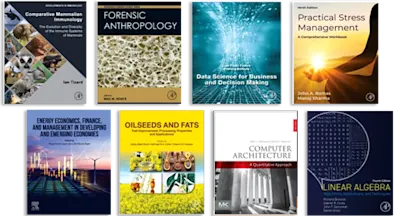
Chemical Process Safety
Learning from Case Histories
- 4th Edition - August 11, 2015
- Imprint: Butterworth-Heinemann
- Author: Roy E. Sanders
- Language: English
- Paperback ISBN:9 7 8 - 0 - 1 2 - 8 0 4 4 2 8 - 5
- Hardback ISBN:9 7 8 - 0 - 1 2 - 8 0 1 4 2 5 - 7
- eBook ISBN:9 7 8 - 0 - 1 2 - 8 0 1 6 6 7 - 1
Chemical Process Safety: Learning from Case Histories, Fourth Edition gives insight into eliminating specific classes of hazards while also providing real case histories with valu… Read more
Purchase options
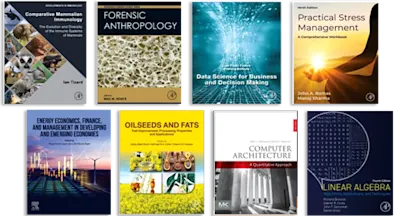
Chemical Process Safety: Learning from Case Histories, Fourth Edition
gives insight into eliminating specific classes of hazards while also providing real case histories with valuable lessons to be learned. This edition also includes practical sections on mechanical integrity, management of change, and incident investigation programs, along with a list of helpful resources.The information contained in this book will help users stay up-to-date on all the latest OSHA requirements, including the OSHA-required Management of Change, Mechanical Integrity, and Incident Investigation regulations. Learn how to eliminate hazards in the design, operation, and maintenance of chemical process plants and petroleum refineries.
World-renowned expert in process safety, Roy Sanders, shows how to reduce risks in plants and refineries, including a summary of case histories from high profile disasters and recommendations for how to avoid repeating the same mistakes. Following the principles outlined in this text will help save lives and reduce loss.
- Features additional new chapters covering safety culture, maintaining a sense of vulnerability, and additional learning opportunities from recent incidents and near misses
- Contains updated information from the US Bureau of Labor Statistics and the National Safety Council, with concise summaries of some of the most important case histories of the twenty-first century
- Includes significantly expanded information from the US Chemical Safety Board, US OSHA, American Institute of Chemical Engineers, and the UK Health and Safety Executive (HSE)
- Provides a completely updated chapter to guide readers to a wealth of reference material available on the web and elsewhere
Employees of the chemical manufacturing industries, petroleum refineries, specialty chemical industries, engineering companies and consultants who serve the chemical and petroleum industries, and academics interested in including process safety into their curriculums.
- Preface
- Acknowledgments
- 1: Perspective, perspective, perspective
- Abstract
- Introduction
- The media rarely focuses on the benefits of the chemical industry
- A glance at the history of chemical manufacturing before the industrial revolution
- The modern industrial chemical industry modifies our way of living
- Risks are not necessarily how they are perceived
- Natural pesticides
- Plant employee safety versus life-style choices
- The chemical industry’s excellent safety record
- Who has the most dangerous jobs?
- What events resulted in fatal occupational injuries in 2012?
- Just how dangerous is it to work in a US chemical plant?
- How are the chemical and refinery industries doing today when it comes to major losses? And what should we do in the future?
- Process safety culture
- 2: Good intentions
- Abstract
- Modifications made with good intentions
- A tank truck catastrophically fails
- Siphoning destroys a tender tank
- Tank roof splits from overfilling
- A well-intended change yields a storage tank collapse
- A water drain line is altered and a reactor explodes
- An air system is improved and a vessel blows up
- A new air system improved economics, but jeopardized safety
- Another incident with nitrogen backup for a compressed air supply
- The hazards of nitrogen asphyxiation
- Concerns for safety on a refrigerated ethylene tank
- Beware of impurities, stabilizers, or substitute chemicals
- Good intentions on certain new protection systems lead to troubles
- A gas compressor is protected from dirt, but the plant catches fire
- A replacement check valve installed – one detail overlooked
- What was one of the immediate causes of the fire?
- What did investigators recommend?
