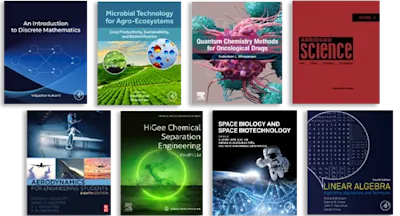
Cemented Paste Backfill
Thickening, Transport and Mechanical Properties
- 1st Edition - May 22, 2024
- Authors: Yong Wang, Bolin Xiao
- Language: English
- Paperback ISBN:9 7 8 - 0 - 4 4 3 - 1 6 0 5 4 - 7
- eBook ISBN:9 7 8 - 0 - 4 4 3 - 1 6 0 5 5 - 4
Cemented Paste Backfill: Thickening, Transport and Mechanical Properties covers a wide range of topics, including a new definition of CPB, past participation and flow-indu… Read more
Purchase options
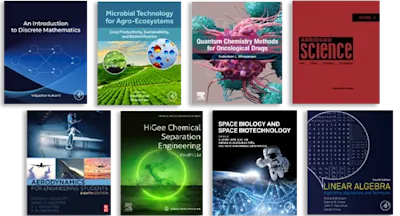
Cemented Paste Backfill: Thickening, Transport and Mechanical Properties covers a wide range of topics, including a new definition of CPB, past participation and flow-induced corrosion of pipeline under the constant temperature condition, multiphysics processes in CPB and the associated consolidation process, the variation of rheological parameters and transport resistance, prediction model for rheological properties, mechanical behavior and properties of CPB and fiber-reinforced CPB, and control technology to reduce the adverse effect of temperature.
- Investigates rheological properties and multiphysics processes in CPB materials around the world
- Looks into systematic studies on pipe transport and mechanical properties of CPB under temperature effects
- Focuses mainly on the effect of temperature on paste transport and mechanical properties under the temperature effect, which provides a theoretical basis for safe and efficient filling operation and associated future research in this field
- Offer in-depth insights into the evolution of the rheological and mechanical properties of CPB under the effect of temperatures
About the authors
Foreword
About this book
1 Introducing cemented paste backfill (CPB) technology
1.1 Benefits and development of CPB technology
1.1.1 Benefits of CPB
1.1.2 Developments of CPB technology
1.2 Workflow and basic concepts of CPB process
1.2.1 Workflow of CPB
1.2.2 Basic concepts of CPB
1.3 Scope of the book
2 Definition of cemented paste backfill
2.1 Definition of CPB from the perspective of saturation rate and
bleeding rate
2.1.1 CPB saturation rate
2.1.2 CPB bleeding rate
2.1.3 Verification of the CPB definition in Huize lead-zinc mine
case
2.2 Improving the definition of CPB from the perspective of yield
stress
2.2.1 Experimental equipment and methods
2.2.2 Definition of CPB from yield stress
2.2.3 Paste definition validation
2.3 Detailed CPB definition through CPB properties
3 Theory, experiment, and equipment in tailings thickening process
3.1 Trends and challenges in tailings thickening
3.1.1 Research on tailings thickening
3.1.2 Research progress and direction
3.2 Experimental investigation on dewatering performance and torque
evolution in thickening
3.2.1 Introduction
3.2.2 Experimental design
3.2.3 Evolution of concentration of tailings suspension at various
thickening times
3.2.4 Evolution of shear stress and torque during the dynamic
dewatering
3.2.5 Simultaneous evolution of solid mass fraction and torque
at various thickening times
3.2.6 Implication for the DCT operation and design
3.2.7 Conclusions
3.3 Predicting model of the yield stress for thickened tailings 40
3.3.1 Materials and methods
3.3.2 Yield stress
3.3.3 TBC model
3.3.4 Simultaneous effect of saturation degree and solid
concentration on yield stress
3.3.5 Effects of true solid density, bulk density, and solid
concentration on yield stress
3.3.6 Effect of porosity (n) on the yield stress (s0) of thickened
tailings
3.3.7 Effect of volume fraction (4) on the yield stress (s0) of
thickened tailings
