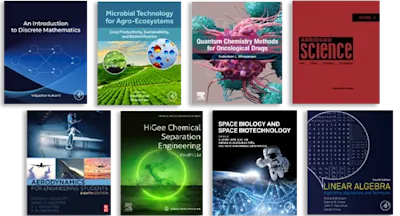
Comprehensive Materials Processing
- 1st Edition - September 12, 2014
- Editor: M.S.J. Hashmi
- Language: English
- Hardback ISBN:9 7 8 - 0 - 0 8 - 0 9 6 5 3 2 - 1
- eBook ISBN:9 7 8 - 0 - 0 8 - 0 9 6 5 3 3 - 8
Comprehensive Materials Processing, Thirteen Volume Set provides students and professionals with a one-stop resource consolidating and enhancing the literature of the materi… Read more
Purchase options
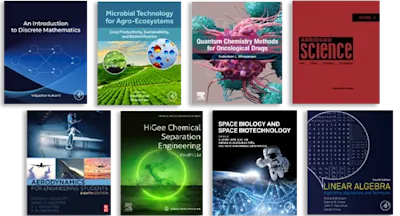
Comprehensive Materials Processing, Thirteen Volume Set provides students and professionals with a one-stop resource consolidating and enhancing the literature of the materials processing and manufacturing universe. It provides authoritative analysis of all processes, technologies, and techniques for converting industrial materials from a raw state into finished parts or products. Assisting scientists and engineers in the selection, design, and use of materials, whether in the lab or in industry, it matches the adaptive complexity of emergent materials and processing technologies. Extensive traditional article-level academic discussion of core theories and applications is supplemented by applied case studies and advanced multimedia features. Coverage encompasses the general categories of solidification, powder, deposition, and deformation processing, and includes discussion on plant and tool design, analysis and characterization of processing techniques, high-temperatures studies, and the influence of process scale on component characteristics and behavior.
- Authored and reviewed by world-class academic and industrial specialists in each subject field
- Practical tools such as integrated case studies, user-defined process schemata, and multimedia modeling and functionality
- Maximizes research efficiency by collating the most important and established information in one place with integrated applets linking to relevant outside sources
Undergraduate (BEng / BSci), Masters (MEng / MSci), Doctoral (PhD) students within, or faculty leading, research in Industrial engineering, materials science, interdisciplinary research, engineering technology, manufacturing and processing and design-related mechanical engineering, including aeronautical and automotive engineering; process, product and industrial design
- Editor-In-Chief
- Editorial Board
- Preface
- Notes on the Subject Index
- Volume 1: Assessing Properties of Conventional and Specialized Materials
- 1.01. Introduction to Assessing Properties of Conventional and Specialized Materials
- Abstract
- 1.02. Techniques for Assessing the Properties of Advanced Ceramic Materials
- Abstract
- 1.02.1 Introduction
- 1.02.2 Evaluation of Microstructural, Chemical, and Physical Properties
- 1.02.3 Evaluation of Mechanical Properties
- 1.02.4 Evaluation of Tribological Properties
- 1.02.5 Evaluation of Thermal Properties
- 1.02.6 Evaluation of Electrical and Magnetic Properties
- 1.02.7 Evaluation of Optical Properties
- 1.02.8 Evaluation of Nuclear Properties
- 1.02.9 Evaluation of Biomedical Properties
- 1.02.10 Conclusions and Future Outlook
- References
- 1.03. Testing of Polymeric Materials
- Abstract
- 1.03.1 Introduction
- 1.03.2 Polymeric Materials
- 1.03.3 Characterization of Basic Physical Properties
- 1.03.4 Polymer Rheology
- 1.03.5 Solid-State Mechanical Properties
- 1.03.6 Fracture and Impact Testing
- 1.03.7 Fiber-Reinforced Polymer Composites (FRPs)
- 1.03.8 Environmental Testing
- 1.03.9 Conclusions
- References
- 1.04. Stress-Based Forming Limit Curves
- Abstract
- 1.04.1 Introduction
- 1.04.2 Strain-Based Forming Limit Criteria
- 1.04.3 Stress-Based Forming Limit Criteria
- 1.04.4 Summary and Conclusions
- References
- 1.05. Sheet Bulge Testing
- Abstract
- 1.05.1 Introduction
- 1.05.2 Bulge Test Equipment and Specimens
- 1.05.3 Measurement Equipment
- 1.05.4 Stress–Strain Curve Calculation
- 1.05.5 Summary
- 1.05.6 Acknowledgments
- References
- 1.06. Biaxial Stress Testing Methods for Sheet Metals
- Abstract
- 1.06.1 Introduction
- 1.06.2 Biaxial Compression Test
- 1.06.3 Biaxial Tensile Testing Method Using a Cruciform Specimen
- 1.06.4 Combined Tension–Compression Testing Method
- 1.06.5 In-plane Stress Reversal Testing Method
- 1.06.6 Multiaxial Tube Expansion Testing Method
- 1.06.7 Combined Tension-Shear Testing Method
- References
- 1.07. Residual Stress Measurements
- Abstract
- 1.07.1 Introduction
- 1.07.2 Powder Diffraction
- 1.07.3 Introduction to Hole-Drilling
- 1.07.4 Introduction to Piezospectroscopy
- References
- 1.08. Testing of Small-Sized Specimens
- Abstract
- Acknowledgments
- 1.08.1 Introduction
- 1.08.2 Tensile Testing
- 1.08.3 Impact (Charpy) Testing
- 1.08.4 Fracture Toughness Testing
- 1.08.5 Fatigue Testing
- 1.08.6 Creep Testing
- 1.08.7 Creep Crack Growth Testing
- 1.08.8 Extreme Miniaturization (Part 1): Small Disk Testing
- 1.08.9 Extreme Miniaturization (Part 2): Use of Microfabrication Technology
- 1.08.10 Concluding Remarks and Future Trends
- References
- 1.09. Advanced High Strength Bainitic Steels
- Abstract
- Acknowledgments
- 1.09.1 Introduction
- 1.09.2 Theory for Bainite Phase Transformation
- 1.09.3 First Approaches to the Design of Carbide-Free Bainitic Steels, AHSS-GEN3 for Automotive Applications
- 1.09.4 A New Steel Concept for the Twenty-First Century: Nanostructured Bainitic Steels (NANOBAIN)
- 1.09.5 Accelerating Low-Temperature Bainite Transformation
- 1.09.6 Advanced Characterization of Nanostructured Steels
- 1.09.7 Understanding the Mechanical Properties of Advanced Bainitic Steels
- References
- 1.10. Thermomechanical Processed Steels
- Abstract
- 1.10.1 Overview of Thermomechanical Processing
- 1.10.2 Properties and Composition of TMCP Steels
- 1.10.3 Austenite Conditioning during Thermomechanical Treatment
- 1.10.4 Phase Transformations during Accelerated Cooling
- 1.10.5 Summary and Outlook
- See also
- References
- 1.11. Quenched and Partitioned Steels
- Abstract
- Acknowledgements
- 1.11.1 The Quenching and Partitioning Process Concept
- 1.11.2 Microstructure Development Fundamentals and Alloy Designs
- 1.11.3 Mechanical Behavior, Potential Applications, and Implementation Status
- References
- 1.12. Material Properties for Numerical Calculations
- Abstract
- Acknowledgments
- 1.12.1 Introduction
- 1.12.2 Material Characterization
- 1.12.3 Material Modeling for Warm Forming
- 1.12.4 Numerical Modeling
- 1.12.5 Summary
- References
- 1.01. Introduction to Assessing Properties of Conventional and Specialized Materials
- Volume 2: Materials Modeling and Characterization
- 2.01. Introduction to Materials Modeling and Characterization
- Abstract
- 2.01.1 Introduction
- 2.01.2 Volume Scope and Objective
- References
- 2.02. Phase Transformations and Characterization of α + β Titanium Alloys
- Abstract
- 2.02.1 Introduction
- 2.02.2 Phase Transformations
- 2.02.3 Characterization of Phases
- 2.02.4 The Effect of Microstructure on Mechanical Properties of Two-Phase Titanium Alloys
- 2.02.5 Development of Microstructure and Plasticity of α + β Titanium Alloys in Plastic Working and Heat Treatment Processes
- 2.02.6 The Influence of Deformation Conditions and Morphology of Phases on the Plasticity of α + β Titanium Alloys
- 2.02.7 Superplasticity of Titanium Alloys
- 2.02.8 Summary
- References
- 2.03. Polymeric Materials Characterization and Modeling
- Abstract
- 2.03.1 Introduction
- 2.03.2 Rubberlike Material Characterization and Modeling
- 2.03.3 Adhesively Bonded Joints Characterization and Modeling
- 2.03.4 Melt Rheology of Multiphase Polymeric Systems
- References
- 2.04. Ultrasonic Characterization of Anisotropic Materials
- Abstract
- 2.04.1 Introduction
- 2.04.2 Acoustic Waves in Elastic and Piezoelectric Media
- 2.04.3 Elastic Constants Determination Using Large-Aperture PVDF Receivers
- 2.04.4 Piezoceramic Characterization Using an Iterative Numerical Simulation
- References
- 2.05. Application of Optical Techniques to Materials Characterization and Modeling
- Abstract
- 2.05.1 Introduction
- 2.05.2 Measurement of Color
- 2.05.3 Materials and Methods
- 2.05.4 Results and Discussion
- 2.05.5 Conclusions and Further Research
- References
- 2.06. Material Behavior at a Wide Range of Strain Rates
- Abstract
- 2.06.1 Introduction
- 2.06.2 Stress–Strain Definitions
- 2.06.3 Quasistatic Tensile Tests
- 2.06.4 Quasistatic Compressive Tests
- 2.06.5 Midrange Strain Rate Tests
- 2.06.6 High-Strain-Rate Tests
- 2.06.7 Discussion
- References
- 2.07. Damage Modeling in Composite Structures
- Abstract
- Acknowledgments
