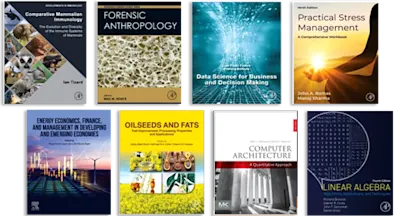
Cooling Towers and Chilled Water Systems
Design, Operation, and Economic Analysis
- 1st Edition - October 17, 2024
- Imprint: Academic Press
- Author: Ricardo de Freitas Fernandes Pontes
- Language: English
- Paperback ISBN:9 7 8 - 0 - 3 2 3 - 9 0 9 7 7 - 8
- eBook ISBN:9 7 8 - 0 - 3 2 3 - 9 0 9 7 8 - 5
Cooling Towers and Chilled Water Systems: Design, Operation, and Economic Analysis is a guide to the design and operation of cooling systems within high temperature settings.… Read more
Purchase options
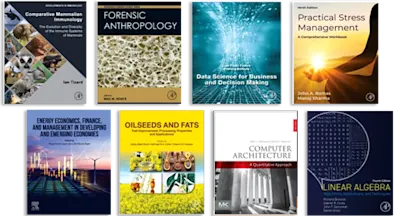
Cooling Towers and Chilled Water Systems: Design, Operation, and Economic Analysis is a guide to the design and operation of cooling systems within high temperature settings. The book presents various strategies to increase the turndown of cooling towers and chilled water systems and provides a toolkit for engineers to determine the use of variable frequency drivers. A guide to equipment selection for optimal design during the detailed engineering phase is provided, ensuring the reader is able to comply with the project specification within budget. Sections discuss various systems, circuits and processes for cooling tower and chiller systems before detailing design principles.
Operational and control strategies are then discussed before a thorough analysis of economic factors, making this book idea for professional engineers, graduate students and researchers working in high-temperature settings, such as power generation or chemical plants.
- Presents strategies and tools for engineers to develop and manage efficient cooling towers and chilled water systems
- Analyzes the economic benefits of cooled water system designs through the full lifecycle, instructing the reader on how to accurately estimate operating costs
- Guides the reader through appropriate equipment selection to comply with project needs
Power engineers in thermal plants, equipment design engineers of cooling towers and chiller designs, plant and operation engineers responsible for troubleshooting plant problems and retrofitting plants, graduate students in power engineering, thermal engineering, nuclear engineering, chemical engineering disciplines
1. Introduction
1.1. Cooling requirements in industrial processes
1.2. Cooling fluids
1.2.1. Water
1.2.1.1. Cooling water
1.2.1.2. Chilled water
1.2.2. Air
1.2.3. Other fluids
1.3. Cooling equipment
1.3.1. Cooling towers
1.3.2. Chillers
1.3.3. Other equipment
1.4. Project uncertainties and operating variations
1.5. Summary
2. Cooling water systems
2.1. Cooling water circuits
2.1.1. Open water circuits
2.1.2. Semi-closed water circuits
2.1.3. Closed water circuits
2.2. Estimative for cooling water consumption
2.2.1. Heat loads
2.2.2. Approach temperature
2.2.3. Temperature range
2.2.4. Thermal energy integration
2.3. Cooling towers
2.3.1. Types of cooling towers
2.3.1.1. Natural draft cooling towers
2.3.1.2. Mechanical (forced and induced) draft cooling towers
2.3.2. Fans
2.3.3. Fills
2.3.4. Cooling water basin
2.4. Multiple cooling water systems
2.6. Cooling water pumps
2.7. Motors
2.8. Cooling water treatment systems
2.9. Summary
3. Chilled water systems
3.1. Estimative for chilled water consumption
3.1.1. Heat loads
3.1.2. Temperature range
3.2. Chillers
3.2.1. Types of chillers
3.2.1.1. Water-cooled chillers
3.2.1.2. Air-cooled chillers
3.2.2. Refrigerant fluids
3.2.3. Evaporators
3.2.4. Condensers
3.2.5. Expansion devices
3.2.6. Chilled water tanks
4. Design of cooling and chilled water systems
