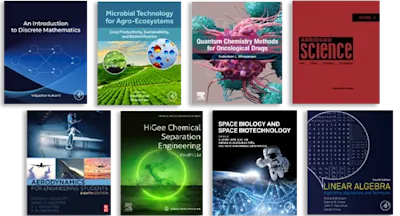
Advances in Chemical Mechanical Planarization (CMP)
- 2nd Edition - September 16, 2021
- Imprint: Woodhead Publishing
- Editor: Babu Suryadevara
- Language: English
- Paperback ISBN:9 7 8 - 0 - 1 2 - 8 2 1 7 9 1 - 7
- eBook ISBN:9 7 8 - 0 - 1 2 - 8 2 1 8 1 9 - 8
Advances in Chemical Mechanical Planarization (CMP), Second Edition provides the latest information on a mainstream process that is critical for high-volume, high-yield semicondu… Read more
Purchase options
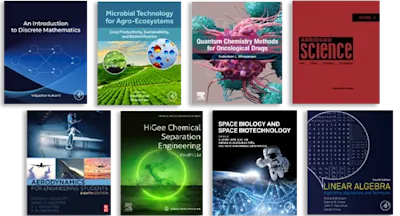
Advances in Chemical Mechanical Planarization (CMP), Second Edition provides the latest information on a mainstream process that is critical for high-volume, high-yield semiconductor manufacturing, and even more so as device dimensions continue to shrink. The second edition includes the recent advances of CMP and its emerging materials, methods, and applications, including coverage of post-CMP cleaning challenges and tribology of CMP.
This important book offers a systematic review of fundamentals and advances in the area. Part one covers CMP of dielectric and metal films, with chapters focusing on the use of current and emerging techniques and processes and on CMP of various materials, including ultra low-k materials and high-mobility channel materials, and ending with a chapter reviewing the environmental impacts of CMP processes. New content addressed includes CMP challenges with tungsten, cobalt, and ruthenium as interconnect and barrier films, consumables for ultralow topography and CMP for memory devices. Part two addresses consumables and process control for improved CMP and includes chapters on CMP pads, diamond disc pad conditioning, the use of FTIR spectroscopy for characterization of surface processes and approaches for defection characterization, mitigation, and reduction.
Advances in Chemical Mechanical Planarization (CMP), Second Edition
is an invaluable resource and key reference for materials scientists and engineers in academia and R&D.- Reviews the most relevant techniques and processes for CMP of dielectric and metal films
- Includes chapters devoted to CMP for current and emerging materials
- Addresses consumables and process control for improved CMP, including post-CMP
Materials Scientists and Engineers in academia and R&D. Chemistry
Part One - CMP of dielectric and metal films
1. Chemical and physical mechanisms of dielectric chemical mechanical polishing (CMP)
2. Copper chemical mechanical planarization (Cu CMP) challenges in 22 nm back-end-of-line (BEOL) and beyond
3. Electrochemical techniques and their applications for CMP of metal films
4. Ultra-low-k materials and chemical mechanical planarization (CMP)
5. CMP processing of high mobility channel materials - alternatives to Sis
6. Multiscale modeling of chemical mechanical planarization (CMP)
7. Polishing of SiC films
8. Chemical and physical mechanisms of CMP of gallium nitride
9. Abrasive-free and ultra-low abrasive chemical mechanical polishing (CMP) processes
10. Transient copper removal rate phenomena with implications for polishing mechanisms
11. Environmental aspects of planarization processes
Part Two - Consumables and process control for improved CMP
12. Preparation and characterization of slurry for CMP
13. Chemical metrology methods for CMP quality
14. Diamond disc pad conditioning in chemical mechanical polishing
15. Characterization of surface processes during oxide CMP by in situ FTIR spectroscopy
16. Chemical mechanical polishing (CMP) removal rate uniformity and role of carrier parameters
17. Approaches to defect characterization, mitigation and reduction
18. Challenges and solutions for post-CMP cleaning at device and interconnect levels
19. Applications of chemical mechanical planarization (CMP) to More than Moore devices
20. CMP for phase change materials
21. CMP pads and their performance
22. Latest developments in the understanding of PVA brush related issues during post CMP (pCMP) cleaning
- Edition: 2
- Published: September 16, 2021
- Imprint: Woodhead Publishing
- Language: English
BS