 - 1 - 4 8 3 1 - 1 6 6 9 - 3
- eBook ISBN:9 7 8 - 1 - 4 8 3 1 - 4 9 1 1 - 0
Directional Solidification of Steel Castings summarizes the results of a large number of investigations, mostly scientific in character, on the directional solidification of steel… Read more
Purchase options
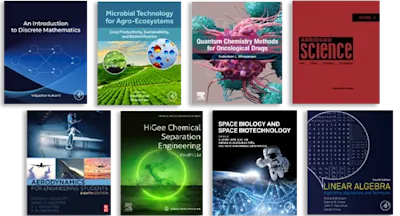
Directional Solidification of Steel Castings summarizes the results of a large number of investigations, mostly scientific in character, on the directional solidification of steel castings. The influence of design on the technical possibilities of producing casting in the foundry is examined. Diagrams, simple basic rules, and formulae are provided, along with many practical examples. This book is comprised of 16 chapters and begins with an introduction to the technical and psychological aspects of steel casting before turning to a discussion of the influence of shape and dimensions on the time it takes for castings to solidify. The thermal gradient, feeder heads, and cavities in steel castings are then considered. In particular, the effect of the thermal gradient on solidification and feeding range are examined. Methods for increasing the thermal gradient in the casting are described, including the use of mold heating pads, breaker cores or Washburn cores; external cooling (iron chills); cooling fins; internal chills; and exothermic pads. Cavities in steel castings which are commonly mistaken for true shrinkage cavities are also analyzed. This monograph is particularly suitable for foundry managers, foremen, technicians, casting designers, and students.
Foreword to the First Edition
Preface to the English Edition
From the Introduction to the First Edition
Chapter 1. Introduction to the English Edition
1.1. The Technical Side of This Book
1.2. The Psychological Side of This Book
Chapter 2. The Influence of Shape and Dimensions on the Time Taken for Castings to Solidify
2.1. Why Does a Casting Solidify? The Solidification Modulus
2.2. The Solidification Time and Modulus of Large Plates
2.3. The Influence of Mould Material and Casting Temperature
2.4. The Practical Significance of Simplified Modulus Calculations
2.5. Further Simplification of the Modulus Calculation by the Use of "Simulation" Bodies—Calculation of Junctions
2.6. Practical Examples of Modulus Calculations
Chapter 3. The Thermal Gradient in the Casting
3.1. What is a Thermal Gradient?
3.2. Thermal Gradient and Difference in Modulus
3.3. Effect of the Thermal Gradient on Solidification and Feeding Range
3.3.1. Solidification Characteristics of Rectangular Section Bars
3.4. Factors Influencing the Feeding Range
Chapter 4. Determination of the Connector between Feeder and Casting (Feeder Neck)
4.1. Calculation of Transition Cross-sections between Feeder and Casting (without Allowing for the Effects of the Flow of Metal)
4.2. Calculation of Ingates, Allowing for the Heating Effects of Metal Flow
Chapter 5. Feeder Heads
5.1. General
5.2. Action of Open Feeder Heads
5.3. Mode of Action of Blind Feeder Heads
5.4. Behavior of the Feeder Head during Solidification
5.5. Shrinkage
5.6. Calculations Giving the Shrinkage Cavity Characteristics of the Best Form of Feeder Head and the Compensating Factor
5.7. Influence of the Structure of the Shrinkage Cavity on the Maximum Yield
5.8. Feeder Head Calculations
5.9. Examples of Feeder Head Calculation
5.10. Other Methods of Calculating Feeder Heads
