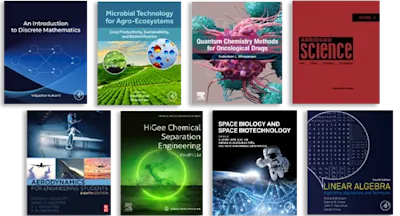
Aliphatic Alkylation
in Petroleum Refining
- 1st Edition - January 22, 2025
- Authors: Weizhen Sun, Weizhong Zheng, Ling Zhao, Jinzhu Li, Huanxin Gao
- Language: English
- Paperback ISBN:9 7 8 - 0 - 4 4 3 - 2 1 9 8 4 - 9
- eBook ISBN:9 7 8 - 0 - 4 4 3 - 2 1 9 8 5 - 6
Aliphatic Alkylation in Petroleum Refining provides a fundamental understanding on the alkylation process, from molecular-level interfacial properties to macroscopic industry… Read more
Purchase options
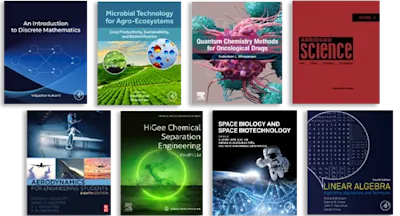
Aliphatic Alkylation in Petroleum Refining provides a fundamental understanding on the alkylation process, from molecular-level interfacial properties to macroscopic industry plants. Since the direct distillation of oil fractions does not satisfy the whole demand for fuel feedstocks, processes such as reforming, isomerization, and alkylation are needed to fulfill the market requirements within the gasoline pool. From the processes mentioned above, this book covers one of the most important refining processes due to the high quality of the alkylate with high research octane number (RON).
Although the Aliphatic alkylation with H2SO4 and HF as catalysts have been industrialized for many years, there still exists lots of problems due to the complex heterogeneous reaction, such as the thermodynamics, reaction mechanism, molecular-level interfacial properties, and so on.
- Introduces industrial alkylation technology and process safety with different catalysts
- Highlights reaction mechanisms and kinetic models using different catalysts
- Presents interfacial behaviors between reactants and catalysts that are fundamental in the process intensification of Aliphatic alkylation
1.1 Definition of Aliphatic alkylation
1.2 History of Aliphatic alkylation
1.3 Role of Aliphatic alkylation unit in the refinery
1.4 Other alkylation processes
This chapter mainly gives the detailed description about the definition and the history of alkylation. In addition, the role of Aliphatic alkylation unit in the refinery will be further emphasized. The aim of this chapter is to make the reader understand the fundamental concepts of the alkylation.
2. Alkylation catalysts and general operation parameters
2.1 Sulfuric acid
2.1.1 Feed
2.1.2 Temperature
2.1.3 Reaction time
2.2 HF 2.2.1 Feed
2.2.2 Temperature
2.2.3 Reaction time
2.3 Chloroaluminate ionic liquids
2.3.1 Feed2.3.2 Temperature
2.3.3 Reaction time
2.4 Zeolites
2.4.1 Feed
2.4.2 Temperature
2.4.3 Reaction time
This chapter describes the catalysts for the alkylation, including the sulfuric acid, HF, ionic liquids, and solid acid. The research progress of these catalysts for the alkylation will be listed, respectively. The advantages and disadvantages of these catalysts will be summarized. Furthermore, the trend of development of these catalysts in the industrial application will be introduced, providing the reference for the industrial alkylation process. In addition, for different catalysts, the effect of the operating parameters on the Aliphatic alkylation.
3. Reaction Thermodynamics
This chapter solves the thermodynamics analysis of the complex alkylation reactions, giving the detailed thermodynamics path and the thermodynamics computation for the reactions.
4. Transport behaviors
4.1 Mass transport
4.2 Heat transport The transport processes will be introduced for the alkylation.
5. Reaction mechanism This chapter will give the general reaction mechanism for the alkylation.
6. Reaction kinetics
6.1 Kinetics using sulfuric acid as catalyst
6.2 Kinetics using ionic liquid as catalyst
6.3 Kinetics using sulfuric acid and additives as catalyst This chapter provides the reaction mechanism and kinetics model. The kinetics parameters for sulfuric acid, ionic liquids, waste acid with and without additives will be outlined.
7. Reactors, Catalysts deactivation and regeneration
7.1 Industrial reactors7.2 Deactivation mechanism
7.2.1 Sulfuric acid
7.2.2 HF
7.2.3 Ionic liquid
7.2.4 Solid acids
7.3 Regeneration strategies This chapter will describe the study on reactor. Based on the reactors, the deactivation of various catalysts will be introduced, figuring out the key deactivation mechanism of various catalysts and the corresponding regeneration strategy.
8. Process intensification
8.1 Process optimization
8.2 Interfacial behaviors
8.3 Intensification mechanism of interfacial behaviors
8.4 Design of interfacial intensification additives
This chapter mainly describes the process optimization. The role of the interfacial behaviors on the alkylation will be introduced. The investigated method for the interfacial properties of alkylation will be given. The detailed interfacial behaviors of alkylation, including interfacial structure, interface compositions, interfacial tension, and interfacial diffusion, will be discussed. At the same time, the improvement of interfacial properties will be given, including stirring and additives.
9. Industrial alkylation process and safety
9.1 Industrial alkylation process
9.2 Industrial alkylation safety
9.3 Industrial operation challenges
This chapter will introduce the current industrial alkylation process based on sulfuric acid, HF, ionic liquids, and solid acid. The capacity and operation process of the alkylation will be listed.
10. Acknowledgements
11. References
- Edition: 1
- Published: January 22, 2025
- Language: English
WS
Weizhen Sun
WZ
Weizhong Zheng
LZ
Ling Zhao
JL
Jinzhu Li
Jinzhu Li is a Senior Engineer at SINOPEC Zhenhai Refining & Chemical Company, Ningbo, China. He graduated from Fushun Petroleum Institute with the bachelor's degree and East China University of Science and Technology with the master's degree in Chemical Engineering. He was engaged in the operation and management of petroleum refining plant for 24 years, responsible for the construction and operation management of 500,000 tons/year liquefied gas separation plant, and the expansion construction and operation management of MTBE plant from 20,000 tons/year to 40,000 tons/year, then to 100,000 tons/year, and finally to 150,000 tons/year. He was also responsible for the operation and technical management of the gasoline-diesel hydrogenation unit and the wax oil hydrocracking unit, as well as the technical comparison, construction, start-up, shutdown and operation management of the 300,000 tons/year sulfuric acid alkylation and the supporting acid regeneration unit. He has rich experience in oil refinery operation safety and technical management.
HG
Huanxin Gao
Gao Huanxin is a Senior Engineer at SINOPEC Shanghai Research Institute of Petrochemical Technology Co., LTD., Shanghai, China. He graduated from Lanzhou Institute of Chemical Physics, Chinese Academy of Sciences, majoring in Physical chemistry. His main research interests include zeolite acid catalyst and selective oxidation catalyst, and their applications in petrochemical industry, especially focusing on the alkylation of benzene with alkene and epoxidation of propylene. His group has developed and commercialized several catalysts and licensed several process technologies. He has published more than 30 publications in international journals.