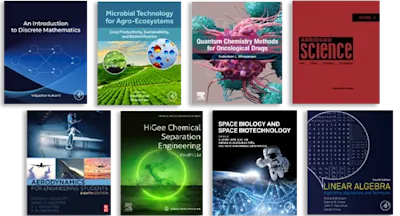
Analytical Approaches for Reinforced Concrete
- 1st Edition - April 22, 2022
- Author: Yufei Wu
- Language: English
- Paperback ISBN:9 7 8 - 0 - 1 2 - 8 2 1 1 6 4 - 9
- eBook ISBN:9 7 8 - 0 - 1 2 - 8 2 3 2 0 1 - 9
Analytical Approaches for Reinforced Concrete presents mathematically-derived theories and equations for RC design and construction. The book applies deductive reasoning, logic and… Read more
Purchase options
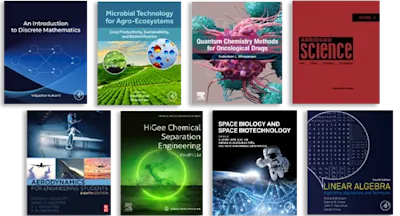
Analytical Approaches for Reinforced Concrete presents mathematically-derived theories and equations for RC design and construction. The book applies deductive reasoning, logic and mathematics to RC. Laying out, deductively, the principles of RC, it encourages researchers to re-imagine and innovate using a solid conceptual framework. Sections consider the reasoning behind key theories, as well as problems that remain unsolved. The title presents key ideas in simple language and illustrates them clearly to help the reader grasp difficult concepts and develop a solid foundation, grounded in mathematics, for further study and research.
The book is future-oriented, demonstrating theories that are applicable not only to conventional reinforced concrete members, but also to the envisaged structures of tomorrow. Such developments will increasingly require a deep, deductive understanding of RC. This title is the first of its kind, presenting a fresh analytical approach to reinforced concrete design and construction.
- Takes an analytical approach to reinforced concrete using mathematics and deduction
- Lays out the reasoning behind key theories and models in reinforced concrete design and construction
- Encourages researchers-new and established- to re-imagine and innovate using a solid conceptual framework
- Presents difficult concepts that are clearly and analytically presented with accompanying illustrations
- Looks forward to the use of reinforced concrete in the complex structures of the future
Chapter 1. Failure of Reinforced Concrete Members
1.1 Introduction
1.2 Typical structure of RC beam
1.3 Experimental observations - an RC practical
1.3.1 Beam 1
1.3.2 Beam 2
1.3.3 Beam 3
1.3.4 Beam 4
1.3.5 Beam 5
1.3.6 Beam 6
1.4 Failure modes
1.4.1 Evolution of failure modes
1.4.2 Safe failure mode and control of failure mode
1.4.3 The principle of weakest link
1.4.4 Other failure modes
1.5 Failure consequence, safety factor, and ductility
1.6 Limit state design approach
1.7 Structural design procedure
1.7.1 Design for serviceability limit states
1.7.2 Design for ultimate limit states
1.7.3 Design procedure
1.8 Design codes of practice
References
Chapter 2. Flexural Failure and Design Theory
2.1 Introduction
2.2 Failure process
2.2.1 Effect of loading type on failure point
2.3 Moment-curvature relationship
2.4 Typical response curves
2.5 Failure modes
2.6 Calculation of design moment
2.6.1 Moment taking
2.6.2 Moment redistribution
2.6.2.1 The mechanism of moment redistribution
2.6.2.2 Effect of redistribution to moment envelope
2.6.2.3 Determination of moment envelope
2.7 Conventional flexural theory
2.7.1 Solution of the equations
2.7.2 Stress block parameters
2.7.3 Discussions on stress block parameters
2.8 Miscellaneous relationships
2.8.1 Curvature of section
2.8.2 The theorem of plane section
References
Chapter 3. Deductive Approach to Flexural Theory
3.1 General Assumptions
3.2 RC Flexural Design Theorems
3.2.1 The first theorem
3.2.2 The second theorem
3.2.3 The third theorem
3.3 Numerical Illustrations
3.3.1 Flexural design parameters
3.3.2 Elastic compression reinforcement
3.3.3 Ultimate failure point
3.4 Ultimate Curvature and Curvature Ductility of RC Sections
3.4.1 Curvature ductility of plain concrete sections
3.4.2 Effect of longitudinal reinforcement on ductility of RC column sections
3.4.2.1 At critical axial load
3.4.2.2 For axial load levels lower than the critical load
3.4.2.3 For axial load levels higher than the critical axial load
3.4.3 Numerical studies
3.5 Derivation of the Theorems
3.5.1 Under-reinforce sections
3.5.2 Maximum reinforcement ratio for cm=cm,u
3.5.3 Elastic solutions
3.5.4 Transition stage
3.5.5 RC sections with elastic compression bars
3.5.6 Equivalent reinforcement ratio
3.5.7 Ultimate curvature
3.5.8 Derivation of cases with elastic bars
3.5.8.1 Flexural design with elastic tension reinforcement
3.5.8.2 Flexural design with elastic compression reinforcement
3.6 Alternative Flexural Design Procedure
3.6.1 Comparison with ACI 318
