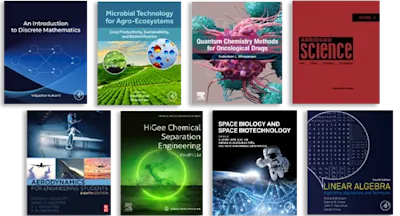
Algal Bioreactors
Vol 1: Science, Engineering and Technology of upstream processes
- 1st Edition - November 27, 2024
- Imprint: Woodhead Publishing
- Editors: Eduardo Jacob-Lopes, Leila Queiroz Zepka, Mariany Costa Depra
- Language: English
- Paperback ISBN:9 7 8 - 0 - 4 4 3 - 1 4 0 5 8 - 7
- eBook ISBN:9 7 8 - 0 - 4 4 3 - 1 4 0 5 6 - 3
Algal Bioreactors: Science, Engineering and Technology of Upstream Processes, Volume One, is part of a comprehensive two-volume set that provides all of the knowledge needed to… Read more
Purchase options
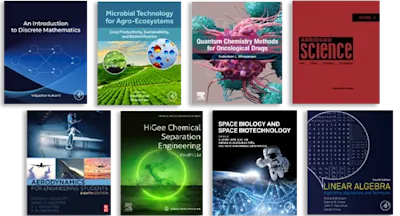
Algal Bioreactors: Science, Engineering and Technology of Upstream Processes, Volume One, is part of a comprehensive two-volume set that provides all of the knowledge needed to design, develop, and operate algal bioreactors for the production of renewable resources. Supported by critical parameters and properties, mathematical models and calculations, methods, and practical real-world case studies, readers will find everything they need to know on the upstream and downstream processes of algal bioreactors for renewable resource production.
Bringing together renowned experts in microalgal biotechnology, this book will help researchers, scientists, and engineers from academia and industry overcome barriers and advance the production of renewable resources and renewable energy from algae. Students will also find invaluable explanations of the fundamentals and key principles of algal bioreactors, making it an accessible read for students of engineering, microbiology, biochemistry, biotechnology, and environmental sciences.
- Presents the physical, biological, environmental, and economic parameters of upstream processes in the operation and development of algal bioreactors to produce renewable resources
- Explains the main configurations and designs of algal bioreactors, presenting recent innovations and future trends
- Integrates the scientific, engineering, technology, environmental, and economic aspects of producing renewable resources and other valuable bioproducts using algal bioreactors
- Provides real-world case studies at various scales to demonstrate the practical implementation of the various technologies and methods discussed
Students, researchers, scientists, and engineers working across a broad spectrum of fields related to renewable energy production from algae, including biotechnology, process engineering, chemical engineering, environmental science, microbiology, mycology (algae specialists). Industry engineers and practitioners actively involved in the commercial implementation and operation of bioenergy plants and biofuel production operations who are interested in using algae as a feedstock
1. Introduction to algal bioreactors: The biotechnology core
2. Algae strains in bioreactors: the adaptability of commercial and emerging species for renewable resource production
3. Principles of interactions between physiology and bioreactor design
4. Global market of algae bioproducts from bioreactor systems
5. Intellectual property and innovation trends applied to algae bioreactors
Part II – Science and engineering of algae bioreactors
6. Predictive models of algae growth in bioreactors
7. Optimal growth and culture conditions for algae in bioreactors
8. Hydrodynamic performance of algae bioreactors
9. Transfer phenomena in algae bioreactors
10. Photosynthetic reactions in algae photobioreactors
11. Contamination control in algae bioreactors
12. Processes control approaches applied to bioreactor models
13. Physical and biokinetic processes of carbon biosequestration in algae bioreactors
14. Biochemicals reactions in algae bioreactors
15. The influence of low carbon to nitrogen (C/N ratio) on phycoremediation
16. Ultrasound in algal bioreactors: A Process intensification strategy for renewable resources production
17. Microwave application in algal bioreactors: A Process intensification strategy for renewable resources production
18. Computational analysis of algae bioreactors performance for renewable resources production
19. Internet of Things (IoT) use for remote monitoring of algae bioreactors for renewable resources production
20. Scale-up of algae bioreactors for renewable resources production
21. Installations of algae bioreactors: design and operational issues in commercial plants
22. Techno-economic aspects and operational costs of algae bioreactors for renewable resources production
Part III – Trends in algal bioreactors design for renewable resource production
23. Industrial fermenters for renewable resource production
24. Air-lift photobioreactors for renewable resource production
25. Tubular photobioreactors for renewable resource production
26. Flat-plate photobioreactors for renewable resource production
27. Column photobioreactors for renewable resource production
28. Bubble column photobioreactors for renewable resource production
29. Hybrid photobioreactors for renewable resource production
30. Plastic bags photobioreactors for renewable resource production
31. Annular photobioreactors for renewable resource production
32. Membrane photobioreactors for renewable resource production
33. Packed Bed Bioreactors for renewable resource production
34. Fluidized Bed Reactors for renewable resource production
35. Exergy analysis of algae bioreactors for renewable resources production
36. Design of clean-in-place systems in algal bioreactors for renewable resources production
Part IV – Bioprocesses, bioenergy, and bioproducts obtained from algae bioreactors
37. Enhancing anaerobic digestion processes in algae bioreactors for renewable products production
38. Biohydrogen production in algae bioreactors
39. Biodiesel production in algae bioreactors
40. Bioethanol production in algae bioreactors
41. Biomethane production in algae bioreactors
42. Bio-jet fuel production in algal bioreactors
43. Bioelectricity from microalgae-microbial fuel cell in bioreactors
44. Biofertilizers production in algal bioreactors
45. Biomass production in algae bioreactors
46. Proteins and amino acids production in algae bioreactors
47. Lipids, sterols, and fatty acids production in algae bioreactors
48. Pigments production in algae bioreactors
49. Bioreactors as core production of specific algal for food supplements
50. Biomedical applications of algal-based products
Part V - Environmental issues for algae bioreactors
51. Industrial wastewater in algae bioreactors
52. Algae bioreactors as strategies for heavy metal phycoremediation
53. Environmental assessment of algae bioreactors for renewable resources production
54. Carbon neutral in renewable resources from algae bioreactors: Is this possible?
- Edition: 1
- Published: November 27, 2024
- Imprint: Woodhead Publishing
- Language: English
EJ
Eduardo Jacob-Lopes
LQ
Leila Queiroz Zepka
MC