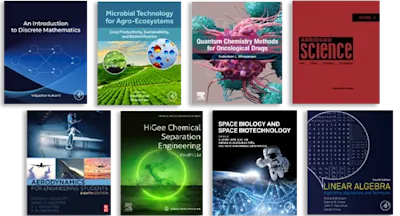
Additive Manufacturing of Shape Memory Materials
Techniques, Characterization, Modeling, and Applications
- 1st Edition - October 24, 2024
- Editors: Mehrshad Mehrpouya, Mohammad Elahinia
- Language: English
- Paperback ISBN:9 7 8 - 0 - 4 4 3 - 2 9 5 9 4 - 2
- eBook ISBN:9 7 8 - 0 - 4 4 3 - 2 9 5 9 5 - 9
Additive Manufacturing of Shape Memory Materials: Techniques, Characterization, Modeling, and Applications outlines an array of techniques and applications for additive manufa… Read more
Purchase options
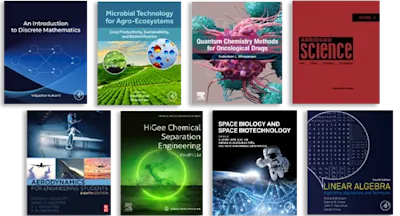
Additive Manufacturing of Shape Memory Materials: Techniques, Characterization, Modeling, and Applications outlines an array of techniques and applications for additive manufacturing (AM) and the use of various shape memory materials, covering corrosion properties, material sensitivity to thermal, magnetic, and electrical effects, as well as sensitivity of shape memory properties to AM parameters, including part geometry effects and post-process treatments.
Design for AM and a number of different AM methods are discussed, with materials covered including shape memory alloys, shape memory polymers, high-temperature shape memory alloys, and magnetic shape memory alloys. Characterization and modeling methods are also included, as is a chapter dedicated to real-world applications of these production techniques and materials.
Design for AM and a number of different AM methods are discussed, with materials covered including shape memory alloys, shape memory polymers, high-temperature shape memory alloys, and magnetic shape memory alloys. Characterization and modeling methods are also included, as is a chapter dedicated to real-world applications of these production techniques and materials.
- Provides an overview of various shape memory materials, their additive manufacturing techniques and processes, their applications, and opportunities and challenges related to their production and use
- Outlines the thermomechanical and functional properties of shape memory alloys that can be applied to their additive manufacturing processes
- Covers techniques for additive manufacturing of shape memory polymers, shape memory alloys, high-temperature shape memory alloys, and magnetic shape memory alloys
- Discusses characterization, post-processing, modeling, and applications of shape memory materials
Beginner to high-level researchers, students and professionals who are working on and learning about shape memory materials and additive manufacturing technology
1. Introduction to additive manufacturing of shape memory materials
2. Functional performance of shape memory alloys
3. Additive manufacturing of shape memory polymers
4. Alloy design for 3D-printed shape memory alloys
5. Additive manufacturing of high-temperature shape
6. Additive manufacturing of magnetic shape memory alloys
7. E-PBF-based additive manufacturing of shape memory alloys
8. L-PBF additive manufacturing of shape memory alloys
9. DED-based additive manufacturing of shape memory alloys
10. Characterization and postprocessing of additively
11. Modeling of 3D-printed shape memory alloys
12. Application of 3D-printed shape memory alloys
2. Functional performance of shape memory alloys
3. Additive manufacturing of shape memory polymers
4. Alloy design for 3D-printed shape memory alloys
5. Additive manufacturing of high-temperature shape
6. Additive manufacturing of magnetic shape memory alloys
7. E-PBF-based additive manufacturing of shape memory alloys
8. L-PBF additive manufacturing of shape memory alloys
9. DED-based additive manufacturing of shape memory alloys
10. Characterization and postprocessing of additively
11. Modeling of 3D-printed shape memory alloys
12. Application of 3D-printed shape memory alloys
- Edition: 1
- Published: October 24, 2024
- Language: English
MM
Mehrshad Mehrpouya
Mehrshad Mehrpouya earned his Ph.D. degree through a fellowship program from Sapienza University of Rome, Italy. He is currently an Assistant Professor in the Department of Design, Production, and Management (DPM) at the University of Twente (UT). His research interests are directed toward Advanced Manufacturing, 3D/4D Printing, Functional Materials, and modeling.
Affiliations and expertise
Assistant Professor, Department of Design, Production, and Management (DPM), University of Twente (UT), The NetherlandsME
Mohammad Elahinia
Mohammad Elahinia is currently a Professor of Mechanical, Industrial and Manufacturing Engineering (MIME) and also serves as Director of the Dynamic and Smart Systems Laboratory at University of Toledo, where has been a faculty member since 2004. He graduated from Villanova University with an MS degree and from Virginia Tech with a Ph.D. in Mechanical Engineering respectively in 2001 and 2004. Dr. Elahinia’s research interests are in smart and active materials. His current research is focused on additive manufacturing of functional materials such as shape memory alloys for aerospace and biomedical application.
Affiliations and expertise
Professor of Mechanical, Industrial and Manufacturing Engineering, The University of Toledo, USARead Additive Manufacturing of Shape Memory Materials on ScienceDirect