3.6.2 Design procedure
References
Chapter 4. Applications of the Flexural Theorems
4.1 Application to design of RC Members under Elevated Temperature
4.1.1 Stress-strain model of concrete under elevated temperature
4.1.2 Stress-strain relationship of steel bar under elevated temperature
4.1.3 Stress block parameters
4.1.4 Design example
4.1.5 Validation of results
4.1.6 Flexural analysis of RC members under elevated temperature
4.1.6.1 Flexural strength
4.1.6.2 Flexural design strain
4.1.6.3 Ultimate curvature
4.1.6.4 Parametric Studies
4.2 Stress Block Parameters for RC Members Reinforced with FRP Bar
4.2.1 Flexural failure of FRP-reinforced concrete beams
4.2.2 Stress strain relationships
4.2.3 Parametric studies
4.2.3.1 Effects of compressive strength of concrete
4.2.3.2 Effects of effective reinforcement ratio
4.2.4 Stress block parameters
4.2.5 Comparisons with existing design codes
4.2.5.1 ACI 440.1R-15
4.2.5.2 CSA-S806-12
4.2.6 Design examples
4.2.7 Comparison of models
References
Chapter 5. Bond Between Reinforcement and Concrete
5.1 Composite action
5.2 Bond of reinforcement
5.3 Bond mechanisms and bond-slip relationship
5.3.1 Adhesion
5.3.2 Mechanical interlock
5.3.3 Friction
5.4 Bond design of rebar
5.5 Anchorage design of rebar for flexural members
5.6 Beam action and arch action
5.7 Effect of crack on bond
5.8 Effect of bond on cracking
5.8.1 Crack formation in RC ties
5.8.2 Crack formation in RC beams
5.9 Evaluation of crack width and spacing
5.9.1 Design for cracking
5.9.2 Slip theory
5.9.3 No-slip theory
5.9.4 Mathematical modeling
5.9.5 Other models
5.10 Tension stiffening
5.11 Flexural strength calculation without considering slip
5.12 Frictional shear for RC joints
References
Chapter 6. Analytical Modeling of Composite Members
6.1 Structural rehabilitation
6.2 Mechanically bonded systems
6.2.1 Classic linear elastic theory
6.2.2 Equilibrium and compatibility
6.2.3 Governing differential equation
6.2.4 Solution for the case of cantilever column
6.2.5 Composite parameters
6.2.5.1 Parameters governing longitudinal slip
6.2.5.2 Parameters affecting flexural deformation
6.2.6 Slip distribution
6.2.7 Other studies on partial-interaction composite members
6.3 Adhesively bonded reinforcement
6.3.1 Failure modes
6.3.2 Flexural design approach
6.3.3 Measures to suppress interfacial debonding
6.4 Analytical solution of EBR pull off test
6.4.1 Governing equations
6.4.2 Analytical solutions
6.4.3 Snapback problem
6.4.4 Control of pull-off test
6.4.5 Peak strength
6.4.6 Parameter identification
6.5 Hybrid bonded reinforcement
6.5.1 Bond enhancement systems
6.5.2 Mechanisms of the HB system
6.5.3 Experimental tests
6.5.4 Bond Modeling
References
Chapter 7. Flexural Deflection
7.1 Introduction
7.2 Deflection under serviceability limit states
7.2.1 General
7.2.2 Short term flexural rigidity and tension stiffening
7.2.2.1 Transformed section
7.2.2.2 Effective moment of inertia
7.2.2.3 Smeared crack approach
7.2.2.4 Curvature modeling considering slip
7.2.3 Long-term deflection
7.2.3.1 Long-term effective modulus of concrete
7.2.3.2 Long-term curvature and deflection due to creep
7.2.3.3 Deflection due to shrinkage and temperature change
7.2.4 Superposition of flexural deflections
7.3 Deflection under ultimate limit states
7.3.1 Physical plastic hinge length and equivalent plastic hinge length
7.3.2 Factors affecting plastic hinge length
7.3.3 Existing plastic hinge length models
7.3.4 Numerical and analytical studies on plastic hinge length
7.3.4.1 Rebar yielding zone
7.3.4.2 Concrete softening zones
7.3.4.3 Curvature localization zone
7.3.4.4 Parametric studies
7.3.4.5 Effect of confinement and minimum jacket length
7.3.4.6 Equivalent plastic hinge length
7.3.4.7 Plastic hinge under cyclic loading
7.3.4.8 Effect of FRP-to-concrete interfacial bond on plastic hinge
7.3.5 The P- effect
7.3.5.1 Implications of the P- effect
7.3.5.2 Evaluation of the simplified method for the P- effect
References:
Chapter 8. Confined Concrete
8.1 Introduction
8.2 Confinement effects to compression failure of concrete
8.3 Strength modeling of confined concrete cylinders/circular columns
8.3.1 Active and passive confinement
8.3.2 Typical strength models
8.4 Strength modeling of non-circular columns
8.4.1 Confinement effectiveness of square jacket
8.4.2 Effective strain of FRP jacket
8.4.3 Development of models for FRP-confined square/rectangular columns
8.4.3.1 Empirical models
8.4.3.2 Unified models
8.4.3.3 Hoek-Brown’s model
8.4.4 Assessment of Models