Chapter 6. Increasing the Thermal Gradient in the Casting by Padding and by the Utilization of Natural End Zones
6.1. Utilization of Natural End Zones and Shape of the Feeder. General
6.2. Use of the Heuvers(14) Circle Method for Castings
6.2.1. Use of the Circle Method for Extending Feeder Zones. Feeding of Bars and Bosses
6.2.2. Application of the Circle Method to Junctions in a Complex Casting
6.3. Calculation of the Modulus Curve
6.4. Further Development and Simplification in Practice of the Methods of Heuvers(14) and Stein(16)
6.5. Casting Sound Tubes
Chapter 7. Increasing the Thermal Gradient by Means of Mould Heating Pads. Breaker Cores or Washburn Cores
7.1. General Thermal Conditions Relating to Breaker Cores and Mould Heating Pads
7.2. Calculation of Washburn Cores and Mould Heating Pads on the Basis of the Thermal Conditions
7.2.1. Calculation of Internal Feeders
7.3. On the Practice of Washburn Cores, Heating Pads and Internal Feeders
7.4. The Heating of Thin Sections of Moulding Sand. Influence on the Size of the Feeder Head. The Minimum Lengths of Ingates Which Will Prevent Harmful Sand Fillet Effects
7.4.1. Harmful Effects of Hot Spots
7.4.2. The Heating of Plane Core Plates by the Superheat of the Liquid Steel
7.4.3. The Decrease in the Cooling Surface Areas of Core Plates as a Result of Heating
7.4.4. Calculation of the Cooling Action of Cores in Long Tubular Bodies
7.4.5. Calculation of the Cooling Action of Cores in Short Tubular Bodies (Discs and Rings)
7.4.6. Retardation of the Solidification Period by Heating
7.4.7. Checking the Calculations for Tubular Castings by Measuring the Solidification Time
7.4.8. Retention of Heat in Junctions
7.4.9. The Importance of the Heating Effect in Feeder Calculations
7.4.10. Approximate Hub Calculations
7.4.11. Special Features of the Heating Effect in the Placing of Blind Feeder Heads
Chapter 8. Increasing the Thermal Gradient by External Cooling (Iron Chills)
8.1. The Formation of Artificial End Zones by the Use of Chills
8.2. Measures Against Cracking Taken by the Use of Chills. Cooling of Junctions
8.3. Porosity at the Point of Attachment of Chills
8.3.1. Porosity Caused by Chills
8.3.2. Aids in Recognizing Porosity Arising from the Molten Steel
8.4. Tears at the Points of Attachment of Chills
8.4.1. Cracks Attributable to the Chills
8.4.2. Cracks at the Point of Attachment of the Chill, Attributable to the Steel. Advice on the Control of the Steelmaking Process to Prevent Such Cracks
8.5. Principles of Calculating External Chills
8.5.1. General
8.5.2. The Apparent Reduction in Volume
8.5.3. The Apparent Increase of Surface Area
8.5.4. The Transfer of Heat at the Point of Application of the Chill
8.5.5. Checking the Previous Chill Calculations by the Experiments Reported by Brandt, Bishop and Pellini(33)
8.5.6. Calculation the Necessary Chill Contact Surfaces
8.5.7. Maximum Cooling Action on Simple Basic Shapes
8.5.8. Chill Dimensions
8.5.9. Summary
8.6. Operating Practice in Cooling Heavy Cross-sections by Means of Chills
8.7. Shrinkage Cavity Due to the Incorrect Placing of Chills
8.8. Use of Contoured Chills
Chapter 9. Increasing the Thermal Gradient by Means of Cooling Fins
9.1. General Discussion of the Action of Cooling Fins
9.2. Effect on the Modulus of the Prior Solidification of Adjacent Cross-sections on Wedge Plates with Attached Fins. Determination of the Modulus on Wedge Plates
Chapter 10. Increasing the Thermal Gradient by Means of Moulding Materials with a Chilling Action