4.1. Integration of cooling water and chiller systems
4.2. Water distribution system
4.2.1. Piping design criteria
4.2.2. Pumping systems
4.2.3. Supply and return headers
4.2.4. Critical consumers
4.2.4.1. Consumers with high flow rate demands
4.2.4.2. Consumers with high pressure drops
4.2.4.3. Consumers with low temperature differences
4.2.4.4. Consumers with high water quality demands
4.2.5. Minimization of pumping energy consumption
4.3. Varying conditions in chemical plants
4.3.1. Batch processes
4.3.2. Process fluctuations
4.3.3. Varying weather
4.4. Design turndown
4.4.1. Estimation of minimum, operating, maximum and design capacities
4.4.2. Equipment turndown
4.4.3. Design strategies for low demands
4.4.3.1. On/off equipment strategies
4.4.3.2. Variable frequency drivers (VFDs)
4.4.3.3. By-pass and recirculation lines
4.4.4. Design strategies for peak demands
4.4.4.1. Surge reservoirs
4.4.4.2. Effects of peak demands
4.5. Design considerations for equipment maintenance
4.6. Safety, health and environmental concerns
4.7. Summary
5. Operational and control strategies
5.1. Start-up procedures
5.2. Intermittent operations
5.2.1. System lag time
5.2.2. Alternating equipment use
5.3. Extreme weather conditions
5.3.1. Operating in high temperatures
5.3.2. Operating in below freezing temperatures
5.4. Instrumentation
5.4.1. Process monitoring instrumentation
5.4.2. Process control instrumentation
5.4.3. Safety instrumentation
5.4.5. Instrumentation turndown
5.5. Control valves
5.5.1. Valve types
5.5.2. Fail positions
5.5.3. Valve turndown
5.6. Real time performance assessment
5.6.1. Equipment efficiency
5.6.2. Slack
5.6.3. Process efficiency
5.6.4. System instability
5.7. Process control
5.7.1. Supply temperature control
5.7.1.1. Fan speed control
5.7.1.2. Compressor control
5.7.1.3. By-pass control
5.7.2. Return temperature control
5.7.3. Flow rate control
5.7.4. Differential pressure control
5.7.5. Equipment preservation control
5.7.6. Safety considerations for operation
5.8. Water quality control
5.8.1. Water quality parameters
5.8.2. Air pollution concerns
5.8.3. Blowdown
5.9. Equipment maintenance
5.10. Summary
6. Economic analysis
6.1. Capital costs estimation
6.1.1. Equipment purchase costs
65.1.2. Installation costs
6.2. Operating costs
6.2.1. Energy consumption costs
6.2.2. Water treatment costs
6.2.3. Maintenance costs
6.2.4. Other operating costs
6.3. Minimization of overall costs
6.3.1. Degrees of freedom
6.3.2. Algorithms for cost minimization
6.3.3. Effect of overdesign on costs
6.4. Summary
- Edition: 1
- Published: October 17, 2024
- Imprint: Academic Press
- Language: English
RP
Ricardo de Freitas Fernandes Pontes
Dr. Pontes’ career started as a chemical engineer at the Universidade de São Paulo (USP), when he started working for the research and development department of Ultragaz. In 2000, he returned to USP to start his Master’s degree in chemical engineering, which he concluded in 2002. He then went to work as a project engineer working for Exen while simultaneously started his Doctor’s degree. From 2010 to 2014, Dr. Pontes went to work for Pöyry also as a project engineer. In 2014, Dr. Pontes worked for American Process, where he left in 2016 to return to his academic career at Universidade Mackenzie. Later in that same year, Dr. Pontes moved to Universidade Federal de São Paulo (UNIFESP), lecturing courses on Process Simulation and Chemical Industry Projects. In 2018, he received a grant from FAPESP for his research project on the Optimal Synthesis of Cooling Water Systems.