3.3.8 Conclusion
3.4 Mechanism and influencing factor of rake blockage in deep cone
thickener
3.4.1 Theory and model
3.4.2 The effect of friction coefficient
3.4.3 The effect of density of stacking mud bed
3.4.4 The corrective and improvement measures for rake blockage
3.5 Conclusions
4 Transport and rheological properties of cemented paste backfill (CPB)
4.1 Rheological and sedimentation properties of CPB
4.1.1 Materials and testing methods
4.1.2 Rheological theoretical models
4.1.3 Evolution of shear stress-shear rate curve
4.1.4 Evolution of apparent viscosity-shear time curve
4.1.5 Sedimentation property of backfilling material
4.1.6 Classification method of sedimentation for backfill material
4.1.7 Sedimentation property of backfilling material from the
viewpoint of yield stress
4.1.8 Conclusions
4.2 Temperature effects on CPB rheological properties
4.2.1 Experimental program
4.2.2 Effect of temperature on shear stress and apparent viscosity
4.2.3 Effect of temperature on shear stress
4.2.4 Bingham model and temperature analysis
4.2.5 Conclusions
4.3 Investigating the effect of solid components on yield stress for
cemented paste backfill via uniform design
4.3.1 Introduction of yield stress in CPB
4.3.2 Uniform design of the yield stress test
4.3.3 Evolution of shear stress-shear rate curve and
HerscheleBulkley yield stress regression
4.3.4 Effect of solid components on yield stress of CPB
4.3.5 Analysis of influence mechanism of solid components
on yield stress of paste
4.4 Estimating the CPB pipeline pressure drop through semiindustrial
L-shape pipe flow test
4.4.1 Introduction
4.4.2 Engineering background and methodology
4.4.3 Field test and results
4.4.4 Analysis and discussion
4.4.5 Industrial test verification
4.4.6 Conclusion
4.5 Quantitative evaluating CPB pipeline wear resistance
4.5.1 Materials and preparation of the test
4.5.2 In-door pipeline loop flow wear test
4.5.3 Wear characteristics under different slurry conditions
4.5.4 Pipeline wear mathematical model
4.5.5 The mechanism of the solid particles
4.6 Quantitative test and engineering application of wear resistance
4.6.1 Pipeline wear resistance test device and methods
4.6.2 Results of the wear test
4.6.3 Engineering application verification
5 Mechanical properties of hardening cemented paste backfill (CPB)
5.1 Hardened CPB mechanical property and its influencing factors
5.2 Effect of mixing proportion on CPB mechanical properties
5.2.1 Materials and method
5.2.2 Strength versus binder content
5.2.3 Strength versus solid mass concentration
5.2.4 Strength versus coarse/fine tailings ratio
5.3 Effect of binder type and water chemistry on CPB properties
5.3.1 Testing materials and methods
5.3.2 Effects of cement type and water quality on paste slump
performance
5.3.3 Effects of cement type and water quality on paste coagulation
performance
5.3.4 Effects of cement type and water quality on paste UCS
performance
5.4 Effects of initial temperature on CPB deformation behavior 155
5.4.1 Experiments and apparatus
5.4.2 Effect of initial temperature on the stress-strain behavior
of CPB
5.4.3 Effect of initial temperature on the modulus of elasticity
E of CPB
5.4.4 Relationship between the strength and modulus of elasticity
of CPB
5.4.5 Evolution of the modulus of elasticity with hydration degree
of the binder
5.4.6 Conclusions
5.5 Effect of curing humidity on the mechanical properties of CPB 166
5.5.1 Materials and methods
5.5.2 Effect of curing humidity on the deformation characteristics
of CPB
5.5.3 Effect of curing humidity on the evolution of the physical