- Another good intentions project: new tanks are destroyed and the neighborhood is disrupted
- Another tragic incident involving hydrogen sulfide takes the lives of two workers
- Closing thoughts on sewers
- Carbon absorption incidents show history repeats
- The lighter side
- A review of good intentions
- 3: Focusing on water and steam: the ever-present and sometimes evil twins
- Abstract
- Hydro-test goes awry
- A flooded column collapses as water is being drained from the system
- Water reacting with strong chemicals
- Easy-to-use steam heat can push equipment beyond safe design limits
- Heating water in a confined system
- Steam condenses and a mega-vessel is destroyed during commissioning
- A tragedy develops when hot oil is pumped upon a layer of water
- Discussion and recommendations
- 4: Major US incidents in the twenty-first century: Some folks thirst for recent case histories
- Abstract
- Unfortunately – there is often a certain sameness in process incidents
- Delaware City, Delaware, incident
- Rouseville, Pennsylvania, incident
- Buffalo, New York, incident
- Learning opportunities from major incidents in the twenty-first century
- President Obama signs an Executive Order relating to process safety management
- An explosion in a plastics manufacturing facility in Illinois results in five deaths, plant closure and eventual tear down of the facility
- A glimpse of the PVC plastic facility, the loss of life and property
- PVC reactor layout and most likely incident scenario
- Not learning from incidents
- Key findings on the Illiopolis PVC plant incident
- The CSB recommendations submitted to Formosa Plastics USA [8]
- The March 2005 Texas City, Texas, refinery incident – the most tragic US refinery accident of the decade
- Besides poor safety culture – what happened prior to the release?
- What happened immediately after the release?
- Besides poor safety culture – what are some key technical findings of the Chemical Safety Board?
- Besides poor safety culture – what are some key organizational findings of the Chemical Safety Board?
- BP shares their investigation findings on key issues
- BP Texas City violations and settlement agreements
- An independent blue ribbon panel investigates BP’s North American operations
- A foreword on the findings published by the Baker Panel – broadens the impact
- The summary of the Baker Panel findings
- Corporate safety culture
- Refinery tragedy in Anacortes, Washington
- Introduction to the Anacortes refinery incident
- Details on the Tesoro refinery incident
- Why the catastrophic rupture? The technical focus
- Other Chemical Safety Board findings
- The CSB video “Tesoro Tragedy – Behind the Curve”
- CSB sweeping game changing recommendations for the US environmental agency
- CSB recommendations for the State of Washington
- CSB recommendations for the American Petroleum Institute
- The Washington Department of Labor and Industries issues citations
- Ammonium nitrate catastrophe in West, Texas April 17, 2013 – fifteen perish
- Major incidents in the twenty-first century
- 5: Two highly destructive twenty-first century vapor cloud explosions: one in the United Kingdom and the other in Venezuela: Two massive explosion incidents with some significant similarities
- Abstract
- Buncefield UK fuel storage and transfer depot explosion and fires 2005
- Introduction to the Buncefield incident and impact in the area
- A look at some details prior to the explosion and massive fire
- The economic costs of the Buncefield incident
- Fuel concerns after the explosion and fires
- Instrumentation and control systems
- Buncefield report recommendations
- Recommendations for design and operation of fuel storage sites
- Summary comments on the Buncefield incident
- A catastrophic explosion at Amuay refinery in Venezuela
- Immediate events leading up to the explosion
- A closer look a details at the Amuay refinery incident
- Petroleos de Venezuela (or PDVSA) leak source study
- RMG presented their view promptly after the incident
- “The Economist” speaks to some underlying issues
- The Manufacturing Center in Energy orientation (COENER) report
- One strongly critical media report speaks about the Amuay refinery operations
- The Amuay refinery based upon an insurance report
- Blunt recommendations by the Manufacturing Center in Energy
- Conclusions and recommendations for the Amuay disaster
- Vapor cloud explosions – closing comments
- When it comes to vapor clouds what can you do?
- 6: Preparation for maintenance
- Abstract
- Some problems when preparing for maintenance
- A tank vent is routed to a water-filled drum to “Avoid” problems
- Preparing to paint large tanks
- Preparing a brine sludge dissolving system for maintenance
- What happened in the brine system?