- 2.07.1 Introduction
- 2.07.2 Intralaminar Damage Modeling
- 2.07.3 Interlaminar Damage Modeling
- 2.07.4 Formulation
- 2.07.5 Applications
- 2.07.6 Summary and Conclusions
- References
- 2.08. Creep Age Forming Modeling and Characterization
- Abstract
- 2.08.1 Introduction
- 2.08.2 CAF Process
- 2.08.3 Aluminum Alloy for CAF
- 2.08.4 Phenomenological Approach
- 2.08.5 Microstructural Characterization Techniques
- 2.08.6 Concluding Remarks on CAF Process Modeling
- References
- 2.09. Use of Neural Networks and Artificial Intelligence Tools for Modeling, Characterization, and Forecasting in Material Engineering
- Abstract
- 2.09.1 Introduction
- 2.09.2 Artificial Intelligence Tools Used in Material Engineering
- 2.09.3 The Scope of Applications of Neural Networks in Material Engineering
- 2.09.4 Artificial Neural Network Design Methodology
- 2.09.5 Engineering Materials Properties Modeling and Simulation
- 2.09.6 Neural Networks Aided Prediction of Development Trends in Materials Surface Engineering
- 2.09.7 Summary
- References
- 2.10. Structure and Mechanical Properties of High-Manganese Steels
- Abstract
- 2.10.1 Introduction
- 2.10.2 Thermo-Mechanical Treatment of High-Manganese Austenitic Steels
- 2.10.3 Mechanical Properties of High-Manganese Austenitic Steels
- 2.10.4 Summary
- References
- 2.11. Modeling and Characterization of Residual Stresses in Material Processing
- Abstract
- Acknowledgments
- 2.11.1 Introduction and Definitions
- 2.11.2 Physical Basis for Residual Stresses and Its Sources
- 2.11.3 Modeling Techniques and Challenges for Residual Stress Prediction
- 2.11.4 A Brief Overview of Experimental Methods for Characterizing Residual Stresses and Their Limitations
- 2.11.5 Exploratory Comparison between X-Ray and Hole-Drilling Methods
- 2.11.6 Concluding Remarks
- References
- 2.12. Modeling of Plastic Yielding, Anisotropic Flow, and the Bauschinger Effect
- Abstract
- Acknowledgments
- 2.12.1 Motivation
- 2.12.2 Plasticity at Different Scales
- 2.12.3 Yielding and Flow Potentials for Isotropic Metals
- 2.12.4 Anisotropic Yield Functions
- 2.12.5 Kinematic Hardening and Bauschinger Effect
- 2.12.6 Homogeneous Potential and the Bauschinger Effect
- 2.12.7 Application to Springback Simulations
- Conclusions
- Appendix
- References
- 2.13. Modeling of Functionally Graded Materials
- Abstract
- Acknowledgments
- 2.13.1 Introduction
- 2.13.2 Functionally Graded Materials
- 2.13.3 Modeling of Graded Structures by Using FEM
- 2.13.4 Examples
- 2.13.5 Conclusions
- References
- 2.01. Introduction to Materials Modeling and Characterization
- Volume 3: Advanced Forming Technologies
- 3.01. Introduction to Advanced Forming Technologies
- Abstract
- 3.01.1 Historical Developments
- 3.01.2 Metalworking: Basic Concepts
- 3.01.3 Classification of Metalworking Processes
- 3.01.4 Preview of the Contents of Volume 3
- 3.01.5 Conclusion
- Further Reading
- 3.02. Incremental Sheet Forming
- Abstract
- 3.02.1 Introduction
- 3.02.2 Incremental Sheet-Forming Processes
- 3.02.3 Materials for Incremental Sheet-Forming Processes
- 3.02.4 Modeling
- 3.02.5 Experimental Assessment of Analytical and FE Models
- 3.02.6 Examples of Applications
- 3.02.7 Conclusions and Future Trends
- References
- 3.03. Hot Stamping
- Abstract
- 3.03.1 Introduction
- 3.03.2 Process
- 3.03.3 Material and Microstructural Properties
- 3.03.4 Material Formability
- 3.03.5 Boundary Conditions
- 3.03.6 FE Modeling
- 3.03.7 Product Characteristics
- 3.03.8 New Developments
- 3.03.9 Conclusions
- References
- 3.04. Tube Hydroforming (Internal High-Pressure Forming)
- Abstract
- 3.04.1 Types and Characteristics of IHPF
- 3.04.2 Main Process Parameters for IHPF
- 3.04.3 Defects in IHPF
- 3.04.4 Forming Limits for IHPF
- 3.04.5 Thickness Distribution Law in IHPF
- 3.04.6 Tubes for IHPF and Lubrication
- 3.04.7 Equipment and Dies for IHPF
- 3.04.8 IHPF Processes for Typical Components
- References
- 3.05. Development of Microstructures and Textures by Cross Rolling
- Abstract
- 3.05.1 Introduction
- 3.05.2 Scope
- 3.05.3 Process Details
- 3.05.4 Science of Microstructure Formation
- 3.05.5 Texture Formation
- 3.05.6 Mechanics of the Processes
- 3.05.7 Technological Importance
- 3.05.8 Concluding Remarks
- Bibliography
- 3.06. Multipoint Forming
- Abstract
- Acknowledgments
- 3.06.1 Introduction
- 3.06.2 Basic Principles
- 3.06.3 Types of Punch Adjustment
- 3.06.4 Deformation Characteristics and Forming Technology
- 3.06.5 Application Examples
- 3.06.6 New Developments
- 3.06.7 Conclusions and Prospects
- References
- 3.07. Dieless Drawing of Bars, Rods, Tubes, and Wires
- Abstract
- 3.07.1 Introduction
- 3.07.2 Overview of Conventional Wire and Rod Manufacturing
- 3.07.3 Dieless Drawing
- 3.07.4 Concluding Remarks
- References
- 3.08. Forming of Metal Matrix Composites
- Abstract
- 3.08.1 Introduction
- 3.08.2 Extrusion
- 3.08.3 Forging
- 3.08.4 Rolling
- 3.08.5 Superplasticity
- 3.08.6 Friction Stir Processing
- 3.08.7 Conclusions
- References
- 3.09. Development of Ultrafine-Grained Metals by Equal-Channel Angular Pressing
- Abstract
- Acknowledgments
- 3.09.1 Introduction
- 3.09.2 Basic Principles of ECAP Processing
- 3.09.3 Application of ECAP for Processing of Low-Ductile and Hard-to-Deform Materials
- 3.09.4 Recent Developments of ECAP Techniques for Processing UFG Materials
- 3.09.5 Summary
- References
- 3.10. Cross-Wedge Rolling
- Abstract
- 3.10.1 Introduction
- 3.10.2 Basic Information
- 3.10.3 States of Stress and Strain
- 3.10.4 Forces in the CWR Process
- 3.10.5 CWR Process Limitations
- 3.10.6 CWR Tools
- 3.10.7 Outline of the CWR Technology
- 3.10.8 Conclusion
- References
- 3.11. Improvement of Mechanical and Physical Properties in Powder Metallurgy
- Abstract
- 3.11.1 Brief Introduction to Powder Metallurgy
- 3.11.2 How to Improve the Properties without Increasing the Density Level
- 3.11.3 Improving Properties by Increasing the Density from High Green Density Levels
- 3.11.4 Improving Properties by Sintering Activation
- 3.11.5 Inhibiting the Grain Growth during Sintering
- 3.11.6 Additive Technologies
- 3.11.7 Summary
- References
- 3.12. Peen Forming
- Abstract
- 3.12.1 Introduction
- 3.12.2 Shot Peening and Peen Forming Principles
- 3.12.3 Historical Account
- 3.12.4 Peen Forming Equipment
- 3.12.5 Peen Forming Procedures
- 3.12.6 Advantages and Limitations
- 3.12.7 Typical Uses of Peen Forming
- 3.12.8 Research on Peen Forming
- 3.12.9 Analytical Explanation of Conventional and Stress Peen Forming Processes
- 3.12.10 Conclusion
- See also
- References
- Further Reading
- 3.13. High-Speed Forming of Magnesium Alloy Sheets
- Abstract
- Acknowledgments
- 3.13.1 Introduction
- 3.13.2 Material Characterization at High Strain Rates
- 3.13.3 Numerical Modeling of EM Forming
- 3.13.4 Experimental Results of EM Forming of AZ31 Sheets
- 3.13.5 Conclusions
- References
- 3.14. Hot Rolling and Direct Cooling
- Abstract
- 3.14.1 Introduction
- 3.14.2 Thermo-Mechanical-Metallurgical Modeling during Hot Rolling
- 3.14.3 Materials Response during Hot Slab Rolling of Mild Steel
- 3.14.4 Outlook
- References
- 3.15. Advanced Techniques to Evaluate Hot Workability of Materials
- Abstract
- 3.15.1 Introduction
- 3.15.2 Stress–Strain Behavior in Hot Deformation
- 3.15.3 Materials Modeling in Hot Deformation
- 3.15.4 Hot Deformation Mechanisms
- 3.15.5 Processing Maps – How to Develop and Interpret
- 3.15.6 Applications of Processing Maps
- 3.15.7 Validation of Processing Maps
- 3.15.8 Design of Bulk Metal Working Processes
- 3.15.9 Summary
- References
- 3.16. Near-Net and Net Shape Forging
- Abstract
- 3.16.1 Introduction into Forming Technology
- 3.16.2 Process Design
- 3.16.3 Tool Design
- 3.16.4 Summary
- References
- 3.17. Texture Control in Aluminum Sheets by Conventional and Asymmetric Rolling
- Abstract
- Acknowledgments
- 3.17.1 Introduction
- 3.17.2 TMP of Al Alloys: Hot Rolling
- 3.17.3 Cold Rolling
- 3.17.4 Annealing
- 3.17.5 Texture-Dependent Properties of Rolled Al Alloys
- References
- 3.01. Introduction to Advanced Forming Technologies
- Volume 4: Films and Coatings: Technology and Recent Development
- 4.01. Introduction to Films and Coatings: Technology and Recent Development
- Abstract
- 4.02. Cathodic-Arc and Thermal-Evaporation Deposition
- Abstract
- 4.02.1 Introduction
- 4.02.2 Thermal Evaporation
- 4.02.3 Cathodic-Arc Deposition Process
- References
- 4.03. Magnetron Sputtering
- Abstract
- 4.03.1 The Basics of Sputtering
- 4.03.2 Sputtering from Planar Diodes
- 4.03.3 Radio-Frequency Sputtering
- 4.03.4 The Magnetron Cathode
