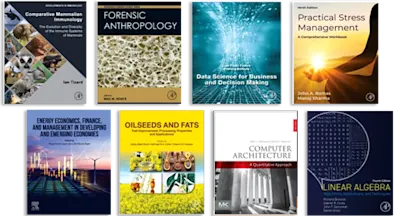
Acoustic Emission Signal Analysis and Damage Mode Identification of Composite Wind Turbine Blades
- 1st Edition - May 24, 2023
- Imprint: Elsevier
- Author: Pengfei Liu
- Language: English
- Paperback ISBN:9 7 8 - 0 - 3 2 3 - 8 8 6 5 2 - 9
- eBook ISBN:9 7 8 - 0 - 3 2 3 - 9 5 8 1 3 - 4
- eBook ISBN:9 7 8 - 0 - 3 2 3 - 8 8 6 4 7 - 5
Acoustic Emission Signal Analysis and Damage Mode Identification of Composite Wind Turbine Blades covers both the underlying theory and various techniques for effective structura… Read more
Purchase options
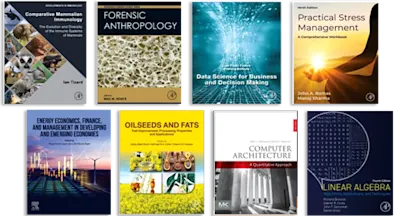
Acoustic Emission Signal Analysis and Damage Mode Identification of Composite Wind Turbine Blades covers both the underlying theory and various techniques for effective structural monitoring of composite wind turbine blades via acoustic emission signal analysis, helping readers solve critical problems such as noise elimination, defect detection, damage mode identification, and more. Author Pengfei Liu introduces techniques for identifying and analyzing progressive failure under tension, delamination, damage localization, adhesive composite joint failure, and other degradation phenomena, outlining methods such as time-difference, wavelet, machine learning, and more including combined methods.
The disadvantages and advantages of using each method are covered as are techniques for different blade-lengths and various blade substructures. Piezoelectric sensors are discussed as is experimental analysis of damage source localization. The book also takes great lengths to let readers know when techniques and concepts discussed can be applied to composite materials and structures beyond just wind turbine blades.
- Features fundamental acoustic emission theories and techniques for monitoring the structural integrity of wind turbine blades
- Covers sensor arrangements, noise elimination, defect detection, and dominating damage mode identification using acoustic emission techniques
- Outlines the wavelet method, the time-difference defect detection method, and damage mode identification techniques using machine learning
- Discusses how the techniques covered can be extended and adapted for use in other composite structures under complex loads and in different environments
Advanced undergraduate and graduate students;
2. Failure Mechanisms in Wind Turbine Blades: Delamination, Adhesive Composite Joint Failure
3. Delamination Analysis of Composite Laminates
4. Damage Analysis of Adhesive Composite Joints
5. Damage Mechanisms of Blade Structures Under Accelerated Fatigue Loads
6. Waveform-Based Feature Extraction Model
7. Experimental Analysis of Damage Source Localization
8. Clustering Method for Damage Mode Identification
- Edition: 1
- Published: May 24, 2023
- Imprint: Elsevier
- Language: English
PL