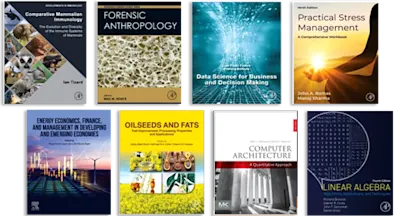
Cyclic Plasticity of Metals
Modeling Fundamentals and Applications
- 1st Edition - November 16, 2021
- Imprint: Elsevier
- Editors: Hamid Jahed, Ali A. A. Roostaei
- Language: English
- Paperback ISBN:9 7 8 - 0 - 1 2 - 8 1 9 2 9 3 - 1
- eBook ISBN:9 7 8 - 0 - 1 2 - 8 1 9 2 9 4 - 8
Cyclic Plasticity of Metals: Modeling Fundamentals and Applications provides an exhaustive overview of the fundamentals and applications of various cyclic plasticity models in… Read more
Purchase options
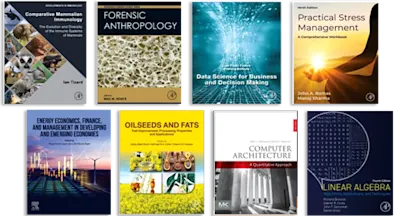
Cyclic Plasticity of Metals: Modeling Fundamentals and Applications provides an exhaustive overview of the fundamentals and applications of various cyclic plasticity models including forming and spring back, notch analysis, fatigue life prediction, and more. Covering metals with an array of different structures, such as hexagonal close packed (HCP), face centered cubic (FCC), and body centered cubic (BCC), the book starts with an introduction to experimental macroscopic and microscopic observations of cyclic plasticity and then segues into a discussion of the fundamentals of the different cyclic plasticity models, covering topics such as kinematics, stress and strain tensors, elasticity, plastic flow rule, and an array of other concepts. A review of the available models follows, and the book concludes with chapters covering finite element implementation and industrial applications of the various models.
- Reviews constitutive cyclic plasticity models for various metals and alloys with different cell structures (cubic, hexagonal, and more), allowing for more accurate evaluation of a component’s performance under loading
- Provides real-world industrial context by demonstrating applications of cyclic plasticity models in the analysis of engineering components
- Overview of latest models allows researchers to extend available models or develop new ones for analysis of an array of metals under more complex loading conditions
Academic researchers in plasticity modelling, mechanics of materials, and fatigue analysis; R&D researchers in automotive and aerospace industries; practicing design engineers, especially durability analysts; advanced engineering grad students
- Edition: 1
- Published: November 16, 2021
- Imprint: Elsevier
- Language: English
HJ
Hamid Jahed
AR