- A violent eruption from a tank being prepared for maintenance
- An explosion while preparing to replace a valve in an ice cream plant
- A chemical cleaning operation kills sparrows, but improves procedures
- Other cleaning, washing, steaming, and purging operations
- A tragedy when preparing for valve maintenance
- A review of changes made to prepare for maintenance
- 7: Maintenance-induced accidents and process piping problems
- Abstract
- Planning and communication
- Repaired reboiler passes the hydro-test and later creates a fire
- A tank explodes during welding repairs after passing a flammable gas test
- A phenol tank’s roof lifts as repairs are made
- Catastrophic failures of storage tanks as reported by the Environmental Protection Agency
- Hot work on tank catwalk results in a contractor’s death, injuries, and a costly off-site environmental insult
- Sulfuric acid tank background basics
- Unsafe condition report and hot work permit shortcomings
- The management of change shortcomings in sulfuric acid tank incident
- Root causes as defined by the CSB
- Similar tragic incidents involving hot work to tanks provided within the CSB full report Delaware City
- The Chemical Safety Board offers safety advice on Hot Work within a 14 min video
- Another tank explosion during maintenance hot work
- Repair activity to a piping spool results in a massive leak from a sphere
- The Phillips 66 incident: tragedy in Pasadena, Texas
- A massive fire, BLEVEs, and $5 million damages after a mechanic improperly removes a valve actuator
- Misdirected precautions on a reactor system isolation plug valve result in a vapor cloud explosion
- A hidden blind surprises the operators
- Poor judgment by mechanics allowed a bad steam leak to result in a minor explosion
- The Flixborough disaster and the lessons we should never forget
- Do piping systems contribute to major accidents?
- Beware of other piping issues
- Specific piping system problems reported as major incidents
- Four case histories of catastrophic pipe failures
- An 8-in. pipeline ruptures and an explosion occurs – December 24, 1989
- Piping problems review
- Concluding thoughts on maintenance – induced accidents and process piping problems
- 8: One-minute modifications: small, quick changes in a plant can create bad memories
- Abstract
- Explosion occurs after an analyzer is repaired
- When cooling methods were changed, a tragedy occurred
- Instrument air backup is disconnected
- A furnace temperature safeguard is altered
- It appeared to be icicles hanging in a small plant
- Another costly gasket error
- While compressed asbestos gaskets are phased out, other leaks will occur
- Other piping gasket substitution problems
- New stud bolts fail unexpectedly
- A “Repaired” hose fails triggering a major fire
- Hurricane procedures are improperly applied to a tank conservation vent lid
- Painters create troubles
- Pipefitters can create troubles when reinstalling relief valves
- Another pipefitter’s error
- Lack of respect for an open vent as a vacuum-relief device results in a partial tank collapse
- Just a bucket of water destroys a tank
- Lack of respect for an open vent as a pressure-relief device costs two lives
- One-minute modifications review
- 9: Accidents involving compressors, hoses, and pumps
- Abstract
- Reciprocating compressors
- A piece of compressor water jacket is launched
- The misuse of hoses can quickly create problems
- The Chemical Safety Board investigates a chlorine unloading hose failure
- The Chemical Safety Board investigated a phosgene hose failure with a fatality
- Fatality from a ruptured hose in HF service
- Hose mishaps frequently lead to loss of containment – maybe more than we think
- The water hose at the Flixborough disaster
- Hoses used to warm equipment
- Three-Mile Island Incident involved a hose
- The Bhopal Tragedy was initiated by use of a hose
- Improper purge hose set up for maintenance creates major problems
- High-pressure hydrogen inadvertently backs into the nitrogen system and an explosion occurs
- A nitric acid delivery to the wrong tank makes front-page news
- How do you prevent such an incident?
- Other truck delivery incidents
- An operator averts a sulfuric acid unloading tragedy
- Hoses cannot take excessive abuse
- What is the advice from practitioners?
- Centrifugal pumps
- River water pump piping explodes
- Severe pump explosions surprise employees
- A large condensate pump explodes
- Closing thoughts on pump explosions. Courtesy of the “Beacon”
- Afterthoughts
- 10: Failure to use, consult, or understand specifications
- Abstract
- Lack of well-defined, rigid operating instructions cost $100,000 in property damages
- Other thoughts on fired heaters
- Low-pressure tank fabrication specifications were not followed
- Explosion relief for low-pressure tanks
- Tinkering with pressured vessel-closure bolts ends with a harmless bang
- Piping specifications were not utilized
- Pump repairs potentially endanger the plant, but are corrected in time to prevent newspaper headlines
- Plastic pumps installed to pump flammable liquids
- Weak walls wanted – but alternate attachments contributed to the damage
- 11: “Imagine If” modifications and practical problem solving
- Abstract
- “Imagine If” modifications – let us not exaggerate the dangers as we perform safety studies
- New fire-fighting agent meets opposition – “Could Kill Men as Well as Fires”
- A process safety management quiz
- New fiber production methods questioned
- Practical problem solving
- The physics student and his mischievous methods
- 12: The role of mechanical integrity in chemical process safety
- Abstract
- Mechanical integrity in a chemical plant
- A regulatory view of mechanical integrity
- Mechanical integrity programs must be tailored to the specific site
- Mechanical integrity in design and installation
- Equipment covered by mechanical integrity
- Regulatory enforcement of mechanical integrity
- What is all this about RAGAGEP?
