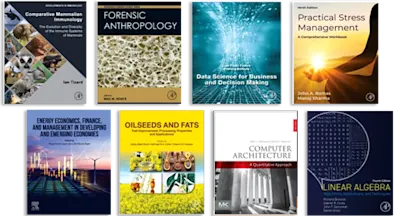
Chemical Engineering Design
Principles, Practice and Economics of Plant and Process Design
- 3rd Edition - September 13, 2021
- Imprint: Butterworth-Heinemann
- Authors: Gavin Towler, Ray Sinnott
- Language: English
- Paperback ISBN:9 7 8 - 0 - 1 2 - 8 2 1 1 7 9 - 3
- eBook ISBN:9 7 8 - 0 - 3 2 3 - 8 5 0 4 8 - 3
Chemical Engineering Design: Principles, Practice and Economics of Plant and Process Design is one of the best-known and most widely adopted texts available for students of chemic… Read more
Purchase options
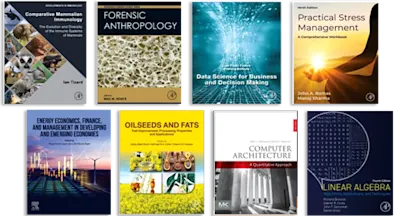
- Provides students with a text of unmatched relevance for chemical process and plant design courses and for the final year capstone design course
- Written by practicing design engineers with extensive undergraduate teaching experience
- Contains more than 100 typical industrial design projects drawn from a diverse range of process industries
NEW TO THIS EDITION
- Includes new content covering food, pharmaceutical and biological processes and commonly used unit operations
- Provides updates on plant and equipment costs, regulations and technical standards
- Includes limited online access for students to Cost Engineering’s Cleopatra Enterprise cost estimating software
Part I: Process Design
1. Introduction to Design
2. Process Flowsheet Development
3. Utilities and Energy Efficient Design
4. Process Simulation
5. Instrumentation and Process Control
6. Materials of Construction
7. Capital Cost Estimating
8. Estimating Revenues and Production Costs
9. Economic Evaluation of Projects
10. Safety and Loss Prevention
11. General Site Considerations
12. Optimization in Design
Part II: Plant Design
13. Equipment Selection, Specification and Design
14. Design of Pressure Vessels
15. Design of Reactors and Mixers
16. Separation of Fluids
17. Separation Columns (Distillation, Absorption and Extraction)
18. Specification and Design of Solids-Handling Equipment
19. Heat Transfer Equipment
20. Transport and Storage of Fluids
- Edition: 3
- Published: September 13, 2021
- Imprint: Butterworth-Heinemann
- Language: English
GT
Gavin Towler
Gavin has 20 years of broad experience of process and product design and has 65 US patents. He is co-author of “Chemical Engineering Design”, a textbook on process design, and is an Adjunct Professor at Northwestern University, where he teaches the senior design classes.
Gavin has a B.A. and M.Eng. in chemical engineering from Cambridge University and a Ph.D. from U.C. Berkeley. He is a Chartered Engineer and Fellow of the Institute of Chemical Engineers, and is a Fellow of the AIChE.
RS
Ray Sinnott
After his career in industry he joined the Chemical Engineering Department, University of Wales Swansea in 1970, specialising in teaching process and plant design, and other engineering practice subjects.
The first edition of Chemical Engineering Design (Coulson and Richardson’s Vol 6) was published in 1983. Subsequent editions have been published at approximately 5 year intervals.
Ray Sinnott retired from full time teaching in 1995 but has maintained close contact with the engineering profession.