- 4.03.5 High Target Utilization
- 4.03.6 Reactive Sputtering
- 4.03.7 Pulse Magnetron Sputtering
- 4.03.8 Special Developments
- 4.03.9 Concluding Remarks and Outlook
- References
- 4.04. High Power Impulse Magnetron Sputtering – HIPIMS
- Abstract
- 4.04.1 Introduction to High Power Impulse Magnetron Sputtering
- 4.04.2 HIPIMS Generation
- 4.04.3 HIPIMS Process Technology
- 4.04.4 HIPIMS Applications
- 4.04.5 Patent Situation
- 4.04.6 Outlook
- References
- 4.05. Atomic Layer Deposition
- Abstract
- 4.05.1 Introduction
- 4.05.2 Characteristic Features of ALD
- 4.05.3 ALD Chemistry
- 4.05.4 ALD Reactors
- 4.05.5 ALD Applications
- References
- 4.06. Laser Ablation
- Abstract
- 4.06.1 Laser Ablation Technology: Introduction and Physical Fundamentals
- 4.06.2 Applications of Laser Ablation in Material Processing I
- 4.06.3 Applications of Laser Ablation in Material Processing II
- 4.06.4 Pulsed Laser Ablation and Pulsed Laser Deposition Technology
- 4.06.5 Thermodynamics of Laser Ablation
- References
- 4.07. Surface Processing Using Cold Atmospheric Pressure Plasmas
- Abstract
- Acknowledgments
- 4.07.1 Classification of Atmospheric Plasmas by Electron Temperature
- 4.07.2 Classification of Atmospheric Plasmas Based on Discharge Type
- 4.07.3 Surface Activation and Coating Deposition Using Cold Atmospheric Plasmas
- 4.07.4 Surface Treatments
- 4.07.5 Coating Deposition
- 4.07.6 Organosilicon Precursors
- 4.07.7 Plasma Medicine
- 4.07.8 Summary
- References
- 4.08. Ion Beam Deposition: Recent Developments
- Abstract
- 4.08.1 Introduction
- 4.08.2 Irradiation Effects of Ion Beam during Thin Film Depositions
- 4.08.3 Ion Beam Assisted Deposition Systems
- 4.08.4 Gas Cluster IBAD
- 4.08.5 Focused Ion Beam Assisted Nanostructure Formation
- 4.08.6 Conclusion
- References
- 4.09. Plasma Polymer Deposition and Coatings on Polymers
- Abstract
- 4.09.1 Plasma Polymer Deposition
- 4.09.2 Coatings on Polymers
- References
- 4.10. Thermal Spray Coating Processes
- Abstract
- 4.10.1 Introduction
- 4.10.2 Spray Materials
- 4.10.3 Thermal Spray Processes
- 4.10.4 Formation of Sprayed Coatings
- 4.10.5 Coating Materials and Properties
- 4.10.6 Industrial Applications
- 4.10.7 Development Trends
- 4.10.8 Concluding Remarks
- References
- 4.11. Electroplating and Electroless Plating
- Abstract
- 4.11.1 Introduction
- 4.11.2 Principal Elements of Plating
- 4.11.3 Electrolytic Plating
- 4.11.4 Alloy Plating
- 4.11.5 Aluminum Finishing
- 4.11.6 Electroless Plating Solutions
- See also
- References
- 4.12. Plasma Sources in Thin Film Deposition
- Abstract
- 4.12.1 Introduction
- 4.12.2 Pressure and Power Source Frequency of Plasma Sources
- 4.12.3 Plasma Sources for CVD Processes
- 4.12.4 Plasma Sources for PVD Processes
- 4.12.5 Plasma Source for Large-Area Process
- 4.12.6 Summary
- References
- 4.13. Hard Nanocomposite Coatings
- Abstract
- Acknowledgments
- 4.13.1 Present State of the Knowledge in the Field of Nanocomposite Coatings
- 4.13.2 Advanced Hard Nanocomposite Coatings
- 4.13.3 Trends of the Present and the Next Development of Hard Nanocomposite Coatings
- References
- 4.14. Protective Transition Metal Nitride Coatings
- Abstract
- Acknowledgments
- 4.14.1 Introduction
- 4.14.2 Transition Metal Nitride Coatings
- 4.14.3 Thermal and Chemical Stability of Nitride Coatings
- 4.14.4 Oxidation and Oxidation Protection
- 4.14.5 Simultaneous Investigation of Nanostructure and Chemistry
- 4.14.6 Multinary Transition Metal Aluminium Nitrides
- 4.14.7 Summary and Outlook
- References
- 4.15. Advanced Carbon-Based Coatings
- Abstract
- Acknowledgments
- 4.15.1 Introduction
- 4.15.2 Bonding Configurations in Carbon Films
- 4.15.3 Carbon Nitride Films
- 4.15.4 Phosphorous-Carbide Films
- 4.15.5 Carbon Fluoride Films
- 4.15.6 Concluding Remarks
- Bibliography
- 4.16. Photocatalytic Coatings
- Abstract
- 4.16.1 Introduction
- 4.16.2 Fundamentals of Photocatalysis
- 4.16.3 Generalities on Photocatalytic Coatings
- 4.16.4 Peculiarities of Photocatalytic Coatings Depending on the Application
- 4.16.5 Peculiarities of Photocatalytic Coatings Depending on the Shape of the Materials
- 4.16.6 Conclusions
- References
- 4.17. Biocompatible Coating
- Abstract
- Acknowledgment
- 4.17.1 Introduction
- 4.17.2 Hemocompatible Coatings
- 4.17.3 Cytocompatible and/or Immunomodulatory Coatings
- 4.17.4 Antibacterial Coatings
- 4.17.5 Summary and Perspectives
- References
- 4.18. Antimicrobial Bioactive Polymer Coatings
- Abstract
- 4.18.1 Introduction
- 4.18.2 Current Thin-Film Approaches
- 4.18.3 Summary
- References
- 4.19. Thin-Film Diffusion Barriers for Electronic Applications
- Abstract
- Acknowledgments
- 4.19.1 Background
- 4.19.2 Definitions and Basic Equations of Permeation
- 4.19.3 Permeation Models for a Thin-Film Diffusion Barrier
- 4.19.4 Methods for Permeation Measurement
- 4.19.5 Ultrabarrier Coating Strategies
- 4.19.6 Concluding Remarks
- References
- 4.20. Diffusion Barrier Layers for Edible Food Packaging
- Abstract
- 4.20.1 Introduction
- 4.20.2 Packaging Films
- 4.20.3 Edible Coating
- 4.20.4 Added Value and Limitations of Edible Coatings: Sensory Properties
- 4.20.5 Toxicity of Polymeric Films into Contact with Foodstuff
- 4.20.6 Conclusion
- References
- 4.21. Large-Scale Industrial Coating Applications and Systems
- Abstract
- Acknowledgment
- 4.21.1 Different Equipment Aspects Classified after Their Application
- 4.21.2 Equipment Aspects Based on Applications
- 4.21.3 Design Phases
- 4.21.4 Maintenance of Batch and In-Line Systems
- 4.21.5 Project Management Organization
- References
- 4.01. Introduction to Films and Coatings: Technology and Recent Development
- Volume 5: Casting, Semi-Solid Forming and Hot Metal Forming
- 5.01. Introduction to Casting, Semi-Solid Forming and Hot Metal Forming
- Abstract
- Acknowledgments
- 5.01.1 Casting
- 5.01.2 Hot Metal Forming
- 5.01.3 Semisolid Processing
- 5.02. Advanced Casting Methodologies: Inert Environment Vacuum Casting and Solidification, Die Casting, Compocasting, and Roll Casting
- Abstract
- Acknowledgments
- 5.02.1 Introduction by Plato Kapranos
- 5.02.2 Inert Environment Vacuum Casting and Solidification by Dermot Brabazon
- 5.02.3 Recent Advances in Die Casting by Steve Midson
- 5.02.4 Compocasting by Sumsun Naher
- 5.02.5 Roll Casting by Toshio Haga and Plato Kapranos
- References
- 5.03. Advanced Casting Methodologies: Investment Casting, Centrifugal Casting, Squeeze Casting, Metal Spinning, and Batch Casting
- Abstract
- 5.03.1 Introduction by Plato Kapranos
- 5.03.2 Investment Casting by Crispen Carney
- 5.03.3 Centrifugal Casting by Annalisa Pola
- 5.03.4 Squeeze Casting by Annalisa Pola
- 5.03.5 Spin Casting by Annalisa Pola
- 5.03.6 Batch Casting by Mark Jolly
- References
- 5.04. Rapid Solidification Processing and Bulk Metallic Glass Casting
- Abstract
- 5.04.1 Introduction
- 5.04.2 Glass Forming Ability in BMG Alloys
- 5.04.3 Rapid Casting of Bulk Metallic Glass
- 5.04.4 Supercooled Alloys
- 5.04.5 Phase Crystallinity and Transformation
- 5.04.6 Conclusion
- References
- 5.05. Single-Crystal Casting/Directional Solidification
- Abstract
- 5.05.1 Directional Solidification
- 5.05.2 Investment Casting Techniques
- 5.05.3 Grain Selection and Single-Crystal Casting
- 5.05.4 Conclusions
- References
- 5.06. Semisolid Processes
- Abstract
- 5.06.1 Introduction
- 5.06.2 Thixoprocessing
- 5.06.3 Rheoprocessing
- 5.06.4 Forming Methods
- 5.06.5 Thixomolding
- 5.06.6 Semisolid Free Forming Technology
- 5.06.7 Summary
- References
- 5.07. Routes to Spheroidal Starting Material for Semisolid Metal Processing
- Abstract
- 5.07.1 Introduction
- 5.07.2 Liquid Metal Routes
- 5.07.3 Solid-State Routes
- 5.07.4 Combinations of Methods
- 5.07.5 Concluding Remarks
- References
- 5.08. Rheology of Semisolid Metallic Alloys
- Abstract
- 5.08.1 Introduction
- 5.08.2 Origins of Thixotropy
- 5.08.3 Background Rheology
- 5.08.4 Measurement of Steady-State Rheological Behavior
- 5.08.5 Exemplar Results for Rheological Behavior
- 5.08.6 Measurement of Transient Rheological Behavior
- 5.08.7 Concluding Remarks
- References
- 5.09. Alloys for Semisolid Processing
- Abstract
- 5.09.1 Fundamental Aspects
- 5.09.2 Basics of Solid to Liquid Transition in Possible Alloys for Semisolid Processing
- 5.09.3 Commercially Processed Semisolid Alloys
- 5.09.4 Alloys That Have Been Semisolid Processed in Research Units
- 5.09.5 Scientific Issues for Alloy Design
- 5.09.6 Concluding Remarks
- References
- 5.10. Modeling of Semisolid Flow
- Abstract
- Nomenclature
- Acknowledgments
- 5.10.1 Why Model Semisolid Flow?