- Struggling with mechanical integrity
- Written procedures and training
- Classification of equipment by hazard potential
- Mechanical integrity programs for pumps/compressors
- Mechanical integrity programs for piping, pressure vessels, storage tanks, and process piping
- Inspecting pressure vessels, storage tanks, and piping
- Inspection of pressure vessels and storage tanks
- Mechanical programs for safety-critical instruments and safety relief valves
- The critical role of safety relief valves
- “In-house” testing safety relief valves
- Mechanical integrity program for process safety interlocks and alarms
- Protective process safety interlocks at a DuPont plant
- Another company – a different emphasis on safety critical instrument systems
- Another approach – prooftesting at a Louisiana plant
- Additional information on mechanical integrity
- 13: Effectively managing change within the chemical industry
- Abstract
- Introduction
- Preliminary thoughts on managing change
- Are management of change systems like snowflakes?
- A reality check provided by previous chapters
- Keeping MOC systems simple
- Losing tribal knowledge
- Some historical approaches to plant changes
- The US OSHA PSM Standard addresses “management of change”
- Principles of an effective management of change system that prevents uncontrolled change and satisfies OSHA
- An overall process description to create or improve a management of change system
- Clear definitions are imperative
- Key steps for an effective management of change system for a medium or large organization
- Key steps for an effective management of change system for a small company
- Multidisciplined committee can provide an in-depth look when identifying hazards
- Operational variances for maintenance need a close examination too
- Variances, exceptions, and special cases of change
- Should the MOC system be paperless?
- Over two dozen plants share their MOC practices
- Management of change approvals, documentation, and auditing
- Closing thoughts on management of change policy
- The Center for Chemical Process Safety
- Recommendations and regulations after 1988
- 14: Investigating and sharing near misses and unfortunate accidents
- Abstract
- Introduction
- What does the regulation say about incident investigations?
- Plant cultures can affect investigations
- More guidelines on the culture of incident reporting
- An OSHA program coordinator’s view
- Layers of incident causes
- A furnace tube failure case history is revisited
- Process safety incident investigation techniques
- Applying root cause analysis
- Some chemical manufacturers’ approaches to incident investigation
- What is a root cause?
- STAMP – a new accident causality model
- Some thoughts on process safety incident investigation techniques
- Complying with the OSHA element on incident investigation
- Report approval, report distribution, sharing the findings, corrective action tracking, and report retention
- Conclusions
- 15: Keep a sense of vulnerability for safety sake: seven recommendations for keeping a sense of vulnerability at your chemical processing or refining site
- Abstract
- Opening thoughts on unease and who should it impact
- How do you create a sense of unease or vulnerability?
- A focused effort is essential
- Success can blind us of reality
- Seven recommendations to reduce your vulnerability
- Why not step back in time?
- 16: A strong safety culture is essential: it is essential to develop a strong safety culture
- Abstract
- Process safety culture has been recognized and accepted in recent years
- Foundation for development of safety culture
- About 65 companies shared to shape the earlier definition of “Safety Culture” in 2003
- What is process safety culture? Perhaps – it is the root cause of the decade!
- A dozen features essential to developing a durable safety culture within PSM
- API RP 754 describes the “Purpose of Indicators” as [17]
- Is safety culture really important?
- 17: Sources of helpful information for practicing chemical process safety
- Abstract
- Key cost free process safety resources at your finger tips
- Process safety resources via consultants, professional associations and trade associations via the web
- Excellent books addressing chemical process safety – from a process engineer’s viewpoint
- Two of the best process safety videos which focus on learning from case histories
- Index
- Edition: 4
- Published: August 11, 2015
- Imprint: Butterworth-Heinemann
- Language: English
RS