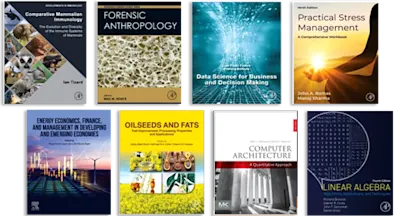
Applied Plastics Engineering Handbook
Processing, Sustainability, Materials, and Applications
- 3rd Edition - November 23, 2023
- Imprint: William Andrew
- Editor: Myer Kutz
- Language: English
- Paperback ISBN:9 7 8 - 0 - 3 2 3 - 8 8 6 6 7 - 3
- eBook ISBN:9 7 8 - 0 - 3 2 3 - 9 1 0 6 7 - 5
Applied Plastics Engineering Handbook: Processing, Sustainability, Materials, and Applications, Third Edition presents the fundamentals of plastics engineering, helping bring rea… Read more
Purchase options
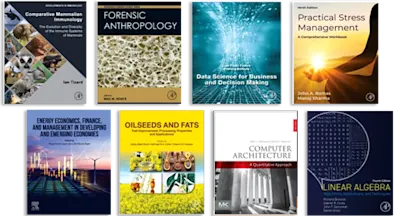
Applied Plastics Engineering Handbook: Processing, Sustainability, Materials, and Applications, Third Edition presents the fundamentals of plastics engineering, helping bring readers up-to-speed on new plastics, materials, processing and technology. This revised and expanded edition includes the latest developments in plastics, including areas such as biodegradable and biobased plastics, plastic waste, smart polymers, and 3D printing. Sections cover traditional plastics, elastomeric materials, bio-based materials, additives, colorants, fillers and plastics processing, including various key technologies, plastic recycling and waste. The final part of the book examines design and applications, with substantial updates made to reflect advancements in technology, regulations, and commercialization.
Throughout the handbook, the focus is on engineering aspects of producing and using plastics. Properties of plastics are explained, along with techniques for testing, measuring, enhancing, and analyzing them. Practical introductions to both core topics and new developments make this work equally valuable for newly qualified plastics engineers seeking the practical rules-of-thumb they don't teach you in school and experienced practitioners evaluating new technologies or getting up-to-speed in a new field.
- Offers an ideal reference for new engineers, experienced practitioners and researchers entering a new field or evaluating a new technology
- Provides an authoritative source of practical advice, presenting guidance that will lead to cost savings and process improvements
- Includes the latest technology, covering 3D printing, smart polymers and thorough coverage of biobased and biodegradable plastics
PART I: PLASTICS, ELASTOMERIC AND BIOBASED MATERIALS1. Engineering Thermoplastics—Materials, Properties, Trends2. Polyolefin3. Introduction to Fluoropolymers4. Poly(Vinyl Chloride)5. Polyamides6. Thermoplastic Elastomers7. Thermoset Elastomers8. Rubber Technology9. Biodegradable and Biobased Polymers10. Polymeric Biomaterials11. New Plastics
PART II: ADDITIVES, COLORANTS AND FILLERS12. Plastics Additives13. Additives for Biobased Plastics14. Dispersants and Coupling Agents15. Functional Fillers for Plastics16. Plasticizers17. Adhesion Promoters: Silane Coupling Agents18. Polymer Stabilization
PART III: PLASTICS PROCESSING19. Recycling of Plastics20. Disposal of Plastic Packaging and Plastic Articles in the Natural Environment21. Recovery of Marine Plastics22. Injection Molding Technology23. Microcellular Injection Molding24. Extrusion Processes25. Blow Molding26. Compression Molding27. Rotational Molding28. Thermoforming29. Processing Biobased Plastics and Sustainable Fillers30. Process Monitoring and Process Control: An Overview31. Surface Modification of Plastic
PART IV: DESIGN AND APPLICATIONS32. Plastics Joining33. Design of Plastic Parts34. Three-Dimensional Printing of Plastics35. Plastics in Buildings and Construction36. Automotive Applications of Plastics: Past, Present, and Future 37. Infrastructure Applications of Fiber-Reinforced Polymer Composites38. The Plastic Piping Industry in North America39. PET Use in Blow Molded Rigid Packaging40. Use of Biobased/Renewable Plastics in Packaging
- Edition: 3
- Published: November 23, 2023
- Imprint: William Andrew
- Language: English
MK