- 5.10.2 General Purpose
- 5.10.3 One-Phase Modeling
- 5.10.4 Two-Phase Modeling
- 5.10.5 Conclusion
- References
- 5.11. Tribology in Hot Forging
- Abstract
- 5.11.1 Introduction
- 5.11.2 Load Types for Forging Tools
- 5.11.3 Optimization of Tribological Conditions
- 5.11.4 Numerical Simulation of the Tribological System in the Hot Forging Using FEM
- 5.11.5 Summary
- References
- 5.12. Casting Simulation Methods
- Abstract
- 5.12.1 Introduction
- 5.12.2 A Holistic Approach to Casting Simulation
- 5.12.3 Mathematical Modeling
- 5.12.4 Simulation Models
- 5.12.5 Special Topics in Casting Simulation
- 5.12.6 Recent Applications and Future Directions
- Appendix A
- Finite Element Formulation
- References
- 5.13. Industrial Practice and Applications
- Abstract
- 5.13.1 Introduction
- 5.13.2 Induction Heating for Thixocasting
- 5.13.3 Controls Used with Semisolid Casting
- 5.13.4 Die Design for Semisolid Castings
- 5.13.5 Examples of Aluminium-Alloy Components Produced by Semisolid Casting
- 5.13.6 Examples of Magnesium-Alloy Components Produced by Semisolid Casting
- 5.13.7 Costing and Economics of Aluminium Rheocasting
- References
- 5.14. Hot Forging
- Abstract
- 5.14.1 Open-Die Forging
- 5.14.2 Closed-Die Forging
- 5.14.3 Isothermal Forging for Complex Integral Component
- 5.14.4 Control Defect of Forgings
- References
- 5.15. Deformation Rules and Mechanism of Large-Scale Profiles Extrusion of Difficult-to-Deform Materials
- Abstract
- Acknowledgment
- 5.15.1 Fundamentals of Extrusion
- 5.15.2 Large-Scale Profiles Extrusion of Difficult-to-Deform Materials
- 5.15.3 FE Modeling and Validation
- 5.15.4 Deformation Rules and Mechanism
- 5.15.5 Optimization Design Based on FE Virtual Orthogonal Experiment
- 5.15.6 Summary and Conclusions
- References
- Relevant Websites
- 5.16. Hot Tube-Forming
- Abstract
- 5.16.1 Introduction
- 5.16.2 Hot Tube Forming for Billet Preparation
- 5.16.3 Tube Material Characterization at Elevated Temperatures
- 5.16.4 Hot Tube Forming for Components
- 5.16.5 Summary and Conclusions
- See also
- References
- 5.17. Hot Stamping
- Abstract
- 5.17.1 Concept of Hot Stamping
- 5.17.2 Advantages and Disadvantages of Hot Stamping
- 5.17.3 Material Requirements and Selection
- 5.17.4 Process Design and Quality Control
- 5.17.5 Tooling Fabrication
- 5.17.6 Forming Behavior and Process Simulation
- 5.17.7 Case Studies
- 5.17.8 Future Outlooks
- References
- 5.18. Superplastic Forming
- Abstract
- 5.18.1 Introduction
- 5.18.2 Superplastic Forming/Diffusion Bonding of Titanium Alloy Multilayer Structure
- 5.18.3 Superplastic Forming of Bellows Expansion
- 5.18.4 Ceramic Die for Superplastic Forming Titanium Alloy
- 5.18.5 Superplastic Forming of Aluminium Alloy
- 5.18.6 Superplastic Forming of γ-TiAl and Nb–Si–Fe Intermetallics
- 5.18.7 Superplastic Forming of Inconel 718 Superalloy
- 5.18.8 Concluding Remarks
- References
- 5.19. Hot Shape Rolling
- Abstract
- Acknowledgments
- 5.19.1 Principle of Shape Rolling
- 5.19.2 Characteristics of Shape Rolling
- 5.19.3 Types of Shape Rolling
- 5.19.4 Ring Rolling
- 5.19.5 Summary and Conclusions
- References
- 5.20. Modeling of Hot Forging
- Abstract
- Acknowledgments
- 5.20.1 Introduction and Definitions
- 5.20.2 Fundamentals for Modeling of Hot Forging
- 5.20.3 Macro Modeling for Hot Forging
- 5.20.4 Microstructure Evolution Modeling for Hot Forging of Ti-Alloy
- 5.20.5 3D-FE Modeling for Hot Forging of Blades
- 5.20.6 Through-Process Macro–Micro Modeling for Isothermal Local Loading Forming of Large-Scale Integral Component
- 5.20.7 Summary and Conclusions
- References
- Relevant Website
- 5.01. Introduction to Casting, Semi-Solid Forming and Hot Metal Forming
- Volume 6: Welding and Bonding Technologies
- 6.01. Introduction to Welding and Bonding Technologies
- 6.01.1 Concluding Remarks and Acknowledgments
- 6.02. Welding Processes and Technologies
- Abstract
- 6.02.1 General Introduction
- 6.02.2 Fusion Welding Processes
- 6.02.3 Solid-State Welding Processes
- See also
- References
- 6.03. Manual Metal Arc Welding and Gas Metal Arc Welding
- Abstract
- Acknowledgments
- 6.03.1 Introduction and General Problem Definition in Welding
- 6.03.2 Manual Metal Arc Welding Also Known as Shielded Metal Arc Welding
- 6.03.3 Gas Metal Arc Welding Also Known as Metal Inert Gas Welding
- See also
- References
- 6.04. Robotic Welding Technology
- Abstract
- 6.04.1 Introduction
- 6.04.2 Robotics in Welding
- 6.04.3 Robotics in Different Welding Techniques
- 6.04.4 Current Research Topics in Robotic Welding
- 6.04.5 Conclusions
- References
- 6.05. Mathematical Modeling of Weld Phenomena, Part 1: Finite-Element Modeling
- Abstract
- 6.05.1 Introduction
- 6.05.2 Application of the FEM to the Welding Processes
- 6.05.3 Thermal Analysis and the Weld Pool
- 6.05.4 Mechanical and Metallurgical Analysis
- 6.05.5 FEM Application to Fusion Welding
- 6.05.6 FEM Application to the Solid-State Welding
- 6.05.7 Concluding Remarks
- References
- 6.06. Mathematical Modeling of Weld Phenomena, Part 2: Design of Experiments and Optimization
- Abstract
- 6.06.1 Introduction
- 6.06.2 ANN Analysis
- 6.06.3 DoE Analysis
- 6.06.4 Concluding Remarks
- References
- 6.07. Welding Defects and Implications on Welded Assemblies
- Abstract
- 6.07.1 Introduction
- 6.07.2 Types of Welding Defects
- 6.07.3 Welding Defects in Several Industries and Applications
- 6.07.4 Concluding Remarks
- References
- 6.08. 9% Nickel Steels and Their Welding Behavior
- Abstract
- 6.08.1 Introduction
- 6.08.2 9% Nickel Steel for Cryogenic Applications
- 6.08.3 Welding of 9% Nickel Steel
- 6.08.4 Weldability of 9% Nickel Steel
- 6.08.5 Quality Control of Weldment
- 6.08.6 Concluding Remarks and Future Directions
- References
- 6.09. Weldability of Nickel-Base Alloys
- Abstract
- 6.09.1 Introduction
- 6.09.2 Welding Considerations
- 6.09.3 Discontinuities in Ni-Base Weldments
- 6.09.4 Dissimilar Welding
- 6.09.5 Special Material Considerations
- 6.09.6 Influence of Welding on Service Performance
- 6.09.7 Weldability Testing Techniques
- 6.09.8 Concluding Remarks
- References
- 6.10. Review of Microstructures, Mechanical Properties, and Residual Stresses of Ferritic and Martensitic Stainless-Steel Welded Joints
- Abstract
- 6.10.1 Introduction
- 6.10.2 Microstructure and Hardness Testing
- 6.10.3 Mechanical Properties
- 6.10.4 Residual Stresses
- 6.10.5 Impact Strength Testing
- 6.10.6 Discussions
- 6.10.7 Concluding Remarks
- References
- 6.11. Quality Control in Welding Process
- Abstract
- 6.11.1 Introduction
- 6.11.2 Testing the Quality of the Weld
- 6.11.3 Distortion in Weldment
- 6.11.4 Measuring Methods of Residual Stress
- 6.11.5 Concluding Remarks
- References
- 6.12. Safety and Security Conditions in Welding Processes
- Abstract
- 6.12.1 Introduction
- 6.12.2 Welding Fumes and Gases
- 6.12.3 Electric Shock Hazards in Welding
- 6.12.4 Burning Hazards
- 6.12.5 Welding Noise Effects
- 6.12.6 Ultraviolet Radiation/Infrared Radiation Hazards
- 6.12.7 Hazards of Welding Equipment
- References
- Relevant Website
- 6.13. Optimum Speed of Friction Stir Welding on 304L Stainless Steel by Finite Element Method
- Abstract
- 6.13.1 Introduction
- 6.13.2 Model Description
- 6.13.3 Computational Process
- 6.13.4 Result and Discussions
- 6.13.5 Conclusion
- 6.13.6 Future Study
- References
- 6.14. Bonding Technologies in Manufacturing Engineering
- Abstract
- 6.14.1 Introduction
- 6.14.2 Direct Bonding
- 6.14.3 Thermocompression Bonding
- 6.14.4 Surface Activated Bonding
- 6.14.5 Adhesive Bonding
- 6.14.6 Eutectic Bonding
- 6.14.7 Glass Frit Bonding
- 6.14.8 Concluding Remarks
- References
- 6.01. Introduction to Welding and Bonding Technologies
- Volume 7: Nano- and Microscale Processing – Modeling
- 7.01. Introduction to Nano- and Microscale Processing – Modeling
- Acknowledgment
- 7.01.1 Chapters in This Volume
- 7.01.2 Concluding Remarks
- 7.02. Micro/Nano Scale Energy Transport in Metallic Films and Stress Analysis: Analytical Approaches
- Abstract
- Acknowledgments
- 7.02.1 Introduction
- 7.02.2 Micro/Nano Scale Energy Transport Model for Thin Films
- 7.02.3 Analytical Solution of Nano-Scale Lattice Transport Model and Thermal Stress Equation for Metallic Film
- 7.02.4 Micro/Nano Scale Transport Model in the Lattice Subsystem in Relation to the Boltzmann Equation
- 7.02.5 Findings and Discussions
- 7.02.6 Concluding Remarks
- References
- 7.03. Thermal Stresses in Micro- and Nanostructures
- Abstract
- 7.03.1 Introduction
- 7.03.2 Analytical Treatment of Thermal Stresses at Micro/Nanosized Length Scales
- 7.03.3 Analytical Approach Incorporating Elastoplastic Analysis
- 7.03.4 Analytical Solution for Thermal Stress Incorporating Thermomechanical Coupling
- 7.03.5 Analysis of Plastic Wave Generation and Propagation due to High Intensity Pulse
- 7.03.6 Findings and Discussion
- 7.03.7 Concluding Remarks
- References
- 7.04. PVD Technology in Fabrication of Micro- and Nanostructured Coatings
- Abstract
- 7.04.1 Introduction
- 7.04.2 Surface Preparation
- 7.04.3 Vacuum Evaporation
- 7.04.4 Evaporation Sources
- 7.04.5 Gas Sputtering Coating
- 7.04.6 Ion Plating
- 7.04.7 Active Reaction Evaporation
- 7.04.8 Application of PVD Technology for Fabrication of Micro- and Nanocoatings
- 7.04.9 Concluding Remarks
- References
- 7.05. Fabrication of Micro/Nanostructured Coatings by CVD Techniques
- Abstract
- 7.05.1 Introduction
- 7.05.2 Process Characteristics
- 7.05.3 Various Types of Reactions
- 7.05.4 Coating Thickness
- 7.05.5 Coating Rate
- 7.05.6 Costs
- 7.05.7 General Suggestions
- 7.05.8 Design of CVD
- 7.05.9 Applications of CVD in Fabrication of Micro- and Nanocoatings
- 7.05.10 Concluding Remarks
- References
- 7.06. Fabrication and Properties of Micro- and Nanostructured Coatings Using Electrochemical Depositions
- Abstract
- 7.06.1 Introduction
- 7.06.2 General Principles
- 7.06.3 Coating in the Cell
- 7.06.4 Selective or Brush Coating
- 7.06.5 Chemical, Autocatalytic, and Electroless Deposition
- 7.06.6 Hard Anodization
- 7.06.7 Coating Materials
- 7.06.8 Composite Electrochemical Deposition
- 7.06.9 Hard Anodizing
- 7.06.10 Selection
- 7.06.11 Process Design for Cell Coating
- 7.06.12 Application of Electrochemical Deposition for Micro- and Nanocoatings
- 7.06.13 Concluding Remarks
- References
- 7.07. Thin Film Coating for Polymeric Micro Parts
- Abstract
- Acknowledgement
- 7.07.1 Introduction
- 7.07.2 Surface Coating Technology for Polymer Products
- 7.07.3 Thin Film Coating Technology for Micro Polymer Parts
- 7.07.4 Future Trends and Perspectives
- References
- 7.08. Electric Field–Assisted Chemical Vapor Deposition for Nanostructured Thin Films
- Abstract
- Acknowledgments
- 7.08.1 Introduction