10.1. Different Heat Removal Rates of Various Moulding Materials. Defects Arising from Their Use
10.2. Calculation of Moulding Materials with a Chilling Action
10.3. Practical Application and Calculation of Moulding Materials Having a Chilling Action
10.4. Manufacture of Extended Artificial End Zones by Means of Chilling Materials
10.5. Displacement of the Segregated Zone by the Use of Moulding Materials with a Chilling Action
Chapter 11. Increasing the Thermal Gradient by the Use of Internal Chills
11.1. General
11.2. The Heat Balance of Welded-in Chills
11.3. The Transfer of Heat When Welding the Chill to the Casting
11.4. The Influence of Temperature on the Melt-down Time of Chill Sections
11.5. The Dimensions of Welded-in Chill Sections as a Function of Steel Temperature and the Desired Chilling Effect
11.6. The Use of Non-bonding Internal Chills
11.7. Checking the Methods of Calculating Internal Chills
11.8. The Chilling Characteristics of Chaplets
11.8.1. General
11.8.2. Chaplets Welding into Plates
11.8.3. Non-bonding, Crack-free Chaplets
11.8.4. Lugs and Bosses for Improving the Welding of Chaplets into Thin-walled Plates
11.8.5. Relationships of Chaplets. Welding-in Without Cracks in Reinforcing Bosses
11.9. Examples of the Use of Internal Chills
11.9.1. General Examples
11.9.2. Influence of Temperature Fluctuations
11.9.3. Further Examples of the Use of Internal Chills
Chapter 12. The Calculation of Exothermic Feeder Head Materials
12.1. General
12.2. Principles of Calculation of Exothermic Feeder Heads, with Reference to Exothermic Sleeves
12.2.1. What Do Exothermic Materials Accomplish, and How Do We Test Their Efficiency?
12.2.2. The Development of the Shrinkage Cavity in Unheated and Exothermic Feeder Heads. Influence of the Cavity on the Effectiveness of the Feeder Head
12.2.3. The Modulus Characteristics of Non-Exothermic and Exothermic Feeder Heads. Influence of the Shape of Shrinkage Cavity and Depth on the Time of Solidification of the Feeder Head
12.3. The Characteristic of Exothermic Feeder Heads
12.3.1. What Is a Feeder Head Characteristic, What Purpose Does It Serve, and How Is It Calculated?
12.3.2. Selection of the Most Suitable Diameter/Height Ratio. Further Computation of the Characteristics for Practical Requirements
12.4. On the Practice of Exothermic Feeder Head Manufacture
12.4.1. Chemical Requirements and Health Regulations for Exothermic Materials
12.4.2. Mechanical and Physical Requirements for Exothermic Materials (Omitting the Thermal Requirements Already Described). Order of Magnitude of the Amounts of Gas Evolved
12.4.3 The Design and Manufacture of Exothermic Sleeves. The Most Suitable Wall Thicknesses of the Sleeves
12.5. Practical Examples and Hints for the Use of Exothermic Feeder Heads
12.6. The Economics of Exothermic Feeder Heads
12.6.1. General
12.6.2. The Feeder Head Comparison; Making Use of the Characteristic
12.6.3. The Rapid Determination of the Most Economical Sleeve Wall Thickness
12.7. The Use of Exothermic Antipiping Powder
12.7.1. The Testing of Exothermic Antipiping Powders. The Structure of the Shrinkage Cavity in Covered Feeder Heads
12.7.2. On the Use of Antipiping Powders. Comparison with Exothermic Feeder Heads
12.7.3. Examples of the Use of Exothermic Powders
12.8. Heat Theory and the Calculation of Exothermic Materials
12.8.1. The Validity of Calculation Formulae Published up to the Present Time
12.8.2. True Physical Causes of the Extended Solidification Time
Chapter 13. The Use of Exothermic Pads to Increase the Thermal Gradient
13.1. Principles of the Calculation of Exothermic Pads
13.1.1. Heat Technology and General Principles
13.1.2. Principles of Feeding and Methods of Calculation for Exothermic Pads
13.2. Shape and Venting of Exothermic Pads. Heated Breaker Cores
13.3. Examples of the Use of Exothermic Pads
13.4. Frequently Occurring Defects with Exothermic Pads
13.4.1. Shrinkage Cavities Formed Because The Pads Have Been Made Too Thick
13.4.2. Blowholes Under Exothermic Pads
Chapter 14. Brief Note on the Use of Insulating Materials in Steel Castings
Chapter 15. Cavities in Steel Castings which are Frequently Confused with True Shrinkage Cavities
15.1. Blowholes Which Can Be Confused with Shrinkage Cavities
15.2. Slag Blowholes, Which Are Confused with Shrinkage Cavities
Chapter 16. Final Brief Word
Conversion Factors
Symbols Used in this Book
References
- Edition: 1
- Published: December 28, 2013
- Imprint: Pergamon
- Language: English
Read Directional Solidification of Steel Castings on ScienceDirect