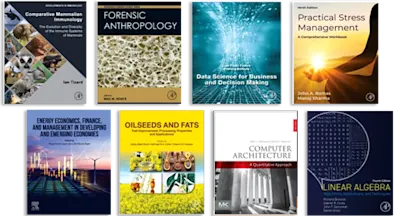
DC Motors, Speed Controls, Servo Systems
An Engineering Handbook
- 3rd Edition - October 22, 2013
- Imprint: Pergamon
- Author: Sam Stuart
- Language: English
- eBook ISBN:9 7 8 - 1 - 4 8 3 1 - 4 8 3 7 - 3
DC Motors - Speed Controls - Servo Systems: An Engineering Handbook is a seven-chapter text that covers the basic concept, principles, and applications of DC and speed motors and… Read more
Purchase options
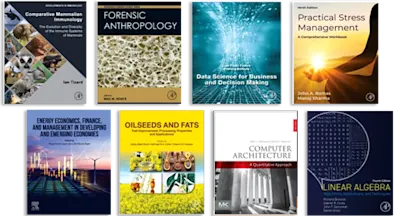
DC Motors - Speed Controls - Servo Systems: An Engineering Handbook is a seven-chapter text that covers the basic concept, principles, and applications of DC and speed motors and servo systems. After providing the terminology, symbols, and systems of units, this book goes on dealing with the basic theory, motor comparison, and basic speed control methods of motors. The subsequent chapters describe the phase-locked servo systems and their optimization and applications. These topics are followed by a discussion of the developments made by Electro-Craft in the field of DC Brushless Motors. The final chapter provides revised data sheets on Electro-Craft products and describes the models in the motomatic range of speed controls, servomotor controls, and digital positioning systems. This handbook is of great value to professional engineers and engineering students.
Foreword
Chapter 1. Terminology, Symbols, Systems of Units
1.1. Terminology
1.2. Symbols
1.3. Systems of Units
Chapter 2. DC Motors and Generators
2.1. Basic Theory
Historical Background
Concept of Torque and Power
Law of Electromagnetic Induction
Magnetic Circuit Principles
Magnetomotive Force
Magnetic Flux
Magnetic Flux Density
Permeability
Magnetic Field Intensity
Working Equations for Voltage and Torque
Voltage
Torque
Commutation
2.2. Motor Comparison
General Description
Wound-Field Motors
Permanent Magnet Motors
2.3. Motor Equations and Transfer Function
2.3.1. Electrical Equations
2.3.2. Dynamic Equations
2.3.3. Motor Transfer Function
2.3.4. Torsional Resonance
2.3.5. Speed-Torque Curve
2.4. Power Dissipation in DC Motors
2.4.1. Origins of Power Dissipation
2.4.2. Power Dissipation
2.4.3. Dissipation at Constant Velocity
2.4.4. Dissipation During Incremental Motion
2.5. Thermal Characterisitcs of DC Motors
2.5.1. Continuous Operation
2.5.2. Intermittent Operation
2.5.3. Thermal Model
2.5.4. Thermal Equations
2.5.5. Thermal Analysis
2.6. Motor Characteristics and Temperature
Armature Resistance
Torque Constant and Voltage Constant
Derating Motor Torque
2.7. Other Characteristics
Mounting
Noise
Noise and Dynamic Balancing
Noise Caused by Side Loading
Bearing Noise
Brush Noise
Environmental Considerations
Brush Wear
Motor Life
Demagnetization of PM Motors
2.8. Moving Coil Motors (MCM)
Moving Coil Motors
Moving Coil Motors and Motor Ratings
Thermal Properties
Resonant Phenomena in Moving Coil Motors
Demagnetizing Current
2.9. Specialty Motors - Permanent Magnet Motors with Variable KT
2.9.1. Introduction
2.9.2. The Wound-Field Motor
2.9.3. New Motor Types
2.10.Motor Testing
End Play
Radial Play
Shaft Runout
Moment of Inertia
Resistance
Inductance
Friction Torque and Starting Current
No-Load Current and Rotational Losses, No-Load Voltage, No-Load Speed
Demagnetization Current
Torque Constant
Voltage Constant
Electrical Time Constant
Mechanical Time Constant
Torque Ripple
Speed Regulation Constant
Efficiency
Frequency Response
Thermal Resistance
Thermal Time Constant
Air Flow Impedance
Incoming Inspection of Motors
Motor Troubleshooting Chart
2.11. DC Generators
Introduction
Theory
Types of DC Generators
Mounting Features
Temperature Effects
Ultrastable Generators
Stable Generators
Compensated Generators
Uncompensated Generators