- 7.08.2 Theoretical Basis
- 7.08.3 Experimental Concerns
- 7.08.4 Results and Discussion
- 7.08.5 Conclusions
- References
- 7.09. AFM Applications in Micro/Nanostructured Coatings
- Abstract
- 7.09.1 Introduction
- 7.09.2 Basic Performance of AFM
- 7.09.3 Cantilever
- 7.09.4 Tips
- 7.09.5 Various Modes of AFM Devices
- 7.09.6 AFM Applications for Coatings
- 7.09.7 Concluding Remarks
- References
- 7.10. Application and Advances in Microprocessing of Natural Fiber (Jute)–Based Composites
- Abstract
- 7.10.1 Introduction
- 7.10.2 Jute: Jute Plant and Jute Fiber
- 7.10.3 Treatment of the Fiber
- 7.10.4 Principles of Fiber Reinforcement
- 7.10.5 Matrix Considerations
- 7.10.6 Experimental Procedure for Composite Preparation
- 7.10.7 Composite Fabrication
- 7.10.8 Conclusions
- References
- 7.01. Introduction to Nano- and Microscale Processing – Modeling
- Volume 8: Health, Safety and Environmental Issues
- 8.01. Introduction to Health, Safety and Environmental Issues
- Abstract
- 8.01.1 Historical Background – Introduction
- 8.01.2 Pre-Industrial Revolution
- 8.01.3 The Industrial Revolution and Manufacturing
- 8.01.4 Impact of the Industrial Revolution on Health and Environment
- 8.01.5 Present Impact of Manufacturing on Health and Environment
- 8.01.6 Preview of the Contents of Volume 8
- 8.01.7 Conclusion
- Further Reading
- 8.02. Health and Environmental Impacts in Metal Machining Processes
- Abstract
- 8.02.1 Introduction
- 8.02.2 Basics of Machining Processes
- 8.02.3 Health and Environmental Impact in Traditional Machining
- 8.02.4 Health and Environmental Impacts in Nontraditional Machining
- 8.02.5 Development of Sustainable Green Machining Technologies
- 8.02.6 Concluding Remarks
- References
- 8.03. Health and Safety Issues in Emerging Surface Engineering Techniques
- Abstract
- 8.03.1 Introduction
- 8.03.2 Surface Engineering Processes
- 8.03.3 Health and Safety in Surface Coating Processes
- 8.03.4 Health and Safety in Surface Modification Processes
- 8.03.5 Strategies for Minimizing Health and Safety Impacts
- 8.03.6 Concluding Remarks
- See also
- References
- 8.04. Health Effects Associated with Welding
- Abstract
- 8.04.1 Welding Process
- 8.04.2 Welding Exposure
- 8.04.3 Health and Safety Hazards in Welding
- 8.04.4 Health Effects of Welding
- References
- 8.05. Ceramic Manufacturing Processes: Energy, Environmental, and Occupational Health Issues
- Abstract
- Acknowledgments
- 8.05.1 Introduction
- 8.05.2 Energy Consumption and CO2 Emissions
- 8.05.3 Environmental Issues
- 8.05.4 Occupational Health Issues
- 8.05.5 Summary
- References
- 8.06. A Review of Engineered Nanomaterial Manufacturing Processes and Associated Exposures
- Abstract
- 8.06.1 Overview
- 8.06.2 Introduction
- 8.06.3 Vapor/Aerosol Phase Synthesis
- 8.06.4 Liquid Phase Synthesis (Wet Chemistry)
- 8.06.5 Solid Phase Synthesis (Physical Methods)
- 8.06.6 Other Synthesis Methods
- 8.06.7 Health Hazards from Engineered Nanomaterial Manufacturing Processes
- 8.06.8 Conclusion
- Disclaimer
- References
- 8.07. Administrative Evil and Patient Health: A Critique of the Impact of Manufacturing Systems on Health Care
- Abstract
- 8.07.1 Introduction
- 8.07.2 The Development of the Key Ideas Underlying Manufacturing Business Systems
- 8.07.3 The Development of Human-Centered Systems Thinking
- 8.07.4 Health Care Systems and AMAT
- 8.07.5 Systems Quality and Health Care Provision
- 8.07.6 Conclusion
- References
- 8.08. Assessment of Impacts to Health, Safety, and Environment in the Context of Materials Processing and Related Public Policy
- Abstract
- 8.08.1 Introduction
- 8.08.2 Materials Processing, Public Policy, and Assessment
- 8.08.3 Characterization of Common Approaches to Health, Safety, and Environmental Assessment
- 8.08.4 Toward Approaches That Serve Multiple Information Needs
- 8.08.5 Summary and Conclusions
- See also
- References
- Relevant Websites
- 8.09. Environmentally friendly Manufacturing Processes in the Context of Transition to Sustainable Production
- Abstract
- 8.09.1 Introduction
- 8.09.2 Sustainable Technologies
- 8.09.3 Evaluation of Technologies’ Sustainability
- 8.09.4 Ecodesign Focused on Life-Cycle Assessment (LCA)
- 8.09.5 Conclusions
- See also
- References
- 8.10. Health and Safety in Today’s Manufacturing Industry
- Abstract
- 8.10.1 Introduction
- 8.10.2 Manufacturing Trends and Contemporary Issues
- 8.10.3 Compliance via Regulatory Bodies and Mandated Committees
- 8.10.4 Organization-Level Health and Safety Practices
- 8.10.5 An Evolving Manufacturing Industry
- 8.10.6 Concluding Remarks
- References
- 8.11. Economic Implications of Impact of Manufacturing on Environment and Health
- Abstract
- 8.11.1 Manufacturing: The Early Days (Eighteenth to Mid-Nineteenth Century)
- 8.11.2 Manufacturing, the Middle Years, Late Nineteenth Century to World War II
- 8.11.3 Impact of Manufacturing on Environment and Health: The Present Time
- 8.11.4 Impact of Manufacturing on Health
- 8.11.5 Economic Impact of Manufacturing
- 8.11.6 Conclusions
- Further Reading
- 8.01. Introduction to Health, Safety and Environmental Issues
- Volume 9: Laser Machining and Surface Treatment
- 9.01. Introduction to Laser Machining and Surface Treatment
- Abstract
- Acknowledgment
- 9.01.1 Laser Machining, Forming, and Welding Processes
- 9.01.2 Surface Engineering Applications
- 9.01.3 Chapters in This Volume
- 9.01.4 Concluding Remarks
- 9.02. Laser Heating and the Phase Change Process
- Abstract
- Acknowledgments
- 9.02.1 Introduction
- 9.02.2 Mathematical Modeling of Laser Nonconduction Heating of Two-Dimensional Solid Plate
- 9.02.3 Analytical Treatment of Steady and Transient Phase Change Processes in Semi-Infinite Solids
- 9.02.4 Numerical Treatment of the Phase Change Process
- 9.02.5 Results and Discussions
- 9.02.6 Concluding Remarks
- References
- 9.03. Laser Treatment of Steel Surfaces: Numerical and Experimental Investigations of Temperature and Stress Fields
- Abstract
- Acknowledgments
- 9.03.1 Introduction
- 9.03.2 Mathematical Analysis Pertinent to Thermal Stresses
- 9.03.3 Experimental
- 9.03.4 Results and Discussions
- 9.03.5 Conclusions
- References
- 9.04. Laser Plasma Interaction and Shock Material Processing
- Abstract
- Acknowledgments
- 9.04.1 Introduction: The Laser Shock Processing Technique
- 9.04.2 Generation of Laser-Induced Shock Waves Following High-Intensity Laser Interaction
- 9.04.3 Numerical Simulation of LSP Treatments: Coupled Laser Interaction + Mechanical Material Behavior Analysis
- 9.04.4 Experimental Implementation of LSP Treatments
- 9.04.5 Experimental Results on Material Properties Modifications Induced by LSP Treatments
- 9.04.6 Discussion and Outlook: LSP as an Emerging Key Technology
- See also
- References
- 9.05. Laser Surface Patterning
- Abstract
- 9.05.1 Introduction
- 9.05.2 Laser Machining-Based Patterning
- 9.05.3 Deposition-Based Patterning by Laser
- 9.05.4 Summary
- References
- 9.06. Laser Drilling of Metallic and Nonmetallic Substrates
- Abstract
- Acknowledgment
- 9.06.1 Introduction
- 9.06.2 Laser Drilling Methods
- 9.06.3 Lasers for Drilling
- 9.06.4 Laser Radiation Absorption Mechanisms and Effects of Laser Beam Parameters on the Drilling Process
- 9.06.5 Physical Processes Involved in Laser Drilling and Material Removal Mechanisms
- 9.06.6 Quality of Laser-Drilled Holes
- 9.06.7 Techniques for Improving Quality of Laser-Drilled Holes
- 9.06.8 Effect of Superposition, Modulation, and Shaping of Laser Pulses on Drilling
- 9.06.9 Elimination of Spatter with Surface Coating
- 9.06.10 Hybrid Laser Drilling
- 9.06.11 Ultrafast Lasers Drilling
- 9.06.12 Laser Micromachining and Nanomachining
- 9.06.13 Modeling of Laser Drilling Process
- 9.06.14 Laser Drilling in Different Materials
- 9.06.15 Industrial Applications of Laser Drilling
- 9.06.16 Summary
- References
- 9.07. Laser Drilling of Metallic and Nonmetallic Materials and Quality Assessment
- Abstract
- 9.07.1 Introduction
- 9.07.2 Drilling Lasers, Associated Equipment, and Processes
- 9.07.3 Quality Assessment
- 9.07.4 The Laser Drilling Process
- 9.07.5 Related Processes
- References
- 9.08. Laser Drilling and Efficiency Analysis
- Abstract
- Nomenclature
- Acknowledgment
- 9.08.1 Introduction
- 9.08.2 Analysis
- 9.08.3 Experimental
- 9.08.4 Results and Discussion
- 9.08.5 Conclusions
- References
- 9.09. Thermal Modeling of Laser Machining Process
- Abstract
- 9.09.1 Introduction
- 9.09.2 Problems in Laser Machining
- 9.09.3 Recent Development of Laser Machining
- 9.09.4 Laser Theory
- 9.09.5 History of Laser
- 9.09.6 Types of Lasers and Their Characteristics
- 9.09.7 Laser Machining Process
- 9.09.8 Process Modeling
- 9.09.9 Thermal Modeling
- 9.09.10 Laser Machining and Thermal Modeling
- 9.09.11 Parameters in Modeling of Laser Machining
- 9.09.12 Conclusions
- References
- 9.10. Laser Machining and Laser-Assisted Machining of Ceramics
- Abstract
- 9.10.1 Introduction
- 9.10.2 Laser Machining of Ceramics
- 9.10.3 Laser-Assisted Machining of Ceramics
- 9.10.4 Conclusion
- References
- 9.11. Laser Cutting Efficiency and Quality Assessments
- Abstract
- Nomenclature
- Acknowledgment
- 9.11.1 Introduction
- 9.11.2 Mathematical Analysis
- 9.11.3 Experimental
- 9.11.4 Results and Discussion
- 9.11.5 Conclusions
- References
- 9.12. Laser Applications in the Field of Plastics
- Abstract
- Acknowledgments
- 9.12.1 Laser Processing of Plastics
- 9.12.2 Laser Cutting
- 9.12.3 Laser Marking and Engraving
- 9.12.4 Laser Welding
- 9.12.5 New Applications
- References
- 9.13. Laser Gas–Assisted Nitriding of Ti Alloys
- Abstract
- Acknowledgments
- 9.13.1 Introduction
- 9.13.2 Nitriding, Carburizing, and Other Surface Treatments
- 9.13.3 CW-Mode Laser Nitriding
- 9.13.4 Pulsed Laser Nitriding
- 9.13.5 Plasma-Assisted Nitriding
- 9.13.6 Conclusions
- References
- 9.14. Laser Duplex Treatment of Surfaces for Improved Properties
- Abstract
- Acknowledgments
- 9.14.1 Introduction
- 9.14.2 Laser Gas-Assisted Nitriding of Titanium Alloy Surface
- 9.14.3 Experimental Study of Laser Treatment of Surfaces
- 9.14.4 Findings and Discussions
- 9.14.5 Concluding Remarks
- References
- 9.15. Laser Surface Treatment and Efficiency Analysis
- Abstract
- Acknowledgment
- 9.15.1 Introduction
- 9.15.2 Experimental
- 9.15.3 Mathematical Analysis
- 9.15.4 Results and Discussion
- 9.15.5 Conclusions
- References
- 9.01. Introduction to Laser Machining and Surface Treatment
- Volume 10: Advances in Additive Manufacturing and Tooling
- 10.01. Introduction to Advances in Additive Manufacturing and Tooling
- Abstract
- 10.02. Additive Manufacturing: An Overview
- Abstract
- 10.02.1 Introduction
- 10.02.2 What Is Additive Manufacturing?
