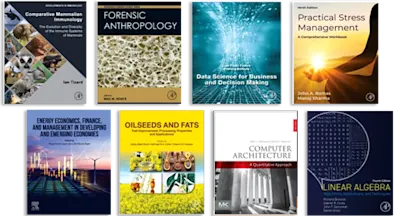
Controller Design for Industrial Robots and Machine Tools
Applications to Manufacturing Processes
- 1st Edition - September 30, 2013
- Imprint: Woodhead Publishing
- Authors: F Nagata, K Watanabe
- Language: English
- Paperback ISBN:9 7 8 - 0 - 0 8 - 1 0 1 5 4 2 - 1
- Hardback ISBN:9 7 8 - 0 - 8 5 7 0 9 - 4 6 2 - 9
- eBook ISBN:9 7 8 - 0 - 8 5 7 0 9 - 4 6 3 - 6
Advanced manufacturing systems are vital to the manufacturing industry. It is well known that if a target work piece has a curved surface, then automation of the polishing process… Read more
Purchase options
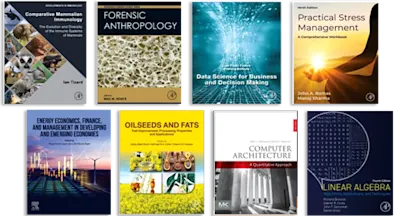
- Presents results where industrial robots have been used successfully to polish difficult surfaces
- Presents the latest technology in the field
- Includes key technology such as customized several position and force controllers
List of figures
List of tables
Preface
About the authors
Introduction
Chapter 1: Velocity-based discrete-time control system with intelligent control concepts for openarchitecture industrial robots
Abstract:
1.1 Background
1.2 Basic Servo System
1.3 Dynamic simulation
1.4 In case of fuzzy control
1.5 In case of neural network
1.6 Conclusion
Chapter 2: Preliminary simulation of intelligent force control
Abstract:
2.1 Introduction
2.2 Impedance model following force control
2.3 Influence of environmental viscosity
2.4 Fuzzy environment model
2.5 Conclusion
Chapter 3: CAM system for articulated-type industrial robot
Abstract:
3.1 Background
3.1 Desired trajectory
3.3 Implementation to industrial robot RV1A
3.4 Experiment
3.5 Passive force control of industrial robot RV1A
3.6 Conclusion
Chapter 4: 3D robot sander for artistically designed furniture
Abstract:
4.1 Background
4.2 Feedfoward position/orientation control based on post-process of CAM
4.3 Hybrid position/force control with weak coupling
4.4 Robotic sanding system for wooden parts with curved surfaces
4.5 Surface-following control for robotic sanding system
4.6 Feedback control of polishing force
4.7 Feedforward and feedback control of position
4.8 Hyper CL data
4.9 Experimental result
4.10 Conclusion
Chapter 5: 3D machining system for artistic wooden paint rollers
Abstract:
5.1 Background
5.2 Conventional five-axis nc machine tool with a tilting head
5.3 Intelligent machining system for artistic design of wooden paint rollers
5.4 Experiments
5.5 Conclusion
Chapter 6: Polishing robot for pet bottle blow molds
Abstract:
6.1 Background
6.2 Generation of multi-axis cutter location data
6.3 Basic Polishing Scheme for a Ball End Abrasive Tool
6.4 Feedback Control of Polishing Force
6.5 Feedforward and Feedback Control of Tool Position
6.6 Update timing of CL data
6.7 Experiment
6.8 Conclusion
Chapter 7: Desktop orthogonal-type robot for LED lens cavities
Abstract:
7.1 Background
7.2 Limitation of a polishing system based on an articulated-type industrial robot
7.3 Desktop orthogonal-type robot with compliance controllability
7.4 Transformation technique of manipulated values from velocity to pulse
7.5 Desired damping considering the critically damped condition
7.6 Design of weak coupling control between force feedback loop and position feedback loop
7.7 Basic experiment
7.8 Frequency characteristics
7.9 Application to finishing an LED lens mold
7.10 Stickslip motion of tool
7.11 Neural Network-Based Stiffness Estimator
7.12 Automatic Tool Truing for Long-Time Lapping Process
7.13 Force Input Device
7.14 Conclusion
Chapter 8: Conclusion
Abstract:
References
Index
- Edition: 1
- Published: September 30, 2013
- Imprint: Woodhead Publishing
- Language: English
FN
F Nagata
KW