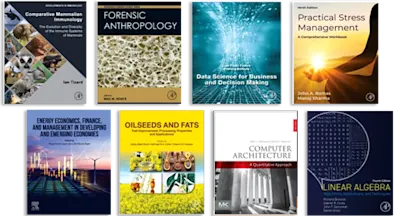
CAPA in the Pharmaceutical and Biotech Industries
How to Implement an Effective Nine Step Program
- 1st Edition - December 11, 2015
- Imprint: Woodhead Publishing
- Author: J Rodriguez
- Language: English
- Hardback ISBN:9 7 8 - 1 - 9 0 7 5 6 8 - 5 8 - 9
- eBook ISBN:9 7 8 - 1 - 9 0 8 8 1 8 - 3 7 - 9
CAPA in the Pharmaceutical and Biotech Industries: How to Implement an Effective Nine Step Program contains the most current information on how to implement, develop, and maint… Read more
Purchase options
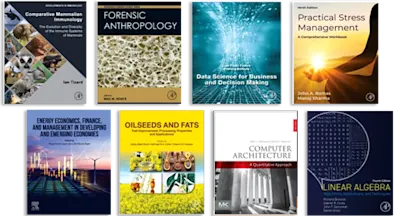
CAPA in the Pharmaceutical and Biotech Industries: How to Implement an Effective Nine Step Program
contains the most current information on how to implement, develop, and maintain an effective Corrective Action and Preventive Action (CAPA) and investigation program using a nine step closed-loop process approach for medical devices and pharmaceutical and biologic manufacturers, as well as any anyone who has to maintain a quality system.This book addresses how companies often make the mistake of fixing problems in their processes by revising procedures or, more commonly, by retraining employees that may or may not have caused the problem. This event-focused fix leads to the false assumption that the errors have been eradicated and will be prevented in the future. The reality is that the causes of the failure were never actually determined, therefore the same problem will recur over and over. CAPA is a complete system that collects information regarding existing and potential quality problems. It analyzes and investigates the issues to identify the root cause of nonconformities. It is not just a quick-fix, simple approach, it is a process and has to be understood throughout organizations.- Provides an understanding of the principles and techniques involved in the effective implementation of a CAPA program, from the identification of the problem, to the verification of preventive action
- Emphasis is placed on the practical aspects of how to perform failure investigations and root cause analysis through the use of several types of methodologies, all explained in detail
- Provides effective methods to use with a Corrective Action system to help quality professionals identify costly issues and resolve them quickly and appropriately
1. Understanding the FDA’s CAPA requirements and regulations
- Part I. 21 CFR part 820.100 for medical devices
- Part II. 21 CFR Part 211: current good manufacturing practice for finished pharmaceuticals
- Part III. The FDA’s current inspectional approaches
- Part IV. QSIT and CAPA: inspectional objectives
- Part V. Quality systems approach to pharmaceutical current good manufacturing practice regulation, September 2006
- Part VI. ISO 13485 and CAPA: inspectional objectives
- Summary to part VI
2. Implementing a CAPA program: Going back to basics
- Corrective and preventive actions
- General requirements
- CAPA process
- Correction/remedial action
- Evaluation of risk
- CAPA process metrics
- Closed-loop corrective action
3. The nine-step CAPA program
- The nine-step process
4. Step 1: identification of the event and writing a proper problem statement
- Write a detailed problem statement
- Use the “Ws” and “Hs”
- Step 1: identification of the problem and effective compliance writing
- Scenario 1
- Scenario 2
- Root cause analysis: methods, whys, and the fishbone diagram
- Understanding the problem statement and the evaluation of the event
- Seeking quality data
- Document the problem
- Explanation of the problem
- Evidence
- Evaluation
- More on report writing
- Summary
5. Step 2: risk assessment and impact assessment
- Why include risk analysis in CAPA programs?