- 10.02.3 The Additive Manufacturing Process Chain
- 10.02.4 Current Usage of Additive Manufacturing
- 10.02.5 How Additive Manufacturing Is Being Used Today
- 10.02.6 Rapid Manufacture and Engineering
- 10.02.7 Future Developments in Additive Manufacturing
- 10.02.8 Speculations on the Impacts Additive Manufacturing Will Have
- 10.02.9 Conclusions
- References
- 10.03. Stereolithography
- Abstract
- 10.03.1 Introduction
- 10.03.2 Stereolithography Process Basics
- 10.03.3 Commercial Stereolithography Systems
- 10.03.4 Material Issues
- 10.03.5 Modeling of the Stereolithography Process
- 10.03.6 Microstereolithography
- 10.03.7 New Topics in Stereolithography
- 10.03.8 Applications
- 10.03.9 Research Overview
- 10.03.10 Research Directions
- See also
- References
- 10.04. Advances in Fused Deposition Modeling
- Abstract
- Acknowledgments
- 10.04.1 Introduction
- 10.04.2 The FDM Process
- 10.04.3 The FDM Machines
- 10.04.4 The FDM Materials
- 10.04.5 Advantages and Limitations
- 10.04.6 FDM Process Parameters
- 10.04.7 FDM Insight Software
- 10.04.8 Research and Developments in FDM
- 10.04.9 Research in FDM Part Quality Improvement
- 10.04.10 Research in FDM Process Improvement
- 10.04.11 Research in New Material Development
- 10.04.12 Research in FDM Material Properties
- 10.04.13 Research in FDM Applications
- 10.04.14 Conclusions and Research Directions
- References
- 10.05. Selective Laser Sintering/Melting
- Abstract
- 10.05.1 Introduction
- 10.05.2 Description of the Process
- 10.05.3 Parameters
- 10.05.4 Laser Microsintering
- 10.05.5 Consolidation of Powders
- 10.05.6 Characterization and Complementary Postprocessing
- 10.05.7 Systems and Manufacturers
- 10.05.8 Application in Tooling
- 10.05.9 Other Applications
- 10.05.10 Comparison with Other AM Processes
- 10.05.11 Economy of the Process
- 10.05.12 Future Work
- See also
- References
- 10.06. Electron Beam Melting
- Abstract
- 10.06.1 Introduction
- 10.06.2 History
- 10.06.3 Basic Operation
- 10.06.4 Additional Equipment Necessary
- 10.06.5 EBM Research
- 10.06.6 EBM Applications
- 10.06.7 Research Overview
- 10.06.8 Conclusions
- References
- 10.07. Laser Powder Deposition
- Abstract
- Acknowledgments
- 10.07.1 Introduction
- 10.07.2 Laser Deposition
- 10.07.3 Laser Deposition Fundamentals
- 10.07.4 Interaction between the Laser Beam and the Powder Jet
- 10.07.5 Microstructure Formation in Laser-Deposited Materials
- 10.07.6 Laser Powder Deposition Models
- 10.07.7 Defects in Laser Deposited Materials
- 10.07.8 Closed-Loop Process Control Methods
- 10.07.9 System Manufacturers
- 10.07.10 Applications
- 10.07.11 Conclusions and Future Directions
- References
- 10.08. Three Dimensional Printing
- Abstract
- 10.08.1 Introduction
- 10.08.2 3DP – Definition and Classification
- 10.08.3 Technical and Economical Evaluation
- 10.08.4 Applications
- 10.08.5 Main Research Areas
- 10.08.6 Strength and Weaknesses of the 3DP Process
- 10.08.7 Conclusions
- References
- Relevant Websites
- 10.09. Tissue Engineering Applications of Additive Manufacturing
- Abstract
- 10.09.1 Introduction
- 10.09.2 TE Scaffold Design
- 10.09.3 TE Scaffold Fabrication by AM Methods
- 10.09.4 Future Directions
- 10.09.5 Conclusion
- References
- 10.10. Recent Advances in Additive Biomanufacturing
- Abstract
- Acknowledgments
- 10.10.1 Introduction
- 10.10.2 Additive Biomanufacturing
- 10.10.3 Conclusions and Future Perspectives
- References
- 10.11. Laser-Assisted Additive Manufacturing for Metallic Biomedical Scaffolds
- Abstract
- 10.11.1 Introduction
- 10.11.2 Scaffolds and Implants in Tissue Engineering
- 10.11.3 Additive Manufacturing Technologies for Scaffolds and Implants
- 10.11.4 Why Metals?
- 10.11.5 Laser-Assisted AM Technologies
- 10.11.6 Laser-Assisted Surface Modification of Metallic Scaffolds
- 10.11.7 Research Gaps, Problems, and Challenges
- 10.11.8 Conclusions
- References
- 10.12. Direct Rapid Tooling
- Abstract
- Acknowledgment
- 10.12.1 Introduction
- 10.12.2 Rapid Tooling Overview
- 10.12.3 Direct Rapid Tooling
- 10.12.4 Case Study I – Direct SL Shell Tooling
- 10.12.5 Case Study II – WAX SL Shell Tooling
- 10.12.6 Conclusion
- 10.12.7 Future Directions
- References
- 10.13. Indirect Rapid Tooling
- Abstract
- 10.13.1 Introduction
- 10.13.2 Tooling Requirements and Rapid-Tooling Challenges
- 10.13.3 Rapid Hard Tooling
- 10.13.4 Indirect Rapid Tooling
- 10.13.5 Rapid Tooling Process Selection and Manufacturability Evaluation
- 10.13.6 Summary
- See also
- References
- 10.14. CAD Issues in Additive Manufacturing
- Abstract
- 10.14.1 Introduction
- 10.14.2 Interface between the CAD and AM System
- 10.14.3 Slicing CAD Model
- 10.14.4 Determination of Build Orientation and Optimization
- 10.14.5 Potential Problems and Procedures for Repairing STL Files
- 10.14.6 Additive Manufacturing File Format
- 10.14.7 Conclusion and Suggestions for Future Work
- References
- 10.01. Introduction to Advances in Additive Manufacturing and Tooling
- Volume 11: Advanced Machining Technologies
- 11.01. Introduction to Advanced Machining Technologies
- Abstract
- 11.01.1 Need for Tool-Based Micro-/Nanoscale Machining
- 11.01.2 Synergistic Development for Micro-/Nanoscale Machining
- 11.01.3 Tool-Based Machining Processes for Micro-/Nanoscale Applications
- 11.01.4 Compound Micromachining – A Recent Frontier in the Horizon
- 11.01.5 Summary
- References
- 11.02. Machine Tools for Micro- and Nanometer Scale Processing
- Abstract
- 11.02.1 Introduction
- 11.02.2 Industrial Demands on Machine Tools for Micro- and Nanometer Scale Processing
- 11.02.3 Structural Design of Machine Tools for Micro- and Nanometer Scale Processing
- 11.02.4 Fundamental Structural Modules in Machine Tool for Micro- and Nanometer Scale Processing
- 11.02.5 Future Evolutionary Trends of Machine Tool Technologies for Micro- and Nanometer Scale Processing
- 11.02.6 Conclusions
- References
- 11.03. Continuum Micromechanics and Molecular Dynamics Simulation
- Abstract
- 11.03.1 Continuum Mechanics Modeling of Machining Processes
- 11.03.2 Micromechanics Modeling of Cutting of Composite Materials
- 11.03.3 Molecular Dynamics Modeling and Simulation of Ductile Mode Cutting of Brittle Materials
- References
- 11.04. Fast and Fine Tool Servo for Ultraprecision Machining
- Abstract
- 11.04.1 Introduction
- 11.04.2 Design Challenges of an FTS System
- 11.04.3 Classification of Fast Tool Servo
- 11.04.4 Long-Stroke Fast Tool Servo
- 11.04.5 Hybrid FTS/STS
- 11.04.6 More Promising Challenges
- 11.04.7 Conclusions
- References
- 11.05. Compound and Hybrid Micromachining Processes
- Abstract
- 11.05.1 Introduction
- 11.05.2 Characteristics of the Compound and Hybrid Micromachining Processes
- 11.05.3 Requirements of Compound and Hybrid Processes
- 11.05.4 Compound Micromachining Processes and Related Applications
- 11.05.5 Hybrid Micromachining Processes and Related Applications
- 11.05.6 Summary
- References
- 11.06. Compound and Hybrid Micromachining: Part II – Hybrid Micro-EDM and Micro-ECM
- Abstract
- 11.06.1 Introduction
- 11.06.2 Overview of Micro-EDM and Micro-ECM
- 11.06.3 Sequential Micro-EDM and Micro-ECM
- 11.06.4 Micro-EDM Using Deionized Water
- 11.06.5 Simultaneous Micro-EDM and Micro-ECM Drilling
- 11.06.6 Simultaneous Micro-EDM and ECM Milling
- 11.06.7 Summary
- References
- 11.07. Micromilling
- Abstract
- 11.07.1 Introduction
- 11.07.2 Microend Mill
- 11.07.3 Micromilling Operation
- 11.07.4 Cutting Process
- 11.07.5 Material
- 11.07.6 Conclusions
- References
- 11.08. Fundamentals and Modeling of Micro-End Milling Operation
- Abstract
- 11.08.1 Introduction
- 11.08.2 Size Effect in Micro-Milling
- 11.08.3 Minimum Chip Thickness
- 11.08.4 Burr Formation
- 11.08.5 Mechanistic Modeling of Micro-Milling Forces
- 11.08.6 Laser-Assisted Micro-Milling
- 11.08.7 Chatter Vibrations in Micro-Milling
- 11.08.8 Concluding Remarks
- References
- 11.09. Diamond Turning
- Abstract
- 11.09.1 Introduction: Background and Definition
- 11.09.2 Products and Applications
- 11.09.3 Machine Tool Development
- 11.09.4 Diamond-Cutting Tool
- 11.09.5 Mechanics of Material Removal
- 11.09.6 Surface Finish Characteristics
- 11.09.7 Tool Wear Characteristics
- 11.09.8 Summary and Outlook
- References
- 11.10. High-Speed Machining
- Abstract
- 11.10.1 Introduction
- 11.10.2 Typical Cutting Tool Materials Used in High-Speed Machining
- 11.10.3 Development of Machine Tools for High-Speed Machining
- 11.10.4 Modeling and Simulation of High-Speed Machining
- 11.10.5 Economics of High-Speed Machining
- 11.10.6 Typical Experimental Studies on High-Speed Machining
- 11.10.7 Conclusions
- References
- 11.11. Machining with Least Quantity Lubrication
- Abstract
- Acknowledgment
- 11.11.1 Introduction
- 11.11.2 Tribology in MQL Machining
- 11.11.3 MQL Machining Technologies
- 11.11.4 Concluding Remarks
- References
- 11.12. Burr Formation in Machining Processes: A Review
- Abstract
- 11.12.1 Introduction
- 11.12.2 Burr Formation in Turning Process
- 11.12.3 Burr Formation in Drilling Process
- 11.12.4 Burr Formation in Milling Process
- 11.12.5 Conclusion and Future Research Direction
- References
- 11.13. Heat-Assisted Machining
- Abstract
- 11.13.1 Introduction
- 11.13.2 Principles of Hot Machining
- 11.13.3 Brief Overview of PEM
- 11.13.4 Brief Overview of Laser-Assisted Machining (LAM)
- 11.13.5 Effect of Heating Temperature (in the Furnace Heating Method) on the Machinability of Materials
- 11.13.6 Induction Heat-Assisted Machining Applied to End Milling
- 11.13.7 Benefits of Induction Heat-Assisted End Milling of Stainless Steel AISI 304
- 11.13.8 Benefits of Induction Heat-Assisted End Milling of Titanium Alloy – Ti–6Al–4V
- 11.13.9 Conclusion
- References
