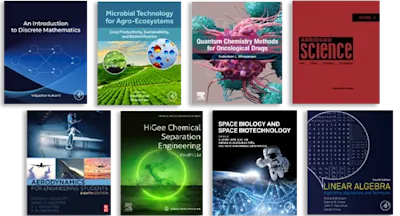
Corrosion Under Insulation (CUI) Guidelines
Revised
- 2nd Edition, Volume 55 - December 1, 2015
- Language: English
- Hardback ISBN:9 7 8 - 0 - 0 8 - 1 0 0 7 1 4 - 3
- eBook ISBN:9 7 8 - 0 - 0 8 - 1 0 0 7 3 9 - 6
Corrosion-under-insulation (CUI) refers to the external corrosion of piping and vessels that occurs underneath externally clad/jacketed insulation as a result of the penetration of… Read more
Purchase options
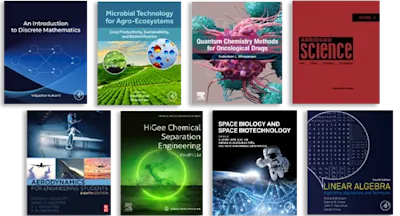
Corrosion-under-insulation (CUI) refers to the external corrosion of piping and vessels that occurs underneath externally clad/jacketed insulation as a result of the penetration of water. By its very nature CUI tends to remain undetected until the insulation and cladding/jacketing is removed to allow inspection or when leaks occur. CUI is a common problem shared by the refining, petrochemical, power, industrial, onshore and offshore industries.
In the first edition of this book published in 2008, the EFC Working Parties WP13 and WP15 engaged together to provide guidelines on managing CUI with contributions from a number of European refining, petrochemical and offshore companies. The guidelines are intended for use on all plants and installation that contain insulated vessels, piping and equipment. The guidelines cover a risk-based inspection methodology for CUI, inspection techniques and recommended best practice for mitigating CUI, including design of plant and equipment, coatings and the use of thermal spray techniques, types of insulation, cladding/jacketing materials and protection guards. The guidelines also include case studies.
The original document first published in 2008 was very successful and provided an important resource in the continuing battle to mitigate CUI. Many members of the EFC corrosion community requested an update and this has taken between 18-24 months to do so. Hopefully this revised document will continue to serve the community providing a practical source of information on how to monitor and manage insulated systems.
- Revised and fully updated technical guidance on managing CUI provided by EFC Working Parties WP13 and WP 15
- Contributions from a number of European refining, petrochemical and offshore companies
- Extensive appendices that provide additional practical guidance on the implementation of corrosion-under-insulation best practice, collected practical expertise and case studies
Engineers in the refining, petrochemical, power, industrial, onshore and offshore industries
- Abstract
- 1.1 Purpose of document
- Abstract
- 2.1 Statistical analysis
- 2.2 Size of the issue
- 2.3 Key performance indicators
- Abstract
- 3.1 Senior management
- 3.2 Engineering manager
- 3.3 Maintenance
- 3.4 Operations
- 3.5 Inspection
- 3.6 Members of a project team: CUI program
- Abstract
- 4.1 Introduction
- 4.2 High-level prioritization
- 4.3 Data validation
- 4.4 Challenging the need for insulation
- 4.5 Using RBI to design CUI inspection plans
- Abstract
- 5.1 General considerations
- 5.2 Typical locations on piping circuits susceptible to CUI
- 5.3 Typical locations on equipment susceptible to CUI
- 5.4 Examples of risk-based inspection plans
- Abstract
- 6.1 NDE/NDT techniques
- Abstract
- 7.1 Background
- 7.2 Current CUI prevention methods
- 7.3 How to achieve a life expectancy of over 25 years
- 7.4 Benefits of TSA
- 7.5 Use of personnel protective guards
- 7.6 Use of aluminum foil to mitigate Cl-ESCC of austenitic stainless steel
- Abstract
- 8.1 Introduction
- 8.2 Challenge the requirement for insulation
- 8.3 Plant layout
- 8.4 Mechanical considerations: Equipment and tanks
- 8.5 Mechanical considerations: Piping
- 8.6 Materials of construction
- 8.7 Coatings and wrappings
- 8.8 Insulation system
- 8.9 Weatherproofing
- 8.10 Implementation
- C.1 Maintenance and remediation issues
- C.2 Minimum standards
- C.3 Types of insulation service
- C.4 Surface preparation
- D.1 Introduction
- D.2 Protective coatings and protective coating selection
- D.3 Thermal spray aluminum
- D.4 Excerpt from NACE SP0198-2010 Section 4 protective coatings
- E.1 Thermal spray application
- E.2 Use of organic topcoats
- E.3 Application strategies
- E.4 TSA specification
- E.5 Definitions
- E.6 Referenced codes, standards, and specifications
- E.7 Coating philosophy
- E.8 Coating system
- E.9 TSA material
- E.10 Seal coat
- E.11 Design
- E.12 Surface preparation
- E.13 Weather and surface conditions
- E.14 Application process
- E.15 Specific requirements for on-site TSA application
- E.16 Piping field welds
- E.17 Inspection and acceptance
- E.18 Documentation
- F.1 Mineral fiber
- F.2 Low density glass fiber
- F.3 Calcium silicate
- F.4 Cellular glass
- F.5 Ceramic fiber paper
- F.6 Glass rope insulation
- F.7 Self-setting cement
- F.8 Flexible reusable insulation cover mattresses
- F.9 Preformed rigid polyurethane foam (polyurethane-polyisocynaurate)
- F.10 Flexible elastomeric foam
- F.11 Flexible elastomeric foam (EPDM)
- F.12 Polyethylene
- F.13 Perlite
- F.14 Vermiculite
- G.1 Metallic cladding materials
- G.2 Nonmetallic materials
- H.1 Design considerations
- H.2 Method guidance notes
- I.1 Visual inspection
- I.2 Manual ultrasonic thickness measurement through inspection openings
- I.3 Radiography
- I.4 Real-time radiography
- I.5 Guided wave ultrasonic measurements
- I.6 Pulsed eddy current
- I.7 Digital radiography
- I.8 Infrared thermography
- I.9 Neutron backscatter
- I.10 Dye penetrant testing
- Edition: 2
- Volume: 55
- Published: December 1, 2015
- Language: English