8.5 Measures to increase confinement effectiveness for rectilinear columns
8.5.1 Increasing the rigidity of jacketing plate
8.5.2 Reducing longitudinal stress
8.5.3 Additional anchoring
8.5.4 Alteration of cross-section
8.5.5 Other means
8.6 Stress-strain relationship of concrete
8.6.1 Methods for stress-strain modelling
8.6.2 Existence and form of the one-dimensional stress-strain relationship
8.6.3 Stress-strain relationship of concrete confined by steel reinforcement
8.6.4 Stress-strain model of concrete for FRP confined columns
8.6.4.1 Models developed by Teng’s group (Lam and Teng 2003a&b; Teng et al. 2009)
8.6.4.2 The model proposed by Harajli et al. (2006)
8.6.4.3 The model proposed by Wu et al. (2007)
8.6.4.4 The model by Youssef et al. (2007)
8.6.4.5 The unified model by Wei and Wu (2012)
8.6.5 Stress-strain model of confined concrete under eccentric loading
8.6.5.1 Effect of load eccentricity on the stress-strain relationship of confined concrete
8.6.5.2 The stress-strain model by Wu and Jiang (2013a)
8.6.5.3 The stress-strain model by Cao et al (2018)
8.6.5.4 Effect of load path on stress-strain relationship
8.6.6 Analytical method for stress-strain modeling
8.6.6.1 The analytical method by Li et al. (2021)
8.6.7 Stress-strain model of confined concrete for repair works by Wu et al. (2014)
8.6.8 Stress-strain model of confined concrete under cyclic loading
8.6.9 Stress-strain model of concrete for axially loaded members with failure localization
References
Chapter 9. Ductility Modification Technologies
9.1 Introduction
9.2 Ductility deficient RC structures reinforced with non-ductile bars
9.3 Avenues for ductility
9.4 Compression yielding structural system
9.5 Compression yielding instruments
9.5.1 Compression yielding mechanisms
9.5.2 Compression yielding material
9.6 Test of CY beams
9.7 Ductility demand on CY zone
9.8 Design of CY members
9.9 CY columns
9.10 Fused structures
9.10.1 A new type of structural fuse
9.10.2 Cost analysis of the fused structures
9.10.3 Determination of safety margin for fused structures
9.11 Increasing concrete strength by reducing perforation
9.12 Failure localization and mitigation
9.12.1 Failure of RC column under concentric loading
9.12.2 Concrete cracking
9.12.3 Plastic hinge failure
9.12.4 Rebar necking
9.12.5 General rule for mitigation of failure localization
References
Chapter 10. Shear Failure of RC Members
10.1 Introduction
10.2 Shear failure process and failure modes
10.3 Shear resisting mechanisms
10.3.1 Shear transfer mechanisms of RC members without web reinforcement
10.3.2 Shear transfer of RC members with web reinforcement
10.4 Development of shear design approaches
10.5 Evaluation of existing shear strength models
10.5.1 Evaluation of total shear strength
10.5.2 Evaluation of shear strength components
10.5.3 Difference between Vc and Vcr
10.5.4 Other test observations
10.5.5 Summary of findings
10.6 Discussion on shear strength modeling
10.6.1 Classic mechanics for derivation of Vcr
10.6.2 Shear resisting system and individual shear mechanisms
10.6.3 Advanced models based on particular shear mechanisms
10.6.4 Criterion based design approach
10.6.5 Lower bound solution
10.7 Potential solutions
10.7.1 More sophisticated modeling of the load-deformation process for the major shear mechanisms
10.7.2 Design RC details of a potential shear failure zone to have a simple and desirable load path and failure mode
10.7.3 Using a structural fuse to convert the shear failure mode to another one
10.7.4 Developing shear strength model with AI technology
References
Chapter 11. Modeling
11.1 Introduction
11.2 Types of model
11.3 Principles of modeling
11.3.1 Accuracy versus complexity of model
11.3.2 Causality of model
11.3.3 Task driven modeling
11.4 Methods of modeling
11.4.1 Logic reasoning
11.4.2 Theoretical vs. empirical modeling
11.4.3 Linear vs. non-linear modeling
11.4.4 Forward vs. inverse modeling
11.4.5 Heuristic modeling
11.5 Evaluation of model
11.5.1 Fitting observations
11.5.2 Scope of model
11.5.3 Philosophical considerations
11.6 Selection of model
11.6.1 Quantitative models
11.6.2 Qualitative models
11.7 Modeling with theorems of plasticity
11.7.1 Theorems of plasticity
11.7.2 Application of the plasticity theorems
11.8 About safety factor
11.9 Detailing of structures
11.10 Size effect
11.11 Research approach
11.11.1 Scientific method
11.11.2 The four dimensions of research approach
11.11.3 Fostering creativity in research
References
- Edition: 1
- Published: April 22, 2022
- Language: English
YW