- 11.14. Micro-Electrical Discharge Machining (Micro-EDM): Processes, Varieties, and Applications
- Abstract
- 11.14.1 Introduction
- 11.14.2 Brief Overview of Micro-EDM
- 11.14.3 Micro-EDM System Components
- 11.14.4 Micro-EDM Process Control Parameters
- 11.14.5 Micro-EDM Performance Measurement Parameters
- 11.14.6 Micro-EDM Process Varieties and Related Applications
- 11.14.7 Advances in Micro-EDM: Innovative Applications
- 11.14.8 Summary
- References
- 11.15. Electrochemical Micromachining
- Abstract
- 11.15.1 Introduction
- 11.15.2 Fundamentals of EMM
- 11.15.3 Pulsed Electrochemical Micromachining
- 11.15.4 Experimental Setup
- 11.15.5 Characteristics of EMM
- 11.15.6 EMM-Based Processes
- 11.15.7 Conclusions and Future Scope
- References
- 11.16. Ultrasonic Vibration Diamond Cutting and Ultrasonic Elliptical Vibration Cutting
- Abstract
- 11.16.1 Introduction
- 11.16.2 Ultrasonic Vibration Diamond Cutting
- 11.16.3 Ultrasonic Elliptical Vibration Cutting
- 11.16.4 Summary
- References
- 11.17. Ultrasonic Vibration Cutting: Part II: Ductile Cutting and Analytical Force Models for the Elliptical Vibration Cutting Process
- Abstract
- 11.17.1 Introduction
- 11.17.2 Ductile Machining Model for the EVC Process
- 11.17.3 Ductile Machining Model Validation and Analysis
- 11.17.4 Analytical Force Model for the Orthogonal EVC Process
- 11.17.5 Conclusion
- References
- 11.18. Electrolytic In-Process Dressing (ELID) Grinding for Nano-Surface Generation
- Abstract
- 11.18.1 Introduction
- 11.18.2 Nano-Surface Generation by Grinding
- 11.18.3 In-Process Dressing of Super Abrasive Wheel
- 11.18.4 History of ELID Grinding
- 11.18.5 Classifications of ELID Grinding
- 11.18.6 Fundamental Study on ELID Grinding
- 11.18.7 Study Related to Control of ELID Grinding Process
- 11.18.8 Study Related to ELID Grinding Machine Development
- 11.18.9 Study Related to Application of ELID Grinding
- 11.18.10 Conclusions
- References
- 11.19. Microelectrochemical Deposition
- Abstract
- 11.19.1 Introduction
- 11.19.2 Process Mechanism
- 11.19.3 Micromanufacturing Using ECD
- 11.19.4 Conclusions
- See also
- References
- 11.01. Introduction to Advanced Machining Technologies
- Volume 12: Thermal Engineering of Steel Alloy Systems
- 12.01. Introduction to Thermal Engineering of Steel Alloy Systems
- Abstract
- Acknowledgments
- 12.02. Introduction to Steel Heat Treatment
- Abstract
- 12.02.1 Introduction
- 12.02.2 Steel Classification
- 12.02.3 Fe–C Diagram
- 12.02.4 Steel Transformation
- 12.02.5 Time-Temperature-Tranformation Diagrams
- 12.02.6 Hardenability
- 12.02.7 Tempering
- References
- 12.03. Hardenability of Steel
- Abstract
- Acknowledgments
- 12.03.1 Introduction
- 12.03.2 Discussion
- 12.03.3 Conclusions
- References
- 12.04. Controlling the Cooling Process – Measurement, Analysis, and Quality Assurance
- Abstract
- 12.04.1 Introduction
- 12.04.2 A Short Historical Overview of Test Methods
- 12.04.3 Standards for Testing Quenching Media
- 12.04.4 Procedure to Record Cooling Curves
- 12.04.5 Different Types of Test Probe
- 12.04.6 Cooling Curve Analysis
- 12.04.7 Influence of Process Parameters, Aging, and Contaminations on Cooling Characteristics for Oils and Polymers
- 12.04.8 Maintenance and Quality Assurance (Flame Point, Water Content, etc., ref to CQI-9)
- 12.04.9 Outlook
- See also
- References
- 12.05. Calculation of the Heat Transfer Coefficient Based on Experiments by the Liscic Probes
- Abstract
- 12.05.1 Characteristics of the Heat Transfer at Quenching
- 12.05.2 Laboratory Tests to Evaluate the Cooling Intensity of Liquid Quenchants
- 12.05.3 Requirement for a Workshop Designed Test to Evaluate the Cooling Intensity of Liquid Quenchants
- 12.05.4 Temperature Gradient Method for Evaluation of Cooling Intensity When Quenching in Workshop Conditions
- 12.05.5 Temperature Measurement and Unavoidable Physical Phenomena When Measuring Transient Temperatures at Quenching
- 12.05.6 Design and Characteristics of the Liscic Probes
- 12.05.7 Influence of Wetting Kinematics on the Heat Transfer Coefficient
- 12.05.8 Inverse Heat Conduction Problem
- 12.05.9 Finite Differences and Finite Volumes for the HCE
- 12.05.10 Smoothing of Measured Temperatures
- 12.05.11 Numerical Examples
- See also
- References
- 12.06. Metallo-Thermo-Mechanical Coupling in Quenching
- Abstract
- Acknowledgments
- 12.06.1 Introduction
- 12.06.2 Kinetics of Phase Transformation and Structures in Solids
- 12.06.3 Basic Theory and Governing Equations
- 12.06.4 Inelastic Constitutive Equation
- 12.06.5 Material Data and the Database
- 12.06.6 Computer Code Relevant to Metallo-Thermo-Mechanical Simulation – COSMAP
- 12.06.7 Jominy End Quenching
- 12.06.8 Carburized Quenching
- 12.06.9 Dual Frequency Induction Hardening
- 12.06.10 Laser – Hardening
- 12.06.11 Japanese Sword
- 12.06.12 Benchmark Results on Heat Treating Simulation
- 12.06.13 Concluding Remarks on This Chapter
- References
- 12.07. Intensive Quenching
- Abstract
- 12.07.1 Introduction
- 12.07.2 Basics of Intensive Quenching
- 12.07.3 Intensive Quenching IQ-2 and IQ-3 Technologies
- 12.07.4 Discussion
- 12.07.5 Summary
- References
- 12.08. Residual Stresses Produced by Quenching of Martensitic Steels
- Abstract
- 12.08.1 Introduction
- 12.08.2 Definitions of Residual Stresses
- 12.08.3 Qualitative Discussion of Residual Stress Formation in Steel
- 12.08.4 Methods to Measure Residual Stresses in Steel
- 12.08.5 Modeling of Heat Treatment Stresses
- 12.08.6 Through Hardening
- 12.08.7 Surface Hardening
- 12.08.8 Effect of Tempering on Residual Hardening Stresses
- 12.08.9 Effect of Fatigue on Residual Hardening Stresses
- 12.08.10 Examples of Commercial Codes for Calculation of Residual Stresses due to Martensite Hardening
- See also
- References
- 12.09. Distortion Engineering: Basics and Application to Practical Examples of Bearing Races
- Abstract
- Acknowledgment
- 12.09.1 Introduction
- 12.09.2 Basics of Distortion Generation
- 12.09.3 Collaborative Research Center ‘Distortion Engineering’
- 12.09.4 Distortion Engineering of Bearing Races: Parameters and Variables
- 12.09.5 Distortion Engineering of Bearing Races: Mechanisms
- 12.09.6 Distortion Engineering: Compensation of Distortion
- 12.09.7 Final Remarks
- See also
- References
- 12.10. Austenite Formation and Microstructural Control in Low-Alloy Steels
- Abstract
- 12.10.1 Introduction
- 12.10.2 Austenite Formation
- 12.10.3 Typical Heat Treatments and Processing of Austenite
- 12.10.4 Effects of Microstructure, Composition, and Heating Rate on Austenite Formation
- 12.10.5 Austenite Structural Development
- 12.10.6 Summary
- See also
- References
- 12.11. Quench and Tempered Martensitic Steels: Microstructures and Performance
- Abstract
- 12.11.1 Introduction
- 12.11.2 Martensite Formation and Crystallographic Considerations
- 12.11.3 Deformation, Strengthening, and Mechanical Properties of Quench and Tempered Martensitic Microstructures
- 12.11.4 Fracture and Low-Toughness Phenomena in Carbon and Low-Alloy Carbon Steels
- 12.11.5 Summary
- References
- 12.12. Microstructure and Properties of Gas Carburized Steels
- Abstract
- 12.12.1 Introduction
- 12.12.2 Fundamentals – Carbon and Hardness Profiles
- 12.12.3 Morphology of Carburized Microstructures
- 12.12.4 Further Microstructural Features
- 12.12.5 Special Applications of Carburizing
- 12.12.6 Properties
- 12.12.7 Summary
- References
- 12.13. Development of Compound Layer and Diffusion Zone during Nitriding and Nitrocarburizing of Iron and Steels
- Abstract
- 12.13.1 Introduction
- 12.13.2 Thermodynamic Principles of Nitriding and Nitrocarburizing
- 12.13.3 Kinetics of Compound Layer Formation
- 12.13.4 Nitriding of Steels
- 12.13.5 Modeling
- References
- 12.14. Case Structure and Properties of Nitrided Steels
- Abstract
- 12.14.1 Microstructure and Development of Nitrided Cases
- 12.14.2 Nitridability of Steels
- 12.14.3 Properties of Nitrided Steels
- 12.14.4 Selection of Steels and Nitriding Conditions for the Manufacture of Load-Specific Nitrided Cases
- Appendix: Chemical Composition of the Investigated Steels
- References
- 12.15. Induction Hardening: Technology, Process Design, and Computer Modeling
- Abstract
- 12.15.1 Introduction
- 12.15.2 Design Considerations for Induction-Hardening Processes
- 12.15.3 Computer Modeling
- 12.15.4 Induction-Hardening Systems and Applications
- 12.15.5 A Review of Modern Power Supplies for Induction Hardening
- 12.15.6 Load Matching Induction-Hardening Power Supplies
- 12.15.7 Conclusion
- References
- 12.16. Microstructures and Mechanical Performance of Induction-Hardened Medium-Carbon Steels
- Abstract
- Acknowledgments
- 12.16.1 Fundamentals of Induction Hardening
- 12.16.2 Rapid Austenitization and Hardenability of Steel Microstructures
- 12.16.3 Residual Stress and Its Effects on Mechanical Properties
- 12.16.4 Characterization of Induction-Hardened Components
- 12.16.5 Strength and Fatigue of Induction-Hardened Parts
- 12.16.6 Industrial Standards Relevant to Induction Hardening
- 12.16.7 Summary and Conclusions
- References
- 12.01. Introduction to Thermal Engineering of Steel Alloy Systems
- Volume 13: Sensor Materials, Technologies and Applications
- 13.01. Introduction to Sensor Materials, Technologies and Applications
- Abstract
- Acknowledgments
- 13.01.1 Sensing and Sensors
- 13.01.2 Concluding Remarks
- 13.02. Review of Physical Principles of Sensing and Types of Sensing Materials
- Abstract
- 13.02.1 Introduction
- 13.02.2 Metals as Sensing Material
- 13.02.3 Optical Fiber Sensing Materials
- 13.02.4 Semiconductors
- 13.02.5 Dielectric Materials
- 13.02.6 Magnetic and Superconducting Materials
- 13.02.7 Solid Electrolytes
- 13.02.8 Biological Sensing Materials