Linearity and Load Effects
2.12. Generator Testing
Output Impedance
Voltage Gradient
Voltage Polarity
Generator Ripple
Iron-Core Generator Ripple
Moving Coil Tachometer Ripple
Temperature Coefficient
Dielectric Test
Linearity
Stability
Incoming Inspection
Generator Troubleshooting Chart
Chapter 3. Unidirectional Speed Controls
3.1. Basic Control Methods
Speed Controllers-An Introduction
Open Loop Controls-The Traditional Approach
Closed-Loop Controls
Speed Controls VS. Servo Systems
3.2. Velocity Control Single Quadrant Controller
Voltage and Current of A Single Quadrant Controller
System Operation
Dynamic Braking
3.3. Amplifiers
The Linear Amplifier
Torque Limiting
Dynamic Braking Devices
Reversible Speed Controls
Controlled Acceleration-Deceleration System
Switching Amplifiers
Pulse-Width Modulated Amplifiers
SCR Controls
Chapter 4. Speed Controls and Servo Systems
4.1. Servo Theory
Laplace Transformation
Inverse Laplace Transformation
Transfer Functions
Block Diagrams
Transfer Function of a DC Motor
Transfer Function of an Amplifier
Stability
Root Locus Method
4.2 Servo Components
4.2.1. DC Motor
4.2.2. Amplifier
4.2.3. Amplifier-Motor System
4.2.4. Tachometer
4.2.5. Potentiometer
4.2.6. Linear Variation Differential Transformer (LVDT)
4.2.7. Encoders
4.3. Servo Systems
4.3.1. Introduction
4.3.2. Velocity Control Systems
4.3.3. Position Control Systems
4.3.4. Torque Control Systems
4.3.5. Hybrid Control Systems
4.4. System Characteristics
4.4.1. Response of the System to a Step Command
4.4.2. System Bandwidth
4.4.3. Effect of Torsional Resonance
4.5. Servo Amplifiers
4.5.1. Linear Amplifiers
4.5.2. SCR Amplifiers
4.5.3. Switching Amplifiers
4.6. Phase-Locked Servo Systems
4.6.1. Introduction
4.6.2. System Components
4.6.3. System Design and Stability
4.6.4. Special Characteristics
4.7. How to Make Systems Work
4.8. Optimization
4.8.1. Introduction
4.8.2. Velocity Profile Optimization
4.8.3. Coupling Ratio Optimization
4.8.4. Capstan Optimization
4.8.5. Optimum Motor Selection for Incremental Application
4.9. Permanent Magnet Motors for Servo Applications
4.10. Systems and Controls Troubleshooting
Theoretical Failure-Symptom Chart
Chapter 5. Applications
5.1. Introduction
5.2. System Classification and Specification
5.2.1. Classification
5.2.2. Specification
5.3. Motor Selection Criteria
5.3.1. Introduction
5.3.2. When to Specify
5.3.3. What to Consider
5.3.4. Selection Analysis
5.4. Application of Motomatic Systems
5.4.1. Speed Range
5.4.2. Output Torque and Ambient Temperature
5.4.3. Speed Regulation and Stability
5.4.4. Motomatic Speed Control Features
5.4.5. Series E-550 Motomatic Controls
5.4.6. Series E-650 Motomatic Controls
5.5. Application Examples
Office Copying Machine
Hydraulic Motor Drives
Automatic Retrieval System
Speed-Torque Analyzer
Energy Chopper
Laboratory Stirrer
Filament Winding Machine
Rewinder Speed Control
Multi-Motor Control for Industrial Knitting Machines
Semiconductor Manufacturing Photoresist Spinner
Blood Oxygenator
Infusion Pump
Crystal Pulling Machine
Conveyor Feed Rate Control
Reflow Soldering
Drive for Disc Memory Testing
Variable Speed Tape Recorder
Motor Testing
Tachometer Ripple Voltage Testing
Torque Limiter
Paper Web Wind-Up Control
Welding Machines
Bidirectional Position Control
Muscle Exerciser - Medical Rehabilitation Device
Punch Press Feed Control
Connector Test Station
Blueprint Machine Drive
Film Scanning Device
Drive for Chart Recorder
Paper Cutting Control
Blood Cell Separator
Adjustable Lathe Feed Rate Control
Contour Lathe
Three-Axis Milling Machine Control
Linear Drive System
Phototypesetter Application
Diamond Sorting System
Printed Circuit Solder Fusing Machine
Component Marking System