- What it means to integrate risk analysis into CAPA
- Evaluation
- Assessment of risk
- Risk-management process
- The level of investigations, and the extent of corrective and preventive actions
- Some important definitions related to risk
- Maintenance of risk-analysis results/worksheets/forms
- Summary
6. Step 3: evaluate event and initiate remedial actions (correction)
- Part I. Internal corrections
- Part II. Corrections and removals (external corrections)
- Responsibilities
- General requirements
- Recalled/recovered product disposition
- FDA reportable field action
- Nonreportable field actions
7. Step 4: data gathering and analysis
- Potential causes and data collection and analysis
- Data, quality indicators, and triggers
- Levels of reviews
- Data collection should be planned as follows
- Data analysis and the investigation process
- Data collection
- Potential causes and data collection and analysis
- Results and data
- CAPA system data collection and analysis
- The general process for data collection and analysis
- CAPA system review
- Problem analysis
- Improvement
- Investigation process metrics
- Closed loop corrective action
8. Step 5: investigation
- When investigation is needed
- Information may not be completely accurate or reliable
- Responsibilities/resources
- Internal data sources
- External data sources
- Introduction of the investigation process
- Investigation initiation
- Investigation owner and team designation
- Team constitution
- Investigation methodologies definition/selection
- Investigation plan elaboration
- Investigation plan approval
- Execution of the investigation
- Potential causes and data collection and analysis
- Results and data
- Problem analysis
- Investigation results submission
- The risk evaluation update
- Investigation results approval
- The investigation owner is responsible for the following:
- The CAPA coordinator is responsible for the following:
- Ensure accurate documentation
- Step 5: investigation part II: out of specification
- Investigating and assessing OOS results—principles of failure investigation
- Step 5: investigation part III—complaint investigation
9. Step 6: part I—root cause analysis
- Outcome
- How to conduct an RCA and the RCA team
- Definition of the problem
- Gathering relevant data
- Cause/effect analysis
- Open issues/notes
- Action plan
- RCA assessment and maintenance
- Part II: RCA tools
- Philosophy of RCA
- Symptom approach versus root cause
- How do we do RCA?
- RCA major steps
- RCA process charting
- Typical checklist for aspects to be considered when doing the RCA
- Barrier analysis
- Barrier analysis: pros and cons
- Definitions
- Change analysis
- Definitions
- Pros and cons
- Discussion
- What is a suitable basis for comparison?
- The purpose of change analysis
- Brainstorming
- Brainstorming guidelines
- Fishbone diagram
- What does it look like?
- How is it done?
- Guidelines
- People
- Machines
- Measurement
- Material
- Environment
- Methods
- Methods
- 5W techniques or why diagram
- Control charts
- Types of variation
- Types of variation
- Check sheets can be used to gather and group data
- Pareto analysis
- It is critical to determine the whys?
- Mistakes do not just happen
- Preventing human error
- Error proofing: 5S methodology
- Continuous improvement models: 5S
- Human error assessment and reduction technique
- Part III: example of investigation tools for why diagrams and fault tree diagrams
- Containment/correction
- Investigation plan
- Investigation elements
- Summary of root/contributing causes
- Investigation and root cause conclusion
10. Step 7: corrective and preventive action plans
- Completing corrective/preventive action plans
11. Step 8: implement and follow-up on action plans
- Action plans
- Execution of the CAPA plan
- Follow-up action plan
- Follow-up: a fundamental step in the CAPA process
- Upon completion of each corrective action/preventive action
- CAPA and change control
- Classification of the change
12. Step 9: verification of effectiveness
- Verification/effectiveness of the actions
- CAPA verification of effectiveness plan
- Conclusion
13. Examples of procedures
- Procedure example #1. SOP: control of nonconforming product
- Procedure example #2. OOS: SOP
- Procedure example #3. SOP: corrective and preventive
- Procedure example #4. SOP: FMEA SOP
- Procedure example #5. OP: RCA
- Procedure example #6. SOP: quality system data analysis
Conclusion: requirements for an effective CAPA program
- Edition: 1
- Published: December 11, 2015
- Imprint: Woodhead Publishing
- Language: English
JR