- 13.02.9 Conclusion
- See also
- References
- 13.03. Review of Recent Developments in Sensing Materials
- Abstract
- 13.03.1 Introduction
- 13.03.2 Metals
- 13.03.3 Metal Oxide
- 13.03.4 Metal Organic Frameworks
- 13.03.5 Solid Electrolytes
- 13.03.6 Carbon Nanotubes and Graphene
- 13.03.7 Sol–Gel Materials
- 13.03.8 Nanomaterials and Nanoparticles
- 13.03.9 Temperature Sensing Materials
- 13.03.10 Optic Fiber Sensing Material
- 13.03.11 Mass Sensing Materials
- 13.03.12 Light Sensing Materials
- 13.03.13 Humidity Sensing Materials
- 13.03.14 Motion Sensing Materials
- 13.03.15 Conclusions
- References
- 13.04. Coatings for Optical Fiber Sensors
- Abstract
- 13.04.1 Introduction
- 13.04.2 Optical Fiber Sensor Configurations
- 13.04.3 Sensitive Coatings
- 13.04.4 Concluding Remarks
- References
- 13.05. Issues of Connectivity, Durability, and Reliability of Sensors and Their Applications
- Abstract
- 13.05.1 Introduction
- 13.05.2 Classification of Sensors and Their Components
- 13.05.3 Application of Sensors
- 13.05.4 Use of Sensor in Monitoring and Measurement
- 13.05.5 Conclusions
- References
- 13.06. Commercialization and Application-Driven Economic Viability of Sensor Technology
- Abstract
- 13.06.1 Economic Trends
- 13.06.2 Fundamentals of Cost Estimates
- 13.06.3 Design Strategies
- 13.06.4 Application Examples
- References
- 13.07. Structural Properties and Sensing Characteristics of Sensing Materials
- Abstract
- 13.07.1 Introduction
- 13.07.2 Operation Mechanism of the Ion-Sensitive Field-Effect Transistor
- 13.07.3 Deposition Method of Sensing Film
- 13.07.4 Structural Properties of Sensing Film
- 13.07.5 Sensing Characteristics of Sensing Film
- 13.07.6 Label-Free Detection of Biomolecules Using a Rare-Earth Oxide-Based EIS Biosensor
- 13.07.7 Conclusions and Perspectives
- References
- 13.08. Developments in Semiconducting Oxide-Based Gas-Sensing Materials
- Abstract
- Acknowledgment
- 13.08.1 Introduction
- 13.08.2 Gas-Sensing Materials and Mechanism
- 13.08.3 Evolution of Dimensionality in Gas Sensor Materials and Device Arrangement
- 13.08.4 Sensing Mechanism of 1-D Nanostructures with Special Morphology
- 13.08.5 Enhancement of Gas-Sensing Performance
- 13.08.6 Summary and Future Outlook
- References
- 13.09. Properties and Customization of Sensor Materials for Biomedical Applications
- Abstract
- 13.09.1 Introduction
- 13.09.2 Ionic Liquids and Sensing
- 13.09.3 Recent Trends in Sensing with Conducting Polymers
- 13.09.4 Recent Developments in Nanomaterial-Based Sensors
- 13.09.5 Ionogels: Diverse Materials for Sensing Platforms
- 13.09.6 Future Trends
- References
- 13.10. Recent Developments in Miniaturization of Sensor Technologies and Their Applications
- Abstract
- 13.10.1 Introduction
- 13.10.2 Examples of Miniaturized Sensors
- 13.10.3 General Design of a Sensor
- 13.10.4 What Is a Nanosensor?
- 13.10.5 Application of Nanotechnology in Development of Smart Sensors
- 13.10.6 Some Nanostructures Applied in Sensors
- 13.10.7 Applications of Nanosensors
- 13.10.8 Nanotube-Based Sensors
- 13.10.9 Nanowire-Based Sensors
- 13.10.10 Other Optical-Based Sensors
- 13.10.11 Nanoparticle-Based Biodetection (Supersensitive Detection of Pathogen Biomarkers)
- 13.10.12 Application of Nanosensors in Quantum Communication Using Learning Automata
- 13.10.13 Application of Nanosensors in Biotechnology
- 13.10.14 Collection and Detection of New Practical Future Objectives
- 13.10.15 Recent Applications of Miniaturized Sensors
- 13.10.16 Future Prospects
- 13.10.17 Concluding Remarks
- References
- 13.11. Optical Spin Generated by a Modified Add-Drop Filter for Network Sensors
- Abstract
- 13.11.1 Introduction
- 13.11.2 Theoretical Background
- 13.11.3 Simulation Results and Discussion
- 13.11.4 Conclusion
- References
- 13.12. Development of an Integrated Electrochemical Sensing System to Monitor Port Water Quality Using Autonomous Robotic Fish
- Abstract
- Acknowledgments
- 13.12.1 Introduction
- 13.12.2 The SHOAL Robotic Fish
- 13.12.3 State of the Art of Portable Analytical Systems for the Monitoring of Seawater
- 13.12.4 Description of the SHOAL Electrochemical Microsystem
- 13.12.5 Testing and Operating the SHOAL Electrochemical Sensing System
- 13.12.6 Perspectives
- References
- 13.13. Wireless Sensor Networks: From Real World to System Integration – Alternative Hardware Approaches
- Abstract
- 13.13.1 Introduction
- 13.13.2 Wireless Sensor Network Technologies
- 13.13.3 Hardware Platforms in the State of the Art
- 13.13.4 New Frontiers in WSN Applications
- 13.13.5 Power Management Approaches
- 13.13.6 Platform Adaptability
- See also
- References
- 13.14. Vision-Based Sensor Technologies – Webcam: A Multifunction Sensor
- Abstract
- 13.14.1 Introduction
- 13.14.2 Image Recognition
- 13.14.3 Webcam as a Multifunction Sensor
- 13.14.4 Summary and Conclusions
- References
- Relevant Websites
- 13.15. Application Field–Specific Synthesizing of Sensing Technology: Civil Engineering Application of Ground-Penetrating Radar Sensing Technology
- Abstract
- 13.15.1 Introduction
- 13.15.2 GPR Sensing Technology
- 13.15.3 Transportation and Geotechnical Engineering
- 13.15.4 Hydraulic and Environmental Engineering
- 13.15.5 Structural Engineering
- 13.15.6 Summary
- References
- 13.16. Sensor Technology for Monitoring of Health-Related Conditions
- Abstract
- Part I Spectroscopic Analysis Technique Based on Photoplethysmogram Signal
- References
- Part II Spectroscopic Analysis Technique Based on Bioimpedance Modulation
- References
- 13.17. Developments of Laser Fabrication Methods for Lab-on-a-Chip Microfluidic Multisensing Devices
- Abstract
- Acknowledgments
- 13.17.1 Introduction
- 13.17.2 Common Materials Employed in the Fabrication of Microfluidic Devices
- 13.17.3 Standard Fabrication Methods for Microfluidic Devices
- 13.17.4 Laser Precision Engineering of Microfluidic Channels
- 13.17.5 Concluding Remarks
- References
- 13.18. Sensor Technology for a Safe and Smart Living Environment for the Aged and Infirm at Home
- Abstract
- 13.18.1 Introduction to Smart Environments
- 13.18.2 Assistive Technologies
- 13.18.3 Device Interoperability
- 13.18.4 Data Processing
- 13.18.5 Smart Environments and Ambient-Assisted Living
- 13.18.6 Concluding Remarks
- References
- 13.19. Sensor-Controlled Intelligent Vehicle Systems: Demand and Needs for a Global Automotive Landscape
- Abstract
- 13.19.1 Introduction to Sensor-Controlled Intelligent Systems in Automotive Vehicles
- 13.19.2 Sensor-Based Fuzzy Logic Expert System Models
- 13.19.3 Application of Fuzzy Logic Expert Systems
- 13.19.4 Conclusion
- References
- 13.20. Technical and Economic Feasibility of Sensor Technology for Health/Environmental Condition Monitoring
- Abstract
- 13.20.1 Introduction
- 13.20.2 Health Condition Monitoring
- 13.20.3 Environmental Condition Monitoring
- 13.20.4 Concluding Remarks
- See also
- References
- 13.21. Multimodal Sensing by a Vision-Based Tactile Sensor Using a Deformable Touchpad
- Abstract
- 13.21.1 Introduction
- 13.21.2 Vision-Based Tactile Sensor
- 13.21.3 Sensing Method of Tactile Information
- 13.21.4 Experimental Results
- 13.21.5 Discussion and Future Work
- References
- 13.22. Review of Sensor Applications in Tool Condition Monitoring in Machining
- Abstract
- Acknowledgments
- 13.22.1 Introduction
- 13.22.2 Factors Monitored during TCM
- 13.22.3 Sensor-Based TCM
- 13.22.4 Concluding Remarks and Challenges
- References
- 13.23. Review of the Reliability and Connectivity of Wireless Sensor Technology
- Abstract
- 13.23.1 Introduction
- 13.23.2 Sensors
- 13.23.3 Wireless Sensor Networks
- 13.23.4 Internal Infrastructure of Wireless Sensor Networks
- 13.23.5 Networking System and Connectivity
- 13.23.6 Communication Protocols and Their Reliability
- 13.23.7 Future Research Contribution Issues in WSNs
- 13.23.8 Concluding Remarks
- See also
- References
- 13.01. Introduction to Sensor Materials, Technologies and Applications
- Index
- Authors
- Edition: 1
- Published: September 12, 2014
- Language: English
MH
M.S.J. Hashmi
Saleem Hashmi PhD, DSc., CEng, FIEI, FIMechE is Emeritus Professor in the School of Mechanical & Manufacturing Engineering at Dublin City University, Ireland. He founded the School in January 1987, in addition to setting up the Material Processing Research Centre (MPRC), a research centre of excellence in the field of material processing. In 1990, Professor Hashmi established Advances in Materials and Processing Technologies (AMPT), a much-needed international conference in materials processing. He continues to be the chairperson of the Steering Committee for this series of conferences. In 1998 he was appointed as editor-in-chief of Elsevier Journal of Material Processing Technology and continued in this role until 2008. In 1995, Professor Hashmi was awarded the higher doctorate degree of DSc, by the University of Manchester, the highest academic degree any university in the UK can award. Professor Hashmi has supervised or co-supervised 110 PhD and 55 MEng research students to successful completion. Over the years he has also acted as an external examiner and expert assessor for PhD candidates and engineering departments with universities in Ireland, the UK, India, Pakistan, Bangladesh, Hong Kong, Canada, Australia, and Malaysia. He has published in excess of 430 papers and 12 books so far. He has been Editor-in-Chief on two MRWs with Elsevier, Comprehensive Materials Finishing and Comprehensive Materials Processing.
Affiliations and expertise
Emeritus Professor, School of Mechanical and Manufacturing Engineering, Dublin City University, IrelandRead Comprehensive Materials Processing on ScienceDirect