and mechanical properties of the CPB
5.5.4 BP neural network predicts the variation law of CPB
strength
5.6 External sulfate attack on the CPB mechanical behavior
5.6.1 Materials and methods
5.6.2 Evolutive compression behavior of CPB under external
sulfate attack
5.6.3 Effect of sulfate concentration on the compression behavior
of CPB
5.6.4 Effect of external sulfate attack on the elastic modulus
of CPB
5.6.5 Neural model for predicting UCS of CPB under external
sulfate attack
5.7 Conclusions
6 Coupling effects during the cemented paste backfill (CPB) hardening
process
6.1 Couplings of thermo-hydromechanical-chemical (THMC)
development of the CPB
6.1.1 Introduction
6.1.2 Experimental study on the multifield performance of CPB
6.1.3 In situ multifield performance mathematical model
6.1.4 Application of the in situ performance simulation
6.1.5 Future perspectives of THMC
6.2 Correlation between hydraulic and mechanical properties of
the CPB
6.2.1 Experimental program
6.2.2 Simultaneous evolution of hydraulic-mechanics properties in
cemented paste backfill
6.2.3 Correlative mechanism of hydraulic-mechanics behavior for
cemented paste backfill
6.2.4 Relationship between hydration reaction rate and volumetric
water content
6.2.5 Relationship between suction and volumetric water content
6.2.6 Prediction model for UCS based on the suction of cemented
paste backfill
6.3 Isothermal multiphysics processes in CPB
6.3.1 Materials and experimental design
6.3.2 Evolution of CPB strength with curing time
6.3.3 Evolution of CPB strength with the cement-to-tailings ratio
6.3.4 Evolution of multiphysics processes of CPB with different
cement-to-tailings ratios
6.3.5 Correlation analysis of isothermal multiphysics processes in
CPB
6.3.6 Quantitative analysis of CPB strength
6.3.7 Conclusion
6.4 In situ monitoring of the CPB performance for real-stope
6.4.1 Introduction
6.4.2 Materials, sensors, and physical scaled model
6.4.3 Field measurement of in situ properties of tailings backfill
6.4.4 Similar simulation results
6.4.5 Field monitoring results of in situ properties of tailings
backfill
6.4.6 Comparison between results of similar simulation and field
monitoring
6.4.7 Prediction model of fluidesolid transition based on pore
water pressure
6.4.8 Conclusions
7 Green backfilling materials for cemented paste backfill (CPB)
7.1 Ultrafine tailings and its grading characterization
7.1.1 Particle size distribution background
7.1.2 Model and algorithm
7.1.3 Statistics of the compressed PSD code
7.1.4 PSD code at classification scenario
7.1.5 Application
7.2 Backfill binder using blast furnace slag and application
7.2.1 Background on binders and blast furnace slag
7.2.2 Materials and methods
7.2.3 Strength (UCS) development of the HDB with different
binder agents
7.2.4 Rheological properties of the HDB
7.2.5 Conclusions
7.3 Backfill binder using steel slag and application
7.3.1 Introduction of steel slag
7.3.2 Materials, methodology, and mixing proportion 308
7.3.3 SSB hydration mechanism
7.3.4 Mechanical and rheological properties of the SSB-CPB
7.3.5 Conclusion
7.4 Cost saving for CPB that considering the green binders
7.4.1 Experimental programs
7.4.2 Hydration properties of the binder
7.4.3 Properties of the SSB-CPB
7.4.4 SSB cost analysis
7.4.5 Prospects of SSB-CPB with high volumetric steel slag
7.5 Conclusions
8 Future perspectives of cemented paste backfill (CPB)
8.1 Rheology theories for CPB technology
8.2 Green and low-cost filling material
8.3 Automatic and intelligent CPB systems
- Edition: 1
- Published: May 22, 2024
- Language: English
YW
Yong Wang
BX