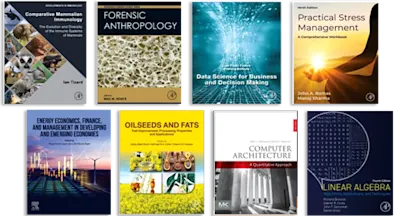
Basic Engineering Plasticity
An Introduction with Engineering and Manufacturing Applications
- 1st Edition - August 24, 2006
- Imprint: Butterworth-Heinemann
- Author: David Rees
- Language: English
- Paperback ISBN:9 7 8 - 0 - 7 5 0 6 - 8 0 2 5 - 7
- eBook ISBN:9 7 8 - 0 - 0 8 - 0 4 7 0 9 0 - 0
Plasticity is concerned with understanding the behavior of metals and alloys when loaded beyond the elastic limit, whether as a result of being shaped or as they are employed for… Read more
Purchase options
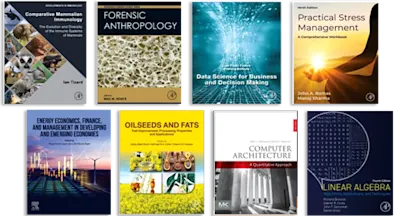
Plasticity is concerned with understanding the behavior of metals and alloys when loaded beyond the elastic limit, whether as a result of being shaped or as they are employed for load bearing structures. Basic Engineering Plasticity delivers a comprehensive and accessible introduction to the theories of plasticity. It draws upon numerical techniques and theoretical developments to support detailed examples of the application of plasticity theory. This blend of topics and supporting textbook features ensure that this introduction to the science of plasticity will be valuable for a wide range of mechanical and manufacturing engineering students and professionals.
- Brings together the elements of the mechanics of plasticity most pertinent to engineers, at both the micro- and macro-levels
- Covers the theory and application of topics such as Limit Analysis, Slip Line Field theory, Crystal Plasticity, Sheet and Bulk Metal Forming, as well as the use of Finite Element Analysis
- Clear and well-organized with extensive worked engineering application examples, and end of chapter exercises
Senior undergrad and graduate level students in mechanical and manufacturing engineering; aeronautical, materials and metallurgical engineering and related disciplines/sub-disciplines (including structural mechanics, solid mechanics, elasticity, plasticity, mechanics of materials, metal forming mechanics, civil engineering);Practicing manufacturing engineers dealing with plastic formed components, such as pressure vessels and other loaded structures; fabrication engineers
PrefaceList of NotationsChapter 1: Stress Analysis1.1 Introduction1.2 Cauchy Definition of Stress1.3 3D Stress Analysis1.4 Principal Stresses and Invariants1.5 Principal Stresses as Co-ordinates1.6 Alternative Stress DefinitionsBibliographyExercisesChapter 2: Strain Analysis2.1 Introduction2.2 Infinitesimal Strain Tensor2.3 Large Strain Definitions2.4 Finite Strain Tensors2.5 Polar Decomposition2.6 Strain DefinitionsReferencesExercisesChapter 3: Yield Criteria3.1 Introduction3.2 Yielding of Ductile Isotropic Materials3.3 Experimental Verification3.4 Anisotropic Yielding in Polycrystals3.5 Choice of Yield FunctionReferencesExercisesChapter 4: Non-Hardening Plasticity4.1 Introduction4.2 Classical Theories of Plasticity4.3 Application of Classical Theory to Uniform Stress States4.4 Application of Classical Theory to Non-Uniform Stress States4.5 Hencky versus Prandtl-ReussReferencesExercisesChapter 5: Elastic-Perfect Plasticity5.1 Introduction5.2 Elastic-Plastic Bending of Beams5.3 Elastic-Plastic Torsion5.4 Closed Thick-Walled Pressure Cylinder with Closed-Ends5.5 Open-Ended Cylinder and Thin Disc Under Pressure5.6 Rotating DiscReferencesExercisesChapter 6: Slip Line Fields6.1 Introduction6.2 Slip Line Field Theory6.3 Frictionless Extrusion Through Parallel Dies6.4 Frictionless Extrusion Through Inclined Dies6.5 Extrusion With Friction Through Parallel Dies6.6 Notched Bar in Tension6.7 Die Indentation6.8 Rough Die Indentation6.9 Lubricated Die IndentationReferencesExercisesChapter 7: Limit Analysis7.1 Introduction7.2 Collapse of Beams7.3 Collapse of Structures7.4 Die Indentation7.5 Extrusion7.6 Strip Rolling7.7 Transverse Loading of Circular Plates7.8 Concluding RemarksReferencesExercisesChapter 8: Crystal Plasticity8.1 Introduction8.2 Resolved Shear Stress and Strain8.3 Lattice Slip Systems8.4 Hardening8.5 Yield Surface8.6 Flow Rule8.7 Micro- to Macro-Plasticity8.6 Subsequent Yield Surface8.7 SummaryReferencesExercisesChapter 9: The Flow Curve9.1 Introduction9.2 Equivalence in Plasticity9.3 Uniaxial Tests9.4 Torsion Tests9.5 Uniaxial and Torsional Equivalence9.6 Modified Compression Tests9.7 Bulge Test9.8 Equations to the Flow Curve9.9 Strain and Work Hardening Hypotheses9.10 Concluding RemarksReferencesExamplesChapter 10: Plasticity With Hardening10.1 Introduction10.2 Conditions Associated with the Yield Surface10.3 Isotropic Hardening10.4 Validation of Levy-Mises and Drucker Flow Rules10.5 Non-Associated Flow Rules10.6 Prandtl-Reuss Flow Theory10.7 Kinematic Hardening10.8 Concluding RemarksReferencesExercisesChapter 11; Orthotropic Plasticity11.1 Introduction11.2 Orthotropic Flow Potential11.3 Orthotropic Flow Curves11.4 Planar Isotropy11.5 Rolled Sheet Metals11.6 Extruded Tubes11.7 Non-Linear Strain Paths11.8 Alternative Yield Criteria11.9 Concluding RemarksReferencesExercisesChapter 12: Plastic Instability12.1 Introduction12.2 Inelastic Buckling of Struts12.3 Buckling of Plates12.4 Tensile Instability12.5 Circular Bulge Instability12.6 Ellipsoidal Bulging of Orthotropic Sheet12.7 Plate Stretching12.8 Concluding RemarksReferencesExercisesChapter 13: Stress Waves in Bars13.1 Introduction13.2 The Wave Equation13.3 Particle Velocity13.4 Longitudinal Impact of Bars13.5 Plastic Waves13.6 Plastic Stress Levels13.7 Concluding RemarksReferencesExercisesChapter 14: Production Processes14.1 Introduction14.2 Hot Forging14.3 Cold Forging14.4 Extrusion14.5 Hot Rolling14.6 Cold Rolling14.7 Wire and Strip Drawing14.8 Orthogonal Machining14.8 Concluding RemarksReferencesExercisesIndex
- Edition: 1
- Published: August 24, 2006
- Imprint: Butterworth-Heinemann
- Language: English
DR
David Rees
Affiliations and expertise
Senior Lecturer in Applied Mechanics, Brunel University, UKRead Basic Engineering Plasticity on ScienceDirect