5.6. Incremental Motion Applications
5.6.1. Introduction
5.6.2. Selecting the Proper Servomotor for an Incremental Motion System
5.6.3. Tag Printer Feed Drive
5.6.4. Conveyor Drive System
5.6.5. Computer Tape Transport Reel Motor
5.7. Application of P6000 Series Servo Motor Systems
5.7.1. General Description of the P6000 Range of Servo Motor Controls
5.7.2. Standard Options
5.7.3. Standard Drive Packages
5.7.4. Amplifier Installation
5.7.5. Control Adjustments
5.7.6. Customer Connections
5.7.7. Summing Amplifier Compensation
5.7.8. Ramp Generator Adjustment
5.7.9. In Case of Difficulty
5.7.10. Troubleshooting Guide
Chapter 6. Brushless DC Motors
6.1. Introduction
6.2. Definition of a Brushless DC Motor System
6.3. Practical Solutions to Brushless Commutation
6.4. Torque Generation by Various Controller Configurations
6.4.1. The Sinusoidal Control Scheme
6.4.2. Trapezoidal Torque Function
6.5. Commutation Sensor Systems
6.6. Power Control Methods
6.7. Motor Constants
6.8. Brushless DC Tachometers
6.9. Examples of Brushless Motors
6.10. Summary
6.11. Step Motors Versus Brushless DC Motors in Digital Position Systems
6.11.1. Introduction
6.11.2. Step Motor Performance Limitations
6.11.3. Brushless DC Motor Incremental Motion Control
6.11.4. Conclusion
Chapter 7. Electro-Craft Corporation Products
7.1. DC Servomotors
E-250
E-508/E-512
E-540/E-542
E-660/E-670
E-701/E-703
7.2. Servomotor Generators
E-576
E-586/E-587
S-586
S-670/596
S-703/596
E-530/E-532
ET-4000
7.3. Moving Coil Motors
M-1030
M-1040
M-1438
M-1450
M-1500
M-1600
M-1700
7.4. Tachometers-Generators
E-591/596
M-100/110
7.5. Special Hybrid Motors
H-5200 Series
7.6. Servomotor Controls and Systems
7.6.1. Motor Speed Controls
7.6.2. P6000 Pulse Width Modulated DC Servomotor Controllers
7.6.3. SD6 Series Servo System Packages
7.6.4. L5000 Linear Servomotor Controls
7.6.5. Options for Use With P6000 and L5000 Controls
7.7. Brushless DC Motors
BLM 340
BLM 341
BLM 342
7.8. Servo Systems for Engineering Education
Motomatic Control System Laboratory (MCSL)
Motomatic Experimenter
Appendix
A.1. SI System of Units Metric System
Definition of Basic SI Units
Length
Mass
Time
Electric Current
Temperature Difference
Review of Main SI Units and Secondary Units
Mechanical Units
Electrical and Magnetic Units
A.2. Units' Conversion Factors and Tables
Conversion Factors
Torque-Power-Speed Nomograph
Moment of Inertia Conversion Factors
Torque Conversion Factors
Explanation
Relationship of the Speed, Torque and Output Power of a Motor
Inches to Millimeters Conversion
Celsius to Fahrenheit Degrees
Conversion
Index
- Edition: 3
- Published: October 22, 2013
- Imprint: Pergamon
- Language: English
SS
Sam Stuart
Dr. Sam Stuart is a physiotherapist and a research Fellow within the Balance Disorders Laboratory, OHSU. His work focuses on vision, cognition and gait in neurological disorders, examining how technology-based interventions influence these factors. He has published extensively in world leading clinical and engineering journals focusing on a broad range of activities such as real-world data analytics, algorithm development for wearable technology and provided expert opinion on technology for concussion assessment for robust player management. He is currently a guest editor for special issues (sports medicine and transcranial direct current stimulation for motor rehabilitation) within Physiological Measurement and Journal of NeuroEngineering and Rehabilitation, respectively.
Affiliations and expertise
Senior Research Fellow, Department of Sport, Exercise and Rehabilitation, Northumbria University, UK
Honorary Physiotherapist, Northumbria Healthcare NHS Foundation Trust, North Shields, UKRead DC Motors, Speed Controls, Servo Systems on ScienceDirect